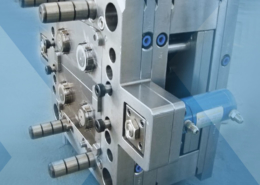
Stanley Black & Decker Backs Injection Molding/3D Printing Combination - prototy
Author:gly Date: 2024-09-30
Although the print bead is constant for each print, it could be 4-24 millimeters wide and 1-5 millimeters tall. That rough surface creates issues with achieving a good seal for the ROBIN mold and runout of the injection material during overmolding. “Thermoforming provides a smooth surface, and we also achieve a good connection between the overmolding and substrate materials,” says Stegelmann (Fig. 3).
“We developed this robotized injection molding machine in 2019 to produce hybrid components,” says Michael Stegelmann, managing partner at Anybrid (see “Robotic injection molding for functionalize composites”). “Hybrid components” refers to functionalizing a structure with an injection molded polymer to create local attachment points, stiffening ribs, etc. This overmolding process has gained traction in composites, but typically uses a traditional injection molding machine.
As global industries and markets demand increased sustainability, novel automated systems such as Anybrid’s (Dresden, Germany) robotized injection molding (ROBIN) offer a means to functionalize composite components, eliminating bonding and facilitating lightweight assemblies.
Processors with sustainability goals or mandates have a number of ways to reach their goals. Biopolymers are among them.
“Mobile injection molding allows us to apply recurring elements as needed with a high degree of flexibility to profiles or large-scale components,” says Stegelmann. He points out a shell demonstrator (Fig. 2), “where we show that with overmolded omega profiles, you can achieve a very quick, simple construction to achieve light-weight, high-strength assemblies.” REHAU and Anybrid plan to continue development, looking at processes beyond extrusion and joining technologies for composite parts.
Mike Sepe has authored more than 25 ANTEC papers and more than 250 articles illustrating the importance of this interdisciplanary approach. In this collection, we present some of his best work during the years he has been contributing for Plastics Technology Magazine.
In this three-part collection, veteran molder and moldmaker Jim Fattori brings to bear his 40+ years of on-the-job experience and provides molders his “from the trenches” perspective on on the why, where and how of venting injection molds. Take the trial-and-error out of the molding venting process.
For automotive applications, demonstrations used Lanxess Bond-Laminates (Brilon, Germany) Tepex 102-RG600 PA6 with 47% glass fiber roving for compression molding. Resulting composite profiles were then overmolded using Lanxess’ (Cologne, Germany) PA6 flame-retardant Durethan BKV60 and BKV30 with 60% and 30% chopped glass fiber, respectively. For this application, ROBIN was used to integrate threaded fasteners from Böllhoff (Bielefeld, Germany) into a narrow omega-shaped profile (Fig. 1).
Fig. 3. Overmolding and 3D printing. Anybrid demonstrated ROBIN’s ability to overmold GF/PP features onto a cellulose fiber/PLA panel made by a large-format 3D printer.
Exhibitors and presenters at the plastics show emphasized 3D printing as a complement and aid to more traditional production processes.
Anybrid and ILK performed demonstrations using the 8 × 2 × 2-meter-high “Supertooler” LFAM developed and built in-house at ILK onto an eight-axis Kuka Robotics (Augsburg, Germany) system. Materials included bio-based polylactic acid (PLA) reinforced with cellulose fibers supplied by UPM Biocomposites’ (Helsinki, Finland) UPM Formi (Lahti, Finland) division. The printed structure was then overmolded using polypropylene (PP) with 30% glass fiber supplied by Mitsui Chemicals (Tokyo, Japan). “The black PP compound allowed us to see the material flow onto the 3D-printed PLA substructure,” says Stegelmann. “We quickly preheated the 3D-printed surface using an infrared heater and then closed the ROBIN mold onto the panel, thermoforming the part surface. This thermoforming is needed due to the large bead size of the printed materials.”
