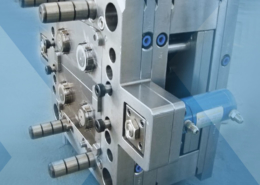
Silcotech expands LSR injection moulding capacity - injection moulding manufactu
Author:gly Date: 2024-09-30
Economists and analysts are watching trends in manufacturing closely, as it’s an industry that is in part driving the economic recovery in the United States. While predictions vary, they all point to significant change. Below are a few trends and predictions related to U.S. plastic manufacturing.
ARBURG is taking a new approach with its local-to-local activities: Whereas ALLROUNDERs were previously built exclusively at the German headquarters in Lossburg, value-added stages are now being internationalised. ARBURG has systematically tailored the ALLROUNDER GOLDEN ELECTRIC EVO, which is available in sizes 370, 470, 520 and 570, to the Asian market. The production of all components and parts requiring expertise and key technologies continues to take place in Germany. Assembly is carried out at the ARBURG Technology Factory in Pinghu, where the range of automation and turnkey solutions is also being continuously expanded in cooperation with local partners. An important point to note here is that "Made by ARBURG" remains "Made by ARBURG"! The new electric entry-level machine is characterised by the high precision of its injection units, short cycle times, faster dry cycle times and a reduction in the energy requirement of up to 50 per cent. At Chinaplas 2024, the exhibit produced precise LSR components for use in cars. A FLEXLIFT linear robotic system was tasked with handling the parts.
With a total of four machine exhibits at Chinaplas 2024, ARBURG presented exciting examples of applications in the key areas of medicine and mobility, which feature prominently in the dynamic Asian market. ARBURG's ability to also implement very successful turnkey systems in China and Asia in collaboration with local partners was demonstrated by a production cell built around an ALLROUNDER 1600 T vertical rotary table machine, which overmoulded metal inserts with glass fibre-reinforced PBT to form complex fluid distributors. Visitors from the medical technology sector familiarised themselves with the advantages of the hybrid ALLROUNDER 470 H. The production cell made two different adapters for medical technology on a fully automatic basis, including camera inspection and sample part storage. A FLEXLIFT 10+2 linear robotic system was used for handling.
3D printers aren’t necessarily new technology in the United States, but the practice of using 3D printing in plastics manufacturing is becoming more and more common. 3D printing is a technology that allows a manufacturer to create virtually any object — as long as it is self-supporting and in one complete piece. While other materials can be used in 3D printing, it’s typically a manufacturing technique used in plastics and resins. The benefits of 3D printing are that the objects can be made more quickly and more efficiently. And importantly, 3D printers are incredibly accurate. Already, 3D printing is being used in the health care industry and is used to create parts and components for almost every sector of manufacturing. It’s a meaningful trend and one that will likely continue to shape how manufacturing is done in the U.S. and abroad. Expect operations that are far more efficient and objects that are manufactured to be more complex, lighter weight and reliable.
ARBURG had an extremely satisfactory trade fair appearance at Chinaplas 2024, which attracted a great deal of attention. Returning to Shanghai after a six-year break, the trade fair saw huge crowds at the National Exhibition and Convention Center and the ARBURG stand. A key highlight was the premiere and unveiling of the ALLROUNDER 470 E GOLDEN ELECTRIC EVO – the new electric entry-level machine for the Asian market. There was also great interest in arburgSOLUTIONworld and the focal topics of digitalisation, mobility and medicine.
A freeformer 300-3X demonstrated how associated EOAT can be additively manufactured quickly and cost effectively. In the ARBURG Plastic Freeforming (APF) process, this was used to 3D print grippers in a multi-material combination. In general, freeformers are suitable for the 3D printing of functional components, EOAT and operating equipment based on original plastic granules – even from very soft materials and in hard-soft combinations.
For reliable performance, a slimline design and an unbeatable price, there is only one choice: the new ALLROUNDER 720 E GOLDEN ELECTRIC!
The arburgXworld customer portal gives you access to a wide range of digital apps and features that make your daily work easier.
Steve Erickson is the Vice President of Sales and Engineering at First American Plastic, bringing more than 30 years of experience from the injection molding industry. First American Plastic is the leading manufacturer and assembler of custom injection molding services in the United States.
The future of plastic manufacturing in the United States is far from certain, but many trends are beginning to take shape. From the accelerating pace of 3D printing innovation to new production procedures, plastic manufacturing will likely continue to be a strong yet steadily changing segment of the manufacturing industry overall.
