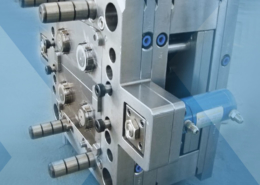
SPE Automotive Division names finalists for 52nd Automotive Innovation
Author:gly Date: 2024-09-30
For us, it is very important to continuously enhance our processing, moulding, and welding technologies in order to offer a combined solution. This gives us an edge compared to some companies that focus only on a single process such as machining or welding.
We are moving to manufacture a portion of our products in Thailand with lower labour costs while maintaining quality using Japanese technology. It may be difficult for us to compete with manufacturers in China and Taiwan if the market priority is cost rather than quality. Of course, it is necessary for us to continually cut costs to survive in the global market. However, I think we should focus on cost-effective performance while maintaining Japanese quality rather than winning in cost-based competition.
Let us focus on your FRP. We know that GFRP is used mainly in clutches for the automotive field as well as an insulator material. With government regulations the materials used in cars have become lighter. The push towards hybrid and EV vehicles has had the manufacturers change the way they design the car. What is your analysis of these changes in the automotive sector? How does your GFRP assist the car manufacturers?
We are mainly focusing on the semiconductor industry with our fluoropolymer products. Although there are already big players in the market as you have mentioned, our precise processing technology is our strength. Our fluoropolymer manufacturing technology is in a constant process of innovation, and we have revolutionized our moulding and processing technologies. We have been challenging ourselves to engage in advanced automation to achieve both high quality and high productivity by combining our partners’ machines with our original mechatronics technologies. In other words, we have managed to automate many of our original and high precision techniques that depend on craftsmanship. I think our company is one of very few examples of this kind of technology. That is our company’s strength.
You have deep expertise in two main fields: you have your Functional Polymer Business where you make PTFE (Polytetrafluoroethylene) products and your FRP. What synergies have been able to create between these two distinct yet similar lines of business?
For example, with our clutch facing which is a friction material we have to manage both low and high levels of friction. We sometimes add PTFE powder to adjust the frictional coefficient of the material. In 2010 we established a factory in Thailand to manufacture friction materials for clutch facings, and last year we began investing in manufacturing fluoropolymer products for the auto industry in Thailand. We not only cater to the semiconductor industry, but also to the auto industry with products such as seal materials. When we design our PTFE products as seal materials to be used in a harsh environment, we sometimes have to modify the sliding properties of the PTFE by incorporating glass fibre or carbon fibre. These are some cases of synergy that we have been able to create.
I think our company has experienced five important milestones. First was the business transformation from commercial to manufacturer; second is the transformation of materials from natural to synthetic; third is developing our business field from parts to machines; fourth is the enhancement of our processing technology to meet the high-level needs of the semiconductor industry through the establishment of our Shiga factory; and fifth is the expansion of our business to the global market through the establishment of our factory in Thailand.
The IML print-to-cut distance is only around 0.08 in. (0.2 mm) for the centrifuge tube application. With a wall thickness of only 57 micrometers, the labels must be precisely positioned in the mold cavities, and equally precisely aligned and applied. A label adjustment head equalizes the manufacturing tolerance to a few hundredths, which is an important requirement for functionality and significantly reduces quality fluctuations and rejects.
A temperature-sensitive element can be included that monitors interruptions in the cold chain. If the temperature of the filled tube exceeds 7°C, for example, the thermo-chromic printing ink irreversibly changes in appearance.
IML is standard for packaging products, but the process is rarely used in medical manufacturing, said Arburg in its announcment. The concept is all the more compelling because both the tube and label are made of polypropylene, thus promoting sustainability and adding value for customers in the pharmaceutical and medical sectors.
A medical in-mold labeling (IML) application will be showcased by Arburg at NPE2024. First presented at Fakuma in 2023 as a proof of concept, the compact turnkey production cell anchored by Arburg’s electric Allrounder 520 A "Ultimate" press will produce a centrifuge tube with label on the NPE show floor.
