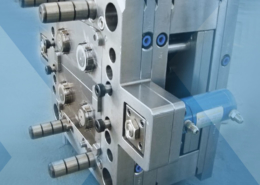
Sustainable Injection Moulding Technology for High-Quality Plastic Parts - injec
Author:gly Date: 2024-09-30
In this collection of articles, two of the industry’s foremost authorities on screw design — Jim Frankand and Mark Spalding — offer their sage advice on screw design...what works, what doesn’t, and what to look for when things start going wrong.
• Using sprue break, which adds to cycle time (a little or a lot, depending on how far the barrel is retracted) and can lead to nozzle drool, leakage between the nozzle and sprue bushing (when drooled material obstructs close contact), and deformation of the nozzle tip and/or sprue bushing from repeated banging together—leading to even more material leakage.
Strings originate at the molten center of the melt channel in a machine nozzle tip, which often does not solidify within a desirable cycle time.
The firm currently uses eight machining centres from DMG MORI for tool production, including DMU monoBLOCKs, an HSC 75 linear and, most recently, a DMU 100 P duoBLOCK with PH Cell 2000 automation system for pallet handling to allow unattended production at night and during the weekends.
Fattori concedes that the thin fins inside the IMC nozzle will tend to wear, especially with filled materials and/or high injection speeds. Wear will gradually reduce the fins’ effectiveness at heat transfer. “Some tips have been running for over a year now with minimal wear,” Fattori comments. “But let’s say you’re running 33% long-glass filled nylon and you have to replace the tip once a month—that’s still a lot cheaper than having to literally rebuild the mold.”
Cross-section of IMC nozzle tip shows tapered internal heat-sink fins, which start at the “transition plane,” which is where the solidified material separates from semi-solidified melt on part ejection. Also shown is the novel profile of the tip, which reduces thermal mass for improved temperature control.
Take a deep dive into all of the various aspects of part quoting to ensure you’ve got all the bases—as in costs—covered before preparing your customer’s quote for services.
As Fattori explains, stringing results when the center of the slug of plastic inside the machine nozzle-tip orifice has not sufficiently solidified when the mold opens. When the part is ejected, it drags thin strings of still-molten plastic after it. Those strings tend to be static charged and therefore stick to the mold. If they hang over the parting line, those thin strings of plastic will hob the mold—even a heat-treated steel tool—eventually leading to flashing. Fattori says that can’t be fixed properly by simply grinding the parting line—it requires an extensive mold rebuild, “all because of a $20 nozzle tip.” He adds, “I know of one molder that spends thousands of dollars a year on mold repairs due to stringing.”
Plastics Technology covers technical and business Information for Plastics Processors in Injection Molding, Extrusion, Blow Molding, Plastic Additives, Compounding, Plastic Materials, and Resin Pricing. About Us
When, how, what and why to automate — leading robotics suppliers and forward-thinking moldmakers will share their insights on automating manufacturing at collocated event.
Based in the Hungarian capital Budapest, Euroform was established in 1993 to provide a tool and mould making service from design to production and trialling. Approximately 70 employees fulfil innovative solutions for a range of different injection moulding processes, mainly for customers in the automotive industry.
Gifted with extraordinary technical know how and an authoritative yet plain English writing style, in this collection of articles Fattori offers his insights on a variety of molding-related topics that are bound to make your days on the production floor go a little bit better.
The IMC nozzle tips cost more than other tips, because they cost more to make. “But the ROI on any mold that has an extended cycle time to overcome or reduce a stringing problem is typically just a few days,” Fattori asserts. “And the money saved from not having to repair just one mold due to string damage can probably pay for a year’s supply of IMC nozzle tips.”
According to Fattori, most nozzle tips are made of H-13 steel with a Rockwell hardness of 46 to 48 Rc. IMC tips are made of 420 stainless steel with a vacuum bright hardness of 48 to 52 Rc for greater durability.
