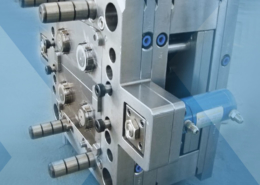
Sumitomo (SHI) Demag showcases LSR double-bill at Fakuma 2023 - demag injection
Author:gly Date: 2024-09-30
ALPLAinject stands for high-quality injection-moulded parts such as closures, caps, jars and multi-part packaging components such as pumps or deodorant sticks. With this new division, the international ALPLA Group is setting the course for further growth. The ALPLAinject brand brings together all human and technical resources in this area in one central organisational structure. It comprises a total of three core technologies – injection blow moulding and compression moulding in addition to injection moulding – as well as global toolmaking, development and sales.
ENGEL will present solutions including a mould that can process different labels at the same time at K 2022 in Dusseldorf, running from the 19th to the 26th of October.
The companies add that the transparent, round containers feature a wall thickness of 0.32 and a volume of 125 ml. The containers are reportedly ready-for-filling as soon as they leave the production cell thanks to integrated in-mould labelling (IML).
The global ALPLA Group is setting the course for further growth in injection moulding by establishing the ALPLAinject division. By strategically concentrating all injection moulding expertise and capacity under this brand, the plastic packaging specialist is increasing efficiency, speeding up the market launch of new products and unlocking new market segments.
PET offers the benefit of having a closed-loop recycling system already in place, the companies claim. They add that the innovation could remove the need to downcycle packaging into products other than bottles and provides an opportunity for bottle-to-bottle, bottle-to-cup, or even cup-to-bottle recycling.
ALPLAinject manufactures roughly 60 billion injection-moulded parts per year at 43 plants around the world. The division has more than 600 high-performance machines and systems. As a specialist in packaging solutions and recycling, ALPLA also relies on technological innovation. ALPLAinject scores highly with its decades of experience in lightweighting, alternative and recyclable materials; and energy-saving production facilities.
The companies say that up until now, it has only been possible to process PET in thick-walled parts such as bottle preforms in injection moulding. The final packaging format was apparently created in a second step of the process, for example, by blow moulding.
Standardised processes, centralised product and technology development; and shorter distances will ensure greater flexibility and efficiency in the future. "With ALPLAinject, we are focusing on the specific requirements of the dynamic injection moulding market. We combine technological expertise and regional market knowledge, promote the global roll-out of innovative processes and enable our customers to bring new products to market faster," emphasised the new ALPLAinject managing director Michael Feltes, who had already been business development director in the injection moulding section of the Group since October 2022. The global headquarters of ALPLAinject are located at the ALPLA headquarters in Hard. There are also global teams in all nine regions of the ALPLA Group.
According to the companies, an ENGEL e-speed injection moulding machine with a newly-developed and extremely powerful injection unit is being used to produce the thin-walled containers produced from recycled PET in a single step.
ENGEL, ALPLA Group, Brink and IPB Printing have collaborated to produce thin-walled containers made of PET and rPET in a single injection moulding process step.
To process rPET, ENGEL adds that it combines the new injection unit with a plasticising unit from in-house development and production specifically designed for processing recycled material. During the plasticising and injection, the viscosity of the PET is configured for thin-wall injection moulding.
ENGEL says that it specifically developed the e-speed 280/50 injection moulding machine with its electrical clamping unit and hydraulic injection unit for the high-performance requirements of thin-wall injection moulding. The new injection unit allegedly achieves injection speeds of up to 1400 mm per second at a maximum injection pressure of up to 2600 bar when processing small shot weights with an extreme wall-thickness to flow path ratio
"The injection moulding sector offers enormous potential and is one of our strategic growth drivers. The competitive market environment requires maximum cost effectiveness and flexibility. As its own injection moulding division, ALPLAinject will continue to ensure our competitiveness in the future," said ALPLA CEO Philipp Lehner with conviction. The new division reports directly to the CEO.
The dyes used on in-mould labels for the American market can apparently be washed off before recycling, while ENGEL says that for the European market, the in-mould label floats off in the recycling process to allow for the dyes and the label to be separated from the PET.
The modified rPET being processed at the K show comes from drinks bottles recycled in the plants of packaging and recycling specialists ALPLA Group, who are headquartered in Hard, Austria. The other collaborators involved with the project will also be at K 2022. This includes Brink (Harskamp, Netherlands) for the mould and IML automation and IPB Printing (Reusel, Netherlands) for the labels.
GETTING A QUOTE WITH LK-MOULD IS FREE AND SIMPLE.
FIND MORE OF OUR SERVICES:
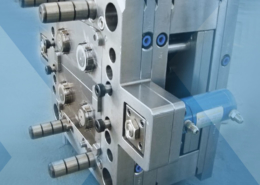
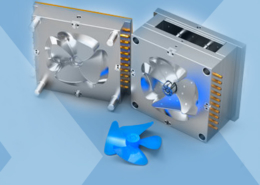
Plastic Molding

Rapid Prototyping
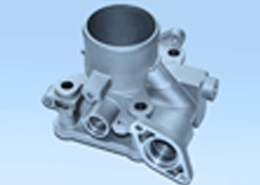
Pressure Die Casting
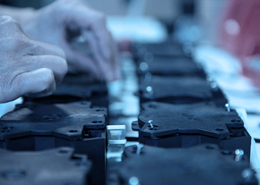
Parts Assembly
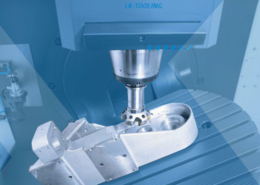