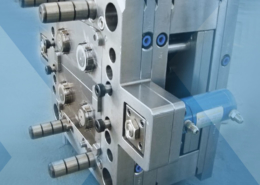
The Best Ice Cube Tray of 2024 | Reviews by Wirecutter - making plastic molds at
Author:gly Date: 2024-09-30
Additive technology creates air pockets in film during orientation, cutting down on the amount of resin needed while boosting opacity, mechanical properties and recyclability.
Mixed in among thought leaders from leading suppliers to injection molders and mold makers at the 2023 Molding and MoldMaking conferences will be molders and toolmakers themselves.
“The machines are much better now,” Ernsberger notes. “They may look the same as they did 30 years ago, but the hydraulics, electrics, and controls are so much improved. The same part I ran in the late ’80s at 160 sec, ran in the ’90s at 145 sec and runs now at 75 sec.”
Discover how artifical intelligence is revolutionizing plastics processing. Hear from industry experts on the future impact of AI on your operations and envision a fully interconnected plant.
The 20/20 plant today has five Uniloy dedicated structural-foam presses of 500, 1000, and 1500 tons, plus four Milacron injection machines of 375 and 725 tons. The latter have oversized barrels (165 and 288 oz, respectively) so they can be used for foam or for solid injection molding of handles, fasteners, and other attachments to be assembled with foam parts.
In addition, new technology was recently announced by Norsdson Xaloy (New Castle, Pa.) for more energy-efficient heating of injection barrels, nozzles, and melt pipes (see Keeping Up section).
Mold maintenance is critical, and with this collection of content we’ve bundled some of the very best advice we’ve published on repairing, maintaining, evaluating and even hanging molds on injection molding machines.
Multiple speakers at Molding 2023 will address the ways simulation can impact material substitution decisions, process profitability and simplification of mold design.
In this collection, which is part one of a series representing some of John’s finest work, we present you with five articles that we think you will refer to time and again as you look to solve problems, cut cycle times and improve the quality of the parts you mold.
Plastics Technology’s Tech Days is back! Every Tuesday in October, a series of five online presentations will be given by industry supplier around the following topics: Injection Molding — New Technologies, Efficiencies Film Extrusion — New Technologies, Efficiencies Upstream/Downstream Operations Injection Molding — Sustainability Extrusion — Compounding Coming out of NPE2024, PT identified a variety of topics, technologies and trends that are driving and shaping the evolution of plastic products manufacturing — from recycling/recyclability and energy optimization to AI-based process control and automation implementation. PT Tech Days is designed to provide a robust, curated, accessible platform through which plastics professionals can explore these trends, have direct access to subject-matter experts and develop strategies for applying solutions in their operations.
Hunerberg says 600 hp is pretty much the limit for a 6-in. extruder. But Uniloy has built 8-in. extruders with 1000 hp, “monsters” capable of 5500 lb/hr apiece, more than twice the output of dual 6-inchers. Another improvement would be a screw design optimized for a specific material, though that may not be a convenient solution for a custom molder.
The issue is monomer inventory tightness which may last for another couple of months. Moreover, on-purpose propylene suppliers have PDH units scheduled for turnarounds in January, and are actively looking for propylene imports, according to PCW’s Barry, who describes the scenario as a pretty dynamic supply situation. This not an issue for PP where demand has continued to struggle, despite an uptick in demand in August that was largely attributed to prebuying activity, notes Spartan Polymers’ Newell.
While prices moved up for three of the five commodity resins, there was potential for a flat trajectory for the rest of the third quarter.
Ernsberger also says he is concerned about energy costs. “My 500-tonner consumes more energy than a 1500- or even 2500-ton injection press because of all the heating on the extruders, accumulators, fill pipes, and manifolds.” Hunerberg replies that Uniloy machines already use electric variable-speed screw drives, hydraulic accumulators, and variable-volume pumps to minimize energy consumption. But he foresees that in the next two years Uniloy’s next generation of machines will adapt electric servo-driven pumps to save additional energy, as is already the case for injection machines.
Across all process types, sustainability was a big theme at NPE2024. But there was plenty to see in automation and artificial intelligence as well.
Plastics Technology’s Tech Days is back! Every Tuesday in October, a series of five online presentations will be given by industry supplier around the following topics: Injection Molding — New Technologies, Efficiencies Film Extrusion — New Technologies, Efficiencies Upstream/Downstream Operations Injection Molding — Sustainability Extrusion — Compounding Coming out of NPE2024, PT identified a variety of topics, technologies and trends that are driving and shaping the evolution of plastic products manufacturing — from recycling/recyclability and energy optimization to AI-based process control and automation implementation. PT Tech Days is designed to provide a robust, curated, accessible platform through which plastics professionals can explore these trends, have direct access to subject-matter experts and develop strategies for applying solutions in their operations.