After successfully introducing a combined conference for moldmakers and injection molders in 2022, Plastics Technology and MoldMaking Technology are once again joining forces for a tooling/molding two-for-one.
Mixed in among thought leaders from leading suppliers to injection molders and mold makers at the 2023 Molding and MoldMaking conferences will be molders and toolmakers themselves.
Formnext Chicago is an industrial additive manufacturing expo taking place April 8-10, 2025 at McCormick Place in Chicago, Illinois. Formnext Chicago is the second in a series of Formnext events in the U.S. being produced by Mesago Messe Frankfurt, AMT – The Association For Manufacturing Technology, and Gardner Business Media (our publisher).
This Knowledge Center provides an overview of the considerations needed to understand the purchase, operation, and maintenance of a process cooling system.
August 29-30 in Minneapolis all things injection molding and moldmaking will be happening at the Hyatt Regency — check out who’s speaking on what topics today.
Resin drying is a crucial, but often-misunderstood area. This collection includes details on why and what you need to dry, how to specify a dryer, and best practices.
Anybrid has miniaturized the process to fit within a robot arm end effector, enabling, for example, pultrusions to be overmolded inline or molded structures to be functionalized within a robotic cell. Anybrid has recently completed a series of demonstrations to highlight new capabilities its technology can offer including:
Branding these materials as Supercore, CQFD claims other advantages, including a modulus of 50-62 gigapascals — roughly 1.5 times more stiffness than conventional glass fiber composite profiles — and a density of 2.0 grams/cubic centimeter. CQFD profiles made using unidirectional (UD) glass fibers (GF) offer a higher specific rigidity versus profiles made using aluminum (2.7 grams/cubic centimeter). Also, because these profiles are thermoplastic composite, they can be thermoformed, reshaped and overmolded.
The Plastics Industry Association (PLASTICS) has released final figures for NPE2024: The Plastics Show (May 6-10; Orlando) that officially make it the largest ever NPE in several key metrics.
Across all process types, sustainability was a big theme at NPE2024. But there was plenty to see in automation and artificial intelligence as well.
Plastics Technology’s Tech Days is back! Every Tuesday in October, a series of five online presentations will be given by industry supplier around the following topics: Injection Molding — New Technologies, Efficiencies Film Extrusion — New Technologies, Efficiencies Upstream/Downstream Operations Injection Molding — Sustainability Extrusion — Compounding Coming out of NPE2024, PT identified a variety of topics, technologies and trends that are driving and shaping the evolution of plastic products manufacturing — from recycling/recyclability and energy optimization to AI-based process control and automation implementation. PT Tech Days is designed to provide a robust, curated, accessible platform through which plastics professionals can explore these trends, have direct access to subject-matter experts and develop strategies for applying solutions in their operations.
In a time where sustainability is no longer just a buzzword, the food and beverage packaging industry is required to be at the forefront of this innovation. By adopting circular packaging processes and solutions, producers can meet regulatory requirements while also satisfying consumer demand and enhancing brand reputation. Join Husky to learn more about the broader implications of the circular economy — as well as how leading brands are leveraging this opportunity to reduce costs, increase design flexibility and boost product differentiation. Agenda: The cost and operational benefits of embracing circularity Key materials in circular packaging — including rPET and emerging bioplastics How to design a circular food and beverage package Strategies for selecting sustainable closures to future-proof packaging solutions Optimization and streamlining of production processes for enhanced efficiency How Husky Technologies can enable your sustainable success
In this collection of articles, two of the industry’s foremost authorities on screw design — Jim Frankand and Mark Spalding — offer their sage advice on screw design...what works, what doesn’t, and what to look for when things start going wrong.
