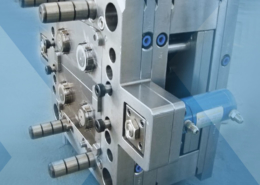
Third-Gen Mars Injection Molding Machines Coming to America - haitian injection
Author:gly Date: 2024-09-30
A project of this magnitude certainly is a partnership, and Phillips commented that Infiltrator is a great partner with which to work. "They are such an innovative company and willing to take risks. We love to have them as a partner," he added. "They've taught us a lot over the years, and through our input we've helped them find solutions as well. They like to challenge us and we enjoy meeting those challenges that result in success."
That turned out to be an understatement. Today, plastics are one of the cornerstones of modern technological civilization — tough, flexible durable, impervious to corrosion, and seemingly endlessly versatile. However, there are downsides to its prevalence. That's why plastic alternatives are worth finding.
When single-use plastic bags first hit the scene, we had a choice: paper or plastic. Today, it's pretty much all plastic. And if you're not that hypervigilant person at the checkout, you'll find yourself walking home with a bag for each item.
You can get them festooned with patterns or printed with the name or your bank/gym/frozen yogurt shop. Everyone hands them out, and they come in canvas, woven plastic fiber, hemp, cotton and even leather. You'll find nylon ones that fold up into a pouch small enough to fit in your pocket. In reality, any type of bag will do, whether it's meant to carry groceries or not.
Phillips noted that the biggest challenge was the logistics involved in delivering the mold. After the mold was built, it was disassembled and placed on a fleet of 15 trucks for shipping from Lansing, MI, to Winchester, KY. A team of moldmakers was then sent to Kentucky to re-assemble the mold on Infiltrator's plant floor.
Once upon a time, both moms and milkmen filled glass bottles with milk. Now look around your kitchen and you'll probably see many plastics — water bottles, soda bottles, food storage containers. Times have changed.
As a totally biodegradable, low-cost, renewable and natural polymer, starch has been receiving lots of attention for developing sustainable materials. When it comes to replacing plastic, however, starch can't cut the mustard; its poor mechanical properties mean it has limited use for the sturdy products that plastics generate.
PLA looks and performs similiarly to the polyethlene used in plastic films, packing materials and bottles, and it can also be used as a substitute for the polystyrene used in foam food plates and containers and plastic cutlery. But unlike conventional petroleum-based plastics, PLA has some big advantages. For one, since it's made from plants that absorb carbon dioxide as they grow, there's no net increase in carbon dioxide from its raw materials. A 2017 study found that switching from conventional plastic to PLA would cut U.S. greenhouse gas emissions by 25 percent [source: Cho].
PHAs already are used in a variety of products, including disposable package for foods, beverages and various consumer products. They're also being used in medical applications such as sutures, and to make the agricultural foil used to store hay bales [source: Creative Mechanisms].
Producing plastic from processed corn may seem like a pipe dream, but it's happening every day. Polylactic acid, or PLA, is another aliphatic polyester and one that can be made from lactic acid, which is produced via starch fermentation during corn wet milling. Although most often generated from corn, PLA can be made from wheat or sugarcane as well.
Bryan Coppes, VP of engineering at Infiltrator Systems, said, "Rounding out the successful IM-Tank product line was a high priority for Infiltrator. Franchino is our largest tooling vendor and with their experience with our other large-part molds it made them the right choice for this project."
Manufacturers mix lignin, a byproduct of paper mills, with water, and then expose the mixture to serious heat and pressure to create a moldable composite material that's strong and nontoxic. German researchers have incorporated this plastic substitute into a variety of items including toys, golf tees and even hi-fi speaker boxes.
In 2018, Bioplastics News reported that Christopher Johnson, a researcher at the U.S. Department of Energy's National Renewable Energy Laboratory, had developed a promising process for improve the conversion of lignin into a substitute material for plastics, as well as nylon.
Glass bottles and jars potentially are 100 percent recyclable, and the glass in them can be reused endlessly, without any loss in quality and purity. Glass manufacturers welcome recycled glass, because when it's used as an ingredient in making new glass, it requires less energy in furnaces. Container manufacturers and the fiberglass industry (which also uses recycled glass) together purchase 3.35 million tons (3.03 million metric tons) of recycled glass annually [source: Glass Packaging Institute].
What one of the hottest trends in biodegradable plastic development can do is make polymer composites more biodegradable. You name it, and starch has probably been combined with it, albeit with varying degrees of success.