Pavlov notes that the supply situation improved significantly between second and third quarter, with days of supplier inventories now at 14-to-16 days, and domestic demand not as strong as expected. Also, more new capacity was being brought on stream by Formosa though a debottleneck. “We’re exporting more PVC this year than in 2022,” Pavlov says.
Plastics Technology covers technical and business Information for Plastics Processors in Injection Molding, Extrusion, Blow Molding, Plastic Additives, Compounding, Plastic Materials, and Resin Pricing. About Us
The pipe and fittings manufacturer’s new 200,000-square-foot facility represents a $200 million investment and will create 150 jobs.
The Plastics Industry Association (PLASTICS) has released final figures for NPE2024: The Plastics Show (May 6-10; Orlando) that officially make it the largest ever NPE in several key metrics.
Say “manufacturing automation” and thoughts immediately go to the shop floor and specialized production equipment, robotics and material handling systems. But there is another realm of possible automation — the front office.
Say “manufacturing automation” and thoughts immediately go to the shop floor and specialized production equipment, robotics and material handling systems. But there is another realm of possible automation — the front office.
In addition, recent major industry news involves the pausing of construction to the 2.6-million lb/yr PET plant in Corpus Christi, Texas, with partners Alpek, Indorama and FENC (Far Eastern New Century). It was originally scheduled to start up in 2025. Construction costs, interest rates and labor shortages are factors.
“We have some ideas of our own on how to customize new machines. We want to increase our plant’s lb/hr throughput by 20% with the same number of presses.”
Learn about sustainable scrap reprocessing—this resource offers a deep dive into everything from granulator types and options, to service tips, videos and technical articles.
While prices moved up for three of the five commodity resins, there was potential for a flat trajectory for the rest of the third quarter.
Polypropylene prices moved up 4.5¢/lb in September in step with propylene monomer, primarily attributed to unplanned and planned monomer production issues, according to PCW’s Barry, Spartan Polymers’ Newell and The Plastic Exchange’s Greenberg. This after dropping 0.5¢/lb in August for a decline of 19.5¢/pound since first quarter. Prices were expected to be flat in October, but unclear going into this month and next, and pretty much dependent on the monomer’s price stability.
Noting that there was a short-squeeze of domestic benzene supply, Barry says, “I think it will be a tough sell for suppliers to get all 8¢/lb, as the majority of PS market operates on feedstock cost formulation. There is not much activity in the secondary market and imports are down 24% from September 2022 year-to-date.” Similarly, Chesshier ventures that PS prices this month and December will see a gradual decline as benzene is currently overvalued.
August 29-30 in Minneapolis all things injection molding and moldmaking will be happening at the Hyatt Regency — check out who’s speaking on what topics today.
And business has been good. His plant has expanded several times from an initial 40,000 ft2 to its current 185,000 ft2, and another 165,000-ft2 expansion is underway for warehousing and secondary operations like decorating and assembly. The plant runs 24/7 and, at 85-90% capacity utilization, is pretty much fully booked. “Lots of new things are going on, new molds being built, sample trials running. Our customer base is active and busy,” says Ernsberger. “We have one new customer that will be in our top 10 this year.”
Additive technology creates air pockets in film during orientation, cutting down on the amount of resin needed while boosting opacity, mechanical properties and recyclability.
Discover how artifical intelligence is revolutionizing plastics processing. Hear from industry experts on the future impact of AI on your operations and envision a fully interconnected plant.
Join Engel in exploring the future of battery molding technology. Discover advancements in thermoplastic composites for battery housings, innovative automation solutions and the latest in large-tonnage equipment designed for e-mobility — all with a focus on cost-efficient solutions. Agenda: Learn about cutting-edge thermoplastic composites for durable, sustainable and cost-efficient battery housings Explore advanced automation concepts for efficient and scalable production See the latest large-tonnage equipment and technology innovations for e-mobility solutions
Sodick Plustech’s VR-G and MS-G2 Series both utilize the company’s proprietary V-Line technology, separating plasticizing and injection functions, and have upgraded displays, energy efficiency, response time and more.
Processors with sustainability goals or mandates have a number of ways to reach their goals. Biopolymers are among them.
Mike Sepe has authored more than 25 ANTEC papers and more than 250 articles illustrating the importance of this interdisciplanary approach. In this collection, we present some of his best work during the years he has been contributing for Plastics Technology Magazine.
This month’s resin pricing report includes PT’s quarterly check-in on select engineering resins, including nylon 6 and 66.
Baystar's Borstar technology is helping customers deliver better, more reliable production methods to greenhouse agriculture.
Formerly a showroom for early-aughts-era Van Dorn hydraulics, the newest additions to Drummond Industries’ transforming fleet are all-electric Niigata injection molding machines.
Multiple speakers at Molding 2023 will address the ways simulation can impact material substitution decisions, process profitability and simplification of mold design.
Ernsberger cites two keys to 20/20’s success. “The first is our knowledgeable, experienced people.” Most are long-timers with the company. It’s very hard to find people with any foam experience, he says. “It’s hard to find people who can pronounce ‘polyethylene,’ let alone ones who know how to mold structural foam.”
