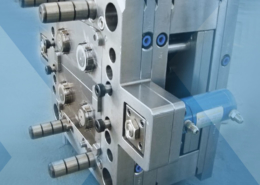
South East Water says it needs cash injection to stay afloat - injection compani
Author:gly Date: 2024-09-30
In this collection, which is part one of a series representing some of John’s finest work, we present you with five articles that we think you will refer to time and again as you look to solve problems, cut cycle times and improve the quality of the parts you mold.
Processors with sustainability goals or mandates have a number of ways to reach their goals. Biopolymers are among them.
The ability to heat the mold quickly and fully control temperature distribution opens up new molding possibilities, including shorter cycles, increased part quality, and longer flow lengths. The hot mold can impart a Class A finish or replicate the finest surface texture. It is now also possible to fully simulate the H&C process with induction heating using Autodesk Moldflow software.
Five industry pros with more than 200 years of combined molding experience provide step-by-step best practices on mounting a mold in a horizontal injection molding machine.
Using Roctool technology, SABIC has demonstrated the ability to achieve a glossy finish on injection molded parts with materials that have historically presented challenges with regard to surface appearance—such as 30% glass-filled Ultem 2300 polyetherimide (PEI), and 50% glass-filled polycarbonate (Thermocomp D551).
A year ago, Roctool sought to address these needs with a new approach whereby we proposed to work with resin providers to quantify the advantages of our H&C technology with their materials versus conventional molding methods. This growing materials database can be used by molders to determine their tool-design choices and by OEMs in their part-design decisions.
Multiple speakers at Molding 2023 will address the ways simulation can impact material substitution decisions, process profitability and simplification of mold design.
While the melting process does not provide perfect mixing, this study shows that mixing is indeed initiated during melting.
This website uses cookies to personalize your content (including ads), and allows us to analyze our traffic. Read more about cookies here. By continuing to use our site, you agree to our Terms of Service and Privacy Policy.
Join KraussMaffei for an insightful webinar designed for industry professionals, engineers and anyone interested in the manufacturing processes of PVC pipes. This session will provide a comprehensive understanding of the technology behind the production of high-quality PVC pipes: from raw material preparation to final product testing. Agenda: Introduction to PVC extrusion: overview of the basic principles of PVC pipe extrusion — including the process of melting and shaping PVC resin into pipe forms Equipment and machinery: detailed explanation of the key equipment involved — such as extruders, dies and cooling systems — and their roles in the extrusion process Process parameters: insight into the critical process parameters like temperature, pressure and cooling rates that influence the quality and consistency of the final PVC pipes Energy efficiency: examination of ways to save material and energy use when extruding PVC pipe products
SABIC, a major global producer of plastics and chemicals with U.S. headquarters in Houston, has collaborated with Roctool for many years. Combining Roctool’s induction-based H&C technology with SABIC’s broad materials portfolio has helped to push the performance and aesthetics of finished parts to a higher level and opens up new application opportunities.
While prices moved up for three of the five commodity resins, there was potential for a flat trajectory for the rest of the third quarter.
In this collection of articles, two of the industry’s foremost authorities on screw design — Jim Frankand and Mark Spalding — offer their sage advice on screw design...what works, what doesn’t, and what to look for when things start going wrong.
Thousands of people visit our Supplier Guide every day to source equipment and materials. Get in front of them with a free company profile.
Roctool’s growing database shows the increased flow length possible for various resins with induction-based H&C technology.
Flex molded this two-piece, snap-fit sphere of glass-filled PC with Roctool H&C technology, demonstrating the adaptability of flexible induction heaters to complex part shapes.
SABIC is now supporting Roctool’s initiative to quantify the effects of induction H&C technology using the HD Plastics Database. Creating a central repository of relevant data on surface replication, weld-line strength and flow length with different materials can provide specific data points to help customers understand the levels of improvement in parts that can be achieved with this H&C technology.
The material characterization is part of Roctool’s ongoing work with resin providers to develop the HD Plastics material database, which is designed to help OEMs achieve exceptional part quality and increased performance. Roctool is constantly adding new providers and materials to grow and reinforce this source of information, which is currently available only to Roctool users but in future will be available to others with a subscription. One snapshot from that database is pictured above.