Join Engel in exploring the future of battery molding technology. Discover advancements in thermoplastic composites for battery housings, innovative automation solutions and the latest in large-tonnage equipment designed for e-mobility — all with a focus on cost-efficient solutions. Agenda: Learn about cutting-edge thermoplastic composites for durable, sustainable and cost-efficient battery housings Explore advanced automation concepts for efficient and scalable production See the latest large-tonnage equipment and technology innovations for e-mobility solutions
“Due to the innovative composition of CQFD’s composite materials and the right process parameters, it is now possible to obtain excellent adhesion with the overmolded PA6 inserts even when using a highly fiber-filled composite,” says Frank Chauzu, founder and CEO at CQFD. “Supercore profiles are also available with compatibility for other material combinations such as PP. To reach that compatibility, the profiles go through a specific treatment developed by CQFD that promotes adhesion between the PA6 and PP materials.”
While the melting process does not provide perfect mixing, this study shows that mixing is indeed initiated during melting.
In a separate trial, Anybrid was able to demonstrate the potential for ROBIN in combination with a new type of sustainable bio-based material. “We met Dongnam Realize [Daejeon, South Korea] when they won the JEC startup competition at last year’s composites show in Paris,” says Stegelmann. “Their CXP material uses a cellulose-based polymer made from waste wood products.” The Dongnam Realize website notes that cellulose cross-linked polymer (CXP) can be made from sawdust, wood chips, discarded vegetables and even invasive species like certain reeds and water hyacinth, for example.
"One person highlighted their thrifty approach to gardening, commenting: "I love finding ways to use whatever is available or free. I make a point to walk around the neighbourhood on garbage night to see what I can salvage.
Anybrid’s ROBIN demonstrates inline/offline functionalization of profiles, 3D-printed panels and bio-based materials for more efficient, sustainable composite parts.
Stegelmann notes the tests with CQFD produced a monomaterial system with excellent adhesion. Overmolding was also demonstrated using Mitsui Chemicals’ PP material. “I was surprised by the great adhesion quality of the first trials using PP,” says Stegelmann.
In 2021, Al-Sheyyab and his team began an extensive study with Anybrid on thermoplastic extrusions, composite profiles and molded parts. By late 2022, they had successfully overmolded profiles offline but also integrated a ROBIN unit into a production line at the REHAU technical center, where profiles were overmolded in-situ.
New robotic and digital technologies are enabling advanced in-house capabilities for small companies and innovative suppliers willing to embrace the move toward more affordable, sustainable composites.
While prices moved up for three of the five commodity resins, there was potential for a flat trajectory for the rest of the third quarter.
Despite price increase nominations going into second quarter, it appeared there was potential for generally flat pricing with the exception of a major downward correction for PP.
Thousands of people visit our Supplier Guide every day to source equipment and materials. Get in front of them with a free company profile.
While the major correction in PP prices was finally underway, generally stable pricing was anticipated for the other four commodity resins.
Fig. 1. Functionalized automotive profiles. Anybrid worked with REHAU Innovation Group to integrate threaded inserts into GF/PA6 profiles by overmolding with GF/PA6 compound, including functionalization such as anti-twist features (top). The small size of the mold enables ROBIN to reach in between the walls on the rear side of the omega profile (bottom).
Multiple speakers at Molding 2023 will address the ways simulation can impact material substitution decisions, process profitability and simplification of mold design.
The aim of this presentation is to guide you through the factors and the numbers that will help you determine if a robot is a smart investment for your application. Agenda: Why are you considering automation? What problems are you trying to solve? How and why automation can help Crunch the numbers and determine the ROI
The expertise of both teams was important in these developments. “The parameters from extrusion have to be brought together with those from injection molding,” says Sell. “It is important to match the speed of the production line to that of the part to be overmolded. For example, the cooling time of the overmolded element must be taken into account.”
This connection was investigated using computed tomography (CT). “We can clearly see diffusion between the two polymer systems, which creates a mechanical interlocking,” says Stegelmann. “There are still some challenges in optimizing the processing temperatures, but we see a real opportunity for in-situ functionalization of 3D-printed parts with local inserts, sealings, clips, etc. Our next step is to demonstrate this potential with a technical component from the marine industry. We can see a future where large-volume 3D printing facilities will be equipped with our mobile injection molding system as standard due to the possibilities it opens for their parts.”
