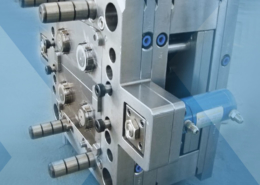
Exploring PPE Injection Molding: Enhancing Safety and Efficiency
Author:gly Date: 2024-06-08
Introduction
In the realm of personal protective equipment (PPE), injection molding stands as a crucial manufacturing process, ensuring the production of high-quality protective gear. With the ever-growing emphasis on safety across various industries, understanding the intricacies of PPE injection molding becomes paramount. This article delves into the nuances of PPE injection molding, shedding light on its significance, processes, materials, challenges, and future prospects.
Significance of PPE Injection Molding
PPE injection molding plays a pivotal role in crafting equipment designed to safeguard individuals in hazardous environments. From healthcare professionals to industrial workers, the demand for reliable protective gear continues to surge. Injection molding facilitates the mass production of PPE, meeting the escalating needs efficiently.
The versatility of injection molding allows for the creation of intricate designs and customized fittings, ensuring optimal comfort and functionality for the end-users. Its significance extends beyond conventional safety gear, encompassing medical devices, automotive components, and consumer goods.
Processes Involved
The process of PPE injection molding involves several intricate steps, starting from design conception to final product inspection. Initially, computer-aided design (CAD) software is utilized to create detailed blueprints, ensuring precise specifications. These designs are then translated into molds, typically made of steel or aluminum.
Molten thermoplastic materials, such as polyethylene, polypropylene, or polycarbonate, are injected into the molds under high pressure. The materials solidify within the mold cavity, taking the desired shape. Post-molding processes like trimming, assembly, and quality control checks ensure the integrity and functionality of the finished products.
Materials Selection
The choice of materials is critical in PPE injection molding, dictating the performance and durability of the end products. Various factors, including chemical resistance, impact strength, flexibility, and cost-effectiveness, influence material selection.
Polypropylene (PP) emerges as a popular choice due to its excellent chemical resistance and ease of molding. Thermoplastic elastomers (TPE) offer flexibility and comfort, making them ideal for components requiring skin contact. Polycarbonate (PC) provides exceptional impact resistance, rendering it suitable for face shields and safety goggles.
Challenges and Innovations
Despite its numerous benefits, PPE injection molding is not devoid of challenges. Design complexities, material limitations, and stringent regulatory standards pose significant hurdles for manufacturers. Addressing these challenges necessitates continuous innovation and advancements in materials science and manufacturing techniques.
Recent innovations in additive manufacturing, such as 3D printing, offer promising solutions to overcome traditional molding limitations. These technologies enable rapid prototyping, intricate designs, and on-demand production, revolutionizing the PPE manufacturing landscape.
Conclusion
In conclusion, PPE injection molding serves as a cornerstone in the production of essential safety equipment, catering to diverse industrial and healthcare needs. Understanding its processes, materials, challenges, and innovations is crucial for ensuring the efficacy and reliability of protective gear.
As industries evolve and safety standards evolve, ongoing research and development in PPE injection molding are imperative. Embracing emerging technologies and materials will not only enhance the quality and efficiency of protective equipment but also contribute to the well-being and safety of individuals worldwide.
By continuously refining manufacturing processes and materials selection, the future of PPE injection molding holds immense potential in mitigating occupational hazards and safeguarding human lives. As we navigate through dynamic environments, the commitment to innovation remains paramount in shaping a safer and more resilient future.
GETTING A QUOTE WITH LK-MOULD IS FREE AND SIMPLE.
FIND MORE OF OUR SERVICES:
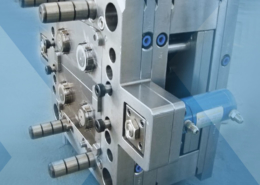
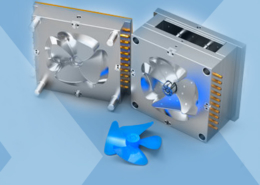
Plastic Molding

Rapid Prototyping
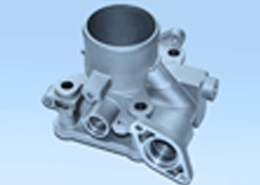
Pressure Die Casting
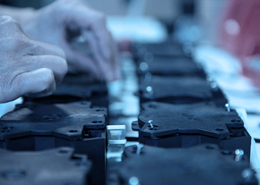
Parts Assembly
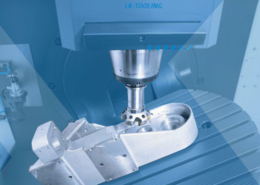