Join Engel in exploring the future of battery molding technology. Discover advancements in thermoplastic composites for battery housings, innovative automation solutions and the latest in large-tonnage equipment designed for e-mobility — all with a focus on cost-efficient solutions. Agenda: Learn about cutting-edge thermoplastic composites for durable, sustainable and cost-efficient battery housings Explore advanced automation concepts for efficient and scalable production See the latest large-tonnage equipment and technology innovations for e-mobility solutions
Exhibitors and presenters at the plastics show emphasized 3D printing as a complement and aid to more traditional production processes.
While the melting process does not provide perfect mixing, this study shows that mixing is indeed initiated during melting.
“People who come into this from injection molding are overwhelmed by the number of pounds these machines can put out,” he adds. His 1500-tonner has dual 6-in., 600-hp extruders, each of which can plasticate 2400 lb/hr. “Full out, our plant will use 15,000 lb/hr with just nine machines.” He commonly runs two different materials in the two extruders of the same press—such as PP and PE or PS and ABS.
Take a deep dive into all of the various aspects of part quoting to ensure you’ve got all the bases—as in costs—covered before preparing your customer’s quote for services.
This month’s resin pricing report includes PT’s quarterly check-in on select engineering resins, including nylon 6 and 66.
Core Technology Molding turned to Mold-Masters E-Multi auxiliary injection unit to help it win a job and dramatically change its process.
Formnext Chicago is an industrial additive manufacturing expo taking place April 8-10, 2025 at McCormick Place in Chicago, Illinois. Formnext Chicago is the second in a series of Formnext events in the U.S. being produced by Mesago Messe Frankfurt, AMT – The Association For Manufacturing Technology, and Gardner Business Media (our publisher).
Structural foam is a niche, and will remain so—Ernsberger and Uniloy’s Hunerberg agree on that. Although it competes with solid injection molding for larger, heavier parts, structural foam enjoys several advantages. “I can do on a 500-ton press what an injection molder needs 2500 tons to do,” says Ernsberger. “You can’t mold four pallets at once by injection molding”—not without a mammoth machine. He routinely runs parts weighing 9 to 15 lb, and one job is 168 lb. His largest press has 200-lb shot capacity and platens 162 in. wide x 107 in. high. One job involves molding 16 eight-ft-long parts in a single mold.
In this collection, which is part one of a series representing some of John’s finest work, we present you with five articles that we think you will refer to time and again as you look to solve problems, cut cycle times and improve the quality of the parts you mold.
Ultradent's entry of its Umbrella cheek retractor took home the awards for Technical Sophistication and Achievement in Economics and Efficiency at PTXPO.
“About six months after I got into this business, I wondered if I had made a big mistake. But then the light came on, and I got it.” That light has burned brightly for Ron Ernsberger, founder and president of 20/20 Custom Molded Plastics, Ltd. in Holiday City, Ohio. In the 14 years since he started the custom structural-foam molder in 1999, it has grown to a $30+ million-dollar business employing 140.
THINNER CUSTOM RANKS From around a dozen custom structural-foam molders in the U.S. when 20/20 started up, the custom ranks have shrunk to single digits, Ernsberger says. Some were acquired by captive molders, which constitute a majority of the foam business, according to Hunerberg.
Baystar's Borstar technology is helping customers deliver better, more reliable production methods to greenhouse agriculture.
What he wants from the machinery suppliers today is higher output. “What any foam molder wants is more lb/hr. We started with 115-hp extruders; in ’93 we went to 400 hp and I thought that’s all I would ever need. We have 600 hp today and that’s not enough.
The other key factor in 20/20’s success, Ernsberger says, is his equipment. “When I started there was no good used machinery available. I was lucky. I had to buy new machines, so I got the latest technology and my maintenance cost was zero.” Now his machines are turning 10 years old. “We take good care of them.”
While prices moved up for three of the five commodity resins, there was potential for a flat trajectory for the rest of the third quarter.
Ultradent's entry of its Umbrella cheek retractor took home the awards for Technical Sophistication and Achievement in Economics and Efficiency at PTXPO.
Thousands of people visit our Supplier Guide every day to source equipment and materials. Get in front of them with a free company profile.
Despite price increase nominations going into second quarter, it appeared there was potential for generally flat pricing with the exception of a major downward correction for PP.
When, how, what and why to automate — leading robotics suppliers and forward-thinking moldmakers will share their insights on automating manufacturing at collocated event.
