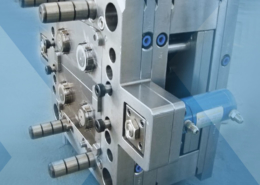
Plastic Moulding Dies: Precision in Manufacturing
Author:gly Date: 2024-06-08
Plastic moulding dies stand as the backbone of modern manufacturing, facilitating the production of intricate plastic components with precision and efficiency. This article delves into the realm of plastic moulding dies, unraveling their significance, functionality, types, applications, challenges, and future prospects.
Introduction: Precision Personified
Plastic moulding dies, also known as molds or tooling, play a pivotal role in the injection moulding process, dictating the quality and precision of the final product. With the ability to shape molten plastic into desired forms, these dies serve as the linchpin of industries ranging from automotive to consumer goods. Their intricate designs and meticulous craftsmanship captivate engineers and manufacturers, driving innovation and progress in manufacturing processes.
Functionality: Crafting Excellence
Plastic moulding dies function by guiding molten plastic into predefined cavities, where it solidifies to form the desired shape. These dies consist of two main parts: the cavity, which imparts the external shape of the part, and the core, which defines the internal features. The design and construction of moulding dies require meticulous attention to detail, considering factors such as part geometry, material flow, cooling rates, and ejection mechanisms. Advanced manufacturing techniques, including computer-aided design (CAD) and computer-aided manufacturing (CAM), facilitate the precise fabrication of moulding dies, ensuring optimal performance and longevity.
Types: Exploring Diversity
Plastic moulding dies encompass a diverse array of types and configurations, tailored to meet the unique requirements of each application. Injection moulds, the most common type, feature a cavity and core that form the basis for injecting molten plastic. Compression moulds compress molten plastic between two heated plates to achieve the desired shape, making them ideal for thick-walled parts. Transfer moulds transfer molten plastic from a pot to a cavity via a plunger, enabling precise control over material flow and pressure. Additionally, blow moulds and extrusion dies cater to specific applications such as bottle manufacturing and profile extrusion, respectively, highlighting the versatility of plastic moulding dies.
Applications: Pervasive Presence
The applications of plastic moulding dies span across diverse industries, ranging from automotive and aerospace to electronics and healthcare. In the automotive sector, moulding dies are utilized to fabricate interior and exterior components such as dashboards, bumpers, and door panels, leveraging the lightweight and durable nature of plastics. In the electronics industry, they enable the production of housings, connectors, and enclosures for electronic devices, accentuating functionality and aesthetics. Furthermore, moulding dies find applications in the medical field for manufacturing surgical instruments, implants, and medical devices, adhering to stringent regulatory standards.
Challenges: Navigating Complexity
Despite their indispensable role, plastic moulding dies pose several challenges in their design, fabrication, and maintenance. Achieving optimal part quality while minimizing defects such as warpage, sink marks, and flash necessitates meticulous process optimization and control. Moreover, variations in material properties and environmental factors can introduce inconsistencies, mandating continuous monitoring and adjustment. Additionally, the complex geometries and intricate features of moulding dies require skilled craftsmanship and precision machining techniques, contributing to lead times and manufacturing costs.
Future Prospects: Embracing Innovation
The future of plastic moulding dies is imbued with promise and innovation, driven by advancements in materials, technologies, and sustainability practices. The development of high-performance materials, including bio-based polymers and recyclable additives, promises to enhance sustainability and reduce environmental impact. Furthermore, the integration of additive manufacturing techniques, such as 3D printing, enables the rapid prototyping and iteration of moulding dies, fostering efficiency and flexibility. Additionally, the adoption of digital twins and predictive analytics facilitates proactive maintenance and optimization of moulding processes, ensuring reliability and performance.
Conclusion: Shaping Tomorrow, Today
In conclusion, plastic moulding dies stand as testaments to precision and ingenuity in modern manufacturing. Their functionality, types, applications, challenges, and future prospects underscore their pivotal role in shaping industries and driving progress. As we navigate an era of relentless innovation and change, embracing advancements in materials, technologies, and sustainability practices will be paramount in unlocking the full potential of plastic moulding dies. By fostering collaboration, innovation, and resilience, we can pave the way towards a future where manufacturing is not only efficient and precise but also sustainable and inclusive.
With these insights in mind, let us embark on a journey of discovery and innovation, harnessing the transformative power of plastic moulding dies to build a brighter and more sustainable future.
GETTING A QUOTE WITH LK-MOULD IS FREE AND SIMPLE.
FIND MORE OF OUR SERVICES:
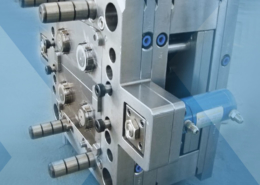
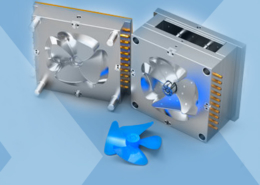
Plastic Molding

Rapid Prototyping
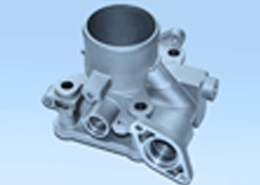
Pressure Die Casting
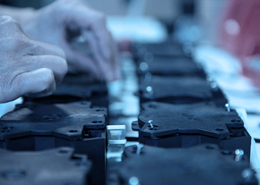
Parts Assembly
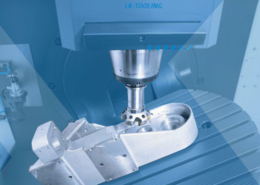