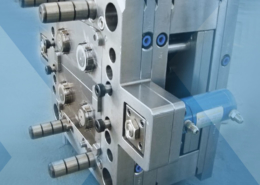
Shin Etsu Silicones of America Open House: Liquid Injection Moulding
Author:gly Date: 2024-09-30
Although not a prerequisite for the automotive and packaging sector, validation can be good business practice for a large number of mass manufacturers of injection-moulded components. Think of it as a long-term investment. Essentially, it’s a risk assessment which, when executed professionally, can deliver efficiency gains and save your business time, money and resources by ensuring product integrity and reducing scrap volumes.
Major repairs, changes, or improvements to the mould tool may require changes in the set up, and this would mean re-validating the process. This is also true of the moulding machines. Significant repairs or machine exchanges if not carefully managed and controlled may trigger a full validation of the process, which takes time and costs the moulder more money.
In accordance with ISO 13485 standards, ongoing documentation of the injection moulding process needs to be maintained. This is a continuous process, which is a significant change under the new directive. From time to time, machine settings may have to be adjusted to compensate for changes in the environment or to address moulding issues, such as pulling, distortion, or aesthetic defects. The key areas that might impact a stable process include changes in pressure, temperature, flow rate and cooling rates, any of which may trigger a re-validation exercise.
When it comes to product quality in injection moulding, machine and tool validation is fundamental to creating a stable manufacturing process and de-risking the project. Yet, it’s often bureaucracy rather than methodology that drives companies to validate. James Hines, Process and Training Engineer at Sumitomo (SHI) Demag goes back to the basics of why we validate and why this complex process shouldn’t be just regarded as a tick-box exercise to get the FDA or other regulatory bodies off your back.
Last year the European Commission issued its first update since 2001, causing more confusion. The new version of Annex 15 now requires manufacturers to ensure that “critical aspects” of their operation are validated throughout the product lifecycle. This includes any changes that could impact a product’s quality. Effective 1st October 2015, the amendment to EurdraLex Volume 4, Annex 15: Qualification and Validation closely mirror the FDA’s (U.S. Food and Drug Administration) lifecycle approach. There’s also a greater emphasis on risk management to reflect today’s manufacturing and regulatory environment. So, how do these changes impact manufacturers?
The validation process requires a step-by-step approach, working with each customer to break down each element of each injection moulding cycle and documenting every stage. Conducted by an engineer, the actual validation usually takes longer than actually building the tool itself. For this reason, the validation is often partially completed at the toolmakers’ facility by a senior engineer from the company as this allows issues to be addressed there and then on site, rather than shipping the tool back and forth. Ultimately, the final phases of the validation will be completed in-house on the specified equipment.
What happens when you combine a vending machine with plastic injection molding and add in a pinch of mid-century flair? You get a Mold-A-Rama machine. If you’re not a Midwesterner, then you might not know what I am talking about. But for those of us who grew up in Illinois, Minnesota, Michigan, or Wisconsin, Mold-A-Rama holds a special place in our nostalgic hearts. Every time I went to the Brookfield Zoo or the Field Museum of Natural History, I would drag my parents to the closest machine and beg them to buy me a tiny plastic statue. The real magic, however, was in watching the figurine being created right in front of our eyes in less than one minute. This became many kids’ first introduction to manufacturing.
From a business perspective, validation will also address profit-driven challenges and design out production weaknesses. Functional tests can help operatives better understand what drives the machine, how fast it goes and the consequences if manufacturing procedures are not correctly followed. In some instances, ramping up to a faster cycle time won’t always be the most optimised process.
Going back to the basics of why validation exists, it’s to ensure that injection moulders have a stable and dimensionally centred process that consistently produces high quality products. Validation is basically providing the scientific evidence that the machine and tool is repeatedly doing everything you expect it to do, every minute of every day.
At the Process Design stage you are looking to see if you have the proper sized machine - shot size and tonnage - and that the equipment is properly calibrated.
During the Process Qualification phase, you will move on to establish the range of process parameters. This involves conducting a selection of statistical and dimensional studies, enabling you to identify and investigate any deviations in the process. A process is not considered as validated if the variations have negatively impacted the finished product in any way.