A novice gardener shared several tips for fellow newbies which will help eradicate weeds from your garden, and the 'genius' hack will be a 'breeze' to use
In a second set of demonstrations, the teams used continuous glass fiber/PEI profiles produced by Xelis (Bermatingen, Germany) using its CCM process. Similar to omega-shaped stringers used in commercial aviation, Hitsert threaded inserts from Böllhoff were integrated via overmolding with glass fiber/PEI materials fom SABIC (Riyadh, Saudi Arabia). “These parts demonstrated our ability to overmold using high-temperature materials approved for aerospace,” notes Stegelmann.
Additive technology creates air pockets in film during orientation, cutting down on the amount of resin needed while boosting opacity, mechanical properties and recyclability.
Although Anybrid works with a wide range of standard materials, the innovative nature of the technology makes it attractive for companies developing new materials and processes. One such partner is CQFD Composites (Mulhouse, France), a supplier of structural thermoplastic composite profiles. Founded in 2006, CQFD Composites has developed a reactive thermoplastic pultrusion system. This technology uses in-situ polymerization of low-viscosity caprolactam monomer to produce, in this case, PA6 pultruded profiles with high glass fiber content, up to 85% by weight.
" Meanwhile, another individual recommended an indoor solution: "My tip is to use an indoor greenhouse plus a heat mat for starting seeds. It saves so much time."
Core Technology Molding turned to Mold-Masters E-Multi auxiliary injection unit to help it win a job and dramatically change its process.
“Dongnam sent us some of their pelletized materials and we did overmolding tests using ROBIN,” says Stegelmann. “The materials processed really well and create a whole new possibility of generating functionalized biocomposites for furniture or consumer goods that eliminate the need for petroleum-based plastics. We see a lot of potential for using ROBIN with these cellulose polymers in the future.”
Another shared their unique method of protecting young plants, stating: "My secret is that I use an old dog crate and some small animal cages that I have to protect my seedlings from squirrels until they get to be a good size. The squirrels could definitely still get into them if they really wanted to but we seem to have reached a truce this way.
Stegelmann and Chauzu also emphasize that it is possible to use the process heat during reactive pultrusion instead of preheating the profile for overmolding, as is typically necessary. This would enable even better process and energy efficiency, they explain. “For example, a PA composite might be heated to 180 to 200°C,” says Stegelmann, “instead of allowing the profile to cool, we can overmold as the pultrusion exits the system to achieve a good connection, saving time and process steps. Again, overmolding is not new, we are just enabling it to become directly part of the process line, but with increased flexibility and lower cost.”
Second quarter started with price hikes in PE and the four volume engineering resins, but relatively stable pricing was largely expected by the quarter’s end.
The opportunity for Anybrid’s ROBIN technology to produce a variety of more sustainable composite parts seems, if not limitless, then at least very broad. “The issue is convincing companies to move beyond the known and familiar,” says Stegelmann. “Overmolding has been well proven and is gaining use in composites. We are just making that process mobile and more flexible to provide really futuristic solutions that can generate value for manufacturers now.”
Discover how artifical intelligence is revolutionizing plastics processing. Hear from industry experts on the future impact of AI on your operations and envision a fully interconnected plant.
The post inspired other green-fingered enthusiasts to share their own tips. One user expressed gratitude, saying: "Excellent tips. Thank you. I'm forgetful and am constantly losing tools so I'm sure I'll be using your bucket idea.
Stegelmann explains the steps involved: “First, we position the metal insert inside the small injection mold within the ROBIN machine [Fig. 2]. Next, the ROBIN system is aligned with the profile, and then the mold is closed and the fastener is overmolded. Because the mold is very small, ROBIN is able to reach even between the high walls on the back side of this profile and overmold fasteners with anti-twist resistance or integrated sealing, for example.”
