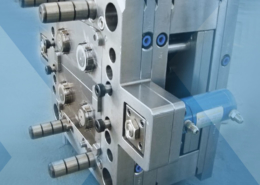
The key drivers: Injection moulding on the grow - medical plastic injection mold
Author:gly Date: 2024-09-30
Until then, click to view a video case study on Achieve Advanced PP8285E1. A large, global manufacturer highlighted the benefits of this new ICP including quality, consistency, overall performance, and reduced molding cycle times. The manufacturer also mentioned reducing weight and increasing impact resistance at low temperatures when using this material.
Using this same approach, many applications in the interior of the vehicle besides door panels can use neat ICP instead of compounded PP. This volume has been estimated at 65 pounds per vehicle based on a recent vehicle launch in North America. Using Achieve Advanced PP8285E1 instead of a compounded PP is saving the automaker approximately 5.5 pounds per vehicle.
The device costs less than $700 in materials and can be fabricated in about 24 hours. The Recyclebot produces 0.4 kg of filament per hour using 0.24 kWh of energy per kilogram produced with a diameter of ±4.6%. Thus, filament can be manufactured from commercial pellets for less than 22% of commercial filament costs. In addition, it can fabricate recycled waste plastic into filament for 2.5 cents/kg, which is around 1,000 times commercial filament costs. The system can fabricate filament from polymers with extrusion temperatures less than 250oC. These temperatures make the equipment capable of manufacturing custom filament over a wide range of thermopolymers and composites for material science studies of new materials, recyclability studies, and novel applications of fused filament-based 3D printing.
At Maker Faire 2015, Filabot displayed its offer multiple desktop solution, which allows users to extrude or pelletize recycled or new types of plastics.
One of the problems with recycling is transportation—moving post-consumer polymers from consumer to recycling location and back to the processor. 3D printing has disrupted transportation. With its ability to decentralize manufacturing, parts can be emailed and printed on location.
This is changing with the development of an ICP with greater ductility and an excellent balance of properties. Achieve™ Advanced PP8285E1 is enabling automakers to use neat ICPs in the interior of the car and take advantage of the lowest density materials in the market. This material was originally developed for use in PP compounds, but it is now finding opportunities in neat applications as automakers continue their push for weight savings.
One method of distributed plastic recycling is to upcycle plastic waste into 3D printing filament with a recyclebot, which is an open-source waste plastic extruder. Previous research on the life cycle analysis (LCA) or the recyclebot process using post-consumer plastics instead of raw materials, showed a 90% decrease in the embodied energy of the filament from the mining, processing of natural resources, and synthesizing compared to traditional manufacturing.
Achieve Advanced PP8285E1 holds promise for automakers and their Tier 1 partners who have searched for a suitable PP to broaden usage in interior trim and door panel applications. It enables automakers to take advantage of weight-saving opportunities and addresses challenges, such as ductility.
Consider how these attributes may finally open new applications for door panel lightweighting. Switching from a compounded PP for a 4-pound door panel on a sedan to this ICP would total around 1.5 pounds of weight savings per vehicle. That weight reduction becomes 150,000 pounds per 100,000 vehicles.
Some companies, such as b-pet, are even producing recycled PET filament. However, other companies are taking it a step further. ProCycler and Filabot are making desktop solutions to grind and extrude your own polymer practically anywhere. Recently, researchers at Michigan Technological University in Houghton Mich., released all the open-source files online to build a machine that can recycle polymers and turn them into filament.
Additionally, there are several examples of commercialized recycled filament (e.g., Filamentive, Fila-cycle, and Refil). However, most filament research, as well as production, is still accomplished with large-scale extruders inappropriate for distributed recycling. These systems range from $6,000 to tens of thousands of dollars for manufacturing-level extrusion lines that can produce a few kg/hr.
The US auto industry sold nearly 15 million cars and light trucks in 2020, according to Statistica. Imagine the improved vehicle efficiency if neat ICPs were used in all viable interior trim applications.
Lower density (0.90 versus a typical density of 0.98 for compounded PP) and therefore lower weight relative to compounds found in automotive interiors
PP impact copolymers (ICPs) are widely used for many of these applications due to the need for excellent impact resistance. The question has been though: “Should I select a compounded or a neat ICP for my part design?”
