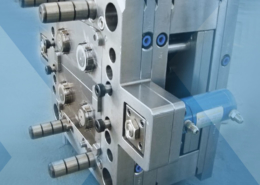
The role of micromoulding in wearable diabetes devices - thin wall moulding
Author:gly Date: 2024-09-30
In addition to facilitating recycling, the mono-material construction and integrated processing of the tube and label contribute to the stability of the tube, enabling a reduction in wall thickness, if needed. The process also eliminates secondary operations, such as bonding and printing. No adhesives are required and there is no waste caused by contamination with liquid color.
Now known as Beacon Engineered Solutions, Acromatic Plastics will continue to provide its customers with the high-quality products, components, services, and support that they have come to expect from this mixed-use facility. Customers will benefit from expanded molding capabilities and engineering services, as well as Beacon Engineered Solutions’ track record of success in launching custom, complex, precision-molded products and component assemblies for use across a broad range of industries and end-use applications, said Beacon in its press release.
A temperature-sensitive element can be included that monitors interruptions in the cold chain. If the temperature of the filled tube exceeds 7°C, for example, the thermo-chromic printing ink irreversibly changes in appearance.
A scale on the scratch-resistant label indicates the exact fill level, which can be relevant for insulin pen and medical measuring cup applications, for example.
The IML print-to-cut distance is only around 0.08 in. (0.2 mm) for the centrifuge tube application. With a wall thickness of only 57 micrometers, the labels must be precisely positioned in the mold cavities, and equally precisely aligned and applied. A label adjustment head equalizes the manufacturing tolerance to a few hundredths, which is an important requirement for functionality and significantly reduces quality fluctuations and rejects.
IML is standard for packaging products, but the process is rarely used in medical manufacturing, said Arburg in its announcment. The concept is all the more compelling because both the tube and label are made of polypropylene, thus promoting sustainability and adding value for customers in the pharmaceutical and medical sectors.
In the future, it is also conceivable that process, quality, and patient data for each individual part will be 100% traceable via an RFID code.
A medical in-mold labeling (IML) application will be showcased by Arburg at NPE2024. First presented at Fakuma in 2023 as a proof of concept, the compact turnkey production cell anchored by Arburg’s electric Allrounder 520 A "Ultimate" press will produce a centrifuge tube with label on the NPE show floor.
Beacon Manufacturing Group has acquired precision molder Acromatic Plastics and will make the 110,000-square-foot facility available to its Beacon MedTech Solutions business to support future growth plans. The company has also entered into a partnership agreement with Sumitomo Demag to purchase several injection molding machines, with the first two expected to be delivered in the fourth quarter of 2021.
The electric Allrounder 520 A "Ultimate" is designed for ISO Class 7 cleanroom use and has a clamping force of 165 tons (1,500 kN). The ready-to-use 15-ml PP tubes are produced in an eight-cavity mold from Kebo at an approximate 10-second cycle time. Servo-electric drives ensure precise and reproducible mold positioning in the press, and a label adjustment head from Beck ensures that the labels are precisely aligned and applied. An integrated camera system from Intravis visually inspects the finished parts in real time. In a real application, the tubes could also be screwed together and packaged in tubular bags in the production cell, added Arburg.
Editor in chief of PlasticsToday since 2015, Norbert Sparrow has more than 30 years of editorial experience in business-to-business media. He studied journalism at the Centre Universitaire d'Etudes du Journalisme in Strasbourg, France, where he earned a master's degree.
NPE2024 visitors can see the system in operation at booth W3743. The event returns to the Orange County Convention Center in Orlando, FL, on May 6 to 10.
Plans are underway to add cleanroom capacity and build out Beacon’s tooling and liquid silicone rubber (LSR) molding capabilities at the facility in Leominster, MA. This will enable Beacon MedTech to meet demand for its contract manufacturing services and precision molded products, components, and sub-assemblies for single-use and Class II medical devices and other life science applications.
“We’re committed to expanding our footprint, scale, and capabilities to support our customers’ growth and are enthused that capacity upgrades, leasehold improvements, and new equipment installations are scheduled to be completed during the first half of 2022,” said Bob May, CEO of Beacon Manufacturing Group. “At the same time, we are pleased to offer Acromatic’s customers greater access to expanded capabilities, engineering resources, and services.”
Moldmaker Kebo, in-mold labeling specialist MCC Verstraete, automation developer Beck, and vision system supplier Intravis contributed to the joint IML project.
GETTING A QUOTE WITH LK-MOULD IS FREE AND SIMPLE.
FIND MORE OF OUR SERVICES:
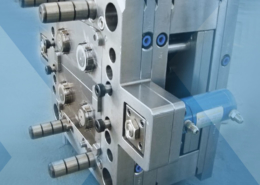
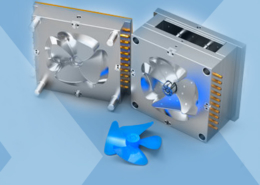
Plastic Molding

Rapid Prototyping
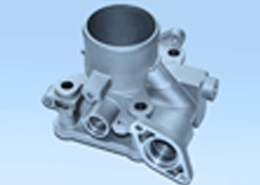
Pressure Die Casting
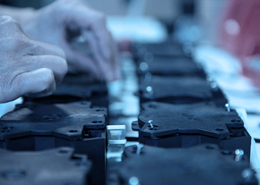
Parts Assembly
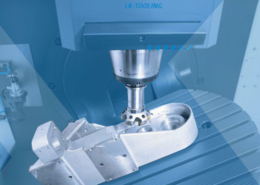