This month’s resin pricing report includes PT’s quarterly check-in on select engineering resins, including nylon 6 and 66.
Successfully starting or restarting an injection molding machine is less about ticking boxes on a rote checklist and more about individually assessing each processing scenario and its unique variables.
Based on the example of a 14-in. laptop cover, 1 mm thick, of PC with 50% carbon fiber, IDH has been shown to provide these advantages:
Dolls related to books and movies were designed as well, and in the 1930s, Reliable manufactured Shirley Temple dolls, plus “Snow White, and in 1949 Canada’s own sweetheart on skates, Barbara Ann Scott and the CBC’s Maggie Muggins,” said the introduction page, “Growing up with a Reliable Toy,” in the company’s 50th Anniversary Spring/Summer catalogue for 1970. (Maggie Muggins was an endearing character created by Mary Grannan (1900-1975), a Canadian children’s book author and CBC radio/tv personality.)
Dedienne Multiplasturgy Group in France was one of Roctool’s first users. This diversified custom plastic processor wanted to maintain its leadership in an evolving market and anticipate the needs of its customers in terms of innovation and differentiation.
During World War Two, the Canadian government and Reliable partnered to use injection molding to manufacture oil bottles and bullet tips for military weapons use. There was no factory waste involved—the leftover plastic was transformed into toys. Reliable designers turned their focus to what was considered boys’ toys. Miniature soldiers, fighter jets and Avro Aero fighters, ships, jeeps, tractors, and even a version of Sikorsky helicopters with three blades, came off the line.
Electronic OEM Dekko, based in Garrett, Ind., produces high-gloss electrical and USB power packs. Before using H&C technology, Dekko had to deal with part defects and surface imperfections such as knit lines, flow lines, gate blush, and splay.
Reliable Toys offered the classics—cash registers, a “Tidy Miss Housekeeping Set,” plastic tools, toy telephones, several styles of small swimming pools… and let’s not forget the toy boats to keep every kid happy at the water’s edge. The “Souvenir” section featured a statue of a Mountie in red serge and First Nations dolls in stereotypical fashions. (No prices were listed in the catalogue.)
In a time where sustainability is no longer just a buzzword, the food and beverage packaging industry is required to be at the forefront of this innovation. By adopting circular packaging processes and solutions, producers can meet regulatory requirements while also satisfying consumer demand and enhancing brand reputation. Join Husky to learn more about the broader implications of the circular economy — as well as how leading brands are leveraging this opportunity to reduce costs, increase design flexibility and boost product differentiation. Agenda: The cost and operational benefits of embracing circularity Key materials in circular packaging — including rPET and emerging bioplastics How to design a circular food and beverage package Strategies for selecting sustainable closures to future-proof packaging solutions Optimization and streamlining of production processes for enhanced efficiency How Husky Technologies can enable your sustainable success
Join Wittmann for an engaging webinar on the transformative impact of manufacturing execution systems (MES) in the plastic injection molding industry. Discover how MES enhances production efficiency, quality control and real-time monitoring while also reducing downtime. It will explore the integration of MES with existing systems, emphasizing compliance and traceability for automotive and medical sectors. Learn about the latest advancements in IoT and AI technologies and how they drive innovation and continuous improvement in MES. Agenda: Overview of MES benefits What is MES? Definition, role and brief history Historical perspective and evolution Longevity and analytics Connectivity: importance, standards and integration Advantages of MES: efficiency, real-time data, traceability and cost savings Emerging technologies: IoT and AI in MES
A snapshot of part of Roctool’s resin database shows improved results possible with SABIC’s LNP Thermocomp D551 compound of 50% glass-filled PC.
Determining the source of streaking or contamination in your molded parts is a critical step in perfecting your purging procedures ultimately saving you time and money.
Mixed in among thought leaders from leading suppliers to injection molders and mold makers at the 2023 Molding and MoldMaking conferences will be molders and toolmakers themselves.
Dedienne uses Roctool H&C technology for both injection and compression molding. Increased efficiency in compression molding of high-performance materials at high temperatures has made them accessible for mass production. Normally, these materials are reserved for short runs because their processing requires a large amounts of labor and long cycle times. Thanks to rapid induction heating, Dedienne is able to produce a part in a few minutes that would have taken hours otherwise.