Dr. Ahmad Al-Sheyyab, manager of the Composites Technologies Department of REHAU Innovation Group, notes, “Our mission is to check every idea for relevance and make what sometimes seems impossible possible.”
Their post detailed: "I recently discovered that a claw hammer works great for removing creeping buttercup. I use the claw to grab onto the plant just below the crown and the handle gives me the leverage I need to pop them right out of the ground," they added. A claw hammer is available at B&Q for just £4.99.
Sustainability continues to dominate new additives technology, but upping performance is also evident. Most of the new additives have been targeted to commodity resins and particularly polyolefins.
Implementing a production monitoring system as the foundation of a ‘smart factory’ is about integrating people with new technology as much as it is about integrating machines and computers. Here are tips from a company that has gone through the process.
Mold maintenance is critical, and with this collection of content we’ve bundled some of the very best advice we’ve published on repairing, maintaining, evaluating and even hanging molds on injection molding machines.
To top off their advice, they offered a tip to help gardeners avoid back pain and extend their time tending to plants. By using an old shower bench, they can comfortably sit while working, reports the Mirror. They explained: It's super lightweight, so easy to move around, and has holes in it, so water doesn't accumulate on it from rain.
“We see great potential to use Anybrid’s mobile injection molding in a variety of continuous process lines,” says Sell, “such as thermoplastic extrusion, pultrusion or CCM, for the production of composites parts for transport or industrial applications, for example. It enables monomaterial systems — products that consist of the same polymer matrix. Steps such as gluing are eliminated. This makes production faster and the products easier to repair or recycle.”
When, how, what and why to automate — leading robotics suppliers and forward-thinking moldmakers will share their insights on automating manufacturing at collocated event.
Chauzu adds, “Due to the great flexibility of the Anybrid technology, the combination with our thermoplastic pultrusion leads to many interesting applications to develop together.”
In this collection of content, we provide expert advice on welding from some of the leading authorities in the field, with tips on such matters as controls, as well as insights on how to solve common problems in welding.
“The use of composite materials in structural applications creates specific challenges for joining,” explains Stegelmann. “ROBIN can be added to production lines to integrate inserts that enable attachments and facilitate assembly [Fig. 1]. Anybrid has demonstrated this in two projects with the Innovation Group of REHAU Industries [Rehau, Germany]. REHAU produces polymer-based solutions for construction, automotive and industrial applications including window profiles and components for car exteriors, bumpers and air duct systems. REHAU is also researching a variety of innovations using composites, including natural fiber and bio-based composites.”
In this collection, which is part one of a series representing some of John’s finest work, we present you with five articles that we think you will refer to time and again as you look to solve problems, cut cycle times and improve the quality of the parts you mold.
Ultradent's entry of its Umbrella cheek retractor took home the awards for Technical Sophistication and Achievement in Economics and Efficiency at PTXPO.
Join this webinar to explore the transformative benefits of retrofitting your existing injection molding machines (IMMs). Engel will guide you through upgrading your equipment to enhance monitoring, control and adaptability — all while integrating digital technologies. You'll learn about the latest trends in IMM retrofitting (including Euromap interfaces and plasticizing retrofits) and discover how to future-proof your machines for a competitive edge. With insights from industry experts, it'll walk you through the decision-making process, ensuring you make informed choices that drive your business forward. Agenda: Maximize the value of your current IMMs through strategic retrofitting Learn how to integrate digital technologies to enhance monitoring and control Explore the benefits of Euromap interfaces and plasticizing retrofits Understand how retrofitting can help meet new product demands and improve adaptability Discover how Engel can support your retrofitting needs, from free consultations to execution
He notes that ROBIN also saves costs. “Using the small injection molding robot makes it possible to dispense with large, expensive tools. The logistical effort is also reduced since profiles no longer have to be moved to injection molding machines. We have shown that costs can be reduced and productivity and flexibility increased in our extrusion lines.”
technotrans says climate protection, energy efficiency and customization will be key discussion topics at PTXPO as it displays its protemp flow 6 ultrasonic eco and the teco cs 90t 9.1 TCUs.