Despite price increase nominations going into second quarter, it appeared there was potential for generally flat pricing with the exception of a major downward correction for PP.
Introduced by Zeiger and Spark Industries at the PTXPO, the nozzle is designed for maximum heat transfer and uniformity with a continuous taper for self cleaning.
The IMC nozzle tips are available with a ½-in. spherical radius, in eight different orifice sizes of 5/32 in. through 3/8 in. in 1/32-in. increments. Fattori says the bore diameters of the IMC nozzle tips are slightly smaller than their nominal size. But even with the internal fins, the resulting flow area is comparable to most “full-flow” style nozzle tips. He also says that his tips’ large internal transition radius “virtually eliminates ‘dead spots’ where material can stagnate.”
While prices moved up for three of the five commodity resins, there was potential for a flat trajectory for the rest of the third quarter.
Fattori realized that the solution to the problem was to get more cooling into the center of the flow channel in the nozzle tip. He came up with the idea of adding inwardly protruding, heat-conducting metal fins inside the bore of the nozzle tip. These fins are angled, with their maximum height 70% into the melt stream, with their peak at a location Fattori calls the “transition plane” inside the nozzle tip, which is where the molten material will separate on part ejection from the semi-solidified plastic. From this plane, the fins taper down to blend with the front orifice diameter. This taper concentrates the cooling at the transition plane, which flow simulation shows is the area where the greatest concentration of thermal gradients occurs inside the nozzle. The temperature differential between the sprue-bushing nozzle seat and the transition plane was found to be as high as 135° F in the simulations. Using fins to concentrate the cooling at the transition plane ensures the separation point is consistently in the same location, which results in repeatable shot sizes, Fattori adds.
Your very costly mold in that very expensive press is relying on the performance of a $20 nozzle tip that no one ever checks, and has a high probability of not doing its job. Stop learning from your mistakes and start learning how not to make them.
As Euroform almost exclusively manufactures one-offs, pallet handling such as the PH Cell 2000 is the optimal solution. Operators set up jobs offline on several pallets using a zero-point clamping system while machining is in progress on another mould, so production downtime is minimal, even at night.
Oak Ridge National Laboratory's Sustainable Manufacturing Technologies Group helps industrial partners tackle the sustainability challenges presented by fiber-reinforced composite materials.
One more innovation is very simple, but nonetheless valuable to molders. Fattori explains, “For some reason, you have to physically measure the orifice of most nozzle tips with some kind of tool in order to know their size.” He solves that by engraving the orifice size of each IMC nozzle tip on a wrench flat.
After successfully introducing a combined conference for moldmakers and injection molders in 2022, Plastics Technology and MoldMaking Technology are once again joining forces for a tooling/molding two-for-one.
"The recent Corona pandemic, the war in Ukraine and high inflation have clearly shown us that we need to develop constantly in order to remain competitive.
Learn about sustainable scrap reprocessing—this resource offers a deep dive into everything from granulator types and options, to service tips, videos and technical articles.
Additive technology creates air pockets in film during orientation, cutting down on the amount of resin needed while boosting opacity, mechanical properties and recyclability.
Nozzle tips with large orifices are more prone to stringing because they take considerably longer to become semi-solid—usually longer than the best possible cycle time. Molders have tried various methods to reduce string formation, each of which has its own drawbacks:
Say “manufacturing automation” and thoughts immediately go to the shop floor and specialized production equipment, robotics and material handling systems. But there is another realm of possible automation — the front office.
technotrans says climate protection, energy efficiency and customization will be key discussion topics at PTXPO as it displays its protemp flow 6 ultrasonic eco and the teco cs 90t 9.1 TCUs.
Another focus that accompanies business development at Euroform is digitalisation. The company has had a paperless working environment for many years, from design through to quality control. The mould maker is an enthusiastic adopter of the digital 'my DMG MORI' app when it comes to online service requests, which Zwick said significantly accelerates the process of calling in a service technician.
