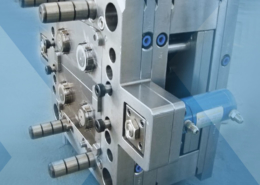
Singapore-based precision plastics manufacturer accelerates seamless
Author:gly Date: 2024-09-30
The test demonstrated for the first time that the plastics injection molding and shredding processes have, in principle, no property-altering effects on the material over the entire period of reuse. With the service life of containers being around 10 to 20 years, this result means that the availability of material for sustainable production from the same recycled plastic is secured for at least 100 to 200 years.
Arburg and CamdenBoss celebrate the Mildenhall-based company’s new investment in moulding capability at the grand launch, 25th October 2022.
Compared to 2015, the collection of HDPE bottles fell by 31.7 million pounds to 1,112.1 million pounds. The HDPE bottle recycling collection rate dropped to 33.3% in 2016 compared to the 2015 rate of 34.4%. The amount of HDPE reported to have been processed by a survey of U.S. HDPE reclaimers fell by 37 million pounds to 992.7 million pounds. While HDPE recycled bottle domestic collection decreased slightly compared with 2015, exports increased and imports held constant to account for the lesser amount of HDPE bottles processed. The number of HDPE reclaimers reporting increased in 2016 as compared to 2015, with 31 companies active at year’s end, noted the report.
By doing this the more vertically-integrated company, part of Heathpatch Ltd, has its design, warehousing and manufacturing operations in one location to meet customer requirements across electro-mechanical components, flat sheet plastic custom enclosures and now injection moulded enclosures.
The new machines, all of which are electric, form part of the firms strategy to bring moulding operations in-house from suppliers in the UK and overseas.
In Europe, ESE World B.V., which became part of RPC Group a year ago, has carried out the first practical experiment to demonstrate that HDPE can be recycled at least 10 times and further processed under controlled conditions. The company has been the leader in the use of recycled plastics for the manufacture of containers for waste and recyclables for over 30 years. Its advanced processes in cleaning, additives and processing of the material enables ESE to make products from recycled plastics having the same quality as virgin material.
Considering that PET (#1) and HDPE (#2) comprise 97% of all plastic bottles on the market in North America and are the easiest materials to recycle, the recycling industry often questions why their rate of recycling is not higher. According to a report from the Association of Plastic Recyclers (APR) and American Chemistry Council (ACC) released this past November, the total pounds of plastic bottles collected decreased by 71 million pounds in 2016 compared with 2015, with decreases for both PET and HDPE.
However, one question that has remained unanswered until now was how often HDPE can be processed, ground and reprocessed via injection molding without fundamentally changing the structure and characteristics of the material.
ESE, therefore, established a controlled experimental model at its production facility. After each step, the material was analyzed in cooperation with external research institutions. The project was led by ESE’s plastics specialist and scientist, Jeanette Köhn, PhD.
All-electric machines typically consume less energy than hydraulic machines on a like-for-like set-up and running cycle times. But there are many variables involved in machine selection, allowing for some set-ups, cycle times and machinery age etc, servo-hydraulic machines can be more suited to the process.
“We are delighted to support CamdenBoss as they bring injection moulding capability in-house at their Mildenhall site,” said Arburg Ltd. managing director Colin Tirel. “Setting up new mould shops is always exciting and satisfying and working towards a long-term relationship is what it is all about. Bringing new capabilities in-house is a great sign of the company’s confidence in their abilities and their customer base, so that’s a really positive sign in these challenging times.”
An all-electric Allrounder 570 A 2000 - 800 ALLDRIVE 200 tonne modular machine is one of CamdenBoss’s four new Arburg machines revealed in October as the company brings some production capacity in-house from the UK and abroad.
“Choosing all-electric machines reflects an increasing trend that more customers are looking at reducing energy consumption,” said Colin Tirel. “Arburg supplies electric, servo-hydraulic and hybrid machines and it is always important to discuss and offer the most appropriate technology against their set requirements before deciding which technology suits the customer's requirements the best. We are delighted that CamdenBoss chose Arburg to be its partner.”
