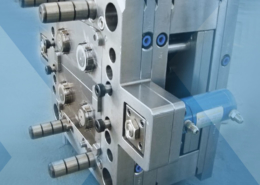
Thermoplastic composite, tube-shaped preforms for large-volume manufacturing - h
Author:gly Date: 2024-09-30
The Moldex3D R16 version expands simulation capabilities for resin transfer molding, polyurethane chemical foaming, fiber-reinforced plastic injection molding, hot-runner molding and more.
Key performance attributes include a dry cycle time (according to the Euromap 6 standard) of 6.8 seconds for the 1900-tonne SM1900 injection machine, high concentricity of screw and barrel of 0.07 mm, and +0.1% injection precision by utilizing a specially-designed injection screw, and optimized hydraulic and control systems. Further, electric plastication employing a servo motor and gearbox is offered as an option, which boasts 90% energy efficiency versus 77% for the efficiency of a hydraulic injection unit.
Further, two injection cylinders deliver a high degree of processing flexibility to the molder lest it want to use the machine for another application in that minimum shot size per cylinder is just 15 kg. The option of using just one injection cylinder is possible.
The R16 version also allows for enhanced simulation capabilities for composite and special molding processes. It expands simulation capabilities for resin transfer molding, polyurethane chemical foaming, fiber-reinforced plastic injection molding, hot-runner molding and so forth.
“Customers who come to us nowadays are not asking for a machine with a specific clamping force. They are coming to us looking for a solution, be it in medical, automotive or other sectors,” Ringo Au, head of international sales for Chen Hsong. The company offers a variety of clamping unit and injection unit options for the SM-TP Series to cater to varying industry requirements: 14 clamping tonnages in all are available between 700 and 6500 tonnes and also 29 shot weights ranging between 1968 and 106,081 grams per cylinder (meaning the options are even more abundant when considering the Y-configuration permeations). The permeations for combining clamping and injection options are thus numerous.
Chen Hsong two-platen machines are selling extremely well in the market of late. The company reports 126 on order for delivery through to March 2017, including 700-tonne, 2200-tonne, and 3600-tonne units.
Another auto parts supplier is using two Chen Hsong two-platen machines, a SM1650 model and a SM1050 model, to mold seat backs for the Audi Q5 using a low-pressure injection technique. The machines use Chen Hsong’s extractable platen technology” to facilitate easy tooling changes.
Until she retired in September 2021, Clare Goldsberry reported on the plastics industry for more than 30 years. In addition to the 10,000+ articles she has written, by her own estimation, she is the author of several books, including The Business of Injection Molding: How to succeed as a custom molder and Purchasing Injection Molds: A buyers guide. Goldsberry is a member of the Plastics Pioneers Association. She reflected on her long career in "Time to Say Good-Bye."
Visitors to the Moldex3D booth (4033) will get an exclusive sneak peek of its upcoming Moldex3D R16 version, which is designed to deliver reliable, high-efficiency, simulation-driven solutions to accelerate the pace of product innovation.
Leading Chinese auto OEMs are among users of Chen Hsong machines that the machine builder is working with, including an auto parts molder in Chongqing that is using a 1650-tonne SM1650 machine with the D130 injection unit (screw diameter of 130 mm, which is the standard injection unit for this machine size) to mold an instrument panel, and an auto parts molder in Shanghai which is employing the same type of machine to mold a mat.
Some of the benefits include rapid mold gating iteration that allows users to achieve ideal gate locations, especially for large parts, in a short amount of time before committing to a comprehensive design validation analysis.
Additionally, the R16 version allows users to simulate more in less time. For example, it reduces filling/packing simulation processing time by up to 30%. It also supports automatic generation of non-matched solid meshes for the entire mold base and its components, including the mold plate and inserts, thus reducing the amount of time and effort required to perform an accurate and reliable mold analysis.
Moldex3D Northern America Inc., headquartered in Farmington Hills, MI, will be previewing the latest innovations in its simulation portfolio for the plastics industry at PLASTEC West, which comes to the Anaheim Convention Center in Anaheim, CA, on Feb. 6 to 8.
The company manufactures two-platen injection machines at its flagship 560,000-m2 campus in Shenzhen. Chen Hsong prides itself in manufacturing all components bar electronic ones in-house. casting of platens and machining of screws included. “In this way we can control what raw materials go into our machines,” says C.K. Chiang, executive director of manufacturing and technology in Chen Hsong.
During PLASTEC West, Moldex3D Engineering Manager Srikar Vallury will be available at booth 4033 to answer questions. To schedule an appointment or live demonstration of Moldex3D’s simulation products, fill out a request form on the Moldex3D website.
When faced with a challenge from a processor requiring a shot weight of 110 kg, Chen Hsong turned to one of its large two-platen machines with a special modification. The solution was to configure a 6,500-tonne SM6500-TP injection molding machine with two parallel injection cylinders of 55 kg shot weight capacity each in a “Y” configuration.
Chen Hsong recently delivered the unit to Australian processor Trident Wastewater Services (Adelaide, SA) for molding large septic tanks from polypropylene in a single color. Shot volume is an incredible 152,094 cubic cm.
Chen Hsong has also worked to reduce sound levels during machine operation. The latest machines operate at a sound level of is 80 dB versus 84 dB for the national standard in China.
Stephen has been with PlasticsToday and its preceding publications Modern Plastics and Injection Molding since 1992, throughout this time based in the Asia Pacific region, including stints in Japan, Australia, and his current location Singapore. His current beat focuses on automotive. Stephen is an avid folding bicycle rider, often taking his bike on overseas business trips, and is a proud dachshund owner.
Automated Simulation Workflow boosts efficiency by allowing users to customize and automate simulation workflows through the integration of Moldex3D API with its product design systems. This reduces the complexity of simulation workflow and possible manual mistakes to ensure accuracy and consistency.
GETTING A QUOTE WITH LK-MOULD IS FREE AND SIMPLE.
FIND MORE OF OUR SERVICES:
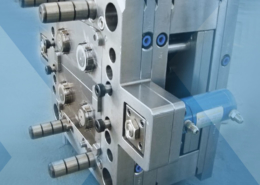
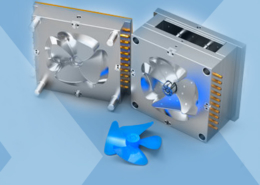
Plastic Molding

Rapid Prototyping
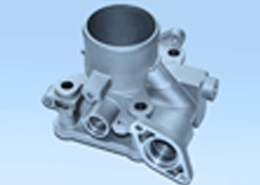
Pressure Die Casting
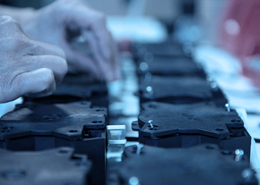
Parts Assembly
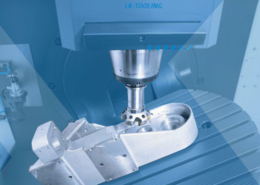