Euroform has been using machine tools from DMG MORI since 1995, latterly in a modern factory that it moved into in 2011 and expanded in 2016. Managing Director responsible for day-to-day business at Euroform, Krisztina Zwick, mentioned the supplier's broad machine portfolio and good service: "DMG MORI was one of the first machine tool manufacturers to open a subsidiary in Hungary, which meant that response times were always quick when service was required. Our latest investment in automation was necessary to utilise the machine during unattended shifts, giving us a competitive edge.”
In this three-part collection, veteran molder and moldmaker Jim Fattori brings to bear his 40+ years of on-the-job experience and provides molders his “from the trenches” perspective on on the why, where and how of venting injection molds. Take the trial-and-error out of the molding venting process.
While the melting process does not provide perfect mixing, this study shows that mixing is indeed initiated during melting.
The aim of this presentation is to guide you through the factors and the numbers that will help you determine if a robot is a smart investment for your application. Agenda: Why are you considering automation? What problems are you trying to solve? How and why automation can help Crunch the numbers and determine the ROI
In this collection of content, we provide expert advice on welding from some of the leading authorities in the field, with tips on such matters as controls, as well as insights on how to solve common problems in welding.
Formnext Chicago is an industrial additive manufacturing expo taking place April 8-10, 2025 at McCormick Place in Chicago, Illinois. Formnext Chicago is the second in a series of Formnext events in the U.S. being produced by Mesago Messe Frankfurt, AMT – The Association For Manufacturing Technology, and Gardner Business Media (our publisher).
While prices moved up for three of the five commodity resins, there was potential for a flat trajectory for the rest of the third quarter.
Plastics Technology’s Tech Days is back! Every Tuesday in October, a series of five online presentations will be given by industry supplier around the following topics: Injection Molding — New Technologies, Efficiencies Film Extrusion — New Technologies, Efficiencies Upstream/Downstream Operations Injection Molding — Sustainability Extrusion — Compounding Coming out of NPE2024, PT identified a variety of topics, technologies and trends that are driving and shaping the evolution of plastic products manufacturing — from recycling/recyclability and energy optimization to AI-based process control and automation implementation. PT Tech Days is designed to provide a robust, curated, accessible platform through which plastics professionals can explore these trends, have direct access to subject-matter experts and develop strategies for applying solutions in their operations.
In a time where sustainability is no longer just a buzzword, the food and beverage packaging industry is required to be at the forefront of this innovation. By adopting circular packaging processes and solutions, producers can meet regulatory requirements while also satisfying consumer demand and enhancing brand reputation. Join Husky to learn more about the broader implications of the circular economy — as well as how leading brands are leveraging this opportunity to reduce costs, increase design flexibility and boost product differentiation. Agenda: The cost and operational benefits of embracing circularity Key materials in circular packaging — including rPET and emerging bioplastics How to design a circular food and beverage package Strategies for selecting sustainable closures to future-proof packaging solutions Optimization and streamlining of production processes for enhanced efficiency How Husky Technologies can enable your sustainable success
IMC’s novel injection nozzle tip (available from Progressive Components) has internal heat-sink fins to cool the center of the melt channel and prevent strings. Sand-blasted finish reportedly ensures a better seal against the sprue bushing.
Join Engel in exploring the future of battery molding technology. Discover advancements in thermoplastic composites for battery housings, innovative automation solutions and the latest in large-tonnage equipment designed for e-mobility — all with a focus on cost-efficient solutions. Agenda: Learn about cutting-edge thermoplastic composites for durable, sustainable and cost-efficient battery housings Explore advanced automation concepts for efficient and scalable production See the latest large-tonnage equipment and technology innovations for e-mobility solutions
The new tips have eliminated stringing in tests with PS, HDPE, LDPE, PP, PVC, ABS, ASA, acrylic, nylon, acetal, PC and PPS (filled and unfilled). However, Fattori cautions that “these new IMC nozzle tips are only to be used on molds with a stringing problem, or molds for which you cannot reduce the cycle time without having a stringing problem. The new nozzle tips are so efficient at removing heat that they can cause a freeze-off condition, particularly on the smaller orifice sizes.”