Lightweighting is an ongoing need in the automotive industry, and plastics continue to play a key role for innovations in internal combustion engine (ICE) vehicles as well as electric vehicles (EVs). Whether the goal is to improve ICE fuel economy or to extend EV range, reduction of vehicle weight is a key enabler.
To see the full Michigan Technological University paper, click here. To contact Joshua Pearce from the university’s Department of Material Science and Engineering, e-mail him at [email protected]. In 2015, worldwide plastic production was 322 million tons per year and is growing 3.86%/year. Both landfilling and incineration of plastic create well-established health and environmental issues. Rather than follow a linear model of materials use, a circular economy model can be used to provide sustainability by separating economic growth from resource consumption. Thus, recycling is now established in the circular economy as the optimum treatment of post-consumer plastics.
Enhanced molding due to a higher melt index of thirty (i.e., melt-flow rate flow rate of 30 g/10 min) vs. the industry standard of twenty - this allows lower pressures, reducing injection molding machine tonnage requirements, and can reduce parting line flash for higher finished product quality
Brian Dujardin, Customer Application Development with ExxonMobil Product Solutions Company, has been with the company for 23 years. His experience includes OEM and supplier support, problem-solving, and process optimization; assembling multi-lot certifications for polypropylene and polyethylene materials; and injection molding prototyping, mold making, and production.
You can download data sheets (like this one) but beware, test methods vary from vendor to vendor. It is not straightforward to conduct a true “apples to apples” comparison, particularly for cold-temperature impact testing. Therefore, a real-world test is where the proverbial rubber meets the road: Get pellets into the hands of suppliers and molders, and have them produce test parts to see how well the material performs.
However, the feedstock must be shipped. If you could find a decentralized feedstock or polymer, you could eliminate transportation. This brings things full circle: There is plastic waste almost everywhere, and a 3D printer that uses plastic to make practically anything. All that is missing is something to turn waste plastic into filament.
With the focus on producing and recycling polymers for research or lab use, researchers explore the full potential of distributed recycling of post-consumer polymer waste. The university paper describes a research-grade recyclebot, which is a waste plastic extruder capable of making commercial quality 3D printing filament. The device design takes advantage of both the open-source hardware methodology and the paradigm developed by the open source self-replicating rapid prototyper (RepRap) 3D printer community. Specifically, this paper describes the design, fabrication, and operation of a RepRapable Recyclebot, which can provide the filament needed to largely replicate itself.
Automotive design engineers have achieved lightweighting success with polypropylene for decades, but large interior panels present ongoing challenges. A new PP impact copolymer from ExxonMobil with greater ductility, high flow, and scratch resistance presents a solution.
The benefit of making your own is the ability to control and change more properties. The paper released from the university mentions that small extruders on the market, as well as the freely posted designs, suffer from one or more of the following deficiencies:
This new advanced ICP can help engineers design large, lighter-weight panels that perform well, and in a cost-effective manner versus compounded PP. Features include:
In addition, the recyclebot provides the potential for consumers to recycle plastic in their own homes to save money by offsetting purchased filament. Recyclebots are also useful for laboratory and industry prototyping research, as failed prototypes are recycled into filament for future work. There have been many versions of recyclebot developed by both companies (e.g., Filastruder) as well as individuals (e.g., Lyman), including open-source versions from the Plastic Bank, Precious Plastic, and Perpetual Plastic. There are also several commercial versions of the recyclebot, including the Filastruder, Filafab, Noztek, Filabot, EWE, Extrusionbot, Filamaker (which also has a shredder), Strooder, and Felfil (OS), that can work with waste plastic.
Production of the ProtoCycler, which is capable of grinding and re-extruding plastics for 3D printing, began after a successful crowd-sourcing campaign.
The history of automakers’ efforts to use neat ICPs for lightweighting large and complex parts has historically had mixed success. Some early efforts were abandoned in favor of compounded PP, while others returned to the material for value-oriented vehicles. Today, automakers are scattered across both camps. However, this new ICP has made an enormous difference in the industry and more door panels are indeed rolling off production lines using this higher performing material.
Designers have been searching for ways to reduce the weight of a vehicle without sacrificing performance. The interior of a car is the perfect place to look at providing weight savings, with so many parts produced from PP: instrument panels, door panels, pillars, quarter trim panels and lift gates.
