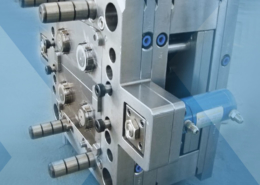
Sustainable Injection Moulding Technology for High-Quality Plastic Parts - plast
Author:gly Date: 2024-09-30
In washing machines, for example, this new three-dimensional carbon fiber composite technology can reduce the inertia to start the machine drum moving, compared to current metal alternatives, which can mean greater efficiency, and potentially a lower carbon footprint for the machine. Additionally, by considering the use of the Ultem resin-based carbon fiber composites with Kringlan's manufacturing technology, appliance manufacturers can potentially save costs by reducing the number of secondary operations required to develop key parts.
Simulation software evaluates the material performance in the office. Materials that fail can be easily replaced with superior materials. The product design is quickly improved for lighter, more robust designs with outstanding performance characteristics.
These complex simulations can predict the product microstructure, part defects, and performance characteristics and guide the designer through process optimization. By avoiding this wasted time, scrap production is avoided, equipment may be best utilized, and the time to market is expedited.
AS9100 refers to aircraft maintenance and repairs. AS9100 B covers the storage and distribution of aircraft parts. AS -5553 is the Aerospace standard for the prevention and use of counterfeit parts. ITAR (International Traffic in Arms Regulations)is specific to the Defense industry and regulates exports overseen by the United States Department of State (DOS). Manufacturing any items intended for defense-related or military end-use applications requires ITAR compliance. These certifications are needed to operate in the aerospace industry.
Aerospace Manufacturing Methods for Prototyping and Production, Pre-Production Prototyping, Production, Material, and Quality for Aerospace Products. Learn more now!
Recently, hybrid manufacturing models have been developed for aerospace and other industries. The hybrid model combines subtractive manufacturing equipment with additive equipment. This may include post-processing finishing, drilling extremely accurate holes, or other subtractive manufacturing processes.
These include; powder bed fusion, material and binder jetting, vat polymerization, direct energy deposition, and material extrusion.
"This new material technology resulting from the ongoing collaboration between Kringlan and Sabic has the potential to be a breakthrough for OEMs in multiple industries," says Steffen Heinecke, CEO of Kringlan. "Already, in the automotive industry alone, several OEMs have shown interest in the carbon composite wheel application, which can enable the reduction of CO2 from a passenger car by two to three percent."
In 2022, the aerospace industry has been boosted by increased aircraft and military orders and the additional demand for air travel. While fuel prices impact air travel and overall costs, The growth of new technologies is improving efficiencies as the industry pursues more fuel-efficient, lower-emission product designs.
Sabic, Kringlan Composites (Otelfingen, Switzerland) and other industry partners are working to further advance the development of the world's first thermoplastic composite wheel. The wheel leverages the properties of Sabic's polyetherimide (PEI) resin and Kringlan's three-dimensional composite design capabilities to create a material solution that can be used to replace heavier traditional materials, such as metal and aluminum alloy.
Industry certifications help companies identify manufacturers that meet the rigorous quality standards of the aerospace industry. The most important certifications for aerospace and defense companies include AS9100D, C, and B, ISO-9001:2015, AS-5553, and ITAR. AS9100 D is the ISO-9001 version of quality requirements for aerospace and was developed by the Society of Automotive Engineers (SAE) and the European Association of Aerospace Industries (EAAI). AS9100 D is the standard for aerospace quality.
With on-demand production, inventories are reduced, as are storage and warehousing costs. The savings can add up quickly with expensive aerospace components. On-demand production is ideal for additive technologies, which often require part and weight reduction and rapid prototyping.
Other materials for unique non-metal applications include boron, carbon fiber, and liquid silicone rubber. New materials include meta-materials, a new class of performance-specific materials with properties not found in naturally occurring materials. Aircraft exhausts may use metamaterials for exhaust systems to reduce noise.
To advance the wheel's development, Kringlan and Sabic have been working on a prototype for a German automotive manufacturer. This innovative and lightweight wheel will reportedly be strong, light, stunning in design. The significant weight savings made possible through Kringlan's revolutionary wheel design, coupled with the material technology employed, can improve fuel economy.
When considering the use of expensive materials in aerospace applications, additive manufacturing has a significant advantage over subtractive manufacturing technologies, where a large portion of the material machined is waste. The aerospace industry highly values component weight reduction. This translates to either less fuel or added range for the craft. Additive manufacturing can take several components and develop a single item while reducing weight and maintaining overall strength and performance.
Additive technologies allow rapid prototyping to expedite the evaluation and testing of new products and materials. Products are quickly designed and evaluated for performance characteristics when combined with simulation software. This powerful software optimizes complex product designs in hours instead of weeks.
Digital technologies and cutting-edge manufacturing methods have provided an advantage for aerospace manufacturing. Aerospace companies' reliance on these technologies will increase as they continue to streamline product design and development. Sourcing should continue transitioning towards regional suppliers and distributed manufacturing services to save time and money and improve quality. The industry is also pursuing new propulsion technologies, including hydrogen and hybrid models. Renewable energy is also an ongoing trend in the aerospace industry.