The future of plastic manufacturing in the United States is far from certain, but many trends are beginning to take shape. From the accelerating pace of 3D printing innovation to new production procedures, plastic manufacturing will likely ...
While 3D printing is one of the more widely recognized manufacturing developments in the last decade — thanks in part to media outlets that like the futuristic sound of it — manufacturing is a hotbed for other innovations. The plastics industry is no different and, in fact, shows much potential for advances resulting from new technologies. The last century saw huge developments in automation — from vehicles to food products to common household items. One major component is the development of robots that can perform manufacturing tasks more quickly than their human counterparts. They are also considered to be less prone to error and cheaper over the long term. Manufacturing robots are getting more precise, and they are increasingly used for more complex tasks. Expect a plastics manufacturing environment in which most physical tasks are done by automated machinery, while engineers, scientists and technology professionals take on a larger role in the industry.
Benefit from our expertise and lower the costs for your injection moulding production by optimising your energy requirement.
Whatever results from the evolving plastics manufacturing industry, it will be an interesting change to observe. In the end, the manufacturers who are best able to adapt will be the ones who thrive. And the ones who are able to embrace changing technology will be the ones who ultimately decide the direction we take.
Some things never change — or at least they are working well enough that the industry has no cause to abandon them. Plastic injection molding falls into that category. It’s one of the most basic and reliable methods for manufacturing plastic components. In short, plastic injection molding is the process of creating a mold and injecting it with thermoplastics and thermosetting polymers to create a sturdy end product. Like 3D printing, it is considered highly accurate and a staple in manufacturing. Every industry from food to automotive relies on plastic injection molding.
"arburgSOLUTIONworld", an exhibition area centred around a four-metre-high LED column, also met with great interest. This is where ARBURG experts offered individual advice on important topics including digitalisation, automation, moulds, sustainability and service. New features for the "arburgXworld" customer portal were also presented, including "ask ARBURG", an AI-supported premium app. The app incorporates the company's extensive injection moulding expertise and can answer specific questions about machines and processes as well as identify and rectify the causes of faults – with no need for an on-site service.
For reliable performance, a slimline design, and an unbeatable price, there is only one choice: the new ALLROUNDER 720 E GOLDEN ELECTRIC!
A bright spot in the seeming manufacturing renaissance (at least, one for U.S. companies) is that it is no longer profitable for manufacturing companies to take business overseas. The global market is changing. Wages are going up in places where labor previously was dirt cheap. Rising costs for shipping have virtually erased any advantage a company might have found by seeking cheaply made products on the other side of the world. Competition is also driving this change. Local companies increasingly have options, and they are getting pickier. They like to have more local control over the products they buy. As a result, they are seeking out manufacturers who do business locally. At this point, it is still unclear what local manufacturers can expect. It’s certainly good news for the locals, but it might not be the return to old times that some hope for — and that’s because the jobs resulting from new domestic manufacturing are almost unrecognizable from the U.S. manufacturing heyday of the mid-1900s. As explained above, technology is largely the reason. So while traditional manufacturing jobs might not make a comeback, the tech side of manufacturing will almost certainly breathe life into the industry.
GETTING A QUOTE WITH LK-MOULD IS FREE AND SIMPLE.
FIND MORE OF OUR SERVICES:
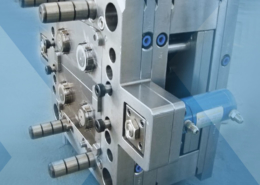
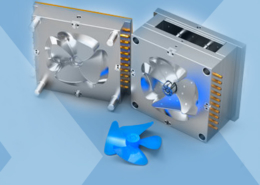
Plastic Molding

Rapid Prototyping
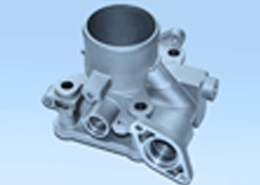
Pressure Die Casting
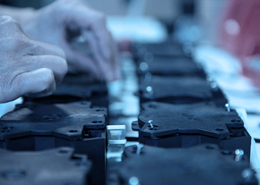
Parts Assembly
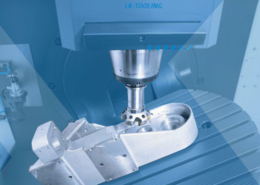