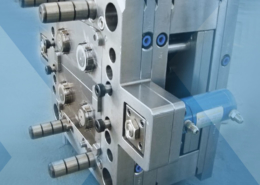
Tariffs Threaten Chinese OEM Growth Potential - pom injection molding
Author:gly Date: 2024-09-30
Today, the Oracle IoT cloud service can automatically pull Noble Plastics’ production data from its robots and molding machines, and then use anomaly-detection algorithms to help keep tabs on machine health, maintenance requirements, and parts quality.
Japanese technology company Asahi Kasei will exhibit its range of diversified material solutions at Fakuma 2024 from Oct. 15 to 19 in Friedrichshafen, Germany. Highlights include polymers for thermal management applications in EVs, a novel thermoplastic elastomer for improved recyclability of automotive interior parts, and a cellulose nanofiber composite for high-performance 3D printing.
Oracle’s IoT cloud service can automatically pull Noble Plastics’ production data from its molding machines, and then use anomaly-detection algorithms to help monitor machine health, maintenance requirements, and parts quality.
The Oracle saleswoman explained that Oracle Internet of Things Insight Asset Monitoring Application was helping other small and midsize businesses monitor their industrial equipment remotely, across multiple facilities, without requiring any onsite machine operators or servers.
Asahi Kasei will present its materials and solutions in three different areas: Compact & Safe EV Batteries, Improved Connectivity & Lightweighting, and Sustainable Material Life Cycle at its location in hall B5, booth 5319.
Productivity gains made possible through industrial automation and the so-called Fourth Industrial Revolution have given small manufacturers such as Noble Plastics an opportunity to compete on a massive scale.
The Louisiana-based contract manufacturer of injection molding products has long been aware that simply automating its processes without integrating the systems that monitor them can result in defective parts and expensive rework.
“I was having a particularly challenging day when I got a call from Oracle,” says Rogers, who notes he’d received several calls from the sales rep before but hadn’t been receptive. “This time I was more open-minded: Maybe Oracle had something that could help.”
Before moving to the cloud, Rogers’ team had to actually make a bad part to determine that there’s a problem, then fix the problem and rebuild the production schedules. “It created nothing but chaos for everyone,” he says.
The impact was particularly severe during the night shift, when the company’s engineers and machine operators were at home and the robots ran the shop floor. Problems with the old monitoring system kept surfacing. “I just didn’t trust it anymore,” Rogers says.
“These KPIs are critical,” Rogers says. “The power of machine learning is being able to analyze millions of product and machinery characteristics, predict if a machine or process is going to break down, and then help us avoid making bad parts.”
Noble Plastics uses Oracle Mobile Cloud Service to extract information from Oracle IoT Asset Monitoring Cloud and send an alert to the appropriate engineer or line operator in the event of a problem. If there’s oil on a pump that’s getting too hot, for example, the production manager doesn’t need to know about it, Rogers says, “but the maintenance tech does.”
Stephen has been with PlasticsToday and its preceding publications Modern Plastics and Injection Molding since 1992, throughout this time based in the Asia Pacific region, including stints in Japan, Australia, and his current location Singapore. His current beat focuses on automotive. Stephen is an avid folding bicycle rider, often taking his bike on overseas business trips, and a proud dachshund owner.
“We had no experience with Oracle,” Rogers says. “But my impression was that Oracle was too big, too expensive for us.” But its pay-as-you-go cloud service is affordable, he says, and Oracle has committed a lot of time and resources to “listening and assisting us through the testing and initial use of the IoT cloud product.”
The Japanese resin supplier will highlight polymers that support sustainability, comfort and performance in automobiles at the plastics-focused trade show in southern Germany.
Oracle Mobile Cloud’s routing feature is important because it helps reduce organizational stress. “I don’t need another alarm,” Rogers says. “If I had an alarm for everything that didn’t go quite right, I’d be responding to alarms all day.”
A novel transparent polymer reportedly outperforms incumbents such as polycarbonate and acrylic in automotive head-mounted displays. Image courtesy of Asahi Kasei/Business Wire.
In parallel, Asahi Kasei will introduce its solvent-based recycling process for the first time in Europe. By applying dissolution recycling, high-quality PA 66 can be obtained from process scraps and post-consumer-recycled (PCR) materials such as airbags.
At Fakuma, Asahi Kasei also will show multilayer cooling pipes that do not require an adhesive layer. These two-layer pipes employ the company’s Leona polyamide (PA) on the outside and Xyron mPPE on the inside. This product offers excellent bending properties, hydrolysis resistance, and low ion elution properties.