Anybrid overmolded panels made of the natural composite wood (cellulose fibers in lignin matrix) with cellulose cross-linked polymer (CXP) from JEC award winner Dongnam Realize.
Join Wittmann for an engaging webinar on the transformative impact of manufacturing execution systems (MES) in the plastic injection molding industry. Discover how MES enhances production efficiency, quality control and real-time monitoring while also reducing downtime. It will explore the integration of MES with existing systems, emphasizing compliance and traceability for automotive and medical sectors. Learn about the latest advancements in IoT and AI technologies and how they drive innovation and continuous improvement in MES. Agenda: Overview of MES benefits What is MES? Definition, role and brief history Historical perspective and evolution Longevity and analytics Connectivity: importance, standards and integration Advantages of MES: efficiency, real-time data, traceability and cost savings Emerging technologies: IoT and AI in MES
Say “manufacturing automation” and thoughts immediately go to the shop floor and specialized production equipment, robotics and material handling systems. But there is another realm of possible automation — the front office.
This month’s resin pricing report includes PT’s quarterly check-in on select engineering resins, including nylon 6 and 66.
Take a deep dive into all of the various aspects of part quoting to ensure you’ve got all the bases—as in costs—covered before preparing your customer’s quote for services.
Learn about sustainable scrap reprocessing—this resource offers a deep dive into everything from granulator types and options, to service tips, videos and technical articles.
Successfully starting or restarting an injection molding machine is less about ticking boxes on a rote checklist and more about individually assessing each processing scenario and its unique variables.
Gifted with extraordinary technical know how and an authoritative yet plain English writing style, in this collection of articles Fattori offers his insights on a variety of molding-related topics that are bound to make your days on the production floor go a little bit better.
While prices moved up for three of the five commodity resins, there was potential for a flat trajectory for the rest of the third quarter.
To demonstrate the ability to functionalize 3D-printed parts, Anybrid worked with the Institute of Lightweight Engineering and Polymer Technology (ILK) at Technische Universität Dresden in Germany. “The use of large-scale/large-format additive manufacturing [LSAM/LFAM] is growing,” notes Stegelmann. “The technology has been proven to be quite capable and cost-effective, but the problem with these big machines is they can print with high deposition rates but not with high resolution, and thus, fine details are impossible. This is where we can help, because ROBIN can overmold detailed functional elements during the print process.”
Plastics Technology covers technical and business Information for Plastics Processors in Injection Molding, Extrusion, Blow Molding, Plastic Additives, Compounding, Plastic Materials, and Resin Pricing. About Us
The green-fingered Redditor didn't stop there; they've also repurposed a plastic bucket as a portable tool carrier that keeps their equipment dry. They shared: "I use a Dollar Store bucket, with holes in the bottom - I put the holes there with a soldering iron - to carry my tools around the garden. And if I happen to forget it outside, at least my tools aren't resting in water when I go out to get them."
Across the show, sustainability ruled in new materials technology, from polyolefins and engineering resins to biobased materials.
CFRP pultrusion and pullwinding specialist Epsilon Composite combines thermoplastic overmolding with traditional thermoset processes, demonstrated through aircraft struts and industrial applications.
As explained on the REHAU Germany website, when Dr. Stephan Sell, research chemist in Al-Sheyyab’s team, first saw Anybrid’s ROBIN technology at the K trade fair in 2019, he could see many opportunities for it at REHAU. “They have succeeded in transforming the otherwise stationary injection molding machine into a mobile machine that can be moved freely in space,” says Sell. “This means that functional elements such as seals, metallic inserts, connecting elements or ribs can be retrofitted to existing molded parts, profiles, semi-finished products and metal hybrid composites.”
