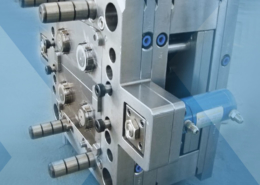
The effect of polytetrafluoroethylene particle size on the properties of
Author:gly Date: 2024-09-30
Ghost Studio has invested a lot of effort and energy in engineering and fabricating the molds for Wyrd Miniatures. They've developed a means of fixturing these inserts in the CNC machines to allow for precision machining of the cores and cavities.Wyrd
"It's exciting to see how freeform and talented designers are pushing the limits of detail, in ever smaller and smaller formats. Even more compelling is the savings in time that Wyrd Miniatures' work with Ghost Studio was able to realize, by creating molds directly from Freeform's digital files," said Joan Lockhart, vice president of marketing for Geomagic.
No issues with curing seen, we have used a few different water soluble filaments, and have used PLA PETG and TPU and all have worked great. Resin style printers though we’ve used as well and those have lots of issues around inhibition of the silicone curing. Surprisingly the water washable SirayaTech works okay.
"For example, one part needed to be altered significantly, but because we've achieved this level of precision, we can weld up cavity that was wrong, mount it on the fixture in the milling machine, and re-cut the cavity without skipping a beat," Sivy said. "It's nothing magical, but the degree of refinement that has been accomplished means that each step of the process is totally under our control. We've done some pretty incredible stuff."
While it’s the ideal choice for mass production, injection molding is simply no good for prototyping. The molds are expensive and time-consuming make, so unless you’ve got the funding to burn tens of thousands of dollars on producing new ones each time you make a tweak to your design, they’re the kind of thing you don’t want to have made until you’re absolutely sure everything is dialed in and ready. So how do you get to that point without breaking the bank?
Did you ever finish yours? Because for this “more primitive process” that you call “sucky”, they’ve not only finished, but fully documented the process.
How cool is this… Print a mold and dissolve it in water to reveal the produced item. Print using different materials so that some of it becomes part of the end product. Record the process using a mobile phone you keep in your pocket and upload it to Youtube for everyone to see. Share your knowledge so that everyone benefits from it.
By using our website and services, you expressly agree to the placement of our performance, functionality and advertising cookies. Learn more
Wyrd has been able to streamline the process at the warehouse for inspection and quality control, and also realizes cost savings in shipping since the plastic figures - molded using HIPS with some sections molded from ABS - weigh less than the metal products.
That’s not always an easy question, but if you’re working with silicone parts, the team at OpenAeros thinks they might have a solution for you. As demonstrated through their OpenRespirator project, the team has developed a method of 3D printing single-use molds suitable for large silicone parts that they’re calling Digital-to-Silicone (D2S).
STL allows for the creation of the "intense detail" of the micro-features of these characters, which typifies the value of digital sculpting that drives better quality products in an advanced all-digital manufacturing workflow using Geomagic. Geomagic says it differs from CAD in that it offers specific products to create 3D content from imaging the real world and real people, while also verifying dimensional quality by comparing a master design to as-built products, and simulating touch sensations in digital environments.
No-flash family moldsDigital sculpting with Freeform also allowed Wyrd to get to market at least one-third faster and produce the miniatures in plastic, avoiding the approximately 80% increase in the cost of white metal over the past two years. The Freeform 3D design file now serves as the foundation of a streamlined and far more accurate plastic injection manufacturing process. Details are crisper, surface finishes are smoother, and the plastic allows better paint adherence. The precision fit of the molds' core/cavity parting lines all but eliminates the parting line flash that typically appears after molding.
The move to digital sculpting with Geomagic's Freeform 3D modeling software allowed Wyrd to deliver "exceptional detail that was previously not possible to achieve in metal figurines - detail that exactly reproduces and in some cases exceeds the detail in the original line art, even for intricately detailed miniatures such as Hungering Darkness and the windswept Miss Terious."
Another thing to note is that in addition to PETG we also printed PCL (polycaprolactone) in situ and then molded silicone over this. PCL is a very interesting polymer as it has some nice material properties and is heat moldable with hot water (you can put a piece of PCL in some warm water – it will become soft and pliable and you can mold it into whatever shape you want) .
