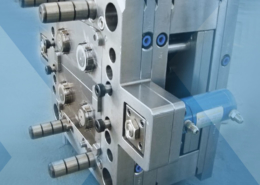
Sabic Debuts PP Compounds for Foam Injection Molding - foam injection molding co
Author:gly Date: 2024-09-30
The combi M's horizontal indexing table technology saves valuable floor space, especially where multiple-cavity moulds are used. A comparable 32-cavity mould with a vertical rotary table would require a larger e-motion injection moulding machine with at least 280 tonnes clamp force. In this application, the horizontal indexing table technology reduces the injection moulding machine's footprint by more than 20 per cent.
The primary parts with cylindrical cavities are injected using a PC material dyed in black. The indexing table then rotates 180 degrees to seal the cylinders with transparent PC on one side with lenticular covers in a second injection moulding step. Simultraneously, the next set of primary parts will be produced on the other side. The two moulds, with 32 cavities each, come from Hack Formenbau in Kirchheim unter Teck, Germany.
The strong position of the automotive sector is a major factor driving the micro injection molding machine market. Electric vehicles are composed of various electronic parts such as all electric auxiliary, electric traction motor, traction battery pack, electric transmission, power electronics controller, and DC converter among others. These small electronics parts are composed of various micro components that are critical during vehicle manufacture and assembly. These are very small and complex components.
The shift towards nanotechnology in every sector including medical, automotive, fiber optics, electronics and others is increasing the necessity of smaller high-precision parts.
ENGEL is introducing a new member of the iQ product family at K 2022. The new smart assistant for nominal values goes by the name of iQ hold control and automatically determines the optimum holding pressure time to help process technicians achieve massive time savings.
The holding pressure time is one of the quality-driving parameters in the injection moulding process. This is why it is individually configured after mould set-up and typically determined empirically. Determining what is known as the sealing point not only takes a lot of time, it also consumes a lot of raw material since several parts first need to be moulded and analysed in the quality control lab. The new holding pressure assistant by ENGEL removes the need for production personnel to make this effort, saving both time and raw materials.
Asia Pacific (APAC) is projected to be the fastest-growing region for the micro injection molding machine market during the forecast period, with China is the largest market by country. Increasing domestic demand due to the rapid increase in manufacturing facilities and other commercial units is expected to continue driving the demand for micro injection molding machine in the region. Increasing population and demand, accompanied by initiatives for new technologies and products, are projected to make this region a promising micro injection molding machine market. The growing population will have a significant impact on automotive and electronics industry in the region.
Micro injection molding machines are machines used for the manufacture of plastics components for shot weights of 1 to 0.1 grams with tolerances in the range of 10 to 100 microns. This molding process permits the manufacture of complicated small geometries with maximum possible accuracy and precision.
As a system solution provider, ENGEL looks to ensure in the scope of process digitalisation that the control units of external systems, such as the mould or peripheral units, can be integrated with the central CC300 control panel on the injection moulding machine. For example, the HACK moldlife sense software is integrated with the CC300 machine control unit with the help of Webviewer technology. HACK moldlife sense detects errors and irregularities in the mould and automatically notifies the machine operator before rejects and high costs occur.
Micro molding produces a component or part that is: micro in size, micro in features, micro in tolerances. However, the basic concept of the micro injection molding process is akin to a standard injection molding process; the micro injection unit is simply integrated into the injection molding machine.
The micro injection molding machine market is projected to reach $609 million by 2026 from $381 million in 2021 at a 9.8% CAGR.
The basis for automatically calculating the holding pressure time is mould breathing on the one hand, and the plasticising screw position on the other. iQ hold control analyses both process values and suggests the optimum holding pressure time via the CC300 injection moulding machine control after just a few cycles. Once the set-up technician has confirmed the value, production can immediately begin.
The Micro Injection Molding Machine Market is projected to reach $609 million by 2026, at a CAGR of 9.8% from $381 million in 2021, according to a report published by MarketsandMarkets.
Because the growing electric vehicle market requires more micro injection molded products than a standard internal combustion (ICE) vehicle, the increased electric demand should positively impact market growth.
An ENGEL viper 20 linear robot will be removing the two-component parts and depositing them in trays. Finally, an ENGEL e pic pick-and-place robot is covering the fully populated trays with an intermediate layer to be able to stack them in boxes and then discharge them via a tray server, which is also integrated.
ENGEL will also establish its new records in plant footprint and energy consumption at K 2022, where a minimal footprint, all-electric, high-performance e-motion 160 combi M injection moulding machine will make its debut and produce sample vessels for medical diagnostics in two-component injection moulding under cleanroom conditions.
Visitors to the K show 2022 can experience the new iQ hold control in action at the ENGEL booth, where connectors for vehicle electronics will be produced on an all-electric e-mac injection moulding machine. The smart assistance systems can be activated and deactivated individually to allow visitors to the show to experience the feature live.
The demand for micro molded plastic parts in automotive, electronics and medical application is driving the demand for micro injection molding machine with clamping force 30 to 40 tons. However, micro injection molding machine with clamping force 0 to 10 tons is expected to grow at the highest CAGR during the forecast period.
The holding pressure time is determined objectively, meaning that even less experienced process technicians can adjust the process parameters at the push of a button in case of a batch change. Further efficiency gains can result from the automatically determined optimum holding pressure time being lower than the holding pressure time set initially. In these cases, the cycle time is reduced. And the energy requirement decreases.
ENGEL is offering all iQ systems, including the new iQ hold control, as trial versions with immediate effect. Various packages are available, including – for example – webinars and in-house training, process engineering consultancy and tests at the ENGEL technology centre.
GETTING A QUOTE WITH LK-MOULD IS FREE AND SIMPLE.
FIND MORE OF OUR SERVICES:
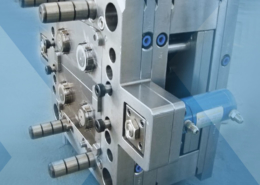
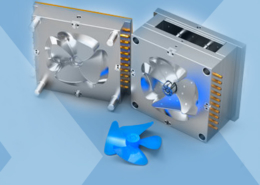
Plastic Molding

Rapid Prototyping
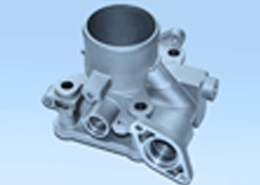
Pressure Die Casting
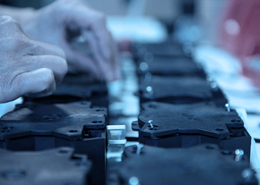
Parts Assembly
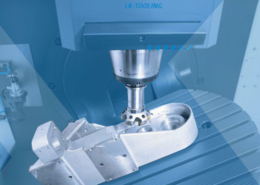