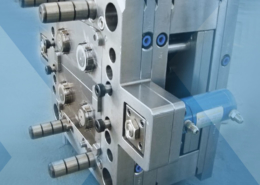
Thermoset-thermoplastic joining, natural fibers enable
Author:gly Date: 2024-09-30
High-performance injection moulds for challenging applications in medical technology require precision and skill. Schöttli, a Husky Company, constructs high-performance moulds in large quantities for medical applications including modern diabetes therapy, producing moulds for syringes to artificial pancreas devices.
Disposable syringes for the administration of insulin usually consist of a cylinder with a firmly glued-in injection needle and a plunger. Here, Schöttli offers productive and reliable mould solutions with hot-edge nozzles and dual side gating for syringe cylinders, syringe plungers and similar applications, usually made of polyolefins.
Globally, as many as 425 million people, which is 9% of the world adult population, are affected by diabetes. The persistent high blood sugar levels of diabetics can lead to serious complications, including strokes, heart attacks, amputations, blindness and the necessity for dialysis treatments. Early diagnosis and proper diabetes management are critical.
The manufacture of pen needle components and safety pen needles requires moulds that precisely produce these components, usually made of polyethylene or polypropylene. Schöttli provides expertise in high-cavity injection moulds for medical components. The company can offer corresponding single-face moulds for pen needle-shields with up to 256 cavities. Pen needle covers and similar components can be produced on stack moulds with up to 192+192 cavities, maintaining the highest precision and highest performance (Fig. 2). Schöttli delivered the world's first 192-cavity mould for pen needle hubs with side gate hot runner technology.
Customization and the potential comforts therein do come with a price: a pair of Personomic grips start at around $97 MSRP, and shipping outside the EU costs another $4.
Key components of the insulin pen are used for fixing the injection needles and for protecting the patients against accidental injury by the needles © Schöttli
Insulin pumps available on the market today are usually worn on the body, with a ‘patch’ housing an appropriate injection needle stuck directly onto the abdominal wall. With these patches, which are usually worn for four to ten days, the needle remains under the skin. However, even when using pumps, the blood sugar level must be measured and controlled separately.
The design is now getting more eyeballs — a 94,000-person German survey ranked Persomic at the top of the list in terms of bike grips. On top of that, the company just struck a deal with sizable German cycling wholesaler Paul Lange & Co. (a major Shimano distributor throughout Central Europe), meaning riders in Germany can now order Personomic products directly from their local bike shop.
In the future, the control of blood sugar levels and the administration of insulin will increasingly be carried out by so-called ‘closed-loop systems’, which are precisely adapted to current requirements. With these systems, blood sugar level is measured with a sensor worn on the skin (Continuous Glucose Monitoring = CGM) and transmitted wirelessly to the pump. The pump doses the correct amount of insulin at the right time. As in other medical fields, the classical treatment method and modern online diagnostic systems are gradually converging in diabetology. Since too much insulin can be as dangerous as too little insulin, this innovation contributes to greater patient safety and fewer complications, thus reducing the global cost of diabetes treatment.
Personomic claims its use of silicon over rubber or plastic results in grips that are hard-wearing, vibration-dampening, and non-sticky. Pair that with a grip that perfectly matches your hand, and you’ve got a seemingly winning combo.
A hundred years ago, a quarter litre of blood was required to determine accurate blood sugar levels. Today, there are devices as small as a smartphone and test strips that use only 0.3 μl of blood to provide an accurate blood sugar measurement. Syringes and pens allow diabetes patients to inject themselves with the precise quantities of insulin required to manage the disease. Insulin pumps work directly on the body, with complex sensors to determine and dose the insulin required.
Here’s how Personomic’s technology works. Place your hand on a sheet of computer paper and snap a photo. Send that photo to Personomic as a part of the ordering process — where you can also choose from five grip and locking ring colors, as well as your preferred texture pattern.
That range could also soon include a whole other category of customized cycling touchpoint products — Schulz and his co-founders told us expansion into the saddle market is right around the corner.
As an alternative to disposable syringes, high-precision pens are often used for the subcutaneous administration of insulin. These ‘disposable pens’ consist of several precise plastic parts with a fixed insulin cartridge, with sufficient volume for several treatments. Slightly more expensive, but also readily available, are long-term pens with replaceable insulin cartridges. In either case, a new injection needle, which is screwed onto the pen-housing in conjunction with a pen needle-hub, should be used for each administration. A needle is intended for a single administration and is then disposed of together with the pen-needle hub.
The company uses the paper as a reference point and creates a “digital twin” of your hand — an actual 3D model. Personomic then uses this digital twin to print a plastic mold of your personalized grip, then fills in that mold with silicon. When the silicon is set, employees remove the mold, package your grips, and stick them in the mail.
Disposable syringes or pens are often preferred for insulin dosage, ensuring cleanliness and accurate dosing. In Germany, for example, about 80% of all patients administer their insulin with pens, while in North America or Asia, disposable insulin syringes account for around 80% of insulin administration.