Coverage of single-use plastics can be both misleading and demoralizing. Here are 10 tips for changing the perception of the plastics industry at your company and in your community.
Part surfaces at 400X magnification shows that induction-based H&C technology produces much finer replication of mold surface texture than with conventional injection molding.
Ultradent's entry of its Umbrella cheek retractor took home the awards for Technical Sophistication and Achievement in Economics and Efficiency at PTXPO.
Roctool’s induction based High Definition Plastics (HD Plastics) technology can produce high-gloss surfaces, even with filled compounds, and exact replication of the finest mold detail, avoiding the need for secondary decoration.
The Plastics Industry Association (PLASTICS) has released final figures for NPE2024: The Plastics Show (May 6-10; Orlando) that officially make it the largest ever NPE in several key metrics.
The aim of this presentation is to guide you through the factors and the numbers that will help you determine if a robot is a smart investment for your application. Agenda: Why are you considering automation? What problems are you trying to solve? How and why automation can help Crunch the numbers and determine the ROI
Join Engel in exploring the future of battery molding technology. Discover advancements in thermoplastic composites for battery housings, innovative automation solutions and the latest in large-tonnage equipment designed for e-mobility — all with a focus on cost-efficient solutions. Agenda: Learn about cutting-edge thermoplastic composites for durable, sustainable and cost-efficient battery housings Explore advanced automation concepts for efficient and scalable production See the latest large-tonnage equipment and technology innovations for e-mobility solutions
This Knowledge Center provides an overview of the considerations needed to understand the purchase, operation, and maintenance of a process cooling system.
Learn about sustainable scrap reprocessing—this resource offers a deep dive into everything from granulator types and options, to service tips, videos and technical articles.
Current hybrid composite overmolding processes generally utilize an infrared oven for preheating a consolidated thermoplastic “organosheet” and then transport the softened sheet via robot and/or conveyor to the cold mold. IDH technology uses a single induction generator for the entire process. It starts with robotic placement of a cold composite insert in the tool, which is already heated by the induction generator. Meanwhile, a small amount of power is sent to second, small induction heating station to heat up a sheet of solid graphite of the same size as the composite insert. The robot takes the hot graphite sheet from the induction station and places it close to the exposed “B” side of the composite insert in order to heat that second surface by radiation. The composite insert is then stamped to the desired shape, the mold opens, and the mold half with the composite insert rotates into the injection station for overmolding. The induction generator switches power from the stamping mold to the injection mold and back again.
Changes were afoot in the overcrowded workplace and the original partnership dissolved in 1922. Owned only by Samuels brothers, the business name changed to Reliable Toy Company Limited. That same year, processes were altered from outsourcing toy components to designing original dolls and producing their own parts.
About to undergo even greater expansion, the firm “bought the assets of their former competitor, Dominion Toy, in 1933,” said CMC. The Canadian toy market was now their own and generations of children delighted in playtime with colourful Reliable toys. Moving beyond borders, Reliable-brand toys were sold in countries scattered across the globe.
Another challenge for H&C molding is cycle time. Many years ago, when Roctool started using its induction heating technique for rapid H&C injection molding, there was an unacceptable cycle-time penalty. Today, we are able to match a conventional molding cycle or even reduce it, depending on the resin used. At NPE2018 last month, we demonstrated a 16-cavity tool molding glass-filled PBT/ASA parts, each with a different surface finish or texture, in a 20-sec total cycle time on a KraussMaffei injection machine. This is a game changer, as now you can make defect-free parts and not sacrifice productivity. We have not seen any other heating method able to heat and cool so quickly and with such accuracy and control.
ABOUT THE AUTHOR: Mathieu Boulanger joined Roctool in January 2004. In 10 years at Roctool headquarters in France, he was responsible for global sales, key accounts, and strategic marketing of the company’s technologies, which he helped introduce into such markets as automotive, electronics, consumer products, and aerospace. In 2013, Matt started developing the North American subsidiary for Roctool, now based in Charlotte, N.C. In 2015, Matt was named Roctool CEO.
Requiring more workspace, “the company was able to move to a larger building on King Street West where they occupied 3,000 square feet of space,” according to Canadian Museum of Civilization. (CMC) Still too small, the plant shifted again. More than quadrupling floorspace to 13,000 square feet, in 1928 the Reliable factory moved to Phoebe Street near downtown Toronto.
