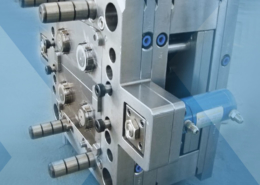
Plastic Injection Mold Tooling: Revolutionizing Manufacturing
Author:gly Date: 2024-06-08
Plastic injection mold tooling stands as a cornerstone of modern manufacturing, driving innovation and efficiency across various industries. From automotive components to household goods, its significance reverberates through every aspect of our daily lives. In this comprehensive exploration, we delve into the intricacies of plastic injection mold tooling, unraveling its processes, applications, and impact on the industrial landscape.
Understanding Plastic Injection Mold Tooling
Plastic injection mold tooling is the process of creating molds or tools used in the injection molding process, where molten plastic is injected into a mold cavity to produce a desired product shape. It encompasses a range of techniques, including mold design, material selection, and tool fabrication. This intricate process demands precision engineering and meticulous attention to detail to ensure the production of high-quality plastic parts.
Evolution of Plastic Injection Mold Tooling
The history of plastic injection mold tooling traces back to the mid-20th century, with the development of the first injection molding machines. Since then, advancements in materials, design software, and manufacturing technologies have propelled the evolution of mold tooling. From simple single-cavity molds to complex multi-cavity molds with intricate geometries, the capabilities of plastic injection mold tooling have expanded exponentially, catering to diverse industry needs.
Key Components and Materials
Plastic injection mold tooling comprises several essential components, including the mold base, cavity, and core. These components are typically constructed from high-strength materials such as steel or aluminum, chosen for their durability and thermal conductivity. The selection of materials is crucial in ensuring the longevity and performance of the mold tooling, as it directly impacts factors such as mold life, cycle time, and part quality.
Process Optimization and Efficiency
Optimizing the plastic injection mold tooling process is essential for maximizing efficiency and minimizing production costs. Advanced simulation software allows engineers to analyze mold flow, cooling, and ejector systems, enabling the identification of potential issues and the implementation of design improvements before production begins. Additionally, innovations such as hot runner systems and in-mold labeling further enhance process efficiency, reducing cycle times and waste while increasing productivity.
Applications Across Industries
Plastic injection mold tooling finds widespread applications across various industries, ranging from automotive and aerospace to consumer electronics and medical devices. In the automotive sector, mold tooling is utilized in the production of interior and exterior components, including dashboards, bumpers, and door panels. Similarly, in the medical field, precision mold tooling is crucial for manufacturing devices such as syringes, IV catheters, and surgical instruments, where quality and consistency are paramount.
Challenges and Future Outlook
Despite its numerous benefits, plastic injection mold tooling faces challenges such as rising material costs, environmental concerns, and the need for continuous innovation. Addressing these challenges requires a concerted effort from manufacturers, engineers, and policymakers to develop sustainable solutions and embrace emerging technologies. Looking ahead, the future of plastic injection mold tooling lies in advanced materials, additive manufacturing techniques, and digitalization, promising further enhancements in efficiency, flexibility, and sustainability.
Conclusion
In conclusion, plastic injection mold tooling stands at the forefront of modern manufacturing, driving innovation, efficiency, and versatility across diverse industries. From its humble origins to its current state of technological sophistication, mold tooling continues to reshape the way we design, produce, and consume plastic products. As we navigate the challenges and opportunities of the 21st century, embracing sustainable practices and embracing emerging technologies will be key to unlocking the full potential of plastic injection mold tooling and ensuring a brighter, more sustainable future for generations to come.
GETTING A QUOTE WITH LK-MOULD IS FREE AND SIMPLE.
FIND MORE OF OUR SERVICES:
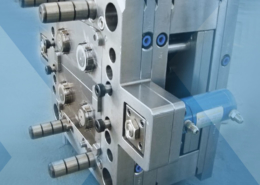
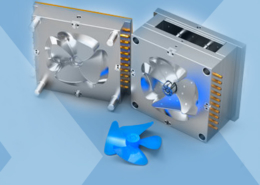
Plastic Molding

Rapid Prototyping
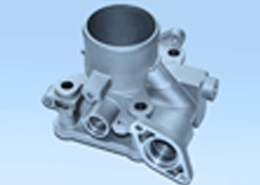
Pressure Die Casting
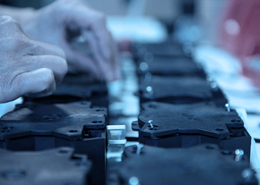
Parts Assembly
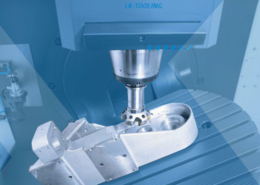