Sometimes going back in time is a good thing. Unlike plastic, which often is derived from fossil fuels, glass is made from sand. This renewable resource doesn't contain chemicals that can leach into your food or body. And it's easily recycled — whether you throw bottles in your recycling bin to be turned into new bottles or reuse glass jars for storing leftovers. Sure, glass may break if dropped, but it won't melt in your microwave.
The next three entries on this list are all biodegradable plastics called aliphatic polyesters. Overall, they aren't as versatile as aromatic polyesters such as polyethylene terephthalate (PET), which is commonly used to make water bottles. But since aromatic polyesters are completely resistant to microbial breakdown, a lot of time and effort is being pumped into finding viable alternatives in aliphatic polyesters.
Take polycaprolactone (PCL), a synthetic aliphatic polyester that isn't made from renewable resources but does completely degrade after six weeks of composting. It's easily processed but hasn't been used in significant quantities because of manufacturing costs. However, blending PCL with cornstarch reduces cost.
The world's largest low-pressure injection molding machine, designed and constructed by Infiltrator Systems at the company's Winchester, KY, manufacturing facility, took five months to engineer and nine months to build. However, today the machine is producing the Infiltrator IM 1530 Septic Tank product line being molded in a mold designed and built by Franchino Mold and Engineering of Lansing, MI. The mold installed in the press weighs 420,000 lbs. and molds a 15-foot long, 245-lb. polypropylene tank half, which the company claims is the world's largest molded part.
Search around for additive technologies and you'll come across the trade names TDPA (an acronym for Totally Degradable Plastic Additives) or MasterBatch Pellets (MBP). They're used to manufacture single-use plastics such as thin plastic shopping bags, disposable diapers, trash bags, landfill covers and food containers (including fast-food containers).
Franchino previously created what is now the world's second largest mold, Infiltrator System's IM-1060 tank in a mold to produce a part weighing 160 lbs.
Scientists have found a way make the protein less susceptible to cracking, thanks to a silicate clay called sodium montmorillonite. Freezing sodium montmorillonite into a spongelike material called an aerogel, they infused the porous network of clay with casein plastic. The result? A polystyrene-type material that, when put in a dump environment, begins to degrade completely [source: The Economist]. The modern milk-based plastic doesn't crack as easily, thanks to that silicate skeleton, and they even made the stuff less toxic by substituting glyceraldehyde for formaldehyde during the process.
Franchino employs 85 people currently, but that will change as the company's expansion plans evolve. Phillips noted that the company recently purchased another 62,000-sf facility behind a current plant and the two buildings will be connected. "We're going through the building modifications now and moving equipment in, which will include a 50-ton crane to accommodate the larger sizes of the molds we build," he said.
So, while there is no silver bullet for making plastics greener, a combination of revitalizing old ideas and revolutionizing plastic technology is a step in the right direction.
Next up is a promising bioplastic, or biopolymer, called liquid wood. Biopolymers fake it; these materials look, feel and act just like plastic but, unlike petroleum-based plastic, they're biodegradable. This particular biopolymer comes from pulp-based lignin, a renewable resource.
Production costs have mostly put PHA in the shadow of cheaper, petroleum-based plastics, but a little creativeness in sourcing inexpensive raw materials may make it a top choice soon. Corn-steeped liquor, molasses and even activated sludge could all supply the sugar the bacteria need to produce the plastic.
Until she retired in September 2021, Clare Goldsberry reported on the plastics industry for more than 30 years. In addition to the 10,000+ articles she has written, by her own estimation, she is the author of several books, including The Business of Injection Molding: How to succeed as a custom molder and Purchasing Injection Molds: A buyers guide. Goldsberry is a member of the Plastics Pioneers Association. She reflected on her long career in "Time to Say Good-Bye."
When added to polyethylene (the standard plastic bag material) at levels of 3 percent, PDCs can promote nearly complete degradation; 95 percent of the plastic is in bacteria-friendly fragments within four weeks [source: Nolan-ITU Pty]. While not strictly biodegradable ('bioerodable' is more like it), PDC-containing polymers are more environmentally friendly than their purer polymer cousins, which sit in landfills for hundreds of years.
Coppes added that the ability to mold septic tanks of this size "opens up a lot of doors" for the company in this marketplace. He noted that there is more demand for polymer septic tanks as replacements for concrete tanks because of the greater strength of the polymer tanks as well as the ease of installation and the fact that no large equipment is required.
In fact, it's tough to make a purchase without it promptly being thrown into plastic. No wonder plastic bags seem omnipresent. The U.S. produced an astonishing 4.13 million tons (3.75 million metric tons) of plastic bags in 2015 and only 530,000 tons (481,000 metric tons) of those were recycled [source: EPA]. The rest end up as litter in cities and towns — and too many find their way to the ocean, where they kill millions of sea turtles, birds and ocean mammals each year. But you have to lug those groceries home somehow. So what do you do? Reusable grocery bags, for starters.
