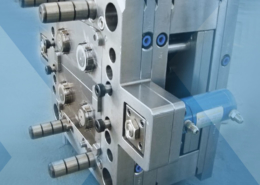
Researchers develop ice cube that doesn't melt or grow mold - heat plastic to mo
Author:gly Date: 2024-09-30
“Silcotech’s business has seen growth in the 15% to 20% per year range over the past two years and the outlook is to keep that pace that in FY2024 and beyond,” said Morris.
“Twenty-five years ago, we set out to become a global leader of liquid silicone moulded parts. Having spent 17 years in a technical capacity with a world-renowned moulding machine manufacturer, injection moulding machines were part of my DNA,” he said.
Silcotech North America, a specialist in Liquid Silicone Rubber (LSR) injection moulding, has announced its expanding capacity with the purchase of two new injection moulding machine workcells.
The patented FIM process uses high-speed Nexa3D printers and xMOLD resin to print injection molding tools that are compatible with thousands of off-the-shelf injection molding materials, including reinforced high-performance feedstocks. The process reduces design, iteration, and validation cycles using end-product materials to a matter of hours rather than weeks.
“At that time there were only two significant players offering LIM options for their moulding machines – Arburg was one of them.”
SPT implemented Nexa3D’s Freeform Injection Molding (FIM) technology to help customers shorten time-to-market on complex medical devices in demanding medical-grade materials and to expand on the range of materials that can be quickly and reliably used in prototyping and early device test manufacturing.
Injection-molded silicone parts were produced within two days, allowing early verification of key design and performance aspects.
He continued, “Our decision to move forward with Arburg was clearly based on our history of success using their machines. Their machines feature a sound mechanical design coupled with a very progressive control system.”
Medical device manufacturers are tasked with developing elaborate test protocols to ensure that the product in development is safe and meets essential requirements. If these tests are conducted late in the development process, the more onerous and risky they become. SPT Vilecon often works with silicone, a material that is extensively used in medical applications because of its chemical resistance, mechanical performance, and biocompatibility. However, silicone parts are notoriously difficult to prototype and test, since most grades need to be injection molded to achieve their full performance potential, said the company. FIM enabled SPT Vilecon to offer an alternative to a customer developing an intravenous (IV) silicone product — the use of 3D-printed tooling to perform early design and material verification at a fraction of the cost of conventional methods.
The 3D-printed molds for the first and second iterations cost less than €2,000 combined. And the technology enabled a two-day design cycle, which is more than 90% faster than conventional metal tooling.
Certified to ISO 13485, Denmark-based SPT Vilecon describes itself as a fully integrated provider of development and manufacturing services to the medical device industry. It offers in-house tool making and injection molding along with other manufacturing services to companies in northern Europe.
Isolde Boettger, vice president and co-founder of Silcotech North America, said, “Michael’s technical experience, coupled with Arburg’s very solid and proven technology developments in LSR moulding technology, were superior when we made the decision to purchase our first two Arburg machines in 1998 when we started Silcotech North America. Looking back on our decision and evaluating the technology on a regular basis, it is clear Arburg was, and continues to be, the right decision for the competitive LSR space.”
Michael Maloney, Silcotech president, said that Arburg was chosen as the supplier of the new machines because of their long history of success providing machines for LSR applications.
Based on input collected from the first two iterations, the design of the silicone part was approved and manufacturing of a metal tool was initiated with full confidence of part moldability and performance. The in-house tool shop built the final metal tooling in four weeks without iterations.
Editor in chief of PlasticsToday since 2015, Norbert Sparrow has more than 30 years of editorial experience in business-to-business media. He studied journalism at the Centre Universitaire d'Etudes du Journalisme in Strasbourg, France, where he earned a master's degree.
SPT Vilecon said it has begun expanding the range of injection mold prototyping with silicone, metal, and ceramic materials to provide medical device manufacturers with an even wider selection of product development and verification services.
Robust and valid prototyping and verification are key to minimizing cost, time, and risk factors in developing medical devices, said SPI Vilecon. FIM is a new toolbox for medical device companies seeking to accelerate their innovation and obtain early verification of part performance and moldability, added the company.
A supplier of development and manufacturing services to medical device OEMs used Freeform Injection Molding from Nexa3D to accelerate time-to-market and slash prototyping costs for a complex silicone-based IV device. SPT Vilecon explained the process in a recent press release.
Freeform Injection Molding technology from Nexa3D compresses design, iteration, and validation cycle times into a matter of hours rather than weeks.
The two new Arburg machines include a 110 US ton ALLROUNDER 470 A 1000 - 290 Comfort, and a 220 US ton ALLROUNDER 570 A 2000 - 400 Comfort. Both are all-electric machines specified with LIM/LSR moulding options as well as thermoplastic moulding capabilities. They will both be equipped with MULTILIFT SELECT 8 servo electric robotics for parts removal and manipulation. Delivery is scheduled for summer 2024.
Design input collected from the first tests was integrated in a second iteration that took only a couple of hours to complete. By contrast, conventional metal tooling would have taken more than six weeks to design and procure, and the adjustments needed for the second iteration would have taken an in-house tool-shop a week to complete.
The new machines will be used to expand capacity at Silcotech's headquarters in Bolton, Ontario. They will be added to the existing fleet to handle growing business volume, and the new machines are sizes where increased capacity is needed, said Dan Morris, Business Development Manager at Silcotech.
GETTING A QUOTE WITH LK-MOULD IS FREE AND SIMPLE.
FIND MORE OF OUR SERVICES:
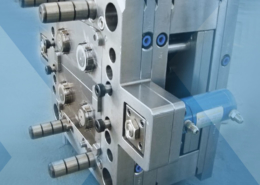
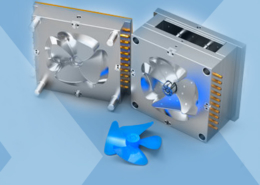
Plastic Molding

Rapid Prototyping
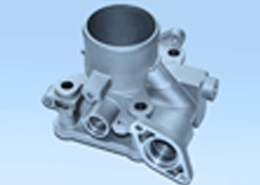
Pressure Die Casting
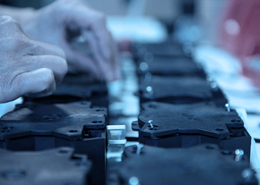
Parts Assembly
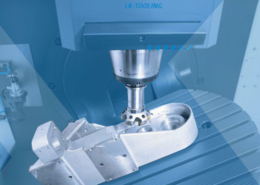