The decision to create a new moulding facility from scratch was driven by the various efficiencies this could bring, and CamdenBoss’s desire to be a more independent and integrated manufacturing company. Katy Davies, managing director of CamdenBoss, said, “CamdenBoss has been committed to repatriating its injection moulding to the UK for several years, and this investment takes us to the next level of producing as much as possible as locally as possible to support our growing customer base efficiently, effectively and with greater resilience. It also allows us to develop the skills of our people through apprenticeships while cementing our commitment to reducing our environmental impact.”
CamdenBoss selected the latest electric Arburg equipment which, along with the company’s recent investment in solar power and lower transport mileage by manufacturing on-site, significantly reduces the carbon footprint of its operations and accelerates CamdenBoss’ transition to net zero.
Experiment demonstrates that HDPE plastic can be recycled at least 10 times and further processed under controlled conditions.
Helping consumers and municipalities understand the value of recycled HDPE would go a long way toward increasing HDPE recycling rates. Much of HDPE’s value lies in the fact that it can be recycled and reused for a long time without diminishing its properties.
He added: “Choosing Arburg as its sole IMM solution reflects the confidence the team at CamdenBoss have in Arburg. We worked closely with them and supported the team there all the way through, from the initial specifying of the equipment, through to installation and start-up to ensure there was a smooth introduction.”
Until she retired in September 2021, Clare Goldsberry reported on the plastics industry for more than 30 years. In addition to the 10,000+ articles she has written, by her own estimation, she is the author of several books, including The Business of Injection Molding: How to succeed as a custom molder and Purchasing Injection Molds: A buyers guide. Goldsberry is a member of the Plastics Pioneers Association. She reflected on her long career in "Time to Say Good-Bye."
Udo Fröhlingsdorf, Director of Product Development & Marketing at ESE, is very pleased with the test results. "Decades of developments under production conditions have put us in the position to process and treat recycled material in such a way that the quality of the products is on a par with virgin material. The findings of this series of experiments now allow us to engage in more targeted research and to develop further future-oriented methods."
The new machine inventory includes robot systems for material handling and comprises one Arburg 570 A 2000 - 800 Alldrive 200 tonne modular electric machine, fitted with a 6kg Multilift Select robot system; two Arburg 370 A 600 - 170 Alldrive 60 tonne modular electric machines, both fitted with Integral picker V's (IPV), and one Arburg 470 A 1000 - 400 100 tonne modular electric machine, which is fitted with a 6kg Multilift Select robot system. Each machine is specified to meet CamdenBoss' requirements and from Arburg’s energy efficient electric Alldrive range of machines. The automation systems are all integrated and controlled from the machines’ Selogica ND controllers.
The APR and ACC report also noted that one of the primary barriers to increased plastic bottle recycling is that “too many consumers continue to be unaware of the significant usefulness, demand and value of recycled plastic, including HDPE” (as well as PET and PP).
GETTING A QUOTE WITH LK-MOULD IS FREE AND SIMPLE.
FIND MORE OF OUR SERVICES:
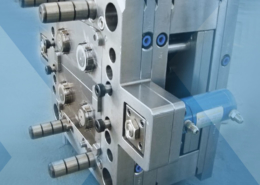
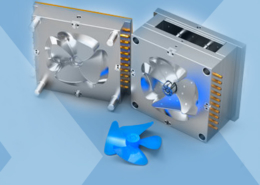
Plastic Molding

Rapid Prototyping
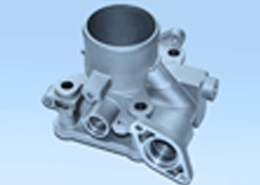
Pressure Die Casting
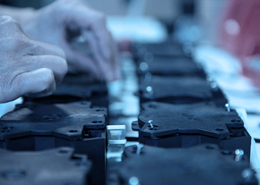
Parts Assembly
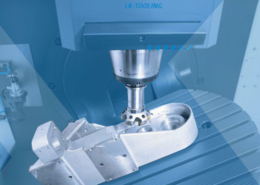