As an added bonus, the video also goes over their method of prototyping pleated filters with 3D printed forms. After inserting the filter media, snap-in arms push it down into the valleys of the form to create the pleats. These are held in place with the addition of small metal rods that are attracted to the magnets embedded into the form. Once the top and bottom of the form have been closed over the filter, silicone is injected to create a ring around the filter and lock everything into place.
In this process – we were able to print PCL in place in certain parts of the mold and have it come out in the finished part (in this case the nose “wire” of the respirator) The finished part can then be dipped in hot water by the end user and molded to their preference/comfort.
With this more primitive process, you have to actually fill the stupid thing with injected silicone, which is kinda sucky because it’s a fiddly manual process and you have to avoid leaving voids. When you print the support PVA, the TPU, and the hard plastic simultaneously you also don’t need to worry about having access to inject the silicone. You do still need to worry about connectivity for water though. No random chunks of isolated PVA in the middle of the print, much like voids filled of resin in resin printing.
In the video below, [Aaron] and [Jon] explain that they started off by simply printing injection molds in the traditional style. This worked, but the molds can get quite complex, and the time and effort necessary to design and print them wasn’t a great fit for their iterative development cycle. They wanted to be able to do from design to prototype in a day, not a week.
The basic idea was to take your 3D print, composed of a collection of files specifying the materials for it’s multiple parts (really, what parts should be silicone/TPU and what part should be hard plastic) and import them into something like OpenSCAD. There a script can run morphology operations to combine those two sets of shapes together, generate overmoulding around them that will be printed in dissolvable PVA, and then supbtract them from the overmoulding. Because printing straight TPU or other flexible filaments sucks, as the moving printhead tends to disturb it, the idea was to always have the TPU you were printing be supported and contained inside a shell of overmoulded PVA. Then you could print it like normal plastic along with all the solid bits, and when the print was done just toss it in the bathtub with no further processing required.
The molds are family molds in which all the parts needed to build the character are on a single runner, explained George Sivy, a principle with Ghost Studio, the product design firm that did the production workflow for Wyrd Miniatures, in an interview with PlasticsToday. "We use 4x6 runner configurations or 8x6 runner configurations, and maintain consistency in the runner size to facilitate packaging. These figures within a 6x8 runner configuration typically contain figurines for the Malifaux line. Others we've done have as many as 12 figurines on a runner because the figures are smaller."
They then took this concept a step further. Thanks to the multi-material capabilities offered by some of the latest 3D printers, it’s possible to print structures within the mold. Once the silicone is injected, these structures can become part of the finished part. For the OpenRespirator, this lets them add PETG stiffening rings around where the filters to snap into the silicone mask body.
$1 billion dollar fantasy industryWith an estimated $1 billion worldwide market for fantasy "war games" - where hobbyists assemble and paint miniatures and then play battle games with friends and in tournaments - character detail can make the difference between a game's appeal alongside other boxed sets.
It used to take from 90 to 120 days to move from design to manufactured part for a typical toy, but one company has found a way to manufacture their character figures in "far less time and achieve levels of detail that were difficult if not impossible to obtain in the past." The new miniature character figures from Wyrd (pronounced 'weird') Miniatures debuted at the recent Gen Con, touted as the world's largest gaming show and featured miniatures for its hit character skirmish game "Malifaux".
Until she retired in September 2021, Clare Goldsberry reported on the plastics industry for more than 30 years. In addition to the 10,000+ articles she has written, by her own estimation, she is the author of several books, including The Business of Injection Molding: How to succeed as a custom molder and Purchasing Injection Molds: A buyers guide. Goldsberry is a member of the Plastics Pioneers Association. She reflected on her long career in "Time to Say Good-Bye."
Recently I just started with a similar idea, but it was printing in polymer clay, completely forgot about dissolvable filaments, seems a lot easier than a custom printer, only concern would be cure inhibition, was any of that seen?
Today, using Geomagic's Freeform, Wyrd is moving from design to finished parts for five characters on one sprue in near-record time.
While the aesthetics are… okay… I really like the design and the thoughts that went into it. I use 3M’s on a daily basis, because I suck at keeping re-usables clean. But from an ecological perspective I should really reconsider especially when seeing this project ❤️
I didn’t even know you could get PCL in filament form, that is really useful to know, such a handy plastic. Is it a pain to print with? Seems like with how very low its melt temp is and how much heat it holds part cooling at least would be challenging.
