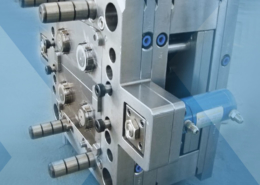
The Marvel of Plastic Injection Parts
Author:gly Date: 2024-06-08
In today's world, where innovation and efficiency are paramount, the realm of manufacturing has seen remarkable advancements. Among these, plastic injection parts stand out as a cornerstone technology, revolutionizing industries with their versatility, durability, and cost-effectiveness. In this article, we delve into the intricacies of plastic injection parts, exploring their significance, applications, and future prospects.
The Essence of Plastic Injection Parts
Plastic injection parts, often referred to as molded plastics, are components manufactured through the process of injecting molten plastic material into a mold cavity. This process allows for the creation of complex shapes with high precision and repeatability, making it a preferred choice across various industries. The versatility of plastic injection parts is unparalleled, ranging from intricate electronic components to sturdy automotive parts.
The Manufacturing Process
The journey of a plastic injection part begins with the design phase, where engineers meticulously craft the mold to exact specifications. Once the mold is ready, plastic pellets are heated to their melting point and injected into the mold cavity under high pressure. After cooling and solidification, the mold opens, revealing the finished part ready for use.
Materials Selection
The selection of materials plays a crucial role in determining the performance and characteristics of the final product. From commodity plastics like polyethylene to engineering-grade polymers such as ABS and polycarbonate, the choice depends on factors like strength, flexibility, and resistance to environmental factors.
Quality Control Measures
Ensuring the quality and consistency of plastic injection parts requires stringent quality control measures throughout the manufacturing process. Advanced technologies such as automated inspection systems and statistical process control enable manufacturers to detect defects early and maintain high standards of precision and reliability.
Applications Across Industries
Plastic injection parts have permeated almost every industry imaginable, owing to their versatility and adaptability to diverse requirements. From consumer electronics to medical devices, automotive components to household appliances, the applications are limitless.
Automotive Industry
In the automotive sector, plastic injection parts are instrumental in reducing vehicle weight, enhancing fuel efficiency, and improving safety. From interior components like dashboard panels to exterior parts like bumpers, the use of plastic injection parts has become ubiquitous, offering manufacturers the flexibility to innovate while meeting stringent regulatory standards.
Consumer Electronics
In the realm of consumer electronics, the demand for sleek, lightweight devices has propelled the use of plastic injection parts. From smartphone casings to intricate components within electronic devices, the precision and scalability of injection molding enable manufacturers to meet consumer demands for both form and function.
Medical Devices
The medical industry relies heavily on plastic injection parts for the production of various devices and equipment. From syringes to surgical instruments, the biocompatibility, sterilizability, and precision of molded plastics are paramount in ensuring patient safety and efficacy in healthcare settings.
Challenges and Innovations
While plastic injection parts offer numerous advantages, they are not without challenges. Addressing these challenges requires continuous innovation and adaptation to emerging technologies.
Environmental Sustainability
The environmental impact of plastic injection parts, particularly in terms of waste generation and recycling, is a growing concern. Manufacturers are increasingly exploring sustainable materials and processes to minimize ecological footprint while maintaining product performance and cost-efficiency.
Advanced Materials and Additive Manufacturing
The advent of advanced materials and additive manufacturing techniques is revolutionizing the landscape of plastic injection parts. From biodegradable polymers to nanocomposites with enhanced properties, the quest for novel materials is driving innovation and opening new avenues for applications across industries.
Digitalization and Industry 4.0
Digitalization and the integration of Industry 4.0 technologies are reshaping the manufacturing landscape, including plastic injection parts production. From digital twin simulations to real-time monitoring and predictive maintenance, embracing digital technologies enhances efficiency, reduces downtime, and optimizes resource utilization in injection molding operations.
Conclusion
In conclusion, plastic injection parts epitomize the marriage of precision engineering and material science, offering unparalleled versatility and efficiency across industries. As we navigate towards a future marked by sustainability and innovation, the role of plastic injection parts will continue to evolve, driving progress and shaping the fabric of modern manufacturing. Embracing emerging technologies and sustainable practices will be key in unlocking the full potential of plastic injection parts and ushering in a new era of industrial excellence.
GETTING A QUOTE WITH LK-MOULD IS FREE AND SIMPLE.
FIND MORE OF OUR SERVICES:
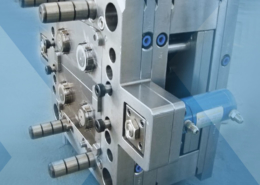
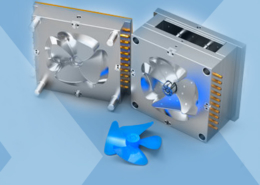
Plastic Molding

Rapid Prototyping
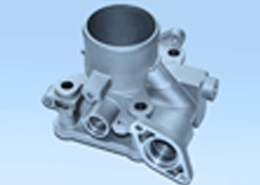
Pressure Die Casting
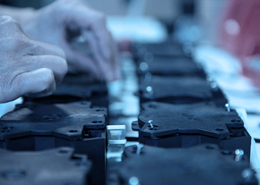
Parts Assembly
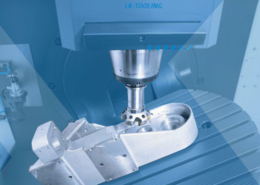