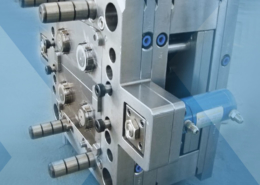
TDL Plastic Mould CO., Ltd: Shaping Excellence in Injection Molding,
Author:gly Date: 2024-09-30
Mold maintenance is critical, and with this collection of content we’ve bundled some of the very best advice we’ve published on repairing, maintaining, evaluating and even hanging molds on injection molding machines.
Take a deep dive into all of the various aspects of part quoting to ensure you’ve got all the bases—as in costs—covered before preparing your customer’s quote for services.
Another key contributor to sustainability in processing is energy efficiency, which lowers the “carbon footprint” of plants and products. Both Carr and Schlüter agree that all-electric EBM machines have finally gained acceptance in the U.S., well after that occurred in Europe and South America. According to Carr, all-electrics and electric hybrids comprise close to half of EBM shuttle machine sales nowadays. What’s driving this trend is not only energy savings versus hydraulics, but also much greater precision and repeatability — leading to faster startups and recovery from production interruptions — as well as oil-free cleanliness.
Mike Sepe has authored more than 25 ANTEC papers and more than 250 articles illustrating the importance of this interdisciplanary approach. In this collection, we present some of his best work during the years he has been contributing for Plastics Technology Magazine.
Megan Dyer, process engineer at ENTEK Manufacturing, agrees: “Trends in compounding include a continued increase in the development of bioresins. We expect to see a large number of all types of companies, from startups to large resin suppliers, who will be looking for answers to their questions about best ways to process their formulations. Twin-screw extruders, from lab-sized machines to high output systems, as well as wear parts like screws and barrels, are all important pieces to the successful development and commercialization of these materials.”
Additive technology creates air pockets in film during orientation, cutting down on the amount of resin needed while boosting opacity, mechanical properties and recyclability.
When, how, what and why to automate — leading robotics suppliers and forward-thinking moldmakers will share their insights on automating manufacturing at collocated event.
Here are some hints of what to look for: retrofittability of coex capability (as mentioned above), screw designs and controls that can adjust for wider viscosity ranges in PCR, user-friendly screen changers to catch contaminants in PCR and regrind, materials-handling systems adapted to the wider range of particle geometries in PCR, improved flash containment in machine designs to facilitate closed-loop reclamation. In extruders for PCR, some suppliers now advocate larger units that operate at lower rpm to treat PCR more gently because it has already experienced at least one heat history.
Across the show, sustainability ruled in new materials technology, from polyolefins and engineering resins to biobased materials.
While prices moved up for three of the five commodity resins, there was potential for a flat trajectory for the rest of the third quarter.
In addition to a smaller utility bill, more energy-efficient hybrid and all-electric machines serve the increasingly important sustainability goals of molders and their customers. To that end, multiple machine suppliers will also be showcasing systems for running reclaimed and biobased materials at the show, whether it’s regrind, postconsumer recycled plastic or bioresins. Increasingly, machine makers have specific packages available to meet the challenges posed by these nontraditional plastics, and those options will be on display at NPE2024.
While automation will be ever present in the injection aisles, what will likely be nearly completely absent from the show floor are fully hydraulic molding machines. Many of the leading OEMs are highlighting fully electric and/or hybrid machines in Orlando, and even where there are hydraulics in play, most use servo-driven pumps. Because of this, many machine makers at the show will lead off with their fleets’ energy savings when molders come to kick the tires on a new press.
technotrans says climate protection, energy efficiency and customization will be key discussion topics at PTXPO as it displays its protemp flow 6 ultrasonic eco and the teco cs 90t 9.1 TCUs.
After a six-year hiatus, NPE is back and, as always, injection machines will have a huge presence in Orlando, even if their actual individual footprints are smaller.
Join Wittmann for an engaging webinar on the transformative impact of manufacturing execution systems (MES) in the plastic injection molding industry. Discover how MES enhances production efficiency, quality control and real-time monitoring while also reducing downtime. It will explore the integration of MES with existing systems, emphasizing compliance and traceability for automotive and medical sectors. Learn about the latest advancements in IoT and AI technologies and how they drive innovation and continuous improvement in MES. Agenda: Overview of MES benefits What is MES? Definition, role and brief history Historical perspective and evolution Longevity and analytics Connectivity: importance, standards and integration Advantages of MES: efficiency, real-time data, traceability and cost savings Emerging technologies: IoT and AI in MES
Discover how artifical intelligence is revolutionizing plastics processing. Hear from industry experts on the future impact of AI on your operations and envision a fully interconnected plant.