Back in 1907, Leo Baekeland invented a new material, Bakelite, that was the first true synthetic plastic, composed of molecules not found in the natural world. It was an amazing breakthrough. Bakelite was durable and heat resistant and could be molded into almost any shape. People called it "the material of a thousand uses" [source: Science History Institute].
The world's largest low-pressure injection molding machine, designed and constructed by Infiltrator Systems at the company's Winchester, KY, manufacturing facility, took five months to engineer and nine months to build. However, today the machine is producing the Infiltrator IM 1530 Septic Tank product line being molded in a mold designed and built by Franchino Mold and Engineering of Lansing, MI. The mold installed in the press weighs 420,000 lbs. and molds a 15-foot long, 245-lb. polypropylene tank half, which the company claims is the world's largest molded part.
Each shot is a mirror image of itself with a cutout in the top for tank access. "Other than that the tanks are symmetrically the same," said Coppes. One half has gaskets and the halves are sealed together. The parts handling and finishing stations utilize what Infiltrator believes is the largest six-axis robot in the world.
What's happening across the country is that the cost of expanding sewer plants has risen and a lot of the federal grant money for these infrastructure projects has dried up," Coppes explained. "That means more people and communities are looking at septic systems rather than sewer systems."
That's the case with polyhydroxyalkanoate (PHA) polyesters, the two main members of which are polyhydroxybutrate (PHB) and polyhydroxyvalerate (PHV). These biodegradable plastics closely resemble man-made polypropylene. While they're still less flexible than petroleum-based plastics, you'll find them in packaging, plastic films and injection-molded bottles.
PLA has the advantage that it's quickly biodegradable, under the right conditions. If the plastic is sent to an industrial composting facility where it's continually subjected to heat and microbes, it can degrade in two to three months. If it's tossed in a landfill, though, it won't break down any quicker than conventional plastic [source: Isom and Shughart].
Infiltrator Systems, a Graham Partners portfolio company, employs approximately 280 people at its facility. Through its subsidiary, Champion Polymer Recycling, Infiltrator is a leading purchaser of "green materials" including post-consumer and post-industrial recycled plastics used in the manufacture of Infiltrator products.
Starch is usually blended with aliphatic polyesters, such as PLA and PCL, and polyvinyl alcohol to make completely biodegradable plastics. Adding in starch also shaves plastic manufacturing costs. But starch content must exceed 60 percent of the composite before it has a significant effect on degradation; as the starch content increases, the polymers become more biodegradable [source: Nolan-ITU Pty Ltd]. Keep in mind, though, that adding more starch also affects the properties of the plastic. If you put wet leaves in a starch bag for a bit, you'll have a mess when you go to pick up the bag.
Franchino has many years (16-18) of experience with building aluminum and hybrid aluminum and steel tooling for very large parts. Phillips said that some of those molds the company built have one to two million shots on them, a testament to the longevity of aluminum tooling in many large-part molding applications.
Coppes told PlasticsToday that the company's success with its 1000-gallon septic tanks led the market to demand tanks in a 1500-gallon size. Infiltrator is the world's largest septic products company. Molding a tank this large required a 6,000-ton low-pressure injection molding machine. "We brought in a lot of resources to help us redesign and engineer a press to make it suitable for our needs," Coppes explained. Infiltrator molds its own product and parts requirements in-house, and also has a number of regular injection molding presses to mold its other products.
For now, plastic objects are all around us, from the food containers and bottles of milk and soda that we buy at the supermarket, to the countertops in our kitchens and the linings of our cooking pans. We wear clothes fashioned from plastic fibers, sit on plastic chairs, and travel in automobiles, trains and airplanes that contain plastic parts. Plastics have even become an important building material, used in everything from insulated wall panels to window frames [source: American Chemistry Council]. We continue to find new uses for plastic all the time.
But we could do a lot better job of recycling glass. In 2015, the most recent year for which the U.S. Environmental Protection Association (EPA) has statistics, Americans only recycled 26.4 percent of the glass containers that they used.
"Naturally produced polyesters" may sound like a phrase lifted from a marketing campaign, but feed sugar to certain types of bacteria and you've got yourself a plastic production line.
