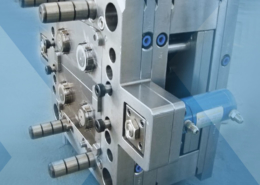
Short carbon fiber compounds expand reach of thermoplastic composites - aerospac
Author:gly Date: 2024-09-30
Get weekly and/or daily updates delivered to your inbox. You can unsubscribe at any time and we'll never share your details to third parties.
Guo and his colleagues started by milling their template for a microfluidic channel 100 micrometers in depth and 100 micrometers in width on a special aluminum alloy. The channel was 100 millimeters in length and included two fluid inlets, one fluid outlet and a serpentine channel as reaction chamber. They then polished this template using a method known as magnetic field-assisted finishing. Two magnetic rollers rotating in opposite directions on either side of the mold create a magnetic field. This field controlled a magnetic abrasive made of carbonyl iron powder and alumina particles bound together by oil, which removed any unwanted material and smoothed the surface.
Asia-Pacific's injection molding machines market share will grow at a CAGR of 6.3% during the forecast period. Due to the region's expanding demand for injection-molded plastics, it is projected that China, India, and Indonesia will contribute to expanding the Asia-Pacific injection molding machine market. This is due to the expansion of the packaging industry. In addition, significant companies such as NISSEI Plastic Industrial Co. Ltd. and Japan Steel Works Ltd. are employing various strategies, such as cooperation, acquisition, and others, to accelerate the expansion of the market.
The researchers compared their template before and after this magnetic polish. They observed that the process preserved the height of the microstructure, although the edges were more rounded after polishing. The polish reduced the roughness of the surface by a factor of four, leaving a mirror-like finish. "The next step will be to use the polished mold template for actual injection molding," says Guo.
Straits Research is a market intelligence company providing global business information reports and services. Our exclusive blend of quantitative forecasting and trends analysis provides forward-looking insight for thousands of decision-makers. Straits Research Pvt. Ltd. provides actionable market research data, especially designed and presented for decision making and ROI.
Use this form if you have come across a typo, inaccuracy or would like to send an edit request for the content on this page. For general inquiries, please use our contact form. For general feedback, use the public comments section below (please adhere to guidelines).
According to Straits Research, “The global injection molding machines market size had a market share of USD 10,724 million in 2021, expected to advance to USD 16,964 million with a CAGR of 5.9% during the forecast period.” Injection molding is an automated process in which an automatic tool operates efficiently on an injection molding machine. Machines and robots perform the majority of injection molding. These persons are solely accountable for overseeing and managing the process. This automation reduces the labor costs of the process. This drop in labor expenditure is predicted to reduce the cost of manufacturing plastic components. In addition, injection molding can make many identical components every hour.
Injection molding enables large-scale production of polymer and plastic materials with micrometer-sized features. Now, A*STAR scientists have developed a method for creating mold templates with high precision and few defects.
Increasing production rates and rapid injection molding output are predicted to boost global injection molding machines market growth. In addition, injection molding allows for producing plastic components with various finishes, including light texture, medium texture, pad printed, smooth, and screen printed. Consequently, it is projected that cheap labor costs and mass manufacturing associated with injection molding machines will promote market growth.
These microfluidic systems are small and portable, easy to use without expert knowledge, and disposable because they are cheap to produce. But this disposability means that microfluidic chips need to be quickly mass produced.
A vital characteristic of the injection-molding process is its capacity to use many types of plastic to make plastic things simultaneously. Manufacturers may use thermoplastics, thermosetting, or a combination of elastomers in injection molding to get the needed properties. This technique allows for producing more complicated objects with various forms and motifs. In addition, once the mold is prepared, the manufacturer can adjust the component's material and color. This factor is projected to drive the global market for injection molding machines. In addition, injection molding helps to reduce manufacturing waste. The majority of polymers produced by injection molding are recyclable.
Europe will hold the second largest market share and is expected to grow at a CAGR of 4.9% during the forecast period. Due to their high quality and energy efficiency, there has been a surge in the usage of all-electric injection molding machines in Europe. In addition, major market participants are spending considerable effort to deliver injection molding machines that fulfill the requirements of their clients by supplying customized and machine-type-based machines. Europe's economic expansion has led to a larger consumer market, indirectly benefiting the injection-molded plastics industry. In addition, the growth of the packaging, automotive, and electrical appliance industries is expected to increase the need for injection-molded plastics, boosting the market for injection molding equipment in Europe.
