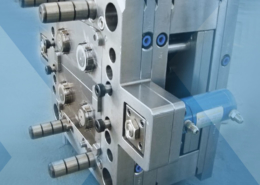
The Best Desktop Injection Molding Machines in 2024 - mold injector
Author:gly Date: 2024-09-30
The surface quality of the injection molded parts produced with the 3D printed plates was limited, the researchers conclude, but post-processing methods such as chemical etching could be used to improve the surface quality. The precision of the surface features was also limited, they add; however, they did find additive manufacturing to be a time- and cost-effective way of producing injection molding inserts for parts with complex surfaces and micro features.
The combination of two Plexiglas Hi-Gloss acrylic resins is used by Austrian automotive supplier, Ulbrichts GmbH, to create the emblem’s modern look. The company uses a special molding compound from Röhm GmbH, which has been a staple for black, high-gloss components in the automotive industry, such as pillar panels, for almost 20 years. This molding compound is used to create Class A surfaces with very high color depth. The contrast between black and white helps the letters of the current logo clearly stand out, regardless of the paint color beneath. Volkswagen has been using this effect for several years now, albeit in a modified version. Here, the famous chrome-colored letters stand out thanks to the high-gloss black background.
There are many ways of manufacturing micro pillars or features, the researchers explain, but most of them can only be applied on flat surfaces or on surfaces with constant curvature. In the paper, they describe how they created micro features on complex surfaces using what they call “a soft tooling process chain.” Steel mold cavities in the injection molding machine were replaced by a set of inserts produced using DLP 3D printing. This technology was able to achieve higher precision than metal additive manufacturing, and the machining time and cost was significantly reduced compared to conventional tooling processes based on CNC machining.
The new logo has been reduced to its essential components and appears in a flat, 2D design. This change is also reflected in the emblems of the current ID models, such as the ID.3: In place of chrome-colored letters on a high-gloss black background, the new brand logo has a modern black-and-white high-gloss look. The emblem’s diameter has been increased by 4.5 cm (1.8 in.), making it even more eye-catching when applied to the front or rear of a car.
In a major leadership shift, VulcanForms has appointed Kevin Kassekert as its new CEO and Jay Martin as President. This change comes at a crucial time as the company moves...
Additive manufacturing and injection molding have been combined before; more frequently, additive manufacturing is being used to manufacture the molds for injection molding. The advantages are many: it is cheaper, faster, and allows for easy production of molds for single or limited use. This paper shows another way that 3D printing can be used to enhance injection molding processes, offering a look at how manufacturing technologies are often better together than by themselves.
Amidst the backdrop of last week’s FAA/EASA workshop in Wichita, Bill Bihlman, Consultant and Volunteer to SAE, analyzes the state of AM aerospace standards. Commercial aviation is notoriously risk averse....
Whether a combination of black and white or black and chrome, the glossy appearance is retained for the entire life of the vehicle, as the polymethyl methacrylate (PMMA) from Röhm is fuel-, chemical-, UV-, and weather-resistant. “A logo is vital for brand recognition and should not fade or become brittle,” said Georg Scharpenack, CEO of Ulbrichts GmbH.
Stay up-to-date on all the latest news from the 3D printing industry and receive information and offers from third party vendors.
The Plexiglas portfolio was recently expanded to include a white coloring of PMMA from Röhm. “We are aware of the strengths of the different materials — and Plexiglas Hi-Gloss molding compounds also have several benefits when it comes to producing emblems,” says Joachim Schicker, Account Manager, Material Science-Polymers, at distributor Brenntag Austria. These benefits mean it is possible to create the black-and-white high-gloss component with a Class A surface in just one work step when injection molding. “There is no need to apply a subsequent high-gloss paint,” says Scharpenack. “We can therefore significantly reduce the cost for each component, a key factor when considering the high number of parts required in the automotive industry.”
The inserts were 3D printed and installed on an injection molding machine. With the inserts installed, the researchers then injection molded parts from PE material.
Stephen has been with PlasticsToday and its preceding publications Modern Plastics and Injection Molding since 1992, throughout this time based in the Asia Pacific region, including stints in Japan, Australia, and his current location Singapore. His current beat focuses on automotive. Stephen is an avid folding bicycle rider, often taking his bike on overseas business trips, and is a proud dachshund owner.
(a) Inserts produced by additive manufacturing process form the mold cavity; one polyethylene (PE) replica produced by injection molding is displayed. Markings on the reference ruler are millimeters; numbers mark centimeters. (b) Scanning electron microscope (SEM) image shows the surface of the insert; (c) SEM image shows the surface of the PE parts made by injection molding.