Dekko chose Roctool induction H&C over other technologies for two main reasons: First, H&C offered a cost-benefit vs. changing the part design to achieve what was required with traditional tooling. Second, Dekko uses a variety of molded-in colors, and Roctool H&C technology provides excellent surface quality that avoids the need for paint.
Flex changed to Roctool induction technology for several reasons, including that it is a clean, safe system offering faster cycle times, lower energy consumption, limitless material possibilities, better temperature control, and low corrosion on molds. Flex faced challenges in changing to Roctool technology—mainly convincing technicians and other coworkers to try something new and different. But Flex is looking to use Roctool H&C technology in the future to be able to process all types of materials, including carbon-fiber composites and new product designs through light-weighting and in-mold decorative effects on high-value parts. “Roctool can be environmentally friendly due to eliminating the need for secondary operations, and is very safe for operators, which comes at no extra price,” explains Sebastien Ignotis, director of Advanced Engineering at Flex.
Competitors from the United States and overseas slammed into the Canadian toy market, disrupting the Canadian toymaker’s dominance. In 1985, Allied Sign Letters acquired Reliable Toy Company Limited. The manufacturer was merged “into one of its divisions, Viceroy Manufacturing Company Limited of Toronto.” stated Fortier. “Production soon shifted to the factory of that well-known Canadian toy making firm.”
Plastics processors are finding applications for 3D printing around the plant and across the supply chain. Here are 8 examples to look for at NPE2024.
Across the show, sustainability ruled in new materials technology, from polyolefins and engineering resins to biobased materials.
© 2024 The Kingston Whig Standard, a division of Postmedia Network Inc. All rights reserved. Unauthorized distribution, transmission or republication strictly prohibited.
Formnext Chicago is an industrial additive manufacturing expo taking place April 8-10, 2025 at McCormick Place in Chicago, Illinois. Formnext Chicago is the second in a series of Formnext events in the U.S. being produced by Mesago Messe Frankfurt, AMT – The Association For Manufacturing Technology, and Gardner Business Media (our publisher).
Despite price increase nominations going into second quarter, it appeared there was potential for generally flat pricing with the exception of a major downward correction for PP.
IDH provides a resin-rich surface, is adapted to complex geometries, and can utilize nonwoven and sandwich composite inserts, which can be more difficult to handle when hot in the conventional process. What’s more, IDH can even use non-consolidated sheets, saving a processing step and potentially reducing the cost of composite raw materials. IDH can provide multi-zone heating at temperatures up to 400 C (752 F), and is suitable for both thermoplastic and thermoset materials.
Say “manufacturing automation” and thoughts immediately go to the shop floor and specialized production equipment, robotics and material handling systems. But there is another realm of possible automation — the front office.
Discover how artifical intelligence is revolutionizing plastics processing. Hear from industry experts on the future impact of AI on your operations and envision a fully interconnected plant.
August 29-30 in Minneapolis all things injection molding and moldmaking will be happening at the Hyatt Regency — check out who’s speaking on what topics today.
Roctool’s patented technology consists of designing a H&C mold layout in order to provide fast and homogeneous heating. Flexible inductors can follow any complex tooling shape. A high-frequency current is generated to run through the inductors, creating eddy currents and a joule effect to heat the mold surface up to 1000 C (1832 F) at rates up to 25° C (45° F) per second. What’s more, the heating is applied only to the cavity surface rather than the whole mold half, minimizing energy consumption. Using standard water-cooling channels and ensuring a fully turbulent flow rate enable efficient cooling of the tool.
According to Matthieu Crepin, Dedienne’s deputy managing director, Roctool is a technology provider and source of design support since it formed a design team last year. These resources have accelerated Dedienne’s deployment of injection molded high-heat materials, especially in the U.S. market with Dedienne’s Met2Plastic subsidiary based in Chicago, which has implemented the Roctool induction technology process. “By opening their own design offices, Roctool has responded to some of our main challenges. We are very much looking forward to the benefits of this new approach for high-heat materials,” Crepin says
Launching a business after the First World War was an operation of hope for the future after surviving the ache of gruesome war. In the mid-1900s, Reliable Toy Company Limited produced toy soldiers, dolls, riding tractors and an array of innovative, fun items. The Toronto factory transformed from a local business into the largest toy manufacturer in the British Empire.
