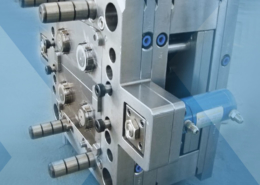
Exploring the Dynamics of Plastic Injection Molding Prices
Author:gly Date: 2024-06-08
Introduction
Understanding the intricacies of plastic injection molding prices is crucial for businesses seeking cost-effective manufacturing solutions. This article delves into the factors influencing pricing in the injection molding industry, providing insights into cost structures and strategies for optimizing production expenses.
Background
Plastic injection molding serves as a cornerstone of modern manufacturing, offering versatility, efficiency, and cost-effectiveness in producing a wide range of plastic components. However, the pricing dynamics of injection molding are influenced by various factors, including material costs, tooling expenses, production volume, and market demand.
Material Costs
Raw Material Selection
The choice of raw material significantly impacts injection molding prices. Resin prices vary based on factors such as type, grade, and market demand. High-performance engineering plastics command higher prices compared to commodity-grade polymers, reflecting their superior properties and processing requirements.
Material Consumption
The amount of material consumed per part directly affects manufacturing costs. Optimizing part design to minimize material usage while maintaining structural integrity can lead to substantial cost savings. Additionally, using recycled or bio-based materials may offer environmental benefits and cost advantages in certain applications.
Market Volatility
Fluctuations in raw material prices, influenced by factors such as global supply chain disruptions, geopolitical tensions, and economic conditions, pose challenges for injection molders. Price volatility can impact profitability and necessitate proactive strategies, such as inventory management and supplier diversification, to mitigate risks.
Tooling Expenses
Mold Design Complexity
The intricacy of mold design plays a pivotal role in determining tooling costs. Complex geometries, undercuts, and intricate features require specialized mold configurations, increasing tooling expenses. Collaborating with experienced mold designers and leveraging advanced manufacturing techniques, such as multi-cavity molds and rapid prototyping, can optimize tooling costs.
Tooling Material and Maintenance
The selection of tooling materials, such as steel or aluminum, impacts both initial investment and long-term maintenance costs. While steel molds offer durability and longevity, they entail higher upfront expenses. Conversely, aluminum molds may provide cost advantages for low-volume production but require periodic maintenance and refurbishment.
Tooling Lifecycle Management
Effective tooling lifecycle management involves regular maintenance, repair, and replacement to ensure optimal performance and prolong tool longevity. Implementing preventive maintenance programs and investing in tooling upgrades and refurbishments can enhance productivity, minimize downtime, and mitigate unplanned expenses associated with mold wear and tear.
Production Volume
Economies of Scale
Production volume exerts a significant influence on per-unit manufacturing costs through economies of scale. Higher production volumes typically result in lower per-part costs due to distributed fixed expenses and increased operational efficiency. Strategic planning and forecasting are essential for maximizing economies of scale and optimizing production costs.
Batch Size Optimization
Balancing production volume with market demand is essential for minimizing costs and avoiding excess inventory. Batch size optimization strategies, such as just-in-time manufacturing and lean production principles, enable manufacturers to align production levels with customer requirements, reduce lead times, and minimize waste while optimizing cost efficiency.
Customization and Complexity
The level of customization and product complexity impacts manufacturing costs, particularly in low-volume, high-mix environments. Customized tooling and setup requirements may incur additional expenses, necessitating flexible production processes and agile manufacturing capabilities to accommodate diverse customer needs while maintaining cost competitiveness.
Conclusion
In conclusion, navigating the intricacies of plastic injection molding prices requires a comprehensive understanding of the underlying factors shaping cost dynamics. By strategically managing material costs, optimizing tooling expenses, and leveraging production volume efficiencies, businesses can achieve cost-effective manufacturing solutions while maintaining product quality and competitiveness. Embracing technological advancements, adopting sustainable practices, and fostering collaborative partnerships are key strategies for driving innovation and resilience in the injection molding industry amidst evolving market dynamics.
GETTING A QUOTE WITH LK-MOULD IS FREE AND SIMPLE.
FIND MORE OF OUR SERVICES:
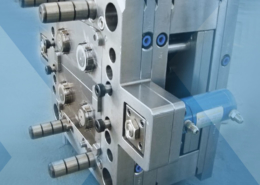
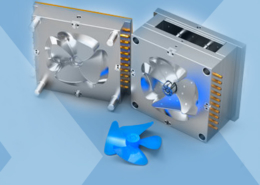
Plastic Molding

Rapid Prototyping
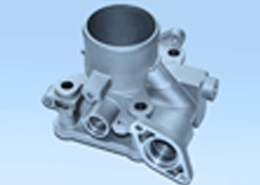
Pressure Die Casting
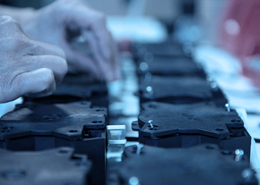
Parts Assembly
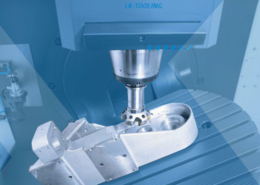