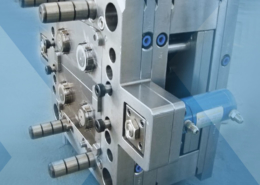
Structural Foam Injection Molding Line Extended - gas assist molding
Author:gly Date: 2024-09-30
For BASF, solving the punch challenge was one of the greatest engineering accomplishments. Due to its extensive application profile, BASF tests a wide range of materials from soft and tough to stiff and brittle polymers. There are also many different sample geometries, including thicknesses varying from 0.8 to 4 mm. All BASF test specimens are manufactured in accordance with the ISO 294 standard. This specifies the precision of the sprue system and specific requirements each sample geometry must fulfil. “Removal by punch is a pre-requisite, as it does not change the material properties and eliminates dust particles,” explains Hausmann.
Cost reduction actions include increasing efficiency in machine utilization, streamlining plant layouts and more closely monitoring factory expenses.
Sumitomo (SHI) Demag’s IntElect 1000 kN injection molding machine is at the core of a fully digitized manufacturing cell producing test specimens for product development and research involving thermoplastic polymers and compounds.
Due to the plan’s initial success in Europe, Carclo executives made the decision to restructure its U.S. operations the same way, Doorenbosch told analysts.
Pooling its engineering competences and technological resources, BASF’s Performance Materials division in collaboration with Sumitomo (SHI) Demag and H + S Automatisierung have created a manufacturing cell to produce a range of test specimens for the product development and research activities of thermoplastic polymers and compounds.
Integrating BASF’s existing mold insert concept and special features into the injection unit, the installation also includes a thermal temperature control unit and a new digital Manufacturing Execution System (MES) to map each test sequence. Reinhard Jakobi, Head of Performance Materials Processing at BASF, describes the project as an achievement of advanced engineering combining mature technology with state-of-the-art automation and molding precision.
For operative safety and efficiency, a linear SDR 5-35S robot serves two purposes. A new feature is full automation of the selection and placement of 12 interchangeable mold inserts from a magazine located within the cell. After the part is molded, the same robot fitted with a multifunctional gripper gently extracts the test specimen from the mold and passes it to the small six-axis, articulated-arm Yaskawa GP8 robot for precise cutting of the specimens from the gate using a servo spindle drive punching machine.
Part of the plan included shuttering Carclo’s injection molding facility in Derry, New Hampshire last year, Doorenbosch added. The company also plans to establish process and technical training centers in the EMEA, U.S. and Asia-Pacific regions “to drive continuous improvement through a very inclusive business approach.”
One of the most popular hot sauce makers in the U.S. has stopped its production again citing difficulty in sourcing and labor.
Then, the change of the mold inserts is synchronized to the cell control via output and input signals with transmission of the new mold data record via the robot interface. After the change of the mold insert, the temperature control units are heated up again. Automatic operation resumes and a new mold data record is initiated as soon as the target temperature is reached.
BASF’s MES informs the cell when the current produced sample setting is about to end, lining up the next mold application. Immediately after the injection process stops, cooling of the mold insert is directed by the integrated temperature control unit interface.
“The focus of the factories has shown that their operating equipment efficiency has gone up in both of the sites,” Doorenbosch said. “Because if you can do something very well, you will excel in it.”
Automation Systems Senior Engineer at Sumitomo (SHI) Demag, Markus Hausmann explains: “In order to lower the temperature to 80°C and depressurize the insert to guarantee that the SDR robot can remove the mold insert safely, our machine control has to talk and interact seamlessly with BASF’s MES.
Other COVID-19 test makers have also had to pivot as sales decline. Medical device conglomerate Danaher’s 4-in-1 test for COVID-19, flu A, flu B and RSV helped the company beat its COVID-19 test sales slump in Q2 last year.
At any time, up to 12 interchangeable inserts can be loaded to the side magazine and then swapped automatically into the injection molding machine. By integrating an HB-Therm temperature control system with Sumitomo (SHI) Demag’s machine control, automated mold insert changes can be completed safely and efficiently, even when running the process at high mold temperatures.