With these products the needles, which protrude out of the hub on both sides, are subsequently glued in place in a fully automated process. This is a particularly challenging application, as the needles have very small outer diameters of down to 34G (34 gauge equals 0.18mm). This requires correspondingly small cylindrical openings in the injection moulded part and accordingly, tremendous precision in the injection mould. Each of the 192 cavities is centered individually so that the forming pins (gauge pins) do not break. Only in this way can the reliability of the molds, which Schöttli is known for, can be achieved. The resulting high level of availability and, depending on the application, unmatched number of cavities, leads to a significant increase in productivity per square meter of production area for the customer.
Currently, insulin cannot be administered orally with sufficient precision, so must be injected directly into subcutaneous tissue. Insulin is preferably administered in the smallest quantities tolerated (a few milligrams at a time), as precisely and regularly as possible. Precise measurement – or even better, continuous monitoring – of the blood sugar level is an important prerequisite for this.
“The whole idea behind using 3D printing is that a custom bike grip will fit each cyclist’s hands perfectly, which will lead to better distribution of pressure across the hands. This prevents widespread issues such as numb fingers when cycling,” Personomic co-founder Andreas Schulz explained to BikeRumor by email.
The International Diabetes Federation (IDF) estimates that one in two cases of diabetes in adults has not yet been diagnosed. Novo Nordisk, a global healthcare company, goes even further and describes a ‘Rule of Halves’. Of diagnosed diabetics, approximately only half are treated and only 50% of those treated actually receive the right amount of insulin at the right time. However, if diagnosed diabetics pay attention to their body, check their blood sugar level regularly and supply insulin accordingly, they can tolerate the disease well and live healthy, active lives. In the case of type 1 diabetes insulin must be administered, whereas type 2 may require insulin depending on the stage of the disease.
All moulds for the medical components presented here are equipped with Schöttli hot runner systems. Moulding is normally done in a cleanroom environment, with fully automated production surroundings.
A pen needle-shield protects both the needle and the user from injuries immediately before and after use. For further protection and packaging, the pen needle cover is sealed with a film during transport (Fig. 1).
Fast forward two years, and the German company made good on its vision. A successful Kickstarter campaign led to 1,000 pre-orders from over 30 countries, and now the grips are available on demand from Personomic’s website. The secret sauce is their material choice, combined with the individual fit made possible by Personomic’s proprietary smartphone-scanning technology.
Mongoose is 50. And they’re bringing back old school BMX cool with a limited edition Classics Collection reissue of bikes & mag wheels…
Embarrassed other riders will notice your non-motorized pump in your jersey pocket? Get hip with the Muc-Off AirMach Electric Mini Inflator
An advanced needle type (safety pen-needles) is a slightly more sophisticated variant; these components are characterised by a special safety mechanism. A protective cap or shield automatically moves over the injection needle as soon as it is removed from the skin surface. This effectively prevents needle prick injuries caused by carelessness. Because insulin is typically administered in a home environment as opposed to a doctor’s office or a hospital, ease of use and consumer protection for diabetes management is important. Another advantage of this type of protection mechanism is the effective prevention of multiple uses.
“Although currently we only sell bike grips, we are a 3D-printing start-up at heart,” Schulz said. “We are currently also developing a custom bike saddle that is adapted to the individual cyclist and want to become the go-to cycling brand for customized, ergonomic bike accessories.”
Way back in the misty yonder days of 2021, Bikerumor’s coverage of Eurobike 2021 included a blurb about Personomic — a scrappy little startup with dreams of bringing personalized 3D-printed grips to the masses.
BOA Technology has been innovating cycling footwear for 16 years. Now, its presence in off-road riding is stronger than ever.
“This is particularly important because our customers do not want to produce two to three million plastic parts per year, but two to three million a day," says Adolph Keller, managing director sales & marketing at Schöttli, "and with consistent accuracy." Schöttli aims to produce moulds that offer maximum accuracy, consistency and adherence to the tightest tolerances. This is critical to ensure the high quality demands of the final product.
GETTING A QUOTE WITH LK-MOULD IS FREE AND SIMPLE.
FIND MORE OF OUR SERVICES:
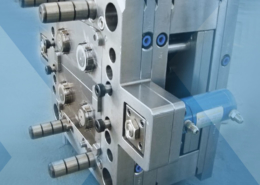
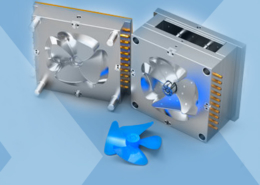
Plastic Molding

Rapid Prototyping
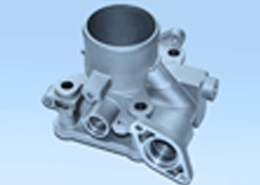
Pressure Die Casting
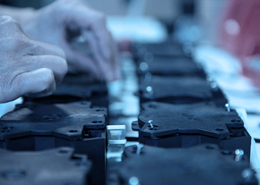
Parts Assembly
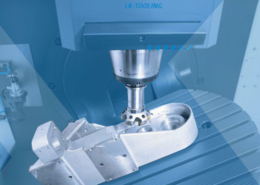