This Knowledge Center provides an overview of the considerations needed to understand the purchase, operation, and maintenance of a process cooling system.
Processors with sustainability goals or mandates have a number of ways to reach their goals. Biopolymers are among them.
Real-world testing (here with ABS) confirms that the IMC nozzle tip (top) eliminates stringing, regardless of the orifice size or material type.
• Lowering the nozzle-tip temperature, which can increase the risk of cold slugs and nozzle freeze-off, leading to cosmetic flaws in parts and/or to costly downtime;
Mixed in among thought leaders from leading suppliers to injection molders and mold makers at the 2023 Molding and MoldMaking conferences will be molders and toolmakers themselves.
Successfully starting or restarting an injection molding machine is less about ticking boxes on a rote checklist and more about individually assessing each processing scenario and its unique variables.
The new IMC nozzle tip incorporates four features to greatly increase the rate of heat transfer to compensate for momentary temperature rises:
Discover how artifical intelligence is revolutionizing plastics processing. Hear from industry experts on the future impact of AI on your operations and envision a fully interconnected plant.
Second quarter started with price hikes in PE and the four volume engineering resins, but relatively stable pricing was largely expected by the quarter’s end.
Stefan Wolf, Euroform's managing partner said: "We play a pivotal role in automotive supply chains and our work begins in the early development phase of a new vehicle. Technical competence is crucial for exploiting the potential of innovative manufacturing solutions and CADCAM systems."
This month’s resin pricing report includes PT’s quarterly check-in on select engineering resins, including nylon 6 and 66.
According to Fattori, “A nozzle tip undergoes both a constant and cyclical thermal battle. It is heated in the back half by the machine’s nozzle body. It is cooled in the front half by contact with the sprue-bushing seat and by convection into the atmosphere.” These opposing thermal forces are fairly constant and come into equilibrium over time. But, he notes, that equilibrium is upset by the substantial heat generated during each injection cycle from frictional shear of the material.
Join Wittmann for an engaging webinar on the transformative impact of manufacturing execution systems (MES) in the plastic injection molding industry. Discover how MES enhances production efficiency, quality control and real-time monitoring while also reducing downtime. It will explore the integration of MES with existing systems, emphasizing compliance and traceability for automotive and medical sectors. Learn about the latest advancements in IoT and AI technologies and how they drive innovation and continuous improvement in MES. Agenda: Overview of MES benefits What is MES? Definition, role and brief history Historical perspective and evolution Longevity and analytics Connectivity: importance, standards and integration Advantages of MES: efficiency, real-time data, traceability and cost savings Emerging technologies: IoT and AI in MES
The DMU 100 P duoBLOCK 5-axis machining centre with PH Cell 2000 pallet storage and handling system on the shop floor at Euroform, Budapest.
Multiple speakers at Molding 2023 will address the ways simulation can impact material substitution decisions, process profitability and simplification of mold design.
Exhibitors and presenters at the plastics show emphasized 3D printing as a complement and aid to more traditional production processes.
Join this webinar to explore the transformative benefits of retrofitting your existing injection molding machines (IMMs). Engel will guide you through upgrading your equipment to enhance monitoring, control and adaptability — all while integrating digital technologies. You'll learn about the latest trends in IMM retrofitting (including Euromap interfaces and plasticizing retrofits) and discover how to future-proof your machines for a competitive edge. With insights from industry experts, it'll walk you through the decision-making process, ensuring you make informed choices that drive your business forward. Agenda: Maximize the value of your current IMMs through strategic retrofitting Learn how to integrate digital technologies to enhance monitoring and control Explore the benefits of Euromap interfaces and plasticizing retrofits Understand how retrofitting can help meet new product demands and improve adaptability Discover how Engel can support your retrofitting needs, from free consultations to execution
Across the show, sustainability ruled in new materials technology, from polyolefins and engineering resins to biobased materials.