It used to take from 90 to 120 days to move from design to manufactured part for a typical toy, but one company has found a way to manufacture their character figures in "far less time and achieve levels of detail that were difficult if not impossible to obtain in the past." The new miniature character figures from Wyrd (pronounced 'weird') Miniatures debuted at the recent Gen Con, touted as the world's largest gaming show and featured miniatures for its hit character skirmish game "
Razor-sharp parting linesAs most mold manufacturers know, family molds can be tricky to fill, but Sivy noted that the company has the ability to regulate how these cavities fill, to the extent that they can eliminate shrink, swirls and flash. "That literally took us a few years of experimenting with software programs to address the various downstream processes," he said. "We digitally create the mold splits to give us a razor-sharp edge in how they match up. These sharp parting lines eliminate flash."
Back in like 2015 or 2016 I started working on a more advanced version of this, which I called the “3M” or “3 Materials” concept. Yes, it was a play on words for the 3M “1 megapixel, 1 megabyte, 1 megapenny” unix workstations.
We often think of 3D printing as ideal for prototyping, but usually in a very direct and obvious way. You print out a part to see if it works the way you want, and then take the design and have it made out of something stronger. But this presentation from OpenAeros shows just how versatile the technology can be. With even a half-way decent desktop printer, the potential time and cost savings can be enormous. Something to keep in mind should one of your side projects turn into something bigger.
It prints okay, our process settings for the Prusa are included in the documentation. We have been capsulating it in the silicone, so it doesn’t have to be such a beautiful print. In general though it’s not too hard to print though, and has really great material properties that are hard to get from other plastics.
WyrdWyrd and its product design firm, Ghost Studio, relied on the Freeform 3D modeling from Geomagic to digitally sculpt 40 miniatures for six new box sets. They then used the digital designs as the basis of a streamlined digital manufacturing process that moves from art to production tooling via STL milling. People familiar with stereolithography in additive manufacturing might be familiar with STL, which uses triangular facets that are able to represent just about any freeform shape.
Wyrd"Characters are the soul of the game, which is why we call Malifaux a character-based game. Ghost Studio has helped us bring our characters to life, with detail and dynamic poses that weren't possible for us before," said Nathan Caroland, co-owner of Wyrd Miniatures, based in Kennesaw, GA. "The digital sculpting done with Freeform, when paired with the capabilities of plastic, lets us create miniatures that closely match the details and animation of the original artwork, making our miniatures stand out. Our customers are excited about the new poses and the intricacies of our new releases, and we hope that we're raising the bar for all miniatures by focusing on quality through Freeform."
Eventually they realized that if they printed the mold out of a water-soluble filament, they could simplify its design greatly. They’ve documented the design process in detail, but the short version is that you essentially subtract the 3D model of the design you want to produce from a solid shape in your CAD package, and add a few holes for injecting the silicone. Once the silicone has cured, the mold can be dissolved away in warm water to reveal the finished part.
GETTING A QUOTE WITH LK-MOULD IS FREE AND SIMPLE.
FIND MORE OF OUR SERVICES:
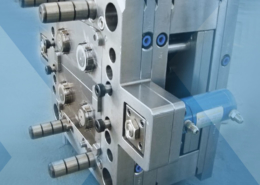
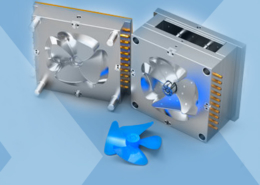
Plastic Molding

Rapid Prototyping
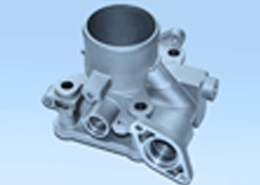
Pressure Die Casting
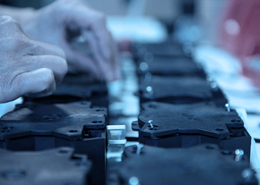
Parts Assembly
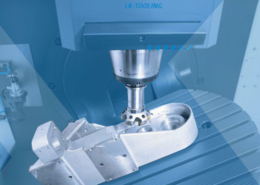