Curiously, though, while processors are running with higher loadings of PCR, those who are running PFAS-free materials — a big trend in processing aids — are seeing scrap rates increase, which defeats the purpose. Both Hosokawa Alpine American and Windmoeller & Hoelscher (W&H) point out that PFAS-free materials tend to build up on the die and create melt fracture and other undesirable effects. Alpine president Dave Nunes says this will likely result in machine builders developing new die lip coatings that mitigate these issues.
In this three-part collection, veteran molder and moldmaker Jim Fattori brings to bear his 40+ years of on-the-job experience and provides molders his “from the trenches” perspective on on the why, where and how of venting injection molds. Take the trial-and-error out of the molding venting process.
Plastics processors are finding applications for 3D printing around the plant and across the supply chain. Here are 8 examples to look for at NPE2024.
Adds Jens Schlüter, president of W. Müller USA, “Everyone will be showing PCR use in blow molding, so what have the OEMs done to make PCR easier to use? There are many challenges to using PCR. How are they dealing with them?”
In a time where sustainability is no longer just a buzzword, the food and beverage packaging industry is required to be at the forefront of this innovation. By adopting circular packaging processes and solutions, producers can meet regulatory requirements while also satisfying consumer demand and enhancing brand reputation. Join Husky to learn more about the broader implications of the circular economy — as well as how leading brands are leveraging this opportunity to reduce costs, increase design flexibility and boost product differentiation. Agenda: The cost and operational benefits of embracing circularity Key materials in circular packaging — including rPET and emerging bioplastics How to design a circular food and beverage package Strategies for selecting sustainable closures to future-proof packaging solutions Optimization and streamlining of production processes for enhanced efficiency How Husky Technologies can enable your sustainable success
Join KraussMaffei for an insightful webinar designed for industry professionals, engineers and anyone interested in the manufacturing processes of PVC pipes. This session will provide a comprehensive understanding of the technology behind the production of high-quality PVC pipes: from raw material preparation to final product testing. Agenda: Introduction to PVC extrusion: overview of the basic principles of PVC pipe extrusion — including the process of melting and shaping PVC resin into pipe forms Equipment and machinery: detailed explanation of the key equipment involved — such as extruders, dies and cooling systems — and their roles in the extrusion process Process parameters: insight into the critical process parameters like temperature, pressure and cooling rates that influence the quality and consistency of the final PVC pipes Energy efficiency: examination of ways to save material and energy use when extruding PVC pipe products
The trends are running down a similar path in compounding. KraussMaffei will be upcycling a blood tube on a twin-screw compounder at its booth, with the pelletized, colored material being delivered to an injection molding machine for an overmolding application.
Plastics Technology covers technical and business Information for Plastics Processors in Injection Molding, Extrusion, Blow Molding, Plastic Additives, Compounding, Plastic Materials, and Resin Pricing. About Us
While the major correction in PP prices was finally underway, generally stable pricing was anticipated for the other four commodity resins.
Second quarter started with price hikes in PE and the four volume engineering resins, but relatively stable pricing was largely expected by the quarter’s end.
Core Technology Molding turned to Mold-Masters E-Multi auxiliary injection unit to help it win a job and dramatically change its process.
Thousands of people visit our Supplier Guide every day to source equipment and materials. Get in front of them with a free company profile.
Energy efficiency can be accomplished in other ways, too. For example, a new barrel-heating/cooling system uses air cooling and aluminum heating tapes instead of ceramic heaters. Schlüter sees a trend toward smaller extruders that run at higher rpm, offering lower investment cost and smaller machine footprint. And look out for recent developments in smaller extruder diameters with higher L/Ds to permit increased output with electric smaller motors.
So expect a slew of new electric machines — and hybrids — reinforced by the influx of several suppliers from Europe and Asia that are new to the U.S. market. You’re also apt to see increased electrification in industrial machines, reflected in new electric accumulator heads and clamping mechanisms. As a benchmark on energy use, some makers of both packaging and industrial machines claim their units can meet the highest category of energy efficiency – Class 10 under Euromap 46.1, or less than 0.29 kWh/kg of resin processed.