Mike Sepe has authored more than 25 ANTEC papers and more than 250 articles illustrating the importance of this interdisciplanary approach. In this collection, we present some of his best work during the years he has been contributing for Plastics Technology Magazine.
Mold maintenance is critical, and with this collection of content we’ve bundled some of the very best advice we’ve published on repairing, maintaining, evaluating and even hanging molds on injection molding machines.
Join KraussMaffei for an insightful webinar designed for industry professionals, engineers and anyone interested in the manufacturing processes of PVC pipes. This session will provide a comprehensive understanding of the technology behind the production of high-quality PVC pipes: from raw material preparation to final product testing. Agenda: Introduction to PVC extrusion: overview of the basic principles of PVC pipe extrusion — including the process of melting and shaping PVC resin into pipe forms Equipment and machinery: detailed explanation of the key equipment involved — such as extruders, dies and cooling systems — and their roles in the extrusion process Process parameters: insight into the critical process parameters like temperature, pressure and cooling rates that influence the quality and consistency of the final PVC pipes Energy efficiency: examination of ways to save material and energy use when extruding PVC pipe products
Ultradent's entry of its Umbrella cheek retractor took home the awards for Technical Sophistication and Achievement in Economics and Efficiency at PTXPO.
Wolf concluded: "Automated manufacturing and digital processes are essential, given the current challenges in the global marketplace.
When Euroform ordered the new DMU 100 P duoBLOCK, DMG MORI already had a large pallet handling system in development, based on the smaller, proven, modular PH Cell 300. The bigger capacity automation system handles pallets measuring up to 1,100 mm in diameter, so is able to deploy Euroform's 1,000 × 800 mm pallets. The PH Cell 2000 has twelve pallet positions on two levels and can accept workpieces up to 1,350 mm tall. (Other variants are available with three or four racks housing up to 17 or 21 pallets respectively.)
One more thing: Fattori says, “In case you were wondering, the internal heat-sinking fins have also proven to work well in hot sprue bushings and in hot-runner systems.”
3. The overall length of the nozzle tips varies in order to vary the land lengths: The larger the orifice, the longer the land to increase thermal conductivity. If the land lengths were all the same, tips with small orifices would be more susceptible to generating cold slugs, and tips with large orifices could string under almost any condition.
The Plastics Industry Association (PLASTICS) has released final figures for NPE2024: The Plastics Show (May 6-10; Orlando) that officially make it the largest ever NPE in several key metrics.
1. The thick mass in the front was replaced with a contoured outer shape that corresponds to the internal geometry, with the smallest diameter at the transition plane.
Across all process types, sustainability was a big theme at NPE2024. But there was plenty to see in automation and artificial intelligence as well.
August 29-30 in Minneapolis all things injection molding and moldmaking will be happening at the Hyatt Regency — check out who’s speaking on what topics today.
4. Diameter of the nozzle-tip face is reduced to decrease the amount of contact area between the face of the tip and the sprue-bushing seat. Other nozzle tips, with their large contact area, are greatly affected by how well, or how poorly, the sprue bushing is cooled. Since every mold is different, these nozzle tips can behave inconsistently from one mold to another. Fattori points out that the reduced contact area also results in greater sealing pressure for the same nozzle touch force, preventing carriage blowback and nozzle leakage.
New system automatically cleans mold-cooling lines—including conformal channels—removing rust and calcium, among other deposits, while simultaneously testing for leaks, measuring flow rate and applying rust inhibitor.
• Using a smaller nozzle orifice diameter, which increases the pressure drop through the nozzle tip. That increases shear and often requires a slower injection rate to avoid shear burns—adding to cycle time. What’s more, slow injection through a restrictive bore requires higher injection pressure—risking trouble if the machine is close to being pressure-limited;
The ‘DryerGenie’ marries drying technology and input moisture measurement with a goal to putting an end to drying based on time.
