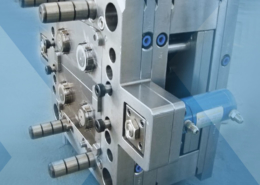
Singlife receives $179.9m capital injection from Sumitomo Life - sumitomo inject
Author:gly Date: 2024-09-30
The result of more consistent part weights throughout the batch is a very rapid return on investment (ROI), assures Schilling. Additionally, it leads to better process consistency, longer machine uptime, and reduced scrap, all contributing to greater sustainability. A lower reject rate results in higher output, increasing efficiency and conserving resources. "Furthermore, customers benefit from greater manufacturing flexibility, as a wider range of material variations can be accommodated when using PCR/PIR types."
Sumitomo (SHI) Demag is aiming to enhance sustainability with the launch of activeMeltControl (aMC) for its all-electric injection moulding machines.
It can be easily activated with a single click and runs fully automatically in the background. "The software compensates for viscosity fluctuations and backflow barrier leaks, adjusting the pressure accordingly. Customers can tailor it to their specific process needs and respond to the machine's characteristics using an adjustment controller," reports Schilling. Initially, aMC will be available for all IntElect 2 series full-electric injection moulding machines from the first quarter of 2024, with retrofits planned for the future.
The system employs Mantle’s H13 and P2X tool steels, which perform like traditional materials in secondary operations such as machining, polishing, coating, and laser welding. Tool paths and machine instructions are automated with the system’s easy-to-use software.
myAssist also aligns with the "Act! Sustainably" motto by reducing downtime and optimising resources and capacities. It also supports the global traceability standard for plastic products, R-Cycle, through QR codes, material labels, end products, and the upload of production data. "myAssist is future-proof, as it serves as our foundation for future cross-process AI applications. AI learns faster, analyses more accurately, and adapts better. It can contribute to greater sustainability and efficiency," concludes Schilling.
The background for this development, which Sumitomo (SHI) Demag has vigorously pursued over the past four years, is the changing quality of plastics with fewer virgin materials and more recyclable content. "Many customers have requested a digital solution to compensate for these variations in our highly efficient and precise machines. That's why we introduced aMC as a completely independent software module alongside our established active modules," explains the product manager for Digital Solutions.
The simplified toolmaking system comes at a critical time for the $265-billion molded parts market, asserted one expert.
Global contract manufacturer Tessy Plastics surpassed 1.25 million cycles on a deodorant packaging mold built with Mantle components and slashed production time 60%, from 150 to 60 hours.
Wisconsin’s Nicolet Plastics will install one of Mantle’s first production systems to bring tool production in house and increase tool complexity. Mantle’s system will let Nicolet “significantly reduce the time it takes to produce production-quality tools and be able to start production in weeks versus months,” according to CEO Tony Cavalco. “Our tool designers and project managers will utilize the Mantle system for projects involving high-volume part manufacturing. Mantle technology will allow us to design conformal cooling channels to reduce molding cycle time and ensure the highest quality products for our customers.”
"We've improved process stability and performance while reducing data volume for better transmission. Additionally, myAssist offers more data exchange and analysis possibilities, as well as improved connectivity to other systems," adds the expert. It also includes a high-speed knowledge database with I/O interfaces as a basic system for IoT 4.0. An HVI (Human Virtual Interface) and an expertise module provide options for manual process annotations. Moreover, myAssist connects all new IntElect machines.
Westminster Tool integrated a Mantle beta system into its mold-making operations, finding that the printer’s precision lets them bypass many internal manufacturing processes, said founder and president Ray Coombs. “Mantle far surpasses any additive metal technology that we have seen previously.”
The P-200 printer, with a build volume of 200 x 200 x 150 mm, is produced on a CNC platform that combines printing and machining for superior accuracy and surface finish. The F-200 furnace sinters parts and can support multiple printers.
Furthermore, Sumitomo (SHI) Demag has optimised its Smart Solution, myAssist, for easier usability. The software enhances process transparency for injection moulders by providing more insights into process parameters. "We are transforming myAssist into a digital process companion. We have optimised interfaces, improved data collection and visualization," says Schilling. The user interface is now flexible and customizable to individual customer preferences, allowing for the representation of cycle- and time-based data. Users can create custom dashboards with material or consumption data or define their own key performance indicators (KPIs) to track the process.
Using its patented TrueShape technology, Mantle’s flagship products, the P-200 printer and F-200 furnace, have already cut tooling lead times and costs by more than 50%, the company said. Toolmakers who have installed beta systems include Tessy Plastics, Nicolet Plastics, Fathom Manufacturing, and Westminster Tool. The first full production systems are slated for delivery in the first half of 2023.
"With aMC, we can compensate for shot weight variations in nearly all applications and materials, whether it's due to batch fluctuations, recyclables, regrind, drying differences, dosing variations, or the use of additional additives," explains Dr. Thomas Schilling, product manager for Digital Solutions. For example, shot weight fluctuations in 100% recycled material can be corrected by the software, bringing it to the level of virgin material. "This significantly reduces the customer's reject rate. Depending on the process and material, it goes towards zero."
“There is a massive skills gap in the injection mold-making industry,” said Hillary Thomas, Westminster Tool Vice President. “Mantle’s technology is so intuitive that, with minimal training, we can have someone quickly operating and running this machine. Mantle will help Westminster Tool change how we do business.”
These machines, known for their unique precision and high energy efficiency, have been leading the way in sustainable plastic processing. At Fakuma 2023, the company is unveiling new digital features that further reinforce its commitment to sustainability, as conveyed by the slogan "Act! Sustainably."
A new metal 3D-printing system from San Francisco’s Mantle promises to dramatically reduce the time and cost of creating injection mold tooling.
Geoff Giordano is a tech journalist with more than 30 years’ experience in all facets of publishing. He has reported extensively on the gamut of plastics manufacturing technologies and issues, including 3D printing materials and methods; injection, blow, micro and rotomolding; additives, colorants and nanomodifiers; blown and cast films; packaging; thermoforming; tooling; ancillary equipment; and the circular economy. Contact him at [email protected].
On-demand digital platform Fathom Manufacturing cut toolmaking time 45%, from 200 to 110 hours, by eliminating or reducing operations including CNC milling, EDM, and polishing.
activeMeltControl (aMC) is an adaptive, fully automatic control process integrated into the machine's control system, providing greater process continuity. This, in turn, generates various effects that benefit sustainable manufacturing.
GETTING A QUOTE WITH LK-MOULD IS FREE AND SIMPLE.
FIND MORE OF OUR SERVICES:
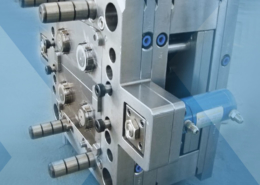
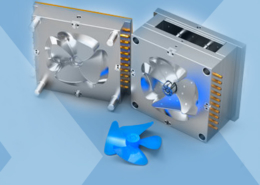
Plastic Molding

Rapid Prototyping
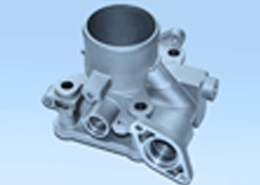
Pressure Die Casting
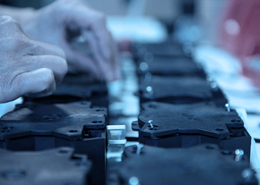
Parts Assembly
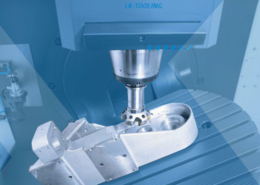