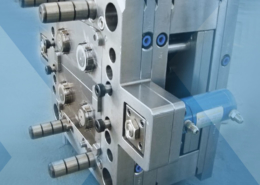
Sumitomo (SHI) Demag develops injection moulding system - demag injection
Author:gly Date: 2024-09-30
Transitioning from paint to masterbatch for metallic-effect parts is not new, but it is nowhere near as widespread as one would expect according to some auto industry observers. Inertia — We’ve always done it that way — and legacy investment in paint lines, supports the continued use of paint.
This white paper kicks off with a brief introduction defining the scope of the project and some of the attributes of the Form 2 SLA printer brought to the project, such as producing chemically bonded parts that are fully dense and isotropic.
Transitioning from paint to the use of MIC with Smartbatch FX helps manufacturers in the automotive, appliance, consumer goods and other industries create attractive, durable parts at reduced cost. PolyOne’s metallic-effect masterbatches can be incorporated into pre-colored compounds or dosed at a molding machine.
The molds in the aluminum frames that were used to injection-mold the plastic blue butterfly were 3D printed on a Form 2 desktop stereolithography (SLA) 3D printer. Image courtesy of Formlabs Inc.
The discussion covers the how, what and why of the test steps. Likely problems such as flash and too-visible part lines are addressed and corrections offered. The paper is frequently illustrated with photos, charts, tables and links to supplementary information like data sheets and third-party suppliers. At its end, the paper offers a set of design guidelines for early adopters.
“Many car parts are painted, not just metal and thermoplastic exterior parts, but also thermoplastic parts in a vehicle’s interior,” notes Gary Fielding, vice president and general manager, Color and Additives EMEA at PolyOne. “We have successfully helped carmakers transition from paint to MIC for many exterior applications such as skid plates and trims. This recent project is a significant step forward in reducing the cost to manufacture highly visible interior applications.”
“Injection Molding from 3D Printed Molds” is written with a moderate level of technical details, making it readily accessible to designers, moldmakers and engineering managers alike. It's a convincing and illuminating read. Hit today's Check it Out link to download your copy.
Want to learn the true meaning of the expression, “frustrating endeavor”? Price out the cost to mill metal molds for injection-molding low volumes of small parts in production plastic that makes budgetary sense. These costs often cause you to nix good ideas or opt for third or fourth best concepts. Today's Check it Out presentation describes a study of an affordable way to create molds for short runs that you can deploy in-house for a faster, more nimble design process.
PolyOne recently collaborated with a leading global automotive OEM and its injection molder to eliminate paint from a new vehicle’s interior. To support the transition to molded-in-color (MIC) parts, PolyOne provided metallic-effect Smartbatch FX masterbatch colorants for two PC/ABS side panels on the center console of a compact SUV now entering commercial production. The parts (two; one on each side of the center console) are C-shaped, 35-cm long, and at their widest point 11-cm wide.
And though the argument against masterbatch always is about these visual defects, little is said about scrap from paint lines, which can reportedly be more than 20%. Painting is not only more costly, and energy-intensive; it also generates very high levels of non-recyclable scrap.
Paint adds a great surface finish to automobile parts, but painting always adds cost, time, and additional logistics requirements according to PolyOne. By using Smartbatch FX metallic masterbatches, the molder was able to produce parts ready for assembly with no secondary processing required. Suitable for standard injection molding machinery, Smartbatch FX reduces the cost per part by 30 percent or more compared to painted parts. Lowered energy requirements versus painting and the reduction of VOCs also make this masterbatch a more environmentally sustainable solution.
“Injection Molding from 3D Printed Molds” reports on a study that teamed a Formlabs Form 2 desktop stereolithography (SLA) 3D printer with a Galomb benchtop Model-B100 Injection Molder. The object was to determine if you could create a synergy between the two systems and make molds for small, functional parts for final products. The molds needed to withstand the temperature and pressure of the plastic injection-molding process as well as last for 10 to 100 parts.
To provide customers with additional information on making the switch from paint to molded-in-color parts, PolyOne has created an eBook titled, “Trend Report: Efficient Manufacturing And Molded-In Color.”
The key to molding good parts is for OEMs to decide, very early on, that a part will be colored with molded-in color masterbatch; that decision will then support the development of a mold and part suitable for masterbatch.
The short of it is yes, it works. But what makes this paper intriguing is that you're walked through the project. The methodology, including post-processing 3D parts, is so well detailed that, later on, you should be able to follow the recipe to judge for yourself the potential of integrating this capability into your workflow.
Next come the granular details. Two mold designs were 3D printed in a clear resin. One mold had a single part; the other had four small parts. A third mold of a USB enclosure was made with a high-temperature resin.
The industry’s challenges, in light of COVID-19 and an uncertain economy, could open the door much wider to greater use of metallic-effect masterbatches, as these significantly lower cost per part. The challenge with masterbatch remains molding parts that do not have visual defects such as flow or weld lines.
PolyOne recently collaborated with a leading global automotive OEM and its injection molder to eliminate paint from a new vehicle’s interior.
Stephen has been with PlasticsToday and its preceding publications Modern Plastics and Injection Molding since 1992, throughout this time based in the Asia Pacific region, including stints in Japan, Australia, and his current location Singapore. His current beat focuses on automotive. Stephen is an avid folding bicycle rider, often taking his bike on overseas business trips, and is a proud dachshund owner.
“Typically, you do not want a bunch of holes or sharp curves in a part if you intend to use metallic-effect masterbatch. Too often, a mold is made for molding of parts that will be painted, and then — when it is time for a facelift — the OEM decides it wants to save some money and shift from paint to masterbatch. However, without investing in a new mold, the existing mold design often makes it very difficult for masterbatch to be successfully used.
GETTING A QUOTE WITH LK-MOULD IS FREE AND SIMPLE.
FIND MORE OF OUR SERVICES:
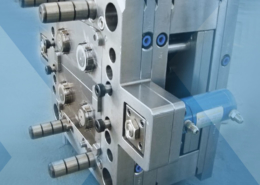
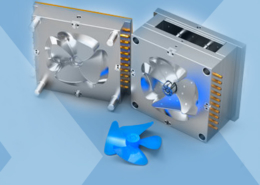
Plastic Molding

Rapid Prototyping
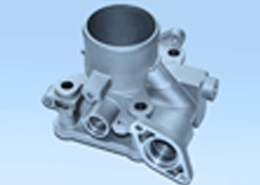
Pressure Die Casting
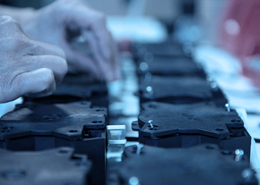
Parts Assembly
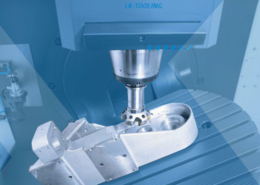