The Mold-A-Rama machine was invented by J.H. “Tike” Miller and debuted at the 1962 Seattle World’s Fair. The initial batch of models included a monorail, a Buddha, and a 3D sculpture of the Fair’s logo. The 1964 World’s Fair in New York City, however, made Mold-A-Rama a household name. It is said that as many as 150 machines were installed over the Fair’s two-year timeframe, and models included various dinosaurs, Disney characters, animals, and presidential busts. After being featured at the Montreal World’s Fair, Expo ’67, Mold-A-Rama machines became staples at museums, zoos, amusement parks, and anywhere that sold souvenirs.
The mid-century machines remain popular to this day. According to the current owner, one in 10 people who pass a machine buy a model, and the company uses about 640 55-pound bags of plastic pellets a year. Each Mold-A-Rama machine hold a gallon of hot liquid plastic and can produce up to 150 figures a day.
The final validation phase - Continued Process Verification - focuses on demonstrating that your process is consistently stable. It involves simulating different production runs using the same production equipment and the processes that you will be routinely using, ensuring repeatability of the set-up conditions throughout the machine’s full lifecycle.
If you’re looking to experience the magic of a Mold-A-Rama (or its cousin, the Mold-A-Matic) for yourself, here is a list of 10 locations where you can see these marvelous machines in action. If you happen to be in the Chicagoland area, take a trip to the Museum of Science and Industry and check out their latest exhibit, Mold-A-Rama: Molded for the Future.
Here's how it works. First, insert your money into the machine. (Back in my day, each statue cost $1. The current price per figurine is $5. Thanks, inflation.) Next, two thick aluminum plates are pushed together, creating the mold. Polyethylene pellets, heated up to approximately 250°F, are then injected into the mold, while a blast of air works to hollow out the piece. Unnecessary plastic is removed through a drainage hole in the bottom of the mold. The statue is then cooled and hardened before the plates pull apart and the piece is pushed into the pick-up box.
Alexis Gajewski has over 15 years of experience in the maintenance, reliability, operations, and manufacturing space. She joined Plant Services in 2008 and works to bring readers the news, insight, and information they need to make the right decisions for their plants. Alexis also authors “The Lighter Side of Manufacturing,” a blog that highlights the fun and innovative advances in the industrial sector.
Before you start validating, it is vital to be clear on your expectations. If it’s to provide a documented source of evidence to satisfy a regulatory body, you need to do it. But that shouldn’t be your sole motivation. Validation is not purely about procedures and scrambling to put the correct documentation in place. The objective of having an efficient process and repeatable high product quality should never be overlooked, as this is ultimately how you can avoid costly product recalls and cosmetic product defects.
Like before, there are three key phases to process validation, only now the FDA categorises them as Process Design, Process Qualification, and Continued Process Verification. These reflect the focus on the manufacturing lifecycle and the need to provide scientifically sound data to verify that your injection moulding processes start and continue to remain stable.
For any plastics manufacturer, zero defects remain the target. In the medical industry, for example, there’s no wiggle room. You can’t shift the parameters to suit. If you’re producing a medical device or a sterile implant, nothing less than 100 percent quality is acceptable.
GETTING A QUOTE WITH LK-MOULD IS FREE AND SIMPLE.
FIND MORE OF OUR SERVICES:
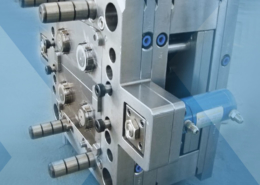
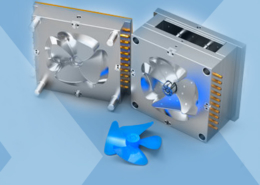
Plastic Molding

Rapid Prototyping
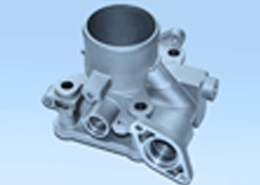
Pressure Die Casting
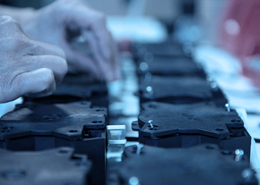
Parts Assembly
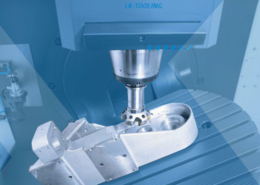