The mold is built with aluminum core and cavity, housed in a steel mold base in what is known as a "hybrid mold" and took more than 10,000 man-hours to build. The cavity work was done using multiple Tarus 5-axis mills with table sizes of 114" x 120." It also contains the largest hot runner manifold system in operation in the world, explained Todd Phillips, VP of Franchino, which specializes the design engineering and manufacturing of very large molds to produce products that challenge the limits of injection molding. "This is the largest mold we've made to date," Phillips told PlasticsToday.
Our dependence upon plastic also has an increasingly serious downside, because we make so much of it, and throw so much of it away. Of the 9.1 billion tons (8.3 billion metric tons) of plastic that the world has produced since 1950, 6.9 billion tons (6.3 billion metric tons) has become waste, and only 9 percent of that has been recycled. The rest ends up in landfills and in the world's oceans, where plastic pollution is ravaging wildlife and washing up on beaches. About 40 percent of the waste is discarded packaging [source: Parker].
The winemaking industry produces a lot of grape waste — basically, the solid material that's left behind after grapes are pressed to extract the juice that's fermented into wine. (That amounts to about 25 percent of the weight of the grapes).
PHAs biodegrade via composting; a PHB/PHV composite (92 parts PHB/8 parts PHV, by weight) will almost completely break down within 20 days of cultivation by anaerobic digested sludge, the workhorse of biological treatment plants [source: Nolan-ITU Pty Ltd].
All newborn mammals survive on it. Without it, there would be no ice cream. There's really no denying the value — or pleasure — of milk.
Biodegradable plastics look and feel exactly like the plastic products we're encouraged to recycle. So what happens if we accidentally recycle those biodegradable bags? Well, the consequences are potentially catastrophic — recycled polyethylene irrigation pumps that are contaminated with PDC additives aren't likely to last very long. In fact, plastic recyclers in South Africa feel so strongly about the inability to keep PDC-containing biodegradables out of recycling streams that they want to ban their use in that country.
Biomedical devices and sutures are already made of the slow-degrading polymer, and tissue-engineering researchers dig it, too. It also has applications for food-contact products, such as trays.
The future of casein plastic isn't certain, but swapping it for petroleum-based polystyrene would certainly give us another reason to love milk.
Bonus: By avoiding plastic bags, you won't have them accumulating in your cupboards, and you don't have to worry about where they go when you throw them out.
While some people are busy developing plastic substitutes, others are bent on making conventional thermoplastics biodegradable. How? By throwing in additives called prodegradant concentrates (PDCs). PDCs are usually metal compounds, such as cobalt stearate or manganese stearate. They promote oxidation processes that break the plastic down into brittle, low-molecular-weight fragments. Microorganisms gobble up the fragments as they disintegrate, turning them into carbon dioxide, water and biomass, which reportedly contains no harmful residues.
Casein-based plastic has been around since the 1880s, when a French chemist treated casein with formaldehyde to produce a material that could substitute for ivory or tortoiseshell. But although it's ideal for jewelry that even Queen Mary admired, casein-based plastic is too brittle for much more than adornment.
Now scientists say it could help to produce a biodegradable plastic for furniture cushions, insulation, packaging and other products. Yep, researchers are revitalizing the idea of converting casein, the principal protein found in milk, into a biodegradable material that matches the stiffness and compressibility of polystyrene.
But an Italian company, Vegea, is using the grape waste to make a synthetic leather that could replace vinyl imitation leather, and also into fabric for clothing. Vegea is now in the process of scaling up its production capacity to manufacture the grape-waste apparel items for sale to clothing stores, so you can add grape waste to your wardrobe [source: Stella McCartney].
GETTING A QUOTE WITH LK-MOULD IS FREE AND SIMPLE.
FIND MORE OF OUR SERVICES:
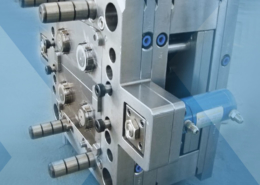
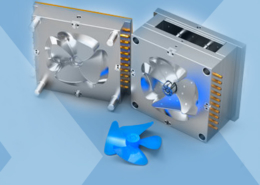
Plastic Molding

Rapid Prototyping
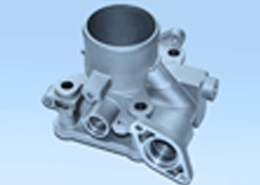
Pressure Die Casting
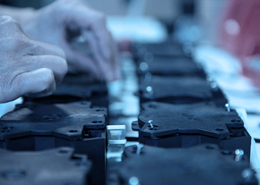
Parts Assembly
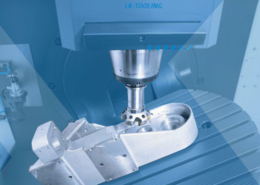