Join Wittmann for an engaging webinar on the transformative impact of manufacturing execution systems (MES) in the plastic injection molding industry. Discover how MES enhances production efficiency, quality control and real-time monitoring while also reducing downtime. It will explore the integration of MES with existing systems, emphasizing compliance and traceability for automotive and medical sectors. Learn about the latest advancements in IoT and AI technologies and how they drive innovation and continuous improvement in MES. Agenda: Overview of MES benefits What is MES? Definition, role and brief history Historical perspective and evolution Longevity and analytics Connectivity: importance, standards and integration Advantages of MES: efficiency, real-time data, traceability and cost savings Emerging technologies: IoT and AI in MES
PET prices rolled over in September (based on raw material formulation contracts), having moved up in August by 3¢/lb, and prices may have possibly peaked this year, according to Mark Kallman RTi’s v.p. of PVC, PET and engineering resins. Moreover, he sees the potential for a 1¢ to 2¢/lb, give or take for October-November. “This remains a well-supplied market with substantial competitive priced imports. So far, imports account for a $250 million/lb versus $40 million/lb that primarily go to Canada.”
After successfully introducing a combined conference for moldmakers and injection molders in 2022, Plastics Technology and MoldMaking Technology are once again joining forces for a tooling/molding two-for-one.
Ernsberger doesn’t mind that the technology has spread to at least seven other countries, including China, Taiwan, Latin America, Russia, and the Middle East. He doesn’t worry about overseas competition because structural-foam parts tend to be too large and heavy to be shipped economically over long distances.
Formnext Chicago is an industrial additive manufacturing expo taking place April 8-10, 2025 at McCormick Place in Chicago, Illinois. Formnext Chicago is the second in a series of Formnext events in the U.S. being produced by Mesago Messe Frankfurt, AMT – The Association For Manufacturing Technology, and Gardner Business Media (our publisher).
In fact, 20/20 has cooperated with Uniloy to train several companies—three domestic and two foreign—in the ways of structural foam. “When I got into this industry, everyone kept to themselves, didn’t want to help other molders, didn’t want to share knowledge. They were so afraid someone would steal something from them. I’ve tried to change this culture, because if a new guy gets into structural foam and doesn’t know what he’s doing, he could give all of us a black eye.”
Mold maintenance is critical, and with this collection of content we’ve bundled some of the very best advice we’ve published on repairing, maintaining, evaluating and even hanging molds on injection molding machines.
Another advantage of low-pressure structural foam is its ability to use aluminum molds at one-third the cost of an injection mold and with shorter lead time. Structural foam also competes in some cases with thermoforming, which enjoys even lower tool cost.
Mixed in among thought leaders from leading suppliers to injection molders and mold makers at the 2023 Molding and MoldMaking conferences will be molders and toolmakers themselves.
Besides its safety advantages, automation stabilizers and even reduces cycle times, boosting production and cutting scrap.
A collaboration between show organizer PLASTICS, recycler CPR and size reduction experts WEIMA and Conair recovered and recycled all production scrap at NPE2024.
Polystyrene prices rose by 3¢/pound in September, having risen by 3¢/lb in August, after dropping a total of 9¢/lb the two previous months, according to PCW’s Barry and RTi’s Chesshier. Moreover, PS prices in October were forecast to increase 8¢/lb, reflecting increases of a 7¢/lb in October benzene contracts that settled at $4/gallon and a 1¢/lb hike in ethylene. According to Barry, the implied styrene cost based on a 70% benzene, 30% ethylene spot formula jumped up 9.8¢/lb within a four-week period going into October.
Take a deep dive into all of the various aspects of part quoting to ensure you’ve got all the bases—as in costs—covered before preparing your customer’s quote for services.
The aim of this presentation is to guide you through the factors and the numbers that will help you determine if a robot is a smart investment for your application. Agenda: Why are you considering automation? What problems are you trying to solve? How and why automation can help Crunch the numbers and determine the ROI
Prices of the five commodity resins going into October were a mixed bag, owing to factors such as supply/demand issues, seemingly temporary spikes in some feedstocks due to primarily to unplanned production shutdowns and prebuying activity as protection to the hurricane season ending midmonth. In the case of PE and PP, unexpected outages in both feedstock and resin production resulted in some force majeure declarations. This apparently translated to drawdowns in suppliers’ PE and PP inventories which gave them the momentum to push through increases. Both PE and PP suppliers have increased operating rates primarily to serve the exports markets.
August 29-30 in Minneapolis all things injection molding and moldmaking will be happening at the Hyatt Regency — check out who’s speaking on what topics today.
That has not been a deterrent to 20/20, says Ernsberger. “For us, a long run is two or three days. We make three mold changes a day.” He says that takes from 4 hr for small parts to two days for the largest (168-lb) job. “We have it down to a science.” One key is that 20/20 has standardized its mold shut heights to simplify changeovers.
Second quarter started with price hikes in PE and the four volume engineering resins, but relatively stable pricing was largely expected by the quarter’s end.
Mike Sepe has authored more than 25 ANTEC papers and more than 250 articles illustrating the importance of this interdisciplanary approach. In this collection, we present some of his best work during the years he has been contributing for Plastics Technology Magazine.
Across the show, sustainability ruled in new materials technology, from polyolefins and engineering resins to biobased materials.