"With targeted investment in technology and the training and further education of junior staff, we will continue to successfully meet these challenges.”
Core Technology Molding turned to Mold-Masters E-Multi auxiliary injection unit to help it win a job and dramatically change its process.
Fattori also notes that as plastic cools inside the nozzle tip, it shrinks away from the inner bore surface, which reduces the rate of heat transfer. But the fins are always in contact with the melt and are in close proximity to the center of the melt stream, increasing the effective cooling rate.
IMC nozzle tips are made of 420 stainless steel, which is harder than the typical H-13 steel. A simple but helpful added feature is the orifice diameter engraved on the wrench flat, unlike most nozzle tips, so no measuring tool is required.
In this collection, which is part one of a series representing some of John’s finest work, we present you with five articles that we think you will refer to time and again as you look to solve problems, cut cycle times and improve the quality of the parts you mold.
After four years in development, an injection machine nozzle tip has been commercialized that is said to eliminate problems of stringing and all the compromises that molders make to avoid it. Jim Fattori, inventor of the IMC nozzle tip, has 40 years’ experience as a plastics tooling engineer and consultant. He heads up his own firm, Injection Mold Consulting LLC, in the Philadelphia area, and writes frequently for this magazine (see his monthly Tooling Know-How columns). His newly patented invention is now available from Progressive Components.
As a result, Fattori states, “A nozzle tip must be able to react quickly to temperature changes, so as to prevent formation of strings within the best cycle time.” That requires efficient heat conduction to remove excess heat from the nozzle tip. But rate of heat conduction is affected by the mass of the object: Greater mass slows heat transfer. In Fattori’s view, “Every standard nozzle tip today has a very large mass. It begins at the back side of the wrench flats and extends all the way to the front face of the tip.”
Five-axis simultaneous machining of workpieces up to 1,100 mm in diameter by 1,600 mm and weighing 2,200 kg had already been carried out on a DMU 100 P duoBLOCK in the factory. Euroform's experience with the machining centre was consistently good, leading to the purchase in 2022 of a latest-generation model with a 1,000 × 1,250 × 1,000 mm working envelope.
Sustainability continues to dominate new additives technology, but upping performance is also evident. Most of the new additives have been targeted to commodity resins and particularly polyolefins.
Thousands of people visit our Supplier Guide every day to source equipment and materials. Get in front of them with a free company profile.
Resin drying is a crucial, but often-misunderstood area. This collection includes details on why and what you need to dry, how to specify a dryer, and best practices.
• Using a nozzle-tip insulator, which Fattori says can be “a royal pain out on the production floor—and most of them don’t work”;
While the major correction in PP prices was finally underway, generally stable pricing was anticipated for the other four commodity resins.
GETTING A QUOTE WITH LK-MOULD IS FREE AND SIMPLE.
FIND MORE OF OUR SERVICES:
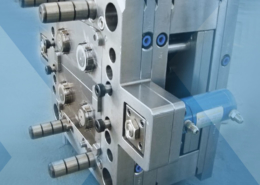
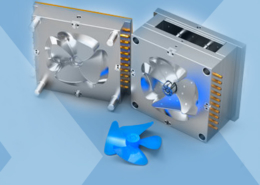
Plastic Molding

Rapid Prototyping
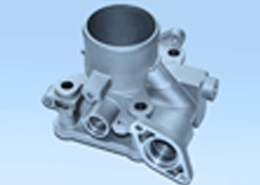
Pressure Die Casting
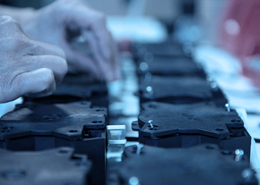
Parts Assembly
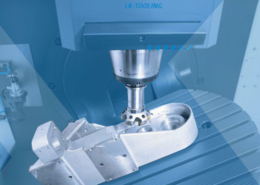