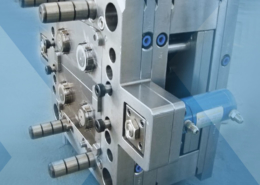
The Best DIY Injection Molding Machines of 2023 - best injection molding compani
Author:gly Date: 2024-09-30
The rising demand for high-performance transport packaging material is fueling spending on expanded polystyrene (EPS), expanding particle foam molding machines market. EPS is observing high demand in the construction and packaging sectors due to its cost-effective, and energy-efficient insulation capabilities. It is widely used to protect shock-sensitive goods during transportation. In addition, advancements in foam molding technologies and compounds will aid in market growth.
Particle Foam Molding Machines Market size valued at USD 1.5 billion in 2022 and is slated to exhibit more than 9.5% CAGR from 2023 to 2032.
Furthermore, the Asia Pacific has a robust HVAC supply chain, with urbanization driving the need for air conditioners, heaters, and other space cooling/heating systems. Particle foam molding machines play a vital role in the development of materials used in HVAC insulation such as EPP, which is fostering the regional industry outlook.
Global Market Insights Inc. 4 North Main Street, Selbyville, Delaware 19975 USA Toll Free: +1-888-689-0688 USA: +1-302-846-7766 Europe: +44-742-759-8484 APAC: +65-3129-7718 Email: sales@gminsights.com
The particle foam molding machines market size from EPS application crossed USD 1 billion in 2022. The increasing focus on sustainability and environment-friendly industrial products is boosting the demand for EPS. It is 100% recyclable and can be reprocessed into different packaging materials, and durable goods. EPS materials offer energy efficiency, recyclability, non-toxicity, and durability, with widespread applications across food processing & packaging. These lightweight insulation materials help reduce carbon emissions, fuel consumption, the release of toxic chemicals, and transportation costs, offering both economic and environmental efficiency, which is facilitating segment expansion.
JEC World 2022 from May 3 to 5 in Paris showcases the entire value chain of the composites industry. One important link in this chain is the shaping of thermoplastic fiber composite preforms. The Engel organomelt process takes this one step further. Organic sheets and unidirectional tapes are not just shaped, but also functionalized in one integrated step by overmolding the preforms. Engel will demonstrate the process at booth N79 in hall 5.
Increasing use of EPS and EPP foam will escalate the demand for particle foam molding. EPP has widespread applications as HVAC foam insulation and acoustic insulation as it absorbs and minimizes sounds. It has a higher strength-to-weight ratio, versatility, and durability, and allows customization. The growing use of EPP foam in HVAC insulation can be attributed to its load-bearing capabilities, and its ability to protect systems against moisture, effectively preventing rust and growth of fungi.
The COVID-19 pandemic had a significant impact on the particle foam molding machines market. The pandemic introduced several opportunities and challenges. While supply chain disruptions hampered production, the dramatic rise in e-commerce accelerated the demand for robust packaging materials, necessitating advanced molding equipment. The growing R&D, drug discovery efforts, and development of novel therapeutics foster the need for innovative packaging solutions for storing sensitive formulations. Furthermore, high consumer spending on HVAC systems during the lockdowns propelled the demand for effective insulation materials such as EPP and EPS.
Composite parts created using the Engel organomelt process combine light weight with excellent crash safety ratings. This technology, which is already in series production in the automotive industry, is suitable for both organic sheets and unidirectional (UD) glass and carbon fiber–reinforced tapes with a thermoplastic matrix. Using a thermoplastic material base enables particularly efficient, fully automated manufacturing processes because reinforcement ribs or assembly elements can be injected directly after forming in the same process step.
The composite blanks are heated in the IR oven, placed and formed in the mold, and overmolded with PA. Heating the prepregs is one of the process steps that drives cycle time and quality in the processing of fiber-reinforced preforms with a thermoplastic matrix. Thickness defines the heat-up and cool-down times. Heating the material quickly without damaging it is crucial, as are short paths for transporting the heated preforms to the mold.
The automatic particle foam molding machines market is projected to witness over 10% CAGR from 2023 to 2032. The advent of automation is transforming the capabilities of conventional molding processes. A recent automation trend in injection and other molding technologies is the development of AI-based smart molding systems.