A budding gardener on Reddit has become the talk of the town with their ingenious 'garden hacks' for novices, promising a weed-free garden without breaking the bank. Sharing their advice on the vegetable gardening subreddit, the user's cost-effective methods have transformed their green space into an enviable oasis.
Fig. 2. Inserts aid assembly. A metal insert can be placed inside the mold (red circle, top) and then ROBIN is positioned over the profile, the mold is closed and the insert overmolded. Such functionalized profiles enable quick assemblies, such as this shell demonstrator using ULTEM PEI composite profiles with integrated aviation-certified Böllhoff inserts.
Join KraussMaffei for an insightful webinar designed for industry professionals, engineers and anyone interested in the manufacturing processes of PVC pipes. This session will provide a comprehensive understanding of the technology behind the production of high-quality PVC pipes: from raw material preparation to final product testing. Agenda: Introduction to PVC extrusion: overview of the basic principles of PVC pipe extrusion — including the process of melting and shaping PVC resin into pipe forms Equipment and machinery: detailed explanation of the key equipment involved — such as extruders, dies and cooling systems — and their roles in the extrusion process Process parameters: insight into the critical process parameters like temperature, pressure and cooling rates that influence the quality and consistency of the final PVC pipes Energy efficiency: examination of ways to save material and energy use when extruding PVC pipe products
Fig. 4. Hybridizing reactive thermoplastic composite pultrusion. Anybrid demonstrated ROBIN’s ability to overmold onto high-fiber-content (up to 85% by weight) GF/PA6 panels (bottom) made by CQFD using its reactive thermoplastic pultrusion process (top). Photo Credit (top): CQFD
Computed tomography (CT) scan of overmolding on 3D-printed panels showing diffusion and interlocking of polymer systems.
Introduced by Zeiger and Spark Industries at the PTXPO, the nozzle is designed for maximum heat transfer and uniformity with a continuous taper for self cleaning.
Functionalized PEI profiles made using CCM. Anybrid worked with REHAU Innovation Group to demonstrate use of its ROBIN robotized injection molding system to overmold Böllhoff Hitsert metal inserts into Xelis glass fiber/PEI omega profiles made using its CCM process, aimed toward possible aerospace applications. Photo Credit for all images: Anybrid
“We wanted to demonstrate a process chain where CQFD’s reactive pultrusion process could be combined with our robotized injection molding inline,” says Stegelmann. The first demonstration used CQFD’s in-house GF/PA6 profiles and a black-tinted PA compound with 30% glass fiber supplied by Lanxess for overmolding. The overmolded feature (Fig. 4) is a shape Anybrid created to demonstrate the complexity that is possible with ROBIN. It also provides a good basis to test for adhesion between the overmolding and the substrate.
GETTING A QUOTE WITH LK-MOULD IS FREE AND SIMPLE.
FIND MORE OF OUR SERVICES:
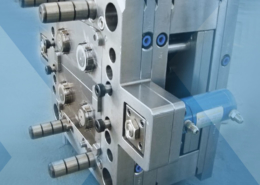
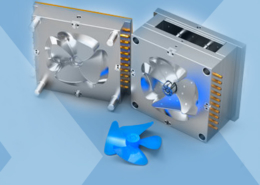
Plastic Molding

Rapid Prototyping
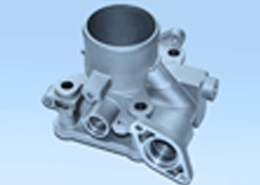
Pressure Die Casting
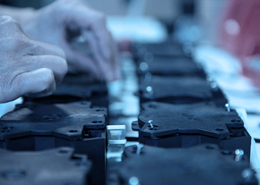
Parts Assembly
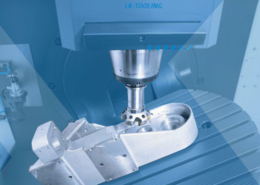