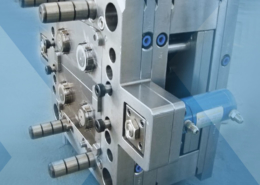
StackTeck announced unconventional application for big stack mold - mold and pla
Author:gly Date: 2024-09-30
TOP 700 provides the same high precision dosing of silicones and additives as Elmet’s flagship TOP 7000 Pro dosing system with its 200 or 20 litre drum size which was launched back in 2021.
"We're in the automotive market but not like most people think," said Denton, in describing some of the applications where Grafilm is in use. "It's interesting because there are many areas within vehicles such as the cabin, under-the-hood components, and exterior requirements, each [of which] has its own market for decoration and labels. At Standard Register, we play in the under-the-hood arena with warning labels on radiator housings, batteries, and other components."
Many labels on durable parts are "functional" labels that contain warnings, instructions, and markings for measurements, etc., Denton explained. "One application was a control panel for a simple lawn and garden part-a knob with marks on the label that had to line up correctly," he said. "If the molded part and the label aren't correctly dimensioned, it won't provide the consumer with a correct setting. Dimensions are very critical with durable products."
In-mold labeling (IML) for durable goods, also known as IMD (in-mold durables), is seeing more application requirements in the durables markets such as automotive, appliances, and toys. Jeff Denton, Marketing and Product Manager for Standard Register (Pasadena, CA), gave a presentation on IML at the recent IMLCON/IMDCON, and noted that in-mold isn't just for polypropylene any longer, referring to IML's popularity in the packaging market.
In-mold labeling for durable products requires a whole different mind-set, noted Denton. "IML for single-use items or for food products need beautiful labels to attract consumers at the shelf level," said Denton. "We have the same requirements for durable goods logos because the logo is their reputation. We have to hit their colors right on and ensure that after postmolding their colors are spot on. If the color isn't exact after postmolding, the entire part is scraped."
Another under-the-hood application, beyond warning labels, is the engine shroud that covers and hides the engine. Denton noted that his Ford Edge has a huge Ford emblem on top of the shroud, adding that many of these large logo labels are PS-applied secondary to production.
"The parts tend to have thicker wall sections, so typically we see more molding issues with labels shifting in the mold due to the injection pressures being greater," said Denton. "We have special coatings and inks that allow the labels to adhere to the mold surface with heat, static, or vacuum and don't see that shifting in the mold. One customer was using 30-60% GF nylon and the part we saw, the label stuck fine. It was almost a PP to PP bond, and with our Grafilm the mold and the label passed inspection. Typically 30% GF is what we see the most. Typically the mold for GF nylon will be a hot surface, 130°F or warmer, then the label will adhere with heat. During the cooling cycle, the label is pulled off the mold wall and bonded to the plastic. With more plastic coming across the label during the injection phase, pinning the label is critical."
Inks for in-mold labels for durable products need to be non-fade because the injection cycles are longer, which tends to break down the inks and can cause a loss in color quality. "We have to use the highest quality inks with heat resistance to prevent fading," said Denton. "Most have UV resistance coatings, as well, because a lot of the products are used outdoors."
Until she retired in September 2021, Clare Goldsberry reported on the plastics industry for more than 30 years. In addition to the 10,000+ articles she has written, by her own estimation, she is the author of several books, including The Business of Injection Molding: How to succeed as a custom molder and Purchasing Injection Molds: A buyers guide. Goldsberry is a member of the Plastics Pioneers Association. She reflected on her long career in "Time to Say Good-Bye."
The company's Grafilm is a high-molecular-weight, heat-resistant material that can withstand temperatures up to 600°F. "OEMs that don't use Grafilm have to look at the plastic being molded, such as PC or nylon, then rely heavily on inks and coatings to provide the chemical and abrasion resistance," explained Denton.
Due to the optimised design of the follower plates, just 40 ml of residues are left behind when the 20 litre drums have to be changed, resulting in material utilisation of up to 99.8%. With a design service life of 20 years or more for all its mechanical components, a modular structure and particular ease of servicing which keeps maintenance costs low, the TOP 700 is synonymous with cost-efficiency. Its low energy consumption of less than 50 Wh and minimal compressed air consumption also help to keep costs down.
In-mold labeling for durable products is still new but growing, noted Denton. "It's smaller than the typical IML market, but it's growing at a double digit rate for us, as more people convert from postmold decorating to IMD in the durables market," Denton commented. "It's a slow education process because molders aren't used to it and generally don't have the automation in house to do it. Plus, volumes usually dictate what projects a molder wants to take on and they have a hard time justifying an automation system for one project or a short run. The hurdle is getting them to the point of trying it."
In-mold labeling (IML) for durable goods, also known as IMD (in-mold durables), is seeing more application requirements in the durables markets such as automotive, appliances, and toys. Jeff Denton, Marketing and Product Manager for Standard Register (Pasadena, CA), gave a presentation on IML at the recent IMLCON/IMDCON, and noted that in-mold isn't just for polypropylene any longer, referring to IML's popularity in the packaging market.