The company’s engineers now spend more time analyzing problems and designing new products, he says. “If life is better at Noble, it’s easier to keep employees and retain customers,” Rogers says. “And what could be better than that?”
The company will also present its comprehensive solutions for establishing a sustainable life cycle for PA 66. In the field of chemical recycling, the company works with Japanese partner company Microwave Chemical, utilizing a microwave process to depolymerize automotive airbags and other PA 66–based parts and directly obtain the monomers hexamethylenediamine (HMD) and adipic acid (ADA). Currently undergoing trials, the process is expected to achieve high yields with low energy consumption. The monomers obtained can then be used to manufacture new PA 66.
From automotive head-up displays to head-mounted displays and smart glasses, requirements related to the weight and design of optical devices have become increasingly demanding. Asahi Kasei’s transparent AZP polymer features almost zero birefringence, overcoming the challenges of conventional transparent polymers in applications with polarizing light. Its superior processability compared to glass enables the large-scale production of injection-molded optical components that fulfill demanding customer requirements.
Asahi Kasei will also showcase a bio-based and biodegradable cellulose nano fiber (CNF) at Fakuma. This material is made from cotton linter and features high heat resistance and a network-forming capability. CNF-reinforced PA exhibits thixotropic behavior, making it highly suitable for 3D-printing applications requiring dimensional accuracy, a smooth appearance, and mechanical performance. Furthermore, CNF exhibits superior material recyclability compared to glass fibers.
At the battery island, the company will showcase Xyron modified polyphenylene ether (mPPE) featuring high non-halogenic flame retardance and low ion elution properties. This material is suitable for thermal management applications in EV batteries.
The company’s 10-year-old asset-monitoring system was supposed to text somebody if a machine went down, but every once in awhile that system stopped working. “There would be a power glitch or our servers would lock up,” says Noble Plastics technology director Scott Rogers. When the system failed, Rogers says, his team was flying blind, risking excessive damage to equipment and large batches of unusable parts. “These events were having a negative effect on our business, causing excessive waste and production delays,” he says.
Not wanting to put stress on the organization by making people work the graveyard shifts (and not wanting to hire and train more people), the company turned to the cloud.
Bonding to the polypropylene (PP) core layer is possible in the same or separate injection molding step. The strong chemical bonding between all layers eliminates the need for additional adhesive layers. Asahi Kasei's new SEBS contributes to reducing the total number of materials, simplifying the manufacturing process, and improving the recyclability of interior components.
A dual-layer polyamide/mPPE cooling pipe for EV battery thermal management offers excellent bending properties, hydrolysis resistance, and low ion elution properties. Image courtesy of Asahi Kasei/Business Wire.
Balancing sustainability and functionality without sacrificing cost-competitiveness is a major issue for car manufacturers. To tackle this challenge, Asahi Kasei is currently developing a thermoplastic styrene block copolymer (SEBS) grade for automotive interior surfaces, which require good haptics and soft touch. Conventional approaches use different materials and production technologies for the skin, foam, and core layers in automotive instrument panels, door panels, armrests, or center consoles. The new SEBS material is suitable for both skin and foam layers, which can be molded in one step by utilizing a core back injection molding process.
GETTING A QUOTE WITH LK-MOULD IS FREE AND SIMPLE.
FIND MORE OF OUR SERVICES:
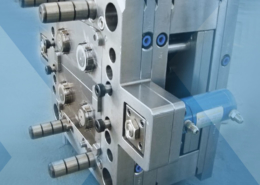
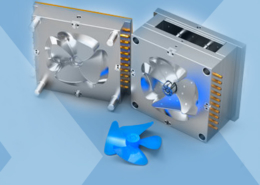
Plastic Molding

Rapid Prototyping
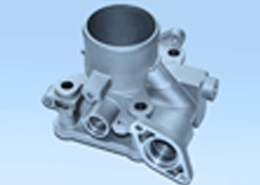
Pressure Die Casting
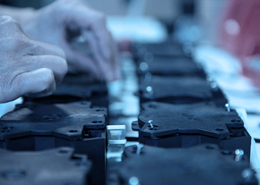
Parts Assembly
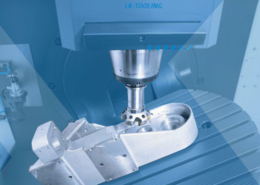