In 1920, Alexander Samuels, his brother Solomon Frank Samuels and two other men established Canadian Statuary and Novelty Company to produce stuffies in plush fabrics, smaller novelty toys, and dolls. Another brother, Ben Samuels, later joined the operation. The workspace was cramped into only 500 square feet at the Queen Street location. At first, the owners “imported bisque doll heads from Germany, put it on a body made from a U.S. company and assembled these into their own dolls,” said Delta Museum and Archives. The dolls were popular with customers, sparking a spurt of commercial growth.
Resin drying is a crucial, but often-misunderstood area. This collection includes details on why and what you need to dry, how to specify a dryer, and best practices.
The part is center-gated behind the logo, but the H&C process leaves no sink mark or blemish. This product design is used by Flex for both a room scent diffuser and a Bluetooth audio speaker.
The toy manufacturing giant moved to Carlaw Street in Toronto with 72,000 square feet of space. Producing composite dolls with heads and limbs created from a recipe of cornstarch, sawdust, and glue or resin, the parts were attached to a cuddly soft body. Reliable then added full-service touches. “This factory contained a complete knitting mill to manufacture clothing for dolls and featured a hairdressing department,” described CMC. The factory had “specialty sections for making voice boxes and squeakers, shoes, and eyes.”
Performing fundamental maintenance inspections frequently assures press longevity and process stability. Here’s a checklist to help you stay on top of seven key systems.
With advocacy, communication and sustainability as three main pillars, Seaholm leads a trade association to NPE that ‘is more active today than we have ever been.’
However, our ongoing investigation with resin providers is demonstrating many other advantages that can greatly help molders around the globe: increasing flow length, reducing or eliminating sink marks, reducing pressure drop, enabling thin-wall molding, and enhancing surface replication for optical and functional applications. The latter benefit, in particular, is one reason Roctool has adopted the trade name “HD Plastics” (HD for High-Definition) to describe our overall H&C technology program.
Winning the hearts of little girls, sweet-faced dolls were made in 300 engaging versions. By 1936, Reliable’s yearly production soared to 1.5 million dolls. One of the company’s first dolls was “Mama,” a baby doll with an internal device that produced crying sounds when turned over on its back.
Adapting amazing new technologies, management invested in injection-molding equipment for plastic toy components. Developed in the late 1800s, plastic was an industry-changing invention, and injection-molding added an enhanced level of progress. “In 1931 French Ivory Products of Toronto, making cellulose acetate caps for toothpaste tubes, operated the first injection-molding machine in North America,” said Charles Law in “Plastics-Processing Industry,” The Canadian Encyclopedia, edited December 16, 2013.
While the major correction in PP prices was finally underway, generally stable pricing was anticipated for the other four commodity resins.
Join this webinar to explore the transformative benefits of retrofitting your existing injection molding machines (IMMs). Engel will guide you through upgrading your equipment to enhance monitoring, control and adaptability — all while integrating digital technologies. You'll learn about the latest trends in IMM retrofitting (including Euromap interfaces and plasticizing retrofits) and discover how to future-proof your machines for a competitive edge. With insights from industry experts, it'll walk you through the decision-making process, ensuring you make informed choices that drive your business forward. Agenda: Maximize the value of your current IMMs through strategic retrofitting Learn how to integrate digital technologies to enhance monitoring and control Explore the benefits of Euromap interfaces and plasticizing retrofits Understand how retrofitting can help meet new product demands and improve adaptability Discover how Engel can support your retrofitting needs, from free consultations to execution
Additive technology creates air pockets in film during orientation, cutting down on the amount of resin needed while boosting opacity, mechanical properties and recyclability.
Plastics Technology covers technical and business Information for Plastics Processors in Injection Molding, Extrusion, Blow Molding, Plastic Additives, Compounding, Plastic Materials, and Resin Pricing. About Us
When, how, what and why to automate — leading robotics suppliers and forward-thinking moldmakers will share their insights on automating manufacturing at collocated event.
Three case histories of customers that switched from other molding methods to rapid H&C with Roctool induction technology.
