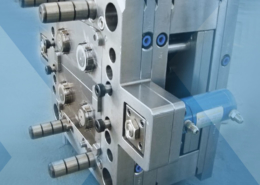
Solidworks 2015 dispels the dark cloud of uncertainty - injection molding solidw
Author:gly Date: 2024-09-30
M-Powered IIoT remote digital solution that uses built-in analytics of real-time machine data to identify causes of downtime, production inefficiencies, and quality issues.
Custom textures and backlighting for automotive and appliance applications using an M-500 machine cell featuring a Mold-Masters hot runner and Kurz in-mold decoration technology.
L-Series low-pressure injection molding machinery, capable of running up to 100% regrind flake material. The machine will not be on site but featured in an animation loop.
Your email address is used only to let the recipient know who sent the email. Neither your address nor the recipient's address will be used for any other purpose. The information you enter will appear in your e-mail message and is not retained by Phys.org in any form.
SG75 extrusion system with a new control, new die heads, and advanced single/twin screws and barrels. The package includes all downstream equipment — vacuum tank, pullers, saws, and more. A cobot at the end of the line will perform demonstrations.
Jobs are in short supply, and yet some sectors have difficulty in finding suitable trainees for specialist tasks, such as polishing injection molds. The work is time-consuming and monotonous but requires highest levels of concentration, because any blemish in the mold can render it useless. A skilled worker may often need a whole week to polish a single metal mold. Up to now it has not been possible to use machines for this dreary work because they cannot get into the curved shapes.
“We can set the melting depth by means of various parameters: the laser output, the speed at which the laser beam travels along the surface and the length of the laser pulses,” states Willenborg. Laser polishing does not achieve the same surface smoothness as perfect hand polishing - hand polishers can achieve a roughness Ra of 5 nanometers, the laser at present can only manage 50 nanometers - but Willenborg still sees considerable market potential for the system. “We will concentrate on automating the medium grades: a roughness of 50 nanometers is adequate for many applications, including the molds used for making standard plastic parts.” The high-end levels of smoothness will therefore remain the domain of skilled hand polishers.
Use this form if you have come across a typo, inaccuracy or would like to send an edit request for the content on this page. For general inquiries, please use our contact form. For general feedback, use the public comments section below (please adhere to guidelines).
Milacron’s M-Series injection molding machine (IMM) platform will make its North American debut at NPE2024, featuring in two applications at the Ohio-based company’s booth from May 6 to 10 in Orlando, FL.
(PhysOrg.com) -- Polishing metal surfaces is a demanding but monotonous task, and it is difficult to find qualified young specialists. Polishing machines do not represent an adequate alternative because they cannot get to difficult parts of the surface. A new solution is provided by laser polishers.
The time gained by laser polishing and the cost saving achieved are enormous. Whereas a skilled polisher needs about 10 to 30 minutes for each square centimeter, the laser polishes the same area in about a minute. A prototype of the laser polishing machine developed by the scientists in cooperation with mechanical engineering firm Maschinenfabrik Arnold has already been built. Willenborg estimates that the system will be ready for industrial use in one to two years’ time. At the Euromold trade show, to be held from December 2 to 5 in Frankfurt, the researchers will be presenting examples of three-dimensional surfaces polished by laser.
Geoff Giordano is a tech journalist with more than 30 years’ experience in all facets of publishing. He has reported extensively on the gamut of plastics manufacturing technologies and issues, including 3D printing materials and methods; injection, blow, micro and rotomolding; additives, colorants and nanomodifiers; blown and cast films; packaging; thermoforming; tooling; ancillary equipment; and the circular economy. Contact him at [email protected].
The M-Series features as standard the largest clamp stroke in the mid-tonnage hybrid range, the company said. Fanuc motors and drives power the platform, which is based on two-platen technology and can be integrated with multiple co-injection technologies to support customer sustainability requirements.
Researchers at the Fraunhofer Institute for Laser Technology ILT in Aachen have developed a way of automating the polishing work: “We do not polish the surface by hand with grinding and polishing media. Instead we use a laser,” explains Dr.-Ing. Edgar Willenborg, group leader at the ILT. “The laser beam melts the surface to a depth of about 50 to 100 micrometers. Surface tension ensures that the liquid metal flows evenly and solidifies smoothly.” Like in conventional grinding and polishing, the process is repeated with increasing degrees of fineness. In the first stage the researchers melt the surface to a depth of about 100 micrometers, in further steps they gradually reduce the depth.
All-electric Fanuc Roboshot in two applications. The Robo 55, using liquid silicone rubber material and automation, will be in a cell featuring a micro plunger to control a tiny shot for an umbrella part. The Robo 275 will demonstrate a 48-cavity medical vial application using Milacron’s stainless steel water system and new M3 thermocouple technology from Mold-Masters.
Q-Series platform, a low- to mid-tonnage range featuring double-toggle design and servo-hydraulic operation for fast production using less energy. A Q-170 machine with G3 Mosaic control and DME mold technology using bio-resin will be featured in a mobile phone holder application.
A 21.5-inch touch screen control panel with swing arm to improve viewing of the mold area. The panel’s “plus” section enables configurable screen viewing; 8+8 configurable I/Os is standard.
A two-cavity mold-pail application with up to 50% recycled core and in-mold labeling automation performed by the M-1070 using Mold-Masters co-injection technology.
We keep our content available to everyone. Consider supporting Science X's mission by getting a premium account.
Get weekly and/or daily updates delivered to your inbox. You can unsubscribe at any time and we'll never share your details to third parties.
GETTING A QUOTE WITH LK-MOULD IS FREE AND SIMPLE.
FIND MORE OF OUR SERVICES:
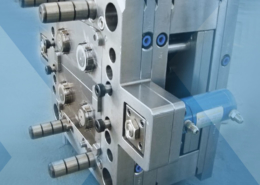
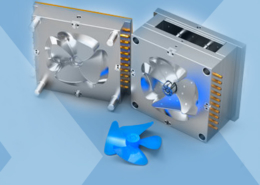
Plastic Molding

Rapid Prototyping
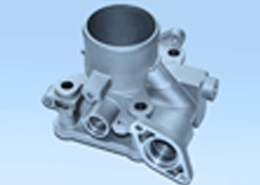
Pressure Die Casting
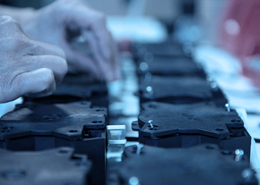
Parts Assembly
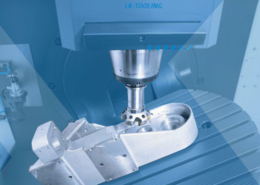