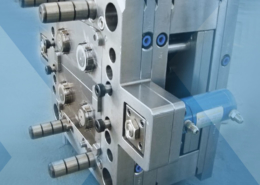
Sustainable Injection Moulding Technology for High-Quality Plastic Parts - plast
Author:gly Date: 2024-09-30
SPEE3D participated in a U.S. Army Combat Capabilities Development Command (DEVCOM) Army Research Laboratory (ARL) demonstration. The demo took place at the University of Tennessee Knoxville and ran from the...
In the subsequent articles of this series, we will look at some of the advantages of 3D printed molds and dies for injection molding and die casting, as well as some of the specific AM processes used and some specific applications.
Depending on the exact requirements of the parts, the AM technology chosen need not be metal. Instead, material jetting and SLA can be used to make molds with high accuracy and good surface finish. This is particularly true for smaller parts, less than 150 mm in size.
The Instapak iMold system tested at the Parts Now facility was designed to create custom-engineered foam cushions by combining two liquid components to create polyurethane packaging foam. The process begins when the system dispenses the liquid foam using patented Foam Dispersion technology, which can strategically place the foam anywhere within the bag.
Parts Now also found it could reuse the molded Instapak® end caps two to three times before needing to be replaced. "When returns arrive that are packaged with the molded end-caps, the boxes are simply opened and the customer's defective core is removed to be remanufactured.
Following the successful testing of the new molded cushions, Parts Now began transitioning to molded-foam end-cap cushions at the start of 2009. When asked about the adjustments that had to be made to accommodate the new systems, Olson said, "The molding systems required very few changes to our facility and were easily integrated, thanks in part to Sealed Air's dedicated sales and account representatives."
"If end caps are crumpled, damaged or no longer suitable for reuse, we take them to the shipping department and they are used for void fill," said Olson. "I'd estimate that about 90 percent of the molded cushions we ship come back to our facility."
Multiple cushion designs can be produced with the Instapak iMold® system and operators can easily change from one cushion to another in a matter of seconds with the system's RFID mold sensing technology, which quickly recognizes a new mold and begins the proper dispensing process.
Stay up-to-date on all the latest news from the 3D printing industry and receive information and offers from third party vendors.
Sealed Air and Parts Now began their relationship in 1996 and have since worked to ensure that Parts Now packages products in a way that reduces damage and overall cost, while minimizing the amount of packaging materials necessary. Due to the longstanding relationship between the companies, Sealed Air approached Matt Olson, Parts Now industrial engineer, and Bob Banke, Parts Now vice president of operations, about testing a new system in their facility.
3D printing dies has many of the same benefits as producing molds for injection molding with AM: fast turnaround and the ability to produce complex geometries. 3D printing can be much more cost-effective when the die will be used for small batch production.
As adoption of 3D printing spreads throughout the larger sector of industrial manufacturing, the value of the technology as more than just a rapid prototyping tool is becoming increasingly evident. Even when additive manufacturing (AM) isn’t being used to produce end parts, businesses are learning that it can be used for the fabrication of tooling for their traditional production processes. In particular, 3D printing molds and dies for injection molding and die casting holds a lot of potential due to the various benefits that AM offers in terms of making custom, on-demand and complex parts.
As 3D Hubs explains in a particularly useful design guide for 3D printing injection molds, aluminum frames are often used to lend support for 3D printed, plastic mold inserts against the pressure and heat of the injection process. Without such a frame, molds are more likely to warp from continued use, but conformal cooling channels can be more easily integrated into the plastic mold. If you’re 3D printing a mold out of metal in the first place, however, you don’t have to worry about this.
Generally dies must be made from metal to survive the high heat and pressure of the die casting process, which isn’t necessarily true for some investment casting techniques. Companies that specialize in 3D printing dies and inserts (used to modify dies and molds) report having a hard time selecting the proper materials. Canadian company Exco Engineering has sometimes chosen maraging steel over H13 tool steel (which might more normally be used for traditional die-casting) due the high porosity and cracking with they’ve experienced 3D-printed molds made from H13. However, as we’ll discuss in a future post, there are technologies that open up the possibility of using multiple metals to achieve certain results for 3D-printed dies.