Core Technology Molding turned to Mold-Masters E-Multi auxiliary injection unit to help it win a job and dramatically change its process.
After successfully introducing a combined conference for moldmakers and injection molders in 2022, Plastics Technology and MoldMaking Technology are once again joining forces for a tooling/molding two-for-one.
Part surfaces at 400X magnification shows that induction-based H&C technology produces much finer replication of mold surface texture than with conventional injection molding.
Plastic became a standard material for toy manufacturers, allowing for smooth edges and no splinters to pierce wee tender fingers. The toy company “founded Reliable Plastics Company Limited no later than 1948, and probably earlier,” wrote Rénald Fortier in “Toys, glorious toys,” at Ingenium Canada.
While prices moved up for three of the five commodity resins, there was potential for a flat trajectory for the rest of the third quarter.
In this collection of content, we provide expert advice on welding from some of the leading authorities in the field, with tips on such matters as controls, as well as insights on how to solve common problems in welding.
“The benefits for us have been largely in the final part appearance, with the elimination of surface defects. Roctool helps us to open the design window to make things feasible that were not achievable for us before,”states Jerry Zawadzde, Dekko program manager.
Flex, based in San Jose, Calif., has used all types of H&C technologies for many years, including heating with steam, pressurized water, and electrical cartridges. Flex began working with Roctool after the K 2010 Show in Dusseldorf. The first Flex mold equipped with Roctool technology was for a very thin electronic e-reader/tablet housing. Induction H&C technology was able to fill the part completely, reduce cycle time, and cut energy consumption, thereby outperforming pressurized hot water.
Mold maintenance is critical, and with this collection of content we’ve bundled some of the very best advice we’ve published on repairing, maintaining, evaluating and even hanging molds on injection molding machines.
Sustainability continues to dominate new additives technology, but upping performance is also evident. Most of the new additives have been targeted to commodity resins and particularly polyolefins.
A complex 3D shape molded by Flex demonstrates some of the capabilities of induction-based H&C molding. Exhibited by Roctool at NPE2018 last month, the product is a sphere composed of two snap-fit parts, one of which has multiple oblong holes of different sizes and a curved depression in the top. It is molded of 10-50% glass-filled PC and has thin walls, high gloss, and a molded-in logo.
Introduced by Zeiger and Spark Industries at the PTXPO, the nozzle is designed for maximum heat transfer and uniformity with a continuous taper for self cleaning.
Postmedia is committed to maintaining a lively but civil forum for discussion. Please keep comments relevant and respectful. Comments may take up to an hour to appear on the site. You will receive an email if there is a reply to your comment, an update to a thread you follow or if a user you follow comments. Visit our Community Guidelines for more information.
Take a deep dive into all of the various aspects of part quoting to ensure you’ve got all the bases—as in costs—covered before preparing your customer’s quote for services.
Plastics Technology’s Tech Days is back! Every Tuesday in October, a series of five online presentations will be given by industry supplier around the following topics: Injection Molding — New Technologies, Efficiencies Film Extrusion — New Technologies, Efficiencies Upstream/Downstream Operations Injection Molding — Sustainability Extrusion — Compounding Coming out of NPE2024, PT identified a variety of topics, technologies and trends that are driving and shaping the evolution of plastic products manufacturing — from recycling/recyclability and energy optimization to AI-based process control and automation implementation. PT Tech Days is designed to provide a robust, curated, accessible platform through which plastics professionals can explore these trends, have direct access to subject-matter experts and develop strategies for applying solutions in their operations.
Heating and cooling are both controlled automatically with aid of thermocouples in the mold. Mutiple heating zones can be accommodated. This technology works with P20 and other conventional mold steels and with any type of injection press.
Manufacturing toys for energetic kids of all ages by the 1970s, Reliable built a lively foundation of entertainment for indoors and outside. Bow-and-arrow sets, skipping ropes, spin flyers, and a mountain of plastic trucks, buckets and shovels, plus riding horses, wagons, scooters… the list was nearly endless. The selection even included Easy-Lock Bricks, looking a lot like Lego®.
technotrans says climate protection, energy efficiency and customization will be key discussion topics at PTXPO as it displays its protemp flow 6 ultrasonic eco and the teco cs 90t 9.1 TCUs.