In this collection of content, we provide expert advice on welding from some of the leading authorities in the field, with tips on such matters as controls, as well as insights on how to solve common problems in welding.
Introduced by Zeiger and Spark Industries at the PTXPO, the nozzle is designed for maximum heat transfer and uniformity with a continuous taper for self cleaning.
Most of the machines at the show will be at the heart of a self-contained manufacturing cell. A statistic often cited by machine makers is the percent of machines sold with automation in a package, a percentage that is only increasing as molders seek customized manufacturing solutions for specific parts and programs.
While the melting process does not provide perfect mixing, this study shows that mixing is indeed initiated during melting.
Multiple speakers at Molding 2023 will address the ways simulation can impact material substitution decisions, process profitability and simplification of mold design.
While prices moved up for three of the five commodity resins, there was potential for a flat trajectory for the rest of the third quarter.
Despite some index components accelerating and others leveling off, April spelled contraction for overall plastics processing activity.
Join Engel in exploring the future of battery molding technology. Discover advancements in thermoplastic composites for battery housings, innovative automation solutions and the latest in large-tonnage equipment designed for e-mobility — all with a focus on cost-efficient solutions. Agenda: Learn about cutting-edge thermoplastic composites for durable, sustainable and cost-efficient battery housings Explore advanced automation concepts for efficient and scalable production See the latest large-tonnage equipment and technology innovations for e-mobility solutions
Exhibitors and presenters at the plastics show emphasized 3D printing as a complement and aid to more traditional production processes.
NPE2024, the Plastics Show, could just as easily have been tagged NPE2024: the Plastics Sustainability Show. Across the spectrum of processes, attendees walking the floors of the Orange County Convention Center (OCC), Orlando, Florida, May 6-10, will bear witness to new products that reflect the industry’s need to be part of the circular economy. On the pages that follow this intro, you will notice technology introductions that consume less energy, take up less space, run more environmentally conscious materials, and then some.
To help navigate the many recycle-related blow molding exhibits, two experts in the EBM field offer some advice: Says Gary Carr, v.p. of sales for Bekum America, “Ask what the OEMs are doing to make their machines more adaptable to multilayer molding with PCR (postconsumer recycle). What are they doing to make the technology more readily available, more retrofittable?”
Mixed in among thought leaders from leading suppliers to injection molders and mold makers at the 2023 Molding and MoldMaking conferences will be molders and toolmakers themselves.
Coverage of single-use plastics can be both misleading and demoralizing. Here are 10 tips for changing the perception of the plastics industry at your company and in your community.
It’s all about sustainability and the circular economy, and it will be on display in Orlando across all the major processes. But there will be plenty to see in automation, AI and machine learning as well.
August 29-30 in Minneapolis all things injection molding and moldmaking will be happening at the Hyatt Regency — check out who’s speaking on what topics today.
Christiano adds, “The challenge of single-use plastics will necessitate practical solutions, with advancements in mechanical and chemical recycling standing out as crucial components toward achieving a circular economy for plastic materials. Biomaterials are anticipated to play a significant role in addressing the issue of single-use plastics, offering sustainable alternatives that align with the growing demand for eco-friendly practices. Moreover, the industry will grapple with the demand for breakthroughs in energy efficiencies, aligning with the overarching trend toward green technologies and environmentally responsible practices.”
Resin drying is a crucial, but often-misunderstood area. This collection includes details on why and what you need to dry, how to specify a dryer, and best practices.
Sustainability continues to dominate new additives technology, but upping performance is also evident. Most of the new additives have been targeted to commodity resins and particularly polyolefins.
Processors with sustainability goals or mandates have a number of ways to reach their goals. Biopolymers are among them.
The Plastics Industry Association (PLASTICS) has released final figures for NPE2024: The Plastics Show (May 6-10; Orlando) that officially make it the largest ever NPE in several key metrics.
In this collection, which is part one of a series representing some of John’s finest work, we present you with five articles that we think you will refer to time and again as you look to solve problems, cut cycle times and improve the quality of the parts you mold.
Gifted with extraordinary technical know how and an authoritative yet plain English writing style, in this collection of articles Fattori offers his insights on a variety of molding-related topics that are bound to make your days on the production floor go a little bit better.
In extrusion, the drive to boost recyclability will be evident in the two blown film lines that will be operating during the show. Both Macchi and Bandera will be running all-polyolefin multilayer blown film lines, reflecting a shift away from complex multimaterial structures that wreak havoc with the recycling stream, should they even get there.