Carclo has been implementing changes in response to several operational challenges, including reduced customer demand, high inflation, rising energy costs and ongoing supply chain issues, Doorenbosch said.
Carclo began executing this plan by modifying its manufacturing operations in the Europe, Middle East and Africa regions, Doorenbosch told analysts. The company invested in two main operational platforms, one in the U.K. and the other in Brno, Czech Republic.
At the pilot center, the BASF research team typically configures 20 test settings daily on this machine. That means the control program of the cell has to be adapted to different materials, sample geometries, temperatures, and processing parameters. Every single setting that runs is recorded and documented digitally.
Creating tomorrow’s polymer innovations starts with understanding the chemical and mechanical performance and processing conditions of materials. At BASF’s Injection Molding & Extrusion Pilot Plant in Ludwigshafen, Germany, the newest all-electric, fully-automated injection molding cell from Sumitomo (SHI) Demag is delivering pioneering and repeatable results for more than 4,000 tests a year.
Many of the specimens processed at BASF’s technical centre are high-temperature thermoplastics, fiber reinforced and often flame retardant. Consequently, melt temperatures can reach up to 400°C with mold temperatures hitting 180°C.
Moving forward, Carclo will focus on other diagnostic test markets not related to COVID-19, CFO Eric Hutchinson told analysts.
The $35 million for sterile injectable medicines is a good start, but more reform for drug supply and pricing is needed, experts say.
The $35 million for sterile injectable medicines is a good start, but more reform for drug supply and pricing is needed, experts say.
Taking center stage in the cell is Sumitomo (SHI) Demag’s ultra-precise IntElect 1000 kN injection molding machine. Selected for its compact design, energy efficiency, and repeatability, the IntElect’s enhanced welfare and safety features were also welcomed by the team of 30 research operatives at the facility. Progressive solutions to automate mold changes and low noise emissions combined with fully-digitized robotic processing solutions also received high marks.
The multifunctional gripper ensures all sample geometries are placed with exacting precision onto the punch plate. This is complex in itself because BASF works with many materials that have high fiber glass content, which can cause warpage. Describing how the servo driven parallel punch gripper overcomes the challenge of placing parts securely onto the punch plate, Hausmann notes: “If the test specimens are not held sufficiently well in place, the punchings could be crooked or not conform to specified quality standards.”
One of the most popular hot sauce makers in the U.S. has stopped its production again citing difficulty in sourcing and labor.
Angelika Homes comments: “Unlike our former MES systems, this one logs every single aspect of a trial and the results, giving us insight for every single shot. This data is extremely valuable as it represents the entire processing sequence and enables us to draw deeper conclusions about how materials perform under certain conditions and how a customer might later process it.”
GETTING A QUOTE WITH LK-MOULD IS FREE AND SIMPLE.
FIND MORE OF OUR SERVICES:
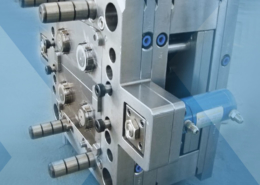
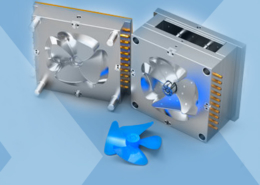
Plastic Molding

Rapid Prototyping
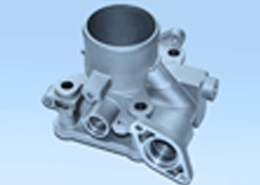
Pressure Die Casting
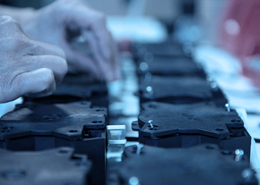
Parts Assembly
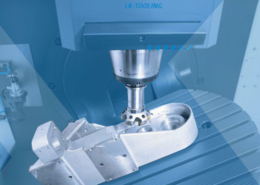