RTi’s Chesshier attributes the increases to a very strong exports market as international feedstock prices had risen and also to an uptick in domestic demand which appeared to be partially attributed to prebuying due to hurricane season. Reports The Plastic Exchange’s Greenberg, “The alternative export demand, which has been approaching 50% of all domestic PE, has helped producers secure consecutive 3¢/lb price increases in August and September. As prices rise, it has been pulling domestic buyers back to the market as they compete to restock their heavily drawn down inventories,” Greenberg reports .
Successfully starting or restarting an injection molding machine is less about ticking boxes on a rote checklist and more about individually assessing each processing scenario and its unique variables.
Polyethylene prices moved up another 3¢ in September, following the August increase, and suppliers had a similar price initiative for October, according to David Barry, PCW’s associate director for PE, PP, and PS, Robin Chesshier, RTi’s v.p. of PE, PS, and nylon 6 markets, and The Plastic Exchange’s CEO Michael Greenberg. Generally, these sources venture that prices in the October-November time frame are likely to be flat-to-down.
Join KraussMaffei for an insightful webinar designed for industry professionals, engineers and anyone interested in the manufacturing processes of PVC pipes. This session will provide a comprehensive understanding of the technology behind the production of high-quality PVC pipes: from raw material preparation to final product testing. Agenda: Introduction to PVC extrusion: overview of the basic principles of PVC pipe extrusion — including the process of melting and shaping PVC resin into pipe forms Equipment and machinery: detailed explanation of the key equipment involved — such as extruders, dies and cooling systems — and their roles in the extrusion process Process parameters: insight into the critical process parameters like temperature, pressure and cooling rates that influence the quality and consistency of the final PVC pipes Energy efficiency: examination of ways to save material and energy use when extruding PVC pipe products
PVC prices were a rollover in September, despite suppliers aiming for a 4¢/pound increase which they hoped would at least partially be implemented that month, following the August 2¢/pound increase, according to Paul Pavlov, RTi’s v.p. of PP and PVC and PCW’s senior editor Donna Todd. The latter reported that an industry pundit who forecast a partial 1¢/lb increase for September, changed the forecast to flat. It appears that suppliers aimed to remedy the situation with Westlake, Shintech and Formosa restating their increase to a 2¢/lb for October. OxyVinyls was missing, but expected to follow suit.
Resin drying is a crucial, but often-misunderstood area. This collection includes details on why and what you need to dry, how to specify a dryer, and best practices.
Join Wittmann for an engaging webinar on the transformative impact of manufacturing execution systems (MES) in the plastic injection molding industry. Discover how MES enhances production efficiency, quality control and real-time monitoring while also reducing downtime. It will explore the integration of MES with existing systems, emphasizing compliance and traceability for automotive and medical sectors. Learn about the latest advancements in IoT and AI technologies and how they drive innovation and continuous improvement in MES. Agenda: Overview of MES benefits What is MES? Definition, role and brief history Historical perspective and evolution Longevity and analytics Connectivity: importance, standards and integration Advantages of MES: efficiency, real-time data, traceability and cost savings Emerging technologies: IoT and AI in MES
Hunerberg says 20/20 is the first structural-foam molder he knows of that put robots on all its machines. He says robots have caught on with captive structural-foam molders but estimates that robots are used by only half of custom foam molders, which have shorter runs and frequent mold changes.
Plastics processors are finding applications for 3D printing around the plant and across the supply chain. Here are 8 examples to look for at NPE2024.
While the major correction in PP prices was finally underway, generally stable pricing was anticipated for the other four commodity resins.
Structural foam also benefits from unusual flexibility. Today’s multi-nozzle presses allow for up to 200 different injection points on the platen, using shutoff nozzles with independent opening and closing control. “It’s a bit like a hot-runner valve-gate system with the hot runner as part of the machine, not the mold,” explains Hunerberg. This system allows multiple injection points on one big mold, or several individual molds to be mounted on one machine. For example, one job has seven molds in one twin-barrel machine, running parts for two different customers in two different materials simultaneously.
Plastics Technology covers technical and business Information for Plastics Processors in Injection Molding, Extrusion, Blow Molding, Plastic Additives, Compounding, Plastic Materials, and Resin Pricing. About Us
This Knowledge Center provides an overview of the considerations needed to understand the purchase, operation, and maintenance of a process cooling system.
This Knowledge Center provides an overview of the considerations needed to understand the purchase, operation, and maintenance of a process cooling system.
Ernsberger and Hunerberg also agree that, in some respects, structural foam is easier to run than solid injection molding. “It’s a very forgiving process,” says Ernsberger. “You run a black foam fan shroud and it’s a lot less trouble than a crystal-clear polycarbonate part.” He notes that “the old structural-foam swirl” is not so evident on today’s parts, but adds that “we don’t do high-finish applications.” He leaves that to other foam molders that specialize in techniques like gas counterpressure.
Second quarter started with price hikes in PE and the four volume engineering resins, but relatively stable pricing was largely expected by the quarter’s end.