New York, United States, March 12, 2024 (GLOBE NEWSWIRE) -- Injection molding is a mechanism that allows for the mass production of components. It operates by injecting molten materials into a mold. It is typically employed in mass production to manufacture thousands of similar things. Components produced by injection molding include metals, glassware, elastomers, and confections. Although thermoplastic and thermosetting polymers are the most common, other polymers exist. The real benefit of injection molding is its mass manufacturing capability. After initial costs are accounted for, the unit cost of injection-molded items is extraordinarily cheap. The ingredients, such as synthetic resins (plastics), are heated and melted before they are put into the mold and cooled to form the desired shape. This process is referred to as injection molding because it resembles the injection of fluids using a syringe. Materials are melted and poured into the mold, where they solidify before being removed and completed.
Advantage of Low Labour Cost and Mass Production Along with Material Flexibility and Low Production Waste to Drive the Global Injection Moulding Machines Market
Whether you are looking at business sectors in the next town or crosswise over continents, we understand the significance of being acquainted with the client’s purchase. We overcome our clients’ issues by recognizing and deciphering the target group and generating leads with utmost precision. We seek to collaborate with our clients to deliver a broad spectrum of results through a blend of market and business research approaches.
March 12, 2024 10:35 ET | Source: Straits Research Private Limited - Reed Intelligence Straits Research Private Limited - Reed Intelligence
We keep our content available to everyone. Consider supporting Science X's mission by getting a premium account.
Injection molding involves shaping a material while in a molten state using a metal template. It is cheap, fast, and useful for creating microfluidic chips. However, engineering a mold with precise micrometer-scale features and smooth surfaces is challenging as burrs and tool marks create defects. A post-polishing process can fix some of these imperfections, but it is difficult for polishing tools to access the recessed corners of microstructured surfaces and remove unwanted material uniformly.
Utilizing injection molding machinery permits the actual mass production of injection-molded plastic components. The injection molding machine is the most effective and energy-efficient way of mass-producing plastic products. The rise of the global injection molding machines market is propelled by the multiple qualities of injection molding machines, such as their durability, user-friendliness, higher manufacturing rates and rapid production, and high quality. Rapidly increasing industrial investment and robust demand for injection-molded polymers in the automotive and healthcare industries are driving the expansion of the global injection molding machine market. In addition, industry leaders' manufacturing of energy-efficient, fully automated injection molding equipment stimulates the expansion of the injection molding market. Market participants provide injection molding machines in numerous sizes and designs to meet customers' needs.
More information: Jiang Guo et al. Magnetic field-assisted finishing of a mold insert with curved microstructures for injection molding of microfluidic chips, Tribology International (2017). DOI: 10.1016/j.triboint.2017.04.019
A fluid behaves very differently when it is confined to micrometer-scale channels. This phenomenon already has several applications such as enabling the analysis of small samples of blood.
Your email address is used only to let the recipient know who sent the email. Neither your address nor the recipient's address will be used for any other purpose. The information you enter will appear in your e-mail message and is not retained by Phys.org in any form.
Now, Jiang Guo and his colleagues from the A*STAR Singapore Institute of Manufacturing Technology have developed a method for fabricating molds that can quickly create microfluidic channels in polymer substrates. "The technology addresses a critical problem in mold insert fabrication for microfluidic chip production, and will enhance local industry," says Guo.
GETTING A QUOTE WITH LK-MOULD IS FREE AND SIMPLE.
FIND MORE OF OUR SERVICES:
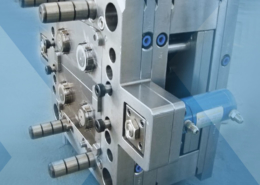
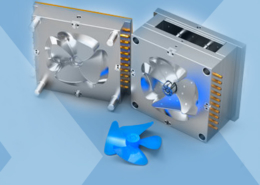
Plastic Molding

Rapid Prototyping
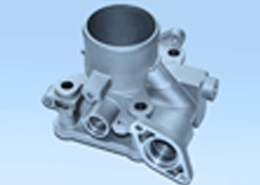
Pressure Die Casting
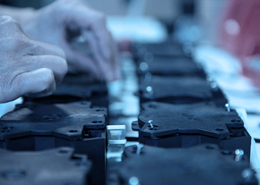
Parts Assembly
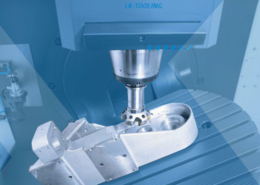