W&H, for one, has developed several automation systems for film processors that shorten product changeovers and format adjustments. The machine builder notes that its automation solution also helps the operators by guiding them through processes and ultimately shortening their learning curve, which addresses the ongoing difficulty in finding and keeping them.
A third leg of the sustainability platform in blow molding is lightweighting. In ISBM, the OEMs have taken an active role in developing bottle designs and tooling to shave weight from PET bottles. In EBM, advances in coextrusion with a foamed center layer show potential for weight saving.
Across all process types, sustainability was a big theme at NPE2024. But there was plenty to see in automation and artificial intelligence as well.
In keeping with a primary theme of the show, sustainability is sure to be emphasized in many, if not most, blow molding exhibits. Among the 50-plus displays of blow molding machinery, tooling and controls, expect to see numerous examples of “circular” technology — involving use of recycled and scrap materials. In extrusion blow molding (EBM), expect the emphasis to be on three-layer coextrusion with the recycled layer in the center between two layers of virgin resin. In PET injection stretch-blow molding (ISBM), you may encounter two-layer sandwiches with a thin virgin inner layer and rPET on the outside. Some PET exhibits (including preform injection molding) may show off capabilities to mold rPET flake without repelletizing.
The aim of this presentation is to guide you through the factors and the numbers that will help you determine if a robot is a smart investment for your application. Agenda: Why are you considering automation? What problems are you trying to solve? How and why automation can help Crunch the numbers and determine the ROI
Comments John Christiano, director of technology at Davis-Standard, “Sustainability is a central theme, reflecting the broader global focus on environmentally conscious practices. The plastics machinery industry will play a significant role in the transition toward renewable energy sources of solar and wind as the global infrastructure moves toward further electrification. Operations will expect to embrace sustainable energy sources in production processes to reduce its environmental impact.”
Keeping all this in mind, when you enter a hardware supplier’s booth, besides asking, “What’s new?” Schlüter recommends some additional questions: “What are you doing to simplify the blow molding process? What are you doing to reduce downtime? What are you doing to add troubleshooting, service and training capabilities?”
This Knowledge Center provides an overview of the considerations needed to understand the purchase, operation, and maintenance of a process cooling system.
Ultradent's entry of its Umbrella cheek retractor took home the awards for Technical Sophistication and Achievement in Economics and Efficiency at PTXPO.
Implementing a production monitoring system as the foundation of a ‘smart factory’ is about integrating people with new technology as much as it is about integrating machines and computers. Here are tips from a company that has gone through the process.
Plastics Technology’s Tech Days is back! Every Tuesday in October, a series of five online presentations will be given by industry supplier around the following topics: Injection Molding — New Technologies, Efficiencies Film Extrusion — New Technologies, Efficiencies Upstream/Downstream Operations Injection Molding — Sustainability Extrusion — Compounding Coming out of NPE2024, PT identified a variety of topics, technologies and trends that are driving and shaping the evolution of plastic products manufacturing — from recycling/recyclability and energy optimization to AI-based process control and automation implementation. PT Tech Days is designed to provide a robust, curated, accessible platform through which plastics professionals can explore these trends, have direct access to subject-matter experts and develop strategies for applying solutions in their operations.
From adviser platforms to banks, there have been some big winners from clients’ cash accounts, including Flagstone, which this week received £108m of private equity (PE) investment.
Learn about sustainable scrap reprocessing—this resource offers a deep dive into everything from granulator types and options, to service tips, videos and technical articles.
Flagstone provides a cash deposit service, where clients transfer a minimum of £10,000 into a holding account, provided by HSBC. The cash is then transferred into a range of savings accounts from banks, with clients able to select the best rates on offer and manage their accounts through the Flagstone platform. Flagstone takes a cut of interest earned, up to 0.3%.
Successfully starting or restarting an injection molding machine is less about ticking boxes on a rote checklist and more about individually assessing each processing scenario and its unique variables.