Exhibitors and presenters at the plastics show emphasized 3D printing as a complement and aid to more traditional production processes.
20/20 is expanding this spring to add space for warehousing and secondary operations like assembly and decorating. (Shown here: trimming a sub-frame floor for a golf cart.)
Sustainability continues to dominate new additives technology, but upping performance is also evident. Most of the new additives have been targeted to commodity resins and particularly polyolefins.
Across the show, sustainability ruled in new materials technology, from polyolefins and engineering resins to biobased materials.
When, how, what and why to automate — leading robotics suppliers and forward-thinking moldmakers will share their insights on automating manufacturing at collocated event.
The aim of this presentation is to guide you through the factors and the numbers that will help you determine if a robot is a smart investment for your application. Agenda: Why are you considering automation? What problems are you trying to solve? How and why automation can help Crunch the numbers and determine the ROI
Join KraussMaffei for an insightful webinar designed for industry professionals, engineers and anyone interested in the manufacturing processes of PVC pipes. This session will provide a comprehensive understanding of the technology behind the production of high-quality PVC pipes: from raw material preparation to final product testing. Agenda: Introduction to PVC extrusion: overview of the basic principles of PVC pipe extrusion — including the process of melting and shaping PVC resin into pipe forms Equipment and machinery: detailed explanation of the key equipment involved — such as extruders, dies and cooling systems — and their roles in the extrusion process Process parameters: insight into the critical process parameters like temperature, pressure and cooling rates that influence the quality and consistency of the final PVC pipes Energy efficiency: examination of ways to save material and energy use when extruding PVC pipe products
Learn about sustainable scrap reprocessing—this resource offers a deep dive into everything from granulator types and options, to service tips, videos and technical articles.
This month’s resin pricing report includes PT’s quarterly check-in on select engineering resins, including nylon 6 and 66.
Apart from technical needs, what Ernsberger wishes for most is more cohesiveness within the structural-foam industry. He recalls how 20 or more years ago, structural foam had a prominent presence in industry conferences. “We need to promote structural foam from within,” he says. Ernsberger himself tried to organize a structural-foam pavilion at NPE 2012 in Orlando, Fla., but that did not bear fruit. If any movement were made in the future to organize this industry sector, he says, “I would want to be a part of that.”
All three sources also noted two ongoing force majeures but also that more significant new capacity was being brought on stream by Baystar, Nova and Shell. PCW’s Barry points out that suppliers have increased export prices by about 7¢/lb, this while there were reports of softer demand in international markets as well. This was forecast to continue into 2024.
ROBOTS: THE NEW NECESSITY Some of that improved productivity is due to the arrival of robots, says Ernsberger. Starting in 2003, 20/20 was an early adopter of robots for structural foam. “Before then, I never thought robots would be a help rather than a hindrance—something that would slow you down on mold changes and setups. I didn’t want to mess with them. But then Ranger Automation Systems (Shrewsbury, Mass.) came in with the biggest robot they had ever built and asked us to try it out for free. Now we have Ranger robots on all our machines, and the two biggest (1000 and 1500 tons) have two robots on the same beam to handle multiple molds.” The robots can carry 280 lb.
Introduced by Zeiger and Spark Industries at the PTXPO, the nozzle is designed for maximum heat transfer and uniformity with a continuous taper for self cleaning.
Join this webinar to explore the transformative benefits of retrofitting your existing injection molding machines (IMMs). Engel will guide you through upgrading your equipment to enhance monitoring, control and adaptability — all while integrating digital technologies. You'll learn about the latest trends in IMM retrofitting (including Euromap interfaces and plasticizing retrofits) and discover how to future-proof your machines for a competitive edge. With insights from industry experts, it'll walk you through the decision-making process, ensuring you make informed choices that drive your business forward. Agenda: Maximize the value of your current IMMs through strategic retrofitting Learn how to integrate digital technologies to enhance monitoring and control Explore the benefits of Euromap interfaces and plasticizing retrofits Understand how retrofitting can help meet new product demands and improve adaptability Discover how Engel can support your retrofitting needs, from free consultations to execution
Across all process types, sustainability was a big theme at NPE2024. But there was plenty to see in automation and artificial intelligence as well.
“The big thing with robots is cycle-time uniformity. It eliminates the variability of a human operator. Your scrap rate goes down and productivity goes up. Adding those nine robots was like adding another machine in terms of overall productivity.”
All of 20/20’s presses are also equipped for gas-assist molding, and the firm sometimes uses that technique together with structural foam to save weight and material. In addition, Ernsberger’s Uniloy foam presses have software for structural web molding, a type of low-pressure gas-assist process that hollows out most of an unfoamed part and leaves a smooth surface.
Even with those top-entry beam robots, some jobs have up to five people working at a machine for secondary operations like trimming, assembly, and hot stamping. And 20/20 does not yet use the robots for loading inserts but probably will in the future, Ernsberger says.