Rapid heat-and-cool molding technologies have attracted increasing interest and use in plastics and composites molding. However, there are still challenges to address before rapid heat-and-cool (H&C) technologies will become widely established as a new molding standard. One of the key challenges is educating the industry on what H&C molding can do and how to quantify the advantages it offers with specific resin families.
Mike Sepe has authored more than 25 ANTEC papers and more than 250 articles illustrating the importance of this interdisciplanary approach. In this collection, we present some of his best work during the years he has been contributing for Plastics Technology Magazine.
Induction heating is more efficient than infrared and can heat to higher temperatures. Replacing the usual infrared preheating of the organosheet before placing it in the mold eliminates the difficulties of handling and precisely positioning a floppy piece of hot organosheet. It also avoids the problem of the preheated insert cooling during transfer. IDH is able to control the heating of both elements in an intelligent way, by adapting the heating time and power automatically. This system is also much more compact and thereby meets the constraints of the electronics sector.
The final challenge for H&C technologies is the ability to integrate heating elements into a complex tool. Our flexible induction coils are available in many diameters and can now be integrated into complex tooling, as we illustrated at NPE2018 in displaying a hemispherical polycarbonate part.
Second quarter started with price hikes in PE and the four volume engineering resins, but relatively stable pricing was largely expected by the quarter’s end.
The results are also shared with Roctool users to support them in their continuing search for improved performance, quality and cost-effectiveness. Many already know that H&C molding can improve surface quality, such as hiding visible weld lines and flow lines.
Exhibitors and presenters at the plastics show emphasized 3D printing as a complement and aid to more traditional production processes.
Additionally, SABIC validated the possibility of combining a low-gloss effect, using texturing, with a high-gloss effect in the same part—a cosmetic effect that appeals to designers.
In this three-part collection, veteran molder and moldmaker Jim Fattori brings to bear his 40+ years of on-the-job experience and provides molders his “from the trenches” perspective on on the why, where and how of venting injection molds. Take the trial-and-error out of the molding venting process.
Gifted with extraordinary technical know how and an authoritative yet plain English writing style, in this collection of articles Fattori offers his insights on a variety of molding-related topics that are bound to make your days on the production floor go a little bit better.
By the early 1960s, Reliable pedalled into the ride-on toy department. “The grand champion Canadian toy that is recognized internationally is the world’s first plastic pedal toy—the Reely Ride-em Tractor introduced in 1961, this Reliable original is popular to this day in advanced design,” noted the company catalogue.
Technical capabilities of the process have advanced to erase former cycle-time penalties, and ongoing developments address creation of a materials database and new applications in hybrid composite injection overmolding.
IDH stands for “Induction Dual Heating,” a new technology for molding parts combining a continuous-fiber thermoplastic composite blank and injection overmolding with additional thermoplastic compound. Such “hybrid” composites are gaining interest because they offer light weight, high strength and stiffness, and design freedom to overmold 3D details and provide surface aesthetics without secondary finishing—and all within a 60-sec cycle time.
Across all process types, sustainability was a big theme at NPE2024. But there was plenty to see in automation and artificial intelligence as well.
GETTING A QUOTE WITH LK-MOULD IS FREE AND SIMPLE.
FIND MORE OF OUR SERVICES:
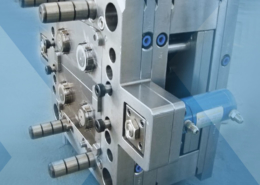
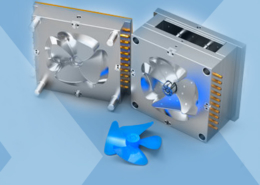
Plastic Molding

Rapid Prototyping
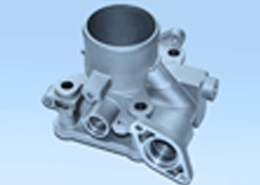
Pressure Die Casting
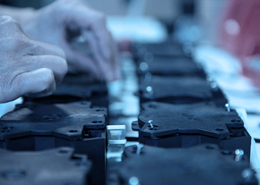
Parts Assembly
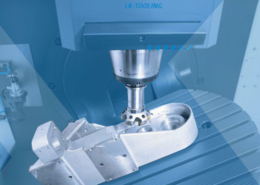