NiKKi Fron is a leading manufacturer of fiber-reinforced polymer (FRP) and fluoropolymer products used in several industries, including pharmaceuticals, semiconductors and automotive. Today, with the push towards manufacturing lighter vehicles, there are opportunities for NiKKi Fron to capitalize on through the provision of its FRP technology. We speak with president Takayuki Kasuga to learn more about how the company is developing its technology to meet the latest demands of the semiconductor and automotive industry.
I think the origin of Japanese monozukuri is craftsmanship that has been accumulated throughout history. Many craftsmen continuously improved their skills in much the same way our engineers have continuously made utmost efforts to analyse, standardize, and automate the manufacturing processes. As a result, the idea of monozukuri has spread to developing countries. Additionally, many industrial machines have been distributed to these regions - machines for pressing, machining, injection moulding, and other operations to produce high-performance products. These machines were developed in Japan but manufactured not only in Japan, hence, although many overseas manufacturers have been able to approach the performance of Japanese products, I think it would be difficult for them to copy the quality of Japanese monozukuri.
One of the big steps your company has taken was your international expansion. You have a trading business in Vietnam, and you have your plant in Thailand. Can you tell us more about your international expansion? What are some of the key markets that you are looking to target?
Yet, Japanese semiconductor production equipment makers have a big presence with very strong competitiveness when you look at the production site, and the manufacturers who supply key components to those makers are mostly Japanese, which includes SMEs like us. I would say that the strong supply chain with Japanese manufacturers' deep cooperation contributes to this competitiveness.
Though Japan is not the biggest in the semiconductor industry today, when we talk about materials consumed in the semiconductor field Japan has 40% global market share. How do you explain that even though Japan is not at the top, all the fields and sub sectors around it have remained world leaders in this tough market?
In the semiconductor field you make PTFE containers mainly for silicon wafers as well as certain wafer carriers. Currently the semiconductor market is having interesting changes, if we talk about silicon semiconductors, we see that the size is increasing. On the other hand, we are seeing the rise of compound semiconductors and compound substrates such as silicon carbide or nitride which are much more fragile and require a different type of handling. With these changes in the semiconductor field how is your company responding to it?
Moldmaker Kebo, in-mold labeling specialist MCC Verstraete, automation developer Beck, and vision system supplier Intravis contributed to the joint IML project.
In the last 25 years Japanese manufacturers have been put under pressure by regional competitors in China, South Korea, and Taiwan that have replicated the Japanese monozukuri processes, but done so at a cheaper labor cost, providing the world with cheaper yet lower quality products. Nevertheless, Japanese companies remain leaders in certain niche fields such as the semiconductor industry or in FRP production in the aerospace industry. What do you think are the reasons why Japanese companies remain competitive despite the price competition?
PTFE (polytetrafluoroethylene) was invented in 1930 and over the years its usage has increased. Originally it was used as an insulation material, then it became famous for cooking wares. Today 50% of its usage is for insulation of wiring in airplanes as well as for computer applications due to its excellent properties. It is an old market with so many applications developed and with big players already in it. What makes your products stand out and how do you compete with these big companies?
When it comes to areas overseas such as East Asia and North America where our products are integrated into the customer’s machines, for example semiconductor production equipment, we have to catch up with the customers’ needs on a global scale. We also have the potential to service new customers in the semiconductor industry around the world and we are currently pursuing these goals. As for clutch facings, the only way to continue our business was to expand into foreign markets. We have developed our clutch facings market all over south and southeast Asia since we established a factory in Thailand. Recently our original brand’s biggest after-sales market has been Pakistan. It seems the demand for clutch facings for manual transmission automobiles will decrease not only in advanced countries but also in developing countries such as India and Pakistan in line with the global objective to be carbon neutral. As I have explained already, hybrid AMT systems are expected to be widely adopted in developing countries such as India as a response to the move towards carbon neutral energy. In terms of our overseas mid-term strategy, we still have potential to grow our sales of clutch facings.
In five years, I hope to start a new business and achieve sales of ¥ 500 million in order to contribute to a carbon neutral society by means of consolidating our resources. This is inspired by our long-standing corporate policy to “utilize limited resources effectively.” This maxim was instilled by my grandfather, the founder of this company, and is the guiding principle which we strive to realize.