20/20 Custom Molded Plastics is one of only a handful of custom structural-foam molders in the U.S., and it is busier than ever. Shown here is a 1500-ton Uniloy press with two Ranger parts-handling robots on one overhead beam. (Bottom photo: HDPE sump basins.)
While the melting process does not provide perfect mixing, this study shows that mixing is indeed initiated during melting.
20/20 was probably the first structural-foam molder to put robots on all its presses. The benefits are cycle-time uniformity, reduced scrap, and increased productivity.
Core Technology Molding turned to Mold-Masters E-Multi auxiliary injection unit to help it win a job and dramatically change its process.
In this collection of articles, two of the industry’s foremost authorities on screw design — Jim Frankand and Mark Spalding — offer their sage advice on screw design...what works, what doesn’t, and what to look for when things start going wrong.
In this collection of content, we provide expert advice on welding from some of the leading authorities in the field, with tips on such matters as controls, as well as insights on how to solve common problems in welding.
In this collection of articles, two of the industry’s foremost authorities on screw design — Jim Frankand and Mark Spalding — offer their sage advice on screw design...what works, what doesn’t, and what to look for when things start going wrong.
PP spot prices were flat to higher, despite an unexciting demand outlook for fourth quarter, according to Barry and The Plastic Exchange’s Greenberg who reported, “Polypropylene trading stayed healthy to close out September; demand picked up while monomer prices rallied as buyers sought to procure additional material ahead of a potential October increase. The supply/demand dynamic for PP is better balanced, especially as producers have begun to tap the export market with more fervor.” Meanwhile, Barry reports that Braskem confirmed the extended idling of one of the two PP trains at its Marcus Hook, Pennsylvania, facility, representing about 450 million pound/year.
Gifted with extraordinary technical know how and an authoritative yet plain English writing style, in this collection of articles Fattori offers his insights on a variety of molding-related topics that are bound to make your days on the production floor go a little bit better.
These are the views of purchasing consultants from Resin Technology Inc. (RTi), senior analysts from Houston-based PetroChemWire (PCW), CEO Michael Greenberg of The Plastics Exchange, and Scott Newell, executive v.p. polyolefins at distributor/compounder Spartan Polymers.
Gifted with extraordinary technical know how and an authoritative yet plain English writing style, in this collection of articles Fattori offers his insights on a variety of molding-related topics that are bound to make your days on the production floor go a little bit better.
In a time where sustainability is no longer just a buzzword, the food and beverage packaging industry is required to be at the forefront of this innovation. By adopting circular packaging processes and solutions, producers can meet regulatory requirements while also satisfying consumer demand and enhancing brand reputation. Join Husky to learn more about the broader implications of the circular economy — as well as how leading brands are leveraging this opportunity to reduce costs, increase design flexibility and boost product differentiation. Agenda: The cost and operational benefits of embracing circularity Key materials in circular packaging — including rPET and emerging bioplastics How to design a circular food and beverage package Strategies for selecting sustainable closures to future-proof packaging solutions Optimization and streamlining of production processes for enhanced efficiency How Husky Technologies can enable your sustainable success
In this collection of content, we provide expert advice on welding from some of the leading authorities in the field, with tips on such matters as controls, as well as insights on how to solve common problems in welding.
Sustainability continues to dominate new additives technology, but upping performance is also evident. Most of the new additives have been targeted to commodity resins and particularly polyolefins.
Resin drying is a crucial, but often-misunderstood area. This collection includes details on why and what you need to dry, how to specify a dryer, and best practices.
Thousands of people visit our Supplier Guide every day to source equipment and materials. Get in front of them with a free company profile.
technotrans says climate protection, energy efficiency and customization will be key discussion topics at PTXPO as it displays its protemp flow 6 ultrasonic eco and the teco cs 90t 9.1 TCUs.
technotrans says climate protection, energy efficiency and customization will be key discussion topics at PTXPO as it displays its protemp flow 6 ultrasonic eco and the teco cs 90t 9.1 TCUs.
While prices moved up for three of the five commodity resins, there was potential for a flat trajectory for the rest of the third quarter.
The Plastics Industry Association (PLASTICS) has released final figures for NPE2024: The Plastics Show (May 6-10; Orlando) that officially make it the largest ever NPE in several key metrics.
In a time where sustainability is no longer just a buzzword, the food and beverage packaging industry is required to be at the forefront of this innovation. By adopting circular packaging processes and solutions, producers can meet regulatory requirements while also satisfying consumer demand and enhancing brand reputation. Join Husky to learn more about the broader implications of the circular economy — as well as how leading brands are leveraging this opportunity to reduce costs, increase design flexibility and boost product differentiation. Agenda: The cost and operational benefits of embracing circularity Key materials in circular packaging — including rPET and emerging bioplastics How to design a circular food and beverage package Strategies for selecting sustainable closures to future-proof packaging solutions Optimization and streamlining of production processes for enhanced efficiency How Husky Technologies can enable your sustainable success
While the major correction in PP prices was finally underway, generally stable pricing was anticipated for the other four commodity resins.
