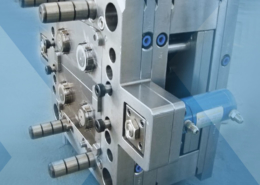
Revised safety standard for injection molding machinery published - plastic inje
Author:gly Date: 2024-09-30
(Left to right) - Peter Giessmann (KraussMaffei), Eric Jan Frijters (Techniplas), Philipp Strasser (KraussMaffei), Michael Fuchs (KraussMaffei), Rene Rudolf (Techniplas), Sarah Seidel (Techniplas)
Dailey commented: “Mack has always been a tremendous regional partner and an integral supporter of the health system for many years.
The ColorForm process effectively works by combining injection moulding and polyurethane processing. The multi-component injection moulding procedure is the foundation of this process. After injection moulding of the thermoplastic mould base body, the body is flow-coated with polyurethane (PUR) or polyurea (PUA) as the surface material in a second cycle.
The MXW 1000 was not just retrofitted for ColorForm technology. Its control system was also completely upgraded to KraussMaffei’s MC6 control system, and a new ORCA cooling system was installed. "The system performs a contact-free temperature measurement, which minimises maintenance. The technology allows us to control the twenty cooling circuits of the MXW precisely and thus makes a critical contribution to the high, uniform quality of the components," explained Luckner.
Shiela Boni, a nursing director and PPE officer for SVHC added: “Our priority is to ensure the safety of our staff while caring for patients during the pandemic.
The RimStar Flex ColorForm reaction process machine, which was designed specifically for this process, and the mixing head, feed the surface material (PUR/PUA) directly into the cavity. “RimStar systems take up very little space and meter even small amounts precisely and at a high cycle frequency,” said Philipp Strasser, global application owner, RPM and automotive at KraussMaffei.
Before being assigned a mask, each SVHC staff member is “fit tested” to ensure an adequate seal. Each employee also receives cleaning and storage guidelines with instructions on how to disinfect and store the masks after each shift. Additionally, before each use, staff conduct a positive and negative pressure test to ensure the masks are holding up for their protection. The fact that the air intake is above the wearer’s head improves the line of site and allows patients to see their physicians’ and nurses’ faces more clearly.
“Our ColorForm system is used to produce parts using the injection compression moulding process, which are given a high-quality, transparent PUR surface for a special depth effect. Another line for the project is currently being commissioned,” said Luckner.
"Our gratitude for the hardworking teams at Mack and Synectic, who put many long hours into this project, cannot be overstated. This is another wonderful example of Mack’s continued support of SVHC.”
Jeff Somple, president at Mack headquarters in nearby Arlington, VT said: “When I informed Synectic’s team about this project, they were ready and excited for the challenge.
“We produce under cleanroom conditions in the process. Thus, when the mould is open, no grain of dust can get between the coating and the substrate surface. We thus achieve very low reject rates,” Luckner said.
"There, all necessary equipment is available on-site, and commissioning at the TechCenter was also completed on schedule – both for the injection moulding machine and for the PUR technology, that is, for the RimStar Flex with two MK 5-2K CCM mixing heads for simultaneous production of two components. This cannot be taken for granted under the current basic conditions determined by the pandemic," says Luckner.
ColorForm is KraussMaffei’s combination of injection moulding technology and surface finishing with polyurethane in a single step. The technology is designed to make large-scale production of high-quality components more economical and sustainable.
Using ColorForm tech means Techniplas doesn’t need to transport and paint components, or invest in a painting plant. The finished components are also ready for installation when they’re discharged from the automated production cell, saving on buffer storage and drying.
Adam Lehman, president of Mack’s Woodbridge, Conn., subsidiary, Synectic, worked quickly to identify available options that could be redesigned to function as a respirator, and Lehman located a snorkelling mask that the Synectic design team could quickly re-engineer into PPE.
Following two weeks of design, testing, and manufacturing, Mack’s team at Synectic fabricated an attachment to a snorkelling scuba mask. The mask covers the entire face and removes the need for disposable masks and shields. To create the masks, Mack’s engineers removed the part that usually protrudes out of the water when snorkelling, and replaced it with a new, custom-designed branched component equipped with cartridges containing P100 HEPA filters.
Techniplas has used the ColorForm process for several years – although the manufacturer refers to it as “ColorFuse” technology. There are four ColorForm systems in Treuen and one in Rüti, Switzerland. An in-house technical center in Treuen also uses two further systems.
Together, Mack and SVHC began investigating alternative mask options that could be modified due to the high demand for N95s masks and 7700 respirators.
“Our customers, major OEMs from the automotive industry, place the highest demands on quality. There must be no defects larger than 0.2mm on the entire transparent component. With the MXW 1000 in combination with the RimStar Flex for PUR metering, we fully meet these requirements,” added Toni Luckner, process developer at Techniplas in Treuen.
Thomas A. Dee, SVHC’s president and CEO, concluded: “This is a great example of how collaboration and innovation sustain us during challenging times.
The collaboration arose because Kevin Dailey, the vice president of administration/CHRO at SVHC had led human resources at Mack until five years ago. Dailey called Mack to help with the PPE.
“As an essential manufacturer of healthcare products, I knew that they would want to help and came through with a brilliant solution for us.”
Unlike medically approved respirators, the scuba mask has been adapted to meet the filtration requirements of PPE. The risk assessment conducted by Mack’s design and SVHC showed that the mask fully seals around the face with silicone - reducing skin breakdown, and the N100 HEPA filters have a higher rate of filtration than the material in the traditional N95 masks. Less than three weeks after the initial request to Mack, its subsidiary Synectic delivered 500 scuba masks and 2,000 N100 HEPA filter casings to the hospital.
A new system has recently been put into operation, for which Techniplas used an existing MXW 1000 injection moulding machine from KraussMaffei as the basis. Techniplas had the MXW retrofitted at its manufacturer's main factory in Munich's Allach neighborhood.
"ColorForm technology offers great potential for a lower CO₂ footprint in the production of components with a noble, multifunctional surface," said Michael Fuchs, global application owner surface and lightweight at KraussMaffei. By consolidating the process down into one step, the user saves time and resource on intermediate storage, painting, and reworking of components. By using a transparent polyurethane surface treatment, Techniplas can also achieve ‘depth effects’ on the final component. The company uses the MXW 1000 ColorForm system at its Treuen, Saxony site.
“It was an opportunity for some ground-breaking innovation and to make a meaningful difference for our region’s front line healthcare workers.”
GETTING A QUOTE WITH LK-MOULD IS FREE AND SIMPLE.
FIND MORE OF OUR SERVICES:
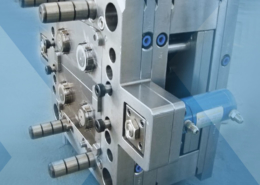
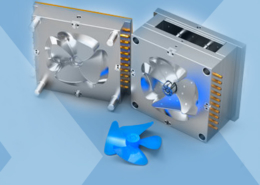
Plastic Molding

Rapid Prototyping
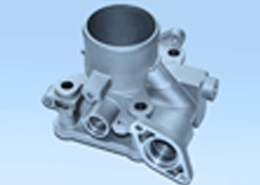
Pressure Die Casting
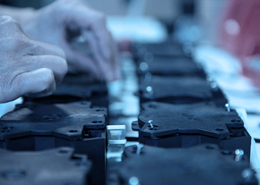
Parts Assembly
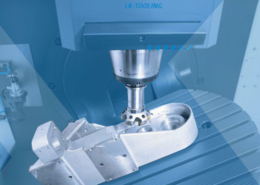