Factors such as material performance, manufacturing/machinability, look-and-feel of the part, cost, and more all must be balanced to select the right material. Even though neat PP, as the lowest density option, provides the greatest weight savings, it hasn’t always been able to meet the demands of these more challenging applications. This has led designers to select compounded PP materials, typically with talc, which increases the density and therefore the weight of the part.
ABS is one of the more popular filaments used in 3D printing, and its processing temperatures are similar to PET. There are more factors that will need to be considered when printing with the different materials. Depending on the grade of material, or the condition of the recycled polymer, the melt temperatures could vary along with their melt flow index.
If you have a 3D printer, not only do you probably have failed prints and prints that are no longer needed, but there are probably some plastic bottles around you. Most plastic produced in the U.S. is Polyethylene Terephthalate (PET), also known as plastic #1. This material is easy to find, and can be used in some 3D printers.
It should be apparent to most people that while plastics are great to design with, they’re hard on the environment. While the U.S. has started recycling programs, the amount of plastic produced every year overshadows what gets recycled. In addition, energy is needed to collect and process materials, which can impede on overall benefit to recycling. Single-use plastics are particularly damaging. Resources and energy for a water bottle, party cup, etc. goes into the trash or back into the recycling stream, while only being used for a single drink. This has led to multiple researchers, engineers, and Makers to look for a better solution.
Higher ductility versus standard ICPs, which allows the door panel and interior trim parts to pass airbag deployment and other real-world impact testing performed by automakers
Unfortunately, there can be significant environmental impacts from the collection and transportation of relatively low-density waste plastics to collection centers and reclamation facilities for separation and reconstruction in traditional recycling. In addition, in developing regions (and even in some developed economies) the labor for this recycling is provided by waste pickers, who collect post-consumer plastic in landfills, among other places, far below poverty-level wages. To reduce the embodied energy of transportation needed for centralized recycling, while at the same time potentially improving the financial situation of waste pickers, a distributed recycling paradigm has been proposed.
Plastics, therefore, remain front and center in the search for new and better lightweighting solutions. Today, plastics represent about 50 percent of the volume of a vehicle but only account for 10 percent of total weight, according to the American Chemistry Council. Even after decades of innovation however, there remain new challenges and new frontiers to cross. Polypropylene (PP) resins, whether used in compounds or “neat” (i.e. no fillers added), provide a prime example of these new solutions and frontiers.
Studying mechanical engineering at Rochester Institute of Technology (RIT), he worked in the Polymer Research Lab. Utilizing RIT’s co-op program Jeff worked for two aerospace companies focusing on drafting, quality, and manufacturing for aerospace fasteners and metallurgy. He also studied abroad living in Dubrovnik, Croatia. After college, he became a commissioning engineer, traveling the world working on precision rotary equipment. Then he attended a few masters courses at the local college, and helped an automation company build equipment.
Growing up in Lancaster County, PA he always liked to tinker, build, and invent. He is ecstatic to be at Machine Design Magazine in New York City and looks forward to producing valuable information in the mechanical industry.
GETTING A QUOTE WITH LK-MOULD IS FREE AND SIMPLE.
FIND MORE OF OUR SERVICES:
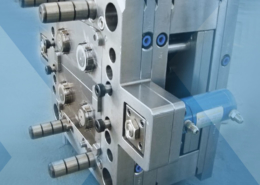
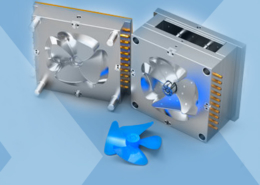
Plastic Molding

Rapid Prototyping
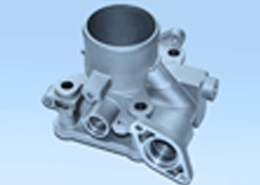
Pressure Die Casting
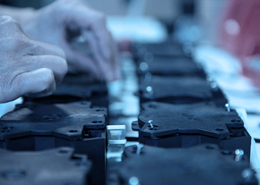
Parts Assembly
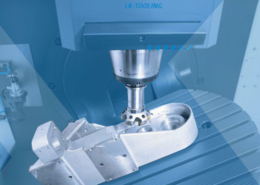