In this three-part collection, veteran molder and moldmaker Jim Fattori brings to bear his 40+ years of on-the-job experience and provides molders his “from the trenches” perspective on on the why, where and how of venting injection molds. Take the trial-and-error out of the molding venting process.
Join this webinar to explore the transformative benefits of retrofitting your existing injection molding machines (IMMs). Engel will guide you through upgrading your equipment to enhance monitoring, control and adaptability — all while integrating digital technologies. You'll learn about the latest trends in IMM retrofitting (including Euromap interfaces and plasticizing retrofits) and discover how to future-proof your machines for a competitive edge. With insights from industry experts, it'll walk you through the decision-making process, ensuring you make informed choices that drive your business forward. Agenda: Maximize the value of your current IMMs through strategic retrofitting Learn how to integrate digital technologies to enhance monitoring and control Explore the benefits of Euromap interfaces and plasticizing retrofits Understand how retrofitting can help meet new product demands and improve adaptability Discover how Engel can support your retrofitting needs, from free consultations to execution
Successfully starting or restarting an injection molding machine is less about ticking boxes on a rote checklist and more about individually assessing each processing scenario and its unique variables.
It’s a good time for the structural-foam business generally, says Ed Hunerberg, v.p. of structural foam technologies for Uniloy North America, Tecumseh, Mich., and a widely respected, 42-year veteran in the field. “We have sold more machines in the past year than in any of the previous 10 years, and our customers overall are the busiest they have been in 10 years.” He also notes that the market has been picked clean of available used machines. Reusable material-handling products—pallets and boxes—are responsible for much of the growth, he says.
In this three-part collection, veteran molder and moldmaker Jim Fattori brings to bear his 40+ years of on-the-job experience and provides molders his “from the trenches” perspective on on the why, where and how of venting injection molds. Take the trial-and-error out of the molding venting process.
Introduced by Zeiger and Spark Industries at the PTXPO, the nozzle is designed for maximum heat transfer and uniformity with a continuous taper for self cleaning.
Despite price increase nominations going into second quarter, it appeared there was potential for generally flat pricing with the exception of a major downward correction for PP.
“When I started in structural foam, it was a novelty. The industry went after the wrong applications—medical enclosures and computer cabinetry—high-tolerance, high-finish parts. The machines of those days (the 1970s) weren’t suitable for those parts, so structural foam got a bad name.” That, and the radical downsizing of computers with the arrival of PCs, put a crimp in the structural-foam business. “It lagged until the end of the ’80s and start of the ’90s, when just-in-time packaging—returnable containers—came in. Since then, structural foam has been growing stronger in new applications and poundage consumed.”
Ernsberger’s firm serves wide range of markets: lawn and garden products (wheelbarrows, parts for riding mowers), janitorial supplies, shelving, pallets, packaging (bins, boxes, dividers, lids), housings, and cabinetry. He focuses on materials that can run at low torque and high throughput—PE, PP, PS, ABS, and Noryl PPO alloys. He avoids polycarbonate—“It’s a high-torque, low-output material.” Ernsberger started in plastics in 1965 with compression molding, but soon moved into injection molding. Starting in 1977, he worked for two structural-foam molders. “I got into this field by accident, but it turned out to be the right choice.” He started his first firm to do structural foam, Vision Molded Plastics, in Napoleon, Ohio, but sold it four years later. When he started 20/20 he chose a name that continued the “vision” theme.
Driven by brand owner demands and new worldwide legislation, the entire supply chain is working toward the shift to circularity, with some evidence the circular economy has already begun.
Processors with sustainability goals or mandates have a number of ways to reach their goals. Biopolymers are among them.
After successfully introducing a combined conference for moldmakers and injection molders in 2022, Plastics Technology and MoldMaking Technology are once again joining forces for a tooling/molding two-for-one.
GETTING A QUOTE WITH LK-MOULD IS FREE AND SIMPLE.
FIND MORE OF OUR SERVICES:
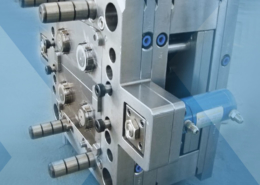
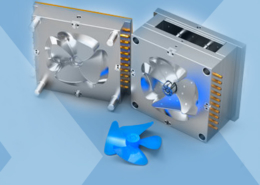
Plastic Molding

Rapid Prototyping
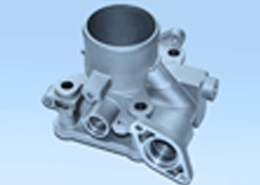
Pressure Die Casting
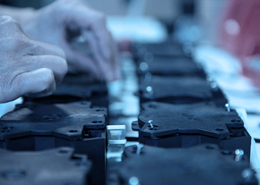
Parts Assembly
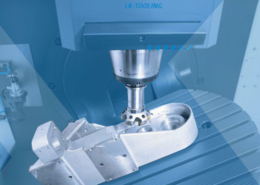