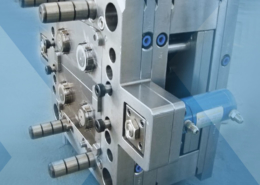
Exploring the Art of Plastic Part Molding
Author:gly Date: 2024-06-08
Plastic part molding, an intricate process of shaping polymers into desired forms, stands as a cornerstone in modern manufacturing. Its versatility, efficiency, and widespread applicability have revolutionized industries ranging from automotive to consumer electronics. This article delves into the multifaceted realm of plastic part molding, elucidating its nuances, innovations, challenges, and future prospects.
1. Evolution of Techniques
Pioneering Methods:
Plastic part molding traces its origins back to the late 19th century, with John Wesley Hyatt's invention of celluloid. Initially, techniques like compression molding and injection molding dominated, catering to diverse manufacturing needs.
Technological Advancements:
The advent of computer-aided design (CAD) and computer-aided manufacturing (CAM) revolutionized plastic molding. Precision, speed, and repeatability improved significantly, ushering in an era of complex geometries and intricate designs.
Emerging Technologies:
Recent years have witnessed the rise of innovative approaches such as 3D printing and multi-material molding. These technologies offer unprecedented flexibility, enabling rapid prototyping and customization while minimizing material waste.
2. Material Selection
Thermoplastics vs. Thermosets:
The choice between thermoplastics and thermosetting polymers significantly impacts the molding process. Thermoplastics, with their ability to be reheated and reshaped, dominate due to their versatility and recyclability.
Material Properties:
Each polymer possesses unique characteristics, influencing factors like strength, durability, and heat resistance. Engineers must meticulously select materials tailored to specific applications, balancing performance with cost-effectiveness.
Sustainability Concerns:
In an era of heightened environmental awareness, sustainable materials gain prominence. Bioplastics derived from renewable sources offer a greener alternative, albeit with challenges in scalability and performance.
3. Molding Processes
Injection Molding:
Widely regarded as the backbone of plastic part manufacturing, injection molding involves injecting molten polymer into a mold cavity. Its high efficiency and versatility make it ideal for mass production of intricate components.
Compression Molding:
Suitable for large, flat parts with intricate details, compression molding applies heat and pressure to a pre-measured amount of polymer placed in a heated mold cavity. Although slower than injection molding, it offers advantages in cost-effectiveness and simplicity.
Blow Molding:
Primarily employed in the production of hollow objects such as bottles and containers, blow molding utilizes compressed air to inflate a heated polymer parison within a mold cavity, conforming it to the desired shape.
4. Quality Control and Optimization
Mold Design:
The design of molds significantly influences product quality and manufacturing efficiency. Factors such as cooling rate, gate location, and venting must be meticulously optimized to minimize defects and cycle times.
Process Monitoring:
Advancements in sensor technology enable real-time monitoring of key process parameters like temperature, pressure, and flow rate. This data-driven approach facilitates early detection of anomalies and ensures consistent part quality.
Continuous Improvement:
Implementing lean manufacturing principles and Six Sigma methodologies empowers manufacturers to continuously optimize processes, minimize waste, and enhance overall efficiency. Regular audits and feedback loops foster a culture of innovation and excellence.
In conclusion, plastic part molding stands as a testament to human ingenuity and technological prowess, driving progress across diverse industries. By embracing emerging technologies, prioritizing sustainability, and continuously refining processes, manufacturers can navigate challenges and unlock new frontiers of innovation in the dynamic world of plastic molding.
GETTING A QUOTE WITH LK-MOULD IS FREE AND SIMPLE.
FIND MORE OF OUR SERVICES:
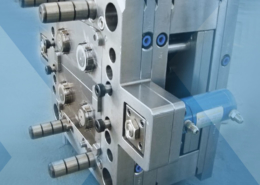
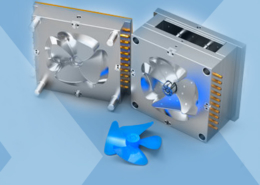
Plastic Molding

Rapid Prototyping
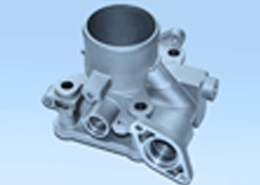
Pressure Die Casting
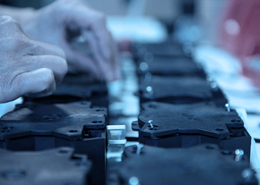
Parts Assembly
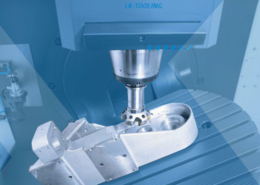