Parts Now plans to continue to update and examine its packaging and shipping methods with the goal of always improving its current process. "We are comfortable in knowing that as business increases, there is plenty of built-in capacity with our Sealed Air solutions," said Olson.
If those end caps are in good shape, they go into specified bins where they will be reused to package other refurbished components," said Olson.
"We found that while the Instapak foam-in-bag cushions performed well, the packaging was only used once because it was very difficult for customers to re-pack their cores for a return shipment," said Olson. "This added cost to the refurbishment processes since cores that were improperly packed had a higher probability of arriving at our facility damaged and requiring additional repair."
Die casting is a process that is very similar to injection molding except that you swap out melted plastic for molten metal. The liquid metal is injected at high pressure into a metal die (the same as a mold in this case), which fills the die’s cavities and hardens to form a metal part. Die casting is usually used for large quantities of small- to medium-sized parts. You’ll find die casting used for such components as belt buckles and car engines.
Once the Instapak molded cushions are produced by the Instapak iMold® system at the Parts Now facility, they are batched and brought to a packaging line and placed in overhead delivery bins where packers can quickly and easily access the right size cushion for each laser printer part on the line. The use of molded end-caps speeds up the packaging process considerably and allows Parts Now employees to keep up with daily packaging demands.
Amidst the backdrop of last week’s FAA/EASA workshop in Wichita, Bill Bihlman, Consultant and Volunteer to SAE, analyzes the state of AM aerospace standards. Commercial aviation is notoriously risk averse....
Other reasons 3D printing might be chosen for mold production include the short turnaround time. A printed mold can be made in just a few days or a couple of weeks, compared to a five- to seven-week lead time for molds made with a CNC machine.
Now, instead of using two bags of foam for most of its cartridges, Parts Now uses molded end-cap cushions, which require less foam material, retain a refined aesthetic appearance, and can be reused multiple times by Parts Now and its customers. The smaller and mid-size fusers only require two end-cap cushions, which are placed on each end of the fuser, providing the necessary protection and adding stability and support to the pack. For the larger and heavier fuser models, Parts Now uses three-part molded foam cushions to completely encapsulate the product and protect it from shipping damage.
The foam-filled bag is then drawn into the integrated mold cavity. As the liquid foam expands, the system encloses the bag within the mold by means of an automated door lid. Once the foam cures and conforms to the mold image, the Instapak iMold system opens the mold door and ejects the finished foam cushion into a bin.
There’s lots to choose from in this week’s 3D Printing Webinar and Event Roundup! Stratasys continues its North American tour, as well as its in-person training classes, and HP will...
The most common for mass manufacturing plastic parts, injection molding involves injecting liquid plastic into a mold at high pressure. Filling all of the cavities of the mold, the plastic hardens, and the finished part is removed. Most often, the polymers used are thermoplastics, which are melted at high temperatures and cool upon entering the mold.
Established in 1989, Parts Now is considered the industry leader in profitable solutions for companies that service business printers. As the number one supplier of laser printer parts in North America, Parts Now is a global company and the only authorized distributor for five OEMs - Hewlett Packard, Lexmark, Toshiba, Canon and OKIData. In addition to successfully growing its business, Parts Now earned the Wisconsin Business Friend of the Environment Award in pollution prevention for its dedication to sustainable practices.
Before incorporating the molding systems into its operations, Parts Now and Sealed Air conducted testing that lasted for nearly three years. In the summer of 2008, Parts Now installed its first Instapak iMold® system at its Middleton, Wis. facility. During this time, Sealed Air made alterations to the design and functionality of the machine. Additionally, Sealed Air conducted ISTA 1A testing in its certified Package Design & Development Center (PDDC) in order to validate the new package designs.
By adopting an automated molded cushion process, Parts Now realized they could offer customers consistent and reusable cushions to help streamline the repacking and returns process. Because Parts Now required multiple unique cushion designs for the diverse shapes and sizes of the printer parts, an automated system that could easily interchange various molds was important as well. For these reasons, Parts Now was an ideal operation to test the new Instapak iMold system.
By reusing these end caps, Parts Now reduces packaging costs and the amount of packaging materials that were once sent to landfills.
