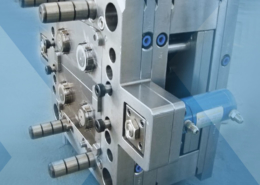
The Best Desktop Injection Molding Machines in 2024 - injection moulding mould c
Author:gly Date: 2024-09-30
The two-color injection molding process has been simplified through a development at Trelleborg Sealing Solutions (Stuttgart, Germany) that employs a single shot and a single tool to manufacture partially colored liquid silicone rubber (LSR) components. Utilizing an innovative and proprietary tool construction, the process has the capability to add color pigment to part of the transparent silicone material stream just prior to its injection into the tool cavity.
"Expertise in tool design is fundamental to our core competences within Trelleborg Sealing Solutions," emphasizes Jarno. "Developing the two-color process required additional considerations during the design and construction of the tool to make sure the flow of the clear and the colored material portions must be kept strictly separated.
The process involves the two components of LSR raw material being mixed in a ratio of 1:1. On the way into the injection tool, this homogenous mass is then divided. Color is added via an additional mixing unit to one part of the volume stream and injected into the tool cavity via a proprietary valve design. Simultaneously, the colorless material is being injected via a second stream.
Jarno Burkhardt, General Manager of the Trelleborg Sealing Solutions European center of excellence for LSR component solutions in Stein am Rhein, Switzerland, comments: "The advantage of the two-colored LSR components to our customer, as well as to the OEM they supply, is that it gives, without adding significant extra cost, product traceability. The beauty of the novel tool design is that it will allow an unlimited number of color combinations from a single machine, in a single tool and in one single shot."
The two-color injection molding process has been simplified through a development at Trelleborg Sealing Solutions (Stuttgart, Germany) that employs a single shot and a single tool to manufacture partially colored liquid silicone rubber (LSR) components. Utilizing an innovative and proprietary tool construction, the process has the capability to add color pigment to part of the transparent silicone material stream just prior to its injection into the tool cavity.
Tim and Caleb discuss the challenges of hiring and retaining employees in the metal fabrication industry, particularly at...
Digital contract manufacturer Protolabs recently posted a blog about whether it’s better to 3D-print molds from thermoplastic or machine them from aluminum. The Maple Plain, Minn., provider of injection molding, CNC machining, 3D printing, and sheet metal fabrication services concluded, “In most cases, use 3D printing for parts—prototype or end use—but not for molds.”
The primary advantage of a 3D-printed mold is its relatively low cost. Protolabs points out, though, that “with 3D-printed molds, you’ll need to print, machine-assemble, and test a new mold every 50 to 100 shots. Aluminum tooling has no such constraints, and often see[s] service well past 10,000 shots.”
Printed molds have their place, the blog continues, noting that some shops have had good success with them. “Proponents argue that 3D printing produces molds up to 90 percent faster and 70 percent cheaper than using traditional moldmaking processes. And while this may be true in some circumstances, it’s important to understand the pros and cons of printed plastic molds compared to those machined from metal.”
Ursula Nollenberger, Product Line Director for LSR Components at Trelleborg Sealing Solutions, says: "Our first application of this revolutionary technology is for a leading automotive tier-one supplier. The company was looking for a solution to visually differentiate geometrically identical parts that Trelleborg produces off a single tool for various vehicle platforms, without impacting the overall aesthetics of the finished product. This new process offered an ideal solution that was both practical and cost-effective."
The company explained that molds made with thermoplastics-based 3D printing are “kind of like the plastic storage sheds some of us put in our backyards. They’re a little cheaper than metal sheds. They go up quickly and are fine under light loads. Pile too much snow on them, however, and they’ll collapse like a house of cards.”
"This novel technology can be applied to any size and number of cavities per tool. Depending on part geometry and size as well as production capacity needed, we construct tools anywhere between 1 and 128 cavities with possibilities even beyond," adds Nollenberger.
GETTING A QUOTE WITH LK-MOULD IS FREE AND SIMPLE.
FIND MORE OF OUR SERVICES:
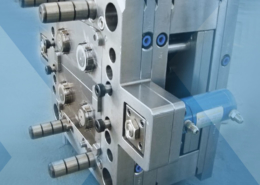
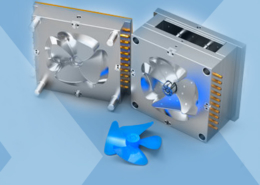
Plastic Molding

Rapid Prototyping
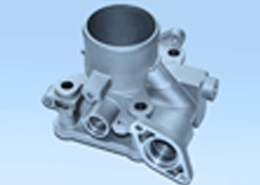
Pressure Die Casting
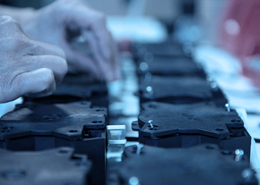
Parts Assembly
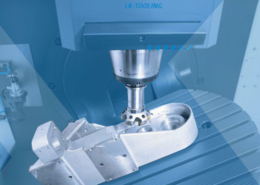