In the future, it is also conceivable that process, quality, and patient data for each individual part will be 100% traceable via an RFID code.
We have an integrated manufacturing process of fluoropolymer in Japan, and we are trying to construct the same type of integrated manufacturing system in our Thai factory. We mainly produce three categories of fluoropolymer products: moulded products, machined products, and PTFE diaphragms. We have already started manufacturing moulded products and machined products in our Thai factory. Our PTFE diaphragms have unique performance; as you know, PTFE has strong heat and chemical resistance, but if we apply a specially designed heat treatment to moulded PTFE products as per our unique process, it also has superb flexibility suitable for diaphragms. We are currently constructing an integrated diaphragm process due to a huge demand in the medical industry. Because of the covid-19 pandemic, the demand for vaccine manufacturing has increased greatly, and therefore we have to strengthen our production capacity, as diaphragms are one of the key components of the production line.
You have improved the production capacity of your factory in Thailand. Can you give us an update on this? What are the advantages brought by this?
When it comes to defining the Japanese concept of monozukuri, I would like to emphasize the stability and trustworthiness of our products as well as the craftsmanship involved in manufacturing them. In other words, the key words for Japanese monozukuri are stability, trustworthy, and craftsmanship. Oftentimes we hear the word “high quality” when others evaluate Japanese monozukuri, but we are very careful to use these words only when appropriate. Developing countries tend to use words like “high quality” inappropriately when trying to emphasize a product’s performance. The performance of the products should be defined by the specifications stated by the manufacturers. Also, the quality of the products should be assured by the stability and the trustworthiness of the product’s performance.
Our main product, fluoropolymer, is seeing increasing demand from the semiconductor industry. However, we are not focusing on semiconductor makers but on semiconductor production equipment manufacturers. For example, three years ago we went to a factory in Europe to research demand for our products. We are continuously approaching this kind of manufacturer. This is our strategy for the semiconductor industry.
We’ve been anticipating the wafer size transition from 8 inches to 12 inches - now the standard is 12 inches. Almost all of our fluoropolymer products for the semiconductor industry, which we call chambers, have a size of over 500mm. Our company has been manufacturing this type of product since the establishment of our branch factory in Shiga Prefecture in 2000. Of course, there are different kinds of PTFE makers in Japan. Our company focuses on 12-inch chambers. I think there are only a few makers around the world who can answer the difficult demands for this kind of PTFE chamber. Our company focuses on more precise technology and products of high value but small in quantity in order to maintain our competitiveness among those players. We continuously enhance our processing technology, and our strength is unique.
I believe both the GFRP and the CFRP will be adopted in the next generations of automobiles although their strengths are different. With regard to functionality CFRP is superior, but in terms of cost-effective performance GFRP is superior. I think CFRP will be adopted for future vehicles when it comes to cutting weight and improving performance. In our company we focus on high-performance composite materials, and I think FRP is one of them. We also have technologies for making composite materials for clutch-facing. However, clutch-facing is mainly used in manual transmission cars and the demand for manual transmission vehicles is decreasing from both advanced and developing countries. Now we are trying to develop new composite materials in order to penetrate the new category of hybrid Automated Manual Transmission (AMT) systems. In manual transmission the clutch facing transfers engine power to the tires through friction. This type of transmission is very efficient, but it does not feel very comfortable. Currently the demand for the more comfortable hybrid AMT systems is increasing and if our engineers can successfully develop a clutch facing to be adopted in hybrid AMT systems, I think it will be a great chance for our company to increase our clutch facing business.
I think monozukuri represents not only a standard of quality but also better manufactured products that can be used easily and safely. In other words, the engineers that are engaged in Japanese monozukuri design and make products according to how customers actually use those products. I think the objective of Japanese monozukuri is to offer peace of mind, safety, convenience, and happiness around the world through high quality products. Additionally, I think it is possible for Japanese manufacturers to be competitive against our regional competitors in terms of prices. For example, we could match their level of product performance and cut costs by making use of overseas bases or by polishing our engineering technologies in automation, mechatronics, and robotics.