Register to view and download proprietary industry data from AM Research and 3DPrint.com Questions? Contact info@3dprint.com
"Sealed Air approached us about a new automated Instapak® molding system that was being beta-tested with existing Sealed Air customers," explained Olson. "Due to our close relationship with Sealed Air, we agreed to be part of the initial testing group for what came to be known as the Instapak iMold system."
Additionally, after switching to the Instapak® molded cushions, Parts Now has seen a reduction in damage during shipping, particularly with the heavier fuser models. "We have fewer cases of shipping damage," Olson said. "When we conducted our "Voice of the Customer" survey, the reaction was extremely positive. They appreciate the continuous improvements we make to ensure our products arrive to our customer in the same condition as when they leave our facility."
As Parts Now continues to expand and grow, the company knows that its packaging process must evolve and grow with it in order to successfully meet its customers' expectations. This includes using packaging solutions that are both cost effective and sustainable.
Sealed Air Instapak iMold systemMany companies are searching for a protective packaging solution that is both cost-effective and sustainable. Wisconsin-based Parts Now found this balance of environmental responsibility and product protection when it worked with its packaging supplier, Sealed Air, to examine its packaging operations and test a new automated system.
"We certainly saw a measurable return on investment by switching to the molded cushions," said Olson. "In practical terms, we save $500 per day by reusing and recycling our packaging materials. This is the number that we came up with when we went from a void-fill packaging mechanism using virgin materials in our shipping department to reusing our molded packaging as void fill." Parts Now estimates that the average weight cost reduction per pack was about 70 cents, and it saw a 26 percent decrease in the material usage. Parts Now now packs 850 to 900 fusers a day with six to eight people working the line. "Our workers were positive about the change because the systems are fast and easy to use," said Olson.
In a major leadership shift, VulcanForms has appointed Kevin Kassekert as its new CEO and Jay Martin as President. This change comes at a crucial time as the company moves...
A die casting insert with integrated cooling channels 3D printed by Exco Engineering. Image courtesy of Exco Engineering.
When Parts Now began shipping printers and printer parts more than two decades ago, the majority were packaged with a crinkled paper product. Later, Parts Now started using molded flat pads and Instapak foam-in-bag packaging for fusers. The company initially used two bags of Instapak® foam to surround the fuser. This provided adequate protection for each fuser, but as business grew, the need for a more efficient process became apparent. Sometimes the finished product would sit in queue for two to three days before packers would get a chance to work through the backlog of finished fusers waiting for packaging.
Stay up-to-date on all the latest news from the 3D printing industry and receive information and offers from third party vendors.
Typically, molds are precision-machined from aluminum or steel, which can cost from thousands to hundreds of thousands of dollars. Therefore, injection molding is most cost-effective at high volumes in making tens of thousands to millions of parts. For low-run injection molding of 50 to 100 parts, 3D printing can be a more cost-effective option.
"We conducted testing internally, as well as by sending items from our Wisconsin facility to our California facility," said Olson. "Once the items arrived safely in California, they were repacked with the same molded cushions and shipped back. When the items made the round trip safely, we realized that there was a great opportunity to reuse these molded cushions multiple times."
GETTING A QUOTE WITH LK-MOULD IS FREE AND SIMPLE.
FIND MORE OF OUR SERVICES:
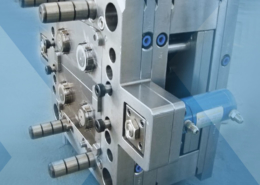
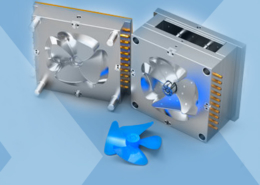
Plastic Molding

Rapid Prototyping
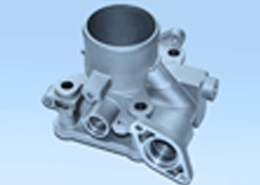
Pressure Die Casting
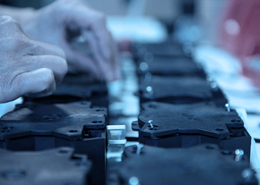
Parts Assembly
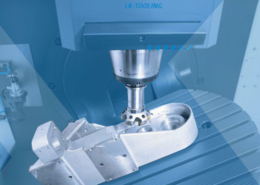