Join this webinar to explore the transformative benefits of retrofitting your existing injection molding machines (IMMs). Engel will guide you through upgrading your equipment to enhance monitoring, control and adaptability — all while integrating digital technologies. You'll learn about the latest trends in IMM retrofitting (including Euromap interfaces and plasticizing retrofits) and discover how to future-proof your machines for a competitive edge. With insights from industry experts, it'll walk you through the decision-making process, ensuring you make informed choices that drive your business forward. Agenda: Maximize the value of your current IMMs through strategic retrofitting Learn how to integrate digital technologies to enhance monitoring and control Explore the benefits of Euromap interfaces and plasticizing retrofits Understand how retrofitting can help meet new product demands and improve adaptability Discover how Engel can support your retrofitting needs, from free consultations to execution
Say “manufacturing automation” and thoughts immediately go to the shop floor and specialized production equipment, robotics and material handling systems. But there is another realm of possible automation — the front office.
Automation is another trend to track in extrusion. Notes Nunes, “The more automation, the better to minimize the need for labor that is getting harder and harder to find and maintain.”
Despite price increase nominations going into second quarter, it appeared there was potential for generally flat pricing with the exception of a major downward correction for PP.
In this collection of articles, two of the industry’s foremost authorities on screw design — Jim Frankand and Mark Spalding — offer their sage advice on screw design...what works, what doesn’t, and what to look for when things start going wrong.
This month’s resin pricing report includes PT’s quarterly check-in on select engineering resins, including nylon 6 and 66.
And biopolymers will play a key role in future compounded formulations. Notes Charlie Martin, president of Leistritz Extrusion, “Although bioplastics represent less than 1% of current plastic products used today, it’s increasing by double digits each year, so there’s a big push to modify the twin-screw design to accommodate these new formulations. Bioplastic materials tend to be heat and shear sensitive as compared to traditional plastics, and generally need to be compounded with modifiers, fillers, additives and other polymers based upon the required functionality of the final product. Elevated melt temperatures and high shear stresses must be managed in the twin-screw extrusion process section to minimize molecular weight loss and maintain mechanical properties. Compounders are visiting NPE to learn more about what’s needed to accomplish these goals.”
Innovations in drive and clamp technologies, as well as advances in the key components that make up the guts of injection molding machines, have enabled the machinery OEMs to cut footprints as much as 30% in some instances.
While we preview the three major processes here, sustainability is also making its mark on the development of new materials (see Close-Up p. xx) and in the way OEMs and brand owners are thinking about plastics (see Close-Up p. xx).
Formnext Chicago is an industrial additive manufacturing expo taking place April 8-10, 2025 at McCormick Place in Chicago, Illinois. Formnext Chicago is the second in a series of Formnext events in the U.S. being produced by Mesago Messe Frankfurt, AMT – The Association For Manufacturing Technology, and Gardner Business Media (our publisher).
In addition to being more compact, many of the presses in the OCCC will be more self-sufficient, applying algorithms and controls with incredibly fast response times to set up, adjust and help maintain consistent processes. These features, as well as the ubiquity of automation on the machines in Orlando, are a nod to the ongoing labor shortage plaguing manufacturing in general and plastics processing specifically.
Conscious of their customers’ increasing need to maximize productivity, as well as the knock-on benefits that running smaller can have from an energy and carbon output perspective, injection molding machine suppliers at NPE2024 have slimmed down their machine fleets, promising molders more output from a smaller package.
After successfully introducing a combined conference for moldmakers and injection molders in 2022, Plastics Technology and MoldMaking Technology are once again joining forces for a tooling/molding two-for-one.
GETTING A QUOTE WITH LK-MOULD IS FREE AND SIMPLE.
FIND MORE OF OUR SERVICES:
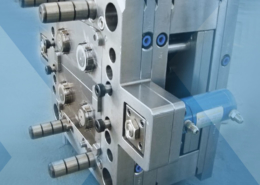
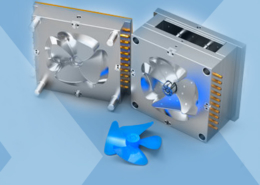
Plastic Molding

Rapid Prototyping
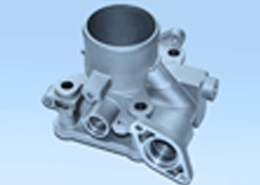
Pressure Die Casting
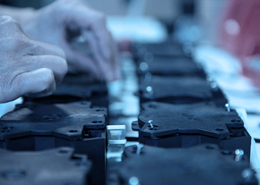
Parts Assembly
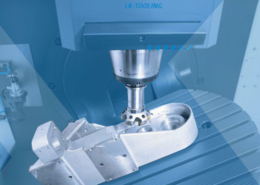