High costs of particle foam molding machines may negatively influence the industry scenario. The integration of advanced and modern technologies, 3D printing, and automation are resulting in expensive pricing models, making large-scale adoption difficult in low- and middle-income economies. Several developed and developing countries with massive labor, and resources prefer affordable alternatives rather than high-cost equipment. Moreover, advanced technologies also rely on high-performance components and superior technical expertise.
A rise in residential construction across countries such as the U.S. driven by rapid urbanization and a growing population will support the particle foam molding machines industry growth. Additionally, several favorable initiatives and policies introduced by the U.S. government are offering owners affordable housing costs and encouraging large-scale residential construction.
Engel will demonstrate how its organomelt process shapes and functionalizes organic sheets and unidirectional tapes in a single, integrated step.
Home > Industrial Machinery > Industrial Equipment > Particle Foam Molding Machines Market
Tapes make it possible to reinforce individual areas in the part to adapt to the load. The door module, produced through the Engel organomelt process, is more rigid in its window frame area than on the inside of the door.
Looking for more? Our expert team of researchers can create market analysis reports for any of your needs.
The thermoplastic composite preforms were prepared in Engel's Center for Lightweight Composite Technologies in Austria. In practice, the production of thermoplastic composite blanks can be placed immediately upstream of the manufacturing process and directly next to the processing machine. Engel offers fully integrated systems, including the processing machine, robots, and IR ovens as well as pick-and-place tape stacking units with optical image processing and consolidation devices.
U.S. particle foam molding machines market is expected to surpass USD 1 billion by 2032 propelled by increasing use of EPS and EPP in various industries. APAC market is anticipated to surpassed USD 732 million in 2022. APAC will emerge as a major hub for particle foaming technologies owing to rapid industrialization. Countries such as China, India, South Korea, and Japan house massive food & beverage sectors, indicating substantial demand for food packaging materials.
The main component of the production cell, which is producing demo parts made of continuous fiber-reinforced polyamide (PA), is a tie-bar-less Engel victory 200/50 injection molding machine equipped with an Engel viper 12 linear robot and a double-sided, vertical Engel IR oven. The component was designed by Brightlands Materials Center, an R&D center in the Netherlands focused on sustainable polymer solutions. Development of innovative lightweight thermoplastic composite technologies for sustainable mobility markets is one of their key research programs, which Engel supports through a partnership.
Three organic sheets in different geometries with thicknesses ranging between 0.6 and 2.5 mm are heated and formed via IR radiation and given a high-quality visible surface through injection molding in the same process step. The process was developed in collaboration with automotive supplier Brose and is fully automated.
The production cell on display at JEC makes extensive use of the efficiency potential of Engel's tie-bar-less technology for the organomelt process. The victory machine's biggest advantage in this application is its very fast hot handling. Barrier-free access to the mold area makes it possible to position the IR oven closer to the mold than would be possible for an injection molding machine with tie-bars, allowing the robot to take the shortest path from the oven to the mold. In this way, even very thin preforms can be processed.
Engel offers IR ovens from in-house development and production in various designs — both horizontal and vertical — and positions them in the production cell near the mold. The ovens and robots are fully integrated with the injection molding machine’s CC300 control unit and can be centrally controlled via the machine’s display.
GETTING A QUOTE WITH LK-MOULD IS FREE AND SIMPLE.
FIND MORE OF OUR SERVICES:
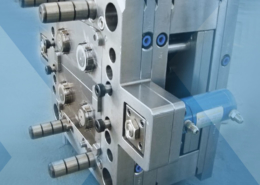
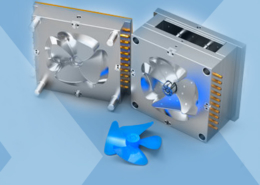
Plastic Molding

Rapid Prototyping
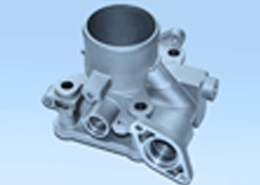
Pressure Die Casting
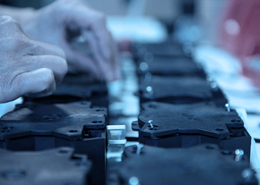
Parts Assembly
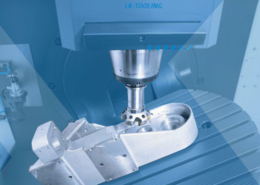