Denton noted that there are a number of smaller labels required throughout the inside of the engine compartment, which typically is a dirty, hot environment exposed to harsh salt and cleaning solvents. "We're seeing a lot of those being converted to IML," he said.
Typically, when using IML technology, it requires like material to like material. However, Grafilm is an exception. "We have applications outside of automotive such as lawn and garden, power equipment, and handheld power tools that are molded using glass-filled nylon or PC blends such as PC-ABS, which are more difficult," said Denton. "ABS labels are available but they are expensive, primarily because in the durables arena you don't see the volumes you see with consumer packaging."
Designed to be FDA- and EMA-compliant, the new TOP 700 dosing system is used for applications requiring the highest levels of cleanliness such as medical technology, personal care, foodstuffs and optics. Virtually abrasion-free pumping also prevents metal particle contamination of the LSR which would impair its functionality. There are also no limits to the consistency of the processed LSR under real-world conditions because Elmet’s new system can dose any commercially available product with the same precision thanks to its ability to handle viscosities of between 0.001 Pas and 2000 Pas (shear rate 10/s) or 16,000 Pas (1/s). Its optionally OPC UA- and Euromap 82.3-compliant control system can be seamlessly integrated into the injection moulding machine’s own control system.
There are other areas where durable labels are required, such as air-bag warning labels on the side panel of the dashboard and tire pressure labels inside the door, and many others are being looked at for IML. "It's much easier to have it applied in-mold onto the plastic than to apply the PS label afterward," said Denton. "The in-mold label is long lasting, which is critical to durable products. With PS labels, putting a laminate over the label offers some protection, but that peels off, as well."
Thorsten Häuser, development manager, explains: “We developed our TOP 700 dosing pump to meet customer demand for a space- and material-saving solution from ELMET. We’ve achieved this with a footprint of less than 0.5 m² (799 mm × 600 mm) and our new pump design. As a result, this new dosing system is particularly suitable not only for customers processing high-value, shear-sensitive or abrasive materials but also for R&D, prototyping and small-batch applications. The TOP 700 rounds out our product range while setting new standards in compact dosing technology.”
One of Standard Register's businesses is developing IML for durable goods to extend the use of these labels beyond just pressure-sensitive (PS) applications for injection molded, blow molded, compression molded, and thermoformed parts. Its Grafilm product used in industrial and durable goods applications is a patented, UL-certified in-mold label file that mechanically bonds to any surface. The newest iteration of Grafilm offers increased abrasion and chemical resistance and optional UV protection and shaping capabilities.
To avoid operating errors, the drums can be changed fully automatically from the drum rim from three sides within two minutes. Intuitive operation of the system, the use of simple clamp connections, a guided drum change procedure and an integrated cooling system mean even relatively low-skilled personnel can operate it without any problem. Fully automatic venting as standard completes the system’s many and varied safety and convenience features.
As in-mold for durable products catches on, however, Denton noted that molders will start looking for new applications. "Once the molder or brand owner begin doing in-mold for their durable products, they love it and they start looking for new applications as a value- add," he said. "About 30 to 40% of the molders we work with are looking for new opportunities in IML/IMD. It increases the value of the part as well as the value of the molding services."
The TOP 700 can achieve delivery rates of over five litres/minute at a maximum pump pressure of 210 bar, so enabling short cycle times both when filling larger parts and with large numbers of small cavities. Additives and colours can be dispensed from 1, 4 and 20 litre containers. In order to achieve the dosing precision that is particularly vital for very small parts, the volumetric meter for colours has a resolution of below 0.1 μl/l. Depending on requirements, dosing can be carried out simultaneously or in a freely selectable mixing ratio.
With all that said, getting approval for in-mold labels is a "slow, tedious process with a lot of testing requirements," commented Denton. "Every automotive company has its own testing criteria, so you have to pass each company's testing requirements. Some of these requirements include special inks, special materials, high-heat resistance, durable coatings, and more," he explained.
GETTING A QUOTE WITH LK-MOULD IS FREE AND SIMPLE.
FIND MORE OF OUR SERVICES:
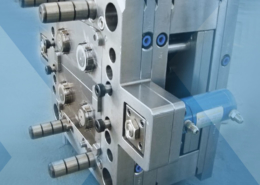
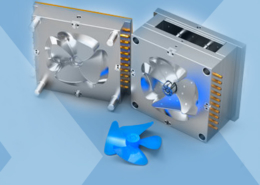
Plastic Molding

Rapid Prototyping
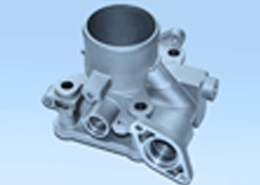
Pressure Die Casting
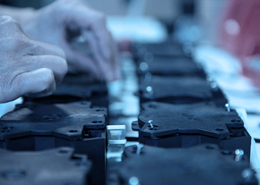
Parts Assembly
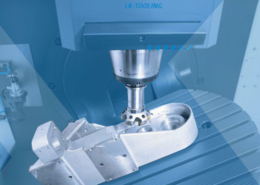