The electric Allrounder 520 A "Ultimate" is designed for ISO Class 7 cleanroom use and has a clamping force of 165 tons (1,500 kN). The ready-to-use 15-ml PP tubes are produced in an eight-cavity mold from Kebo at an approximate 10-second cycle time. Servo-electric drives ensure precise and reproducible mold positioning in the press, and a label adjustment head from Beck ensures that the labels are precisely aligned and applied. An integrated camera system from Intravis visually inspects the finished parts in real time. In a real application, the tubes could also be screwed together and packaged in tubular bags in the production cell, added Arburg.
Editor in chief of PlasticsToday since 2015, Norbert Sparrow has more than 30 years of editorial experience in business-to-business media. He studied journalism at the Centre Universitaire d'Etudes du Journalisme in Strasbourg, France, where he earned a master's degree.
In addition to facilitating recycling, the mono-material construction and integrated processing of the tube and label contribute to the stability of the tube, enabling a reduction in wall thickness, if needed. The process also eliminates secondary operations, such as bonding and printing. No adhesives are required and there is no waste caused by contamination with liquid color.
I like working with manufacturers of raw materials. I have been to PTFE manufacturers in Japan as well as in Germany many times because we have to find good partners to realize challenging automations. For example, we have to control the movement and bulk properties of the PTFE powder. Many manufacturers have achieved this in small-size production, but this is very difficult for large-size production. Our company has already realized these kinds of innovations, meaning that we can now manage automated powder transportation for moulded products in both small and big sizes. The raw material manufacturers gave us insight about how to control the powder. This is one success story that our company has. We have also developed a technique to mix PTFE with carbon or other materials, for instance, if we need to adjust the conductivity of products. Now we need to focus on material improvement in collaboration with raw material makers - not only with PTFE makers but also carbon nanotube suppliers, to answer the semiconductor industry’s greatest needs.
NPE2024 visitors can see the system in operation at booth W3743. The event returns to the Orange County Convention Center in Orlando, FL, on May 6 to 10.
You have had several co-creation partnerships, such as with a company in Europe, universities in Japan, as well as with raw material companies. Could you tell us a success story from your co-creation activities? Moving towards the future, are you looking for more co-creation partners especially overseas?
Imagine we come back to interview you again five years from now for your 130th anniversary, what would you like to tell us? What are your dreams for the company and what would you like to have accomplished by then?
The Worldfolio provides business, industrial and financial news about global economies, with a focus on understanding them from within.
You mentioned that one of your key strategies is to remain in the semiconductor field which is quite difficult because it is always advancing, and there are big players such as Taiwan’s and South Korea’s semiconductor manufacturers. Can you tell us more about your strategies for this industry and your approach to these big players?
A scale on the scratch-resistant label indicates the exact fill level, which can be relevant for insulin pen and medical measuring cup applications, for example.
GETTING A QUOTE WITH LK-MOULD IS FREE AND SIMPLE.
FIND MORE OF OUR SERVICES:
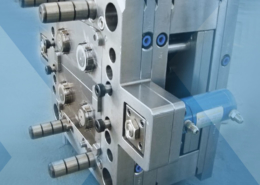
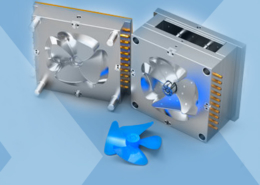
Plastic Molding

Rapid Prototyping
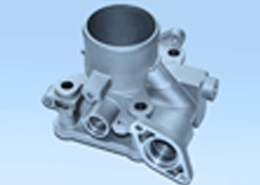
Pressure Die Casting
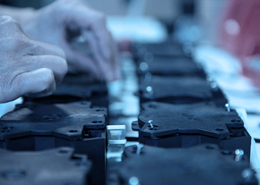
Parts Assembly
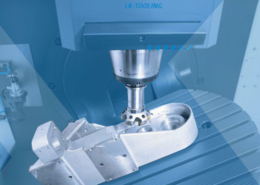