The logo also will be illuminated in the future, not just on the vehicles, but at company sites and dealerships. The ID.ROOMZZ concept car showed off this aspect with its particularly striking light elements and illuminated front and rear emblems. “While European legislation currently does not permit brand logos to be illuminated on the road, several Asian countries do allow it. Plexiglas molding compounds are also available for this, as they can be used for various lighting applications in and around the automobile, guaranteeing the homogeneous scattering of light and enabling flexible design,” says Siamak Djafarian, who heads the Molding Compounds business unit at Röhm.
SPEE3D participated in a U.S. Army Combat Capabilities Development Command (DEVCOM) Army Research Laboratory (ARL) demonstration. The demo took place at the University of Tennessee Knoxville and ran from the...
Register to view and download proprietary industry data from AM Research and 3DPrint.com Questions? Contact info@3dprint.com
Stay up-to-date on all the latest news from the 3D printing industry and receive information and offers from third party vendors.
There’s lots to choose from in this week’s 3D Printing Webinar and Event Roundup! Stratasys continues its North American tour, as well as its in-person training classes, and HP will...
Before the high-gloss emblems were finalized, the European market leader for automobile emblems and lettering had to perform significant development work. “Volkswagen approached us for the first time back in 2012 with the task of developing high-gloss emblems,” says Scharpenack. “Painted components were not feasible for cost reasons, which is why we experimented with various materials.” The goal was to find a material that could be formed into thin, high-quality emblems using an automated injection molding procedure. “We initially thought PMMA was not suitable for this,” Scharpenack reports. “However, Brenntag Austria and the high-quality products from Röhm convinced us otherwise.”
A circle surrounding the letters V and W — just one glance and it’s clear that we’re looking at a Volkswagen. The basic shape of the logo has been in use since 1945 and has been subject to continued development over the years. Volkswagen recently modernized the logo in one of the world’s biggest rebranding exercises. “The new logo represents Volkswagen’s breakthrough into an electric, connected, and CO2-neutral era,” says Klaus Zyciora, Head of Volkswagen Group Design.
Authors of the paper include Yang Zhang, David Bue Pedersen, Michael Mischkot, Matteo Calaon, Federico Baruffi, and Guido Tosello.
“This process chain is suitable for products in intermediate scale (from 1000 – 10,000 cycles by injection molding or similar) production, but high variation in design,” the researchers state. “Moreover, for 3D printed inserts, no special mold plates are required. Standard commercial injection molding plates were purchased and machined to fit the inserts.”
3D printing is a great technology on its own, but it also lends itself well to complementing other manufacturing technologies, such as injection molding. In a paper entitled “A Soft Tooling Process Chain for Injection Molding of a 3D Component with Micro Pillars,” a group of researchers discusses using 3D printing to create injection molding inserts with micro surface features.
“This method will create the possibility for creating micro features on real free-form surface on a new production platform meeting industrial demands,” the researchers state. “Therefore, this method has the potential to be applied and investigated for applications in connection with next generation medical devices that require micro features on complex shapes, for example in connection with medical devices or implanting devices. This method will facilitate value creation through significantly reduced expenses for small-to-medium volume series productions, and positively affect the timescale for production in the gap between 1 – 10 individual devices and real mass production. It will open up new high-value products and design solutions.”
GETTING A QUOTE WITH LK-MOULD IS FREE AND SIMPLE.
FIND MORE OF OUR SERVICES:
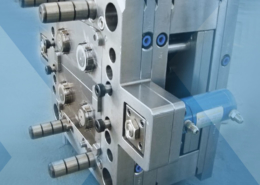
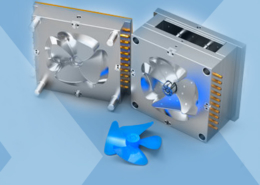
Plastic Molding

Rapid Prototyping
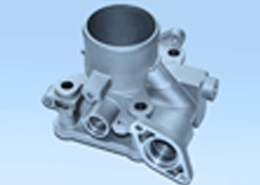
Pressure Die Casting
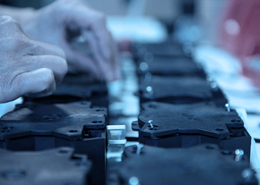
Parts Assembly
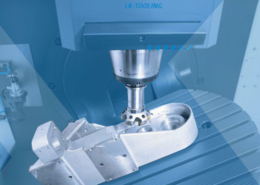