Sabic, Kringlan Composites (Otelfingen, Switzerland) and other industry partners are working to further advance the development of the world's first thermoplastic composite wheel. The wheel leverages the properties of Sabic's polyetherimide (PEI) resin and Kringlan's three-dimensional composite design capabilities to create a material solution that can be used to replace heavier traditional materials, such as metal and aluminum alloy.
The design of the part also provides the flexibility for the wheel to be mounted with traditional metal spokes, or spokes with carbon fiber-reinforced Ultem resin composites, potentially enabling even greater weight savings.
While the first application of this new technology is being driven in the automotive industry, its potential reach extends to multiple industries where weight reduction is a key driver. To illustrate this, in consumer appliances, OEMs are focused on designing their products to achieve energy efficiency certifications. With this carbon fiber composite using Ultem resin, appliance OEMs can replace metal with a lighter and equally strong technology, which can help to reduce the amount of energy used during operation and contribute to the energy efficiency performance required for certification.
The full composite wheel design complies with current standards set for metal wheels by the German testing institute TüV, enhancing the opportunity to work with additional global automotive OEMs for the prototyping of lightweight wheels according to their specific design and specifications.
Based on surveys of aerospace business managers, the general business outlook for aerospace next year ranges from "somewhat to very positive." Agility is needed to stave off potential market instability, and technological growth has been at the forefront of the trends expected to lead the industry in the coming years. In addition to the need for adding more talent to the workforce, the aerospace industry trends include many cutting-edge programs that are defined below:
These technologies have taken off due to the fragility of the global supply chain and the ability of additive manufacturing technologies. These issues have been critical when companies require more agile ways of developing, sourcing, and building products.
Since aerospace products are utilized in demanding and hazardous environments, the products must exceed the performance requirements of standard products. Finished products are evaluated for testing to ensure quality compliance and certification. This often includes coordinate measuring machines (CMMs), computed tomography, x-ray analysis, performance testing, and destructive testing methods. Lot traceability and comprehensive records are required in the event of product failure. Material certifications and product testing data are required for most products.
Additive manufacturing parts also require certifications by different agencies such as the Federal Aviation Administration (FAA), European Space Agency (ESA), Directorate General of Civil Aviation (DGCA), The Center for Military Airworthiness & Certification (CEMILAC), etc. These agencies check the factors impacting product quality and process control. These agencies look for data regarding the material strength properties, testing, performance, process control, and lot traceability.
Additive manufacturing technologies have been instrumental in these industry trends and continue their rapid growth with newly engineered materials. The three key technologies are 3D printing, composite manufacturing, and other additive manufacturing (AM) technologies.
This article discusses Aerospace Manufacturing Methods for Prototyping and Production, the pre-production and prototyping process, methods, production, materials, and quality.
The development of metal additive technologies has been a significant factor in the growth of the overall additive manufacturing sector. Additive processes such as directed metal laser sintering (DMLS), laser powder bed fusion (L-PBF), electron beam powder bed fusion (EB-PBF), and directed energy deposition (DED) create parts with metals. The process manufacture parts from aluminum alloys, copper alloys, iron superalloys, nickel alloys, precious metals, refractory metals, titanium alloys, and more.
The aerospace industry has long been at the forefront of manufacturing innovation as companies have continually pursued cost-reduction methods, improved efficiencies, increased equipment utilization, enhanced profitability, and meeting and exceeding expectations. Advanced manufacturing practices have helped advance the ability to develop prototypes and production parts.
From 2010 to 2020, the additive manufacturing market doubled, projected to gain over 20% annually from 2022 to 2028. The industry is expected to continue to develop new composite materials and to integrate and develop advanced manufacturing technologies. The aerospace industry continues to pursue both dimensionally larger and smaller products, the attainment of volume production, and the manufacture of complex products that were once an assembly of many parts.
"Combining Sabic's high-performance Ultem resin with Kringlan's proprietary three-dimensional manufacturing technology for carbon composites offers OEMs the opportunity for reduced weight, lower production costs, as well as material recyclability. When compared to other thermoplastic materials, the Ultem resin composite concept offers superior strength at high temperatures, dimensional stability as well as resistance to chemicals," says Thierry Materne, Vice President, Technology & Innovation for Sabic's Innovative Plastics business.
GETTING A QUOTE WITH LK-MOULD IS FREE AND SIMPLE.
FIND MORE OF OUR SERVICES:
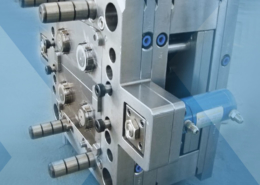
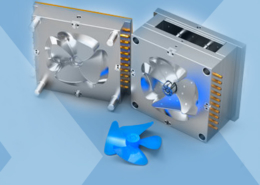
Plastic Molding

Rapid Prototyping
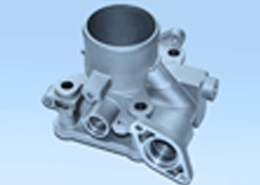
Pressure Die Casting
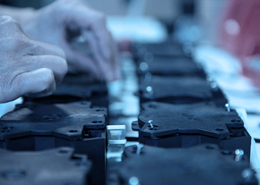
Parts Assembly
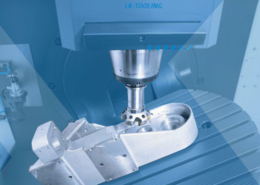