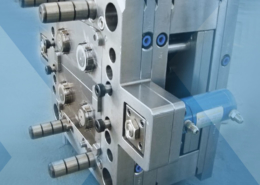
REPSOL: Healthcare polyolefins portfolio expanded / New grades of LDPE
Author:gly Date: 2024-09-30
SPEE3D participated in a U.S. Army Combat Capabilities Development Command (DEVCOM) Army Research Laboratory (ARL) demonstration. The demo took place at the University of Tennessee Knoxville and ran from the...
Plasteurope.com is a business information platform for the European plastics industry. It is part of KI Kunststoff Information and PIE Plastics Information Europe, one of the leading content providers for the European plastics industry. We offer daily updated business news and reports, in-depth market analysis, polymer prices and other services for the international plastics industry, including a suppliers guide, career opportunities, a trade name directory and videos.
“This method will create the possibility for creating micro features on real free-form surface on a new production platform meeting industrial demands,” the researchers state. “Therefore, this method has the potential to be applied and investigated for applications in connection with next generation medical devices that require micro features on complex shapes, for example in connection with medical devices or implanting devices. This method will facilitate value creation through significantly reduced expenses for small-to-medium volume series productions, and positively affect the timescale for production in the gap between 1 – 10 individual devices and real mass production. It will open up new high-value products and design solutions.”
3D printing is a great technology on its own, but it also lends itself well to complementing other manufacturing technologies, such as injection molding. In a paper entitled “A Soft Tooling Process Chain for Injection Molding of a 3D Component with Micro Pillars,” a group of researchers discusses using 3D printing to create injection molding inserts with micro surface features.
There are many ways of manufacturing micro pillars or features, the researchers explain, but most of them can only be applied on flat surfaces or on surfaces with constant curvature. In the paper, they describe how they created micro features on complex surfaces using what they call “a soft tooling process chain.” Steel mold cavities in the injection molding machine were replaced by a set of inserts produced using DLP 3D printing. This technology was able to achieve higher precision than metal additive manufacturing, and the machining time and cost was significantly reduced compared to conventional tooling processes based on CNC machining.
Additive manufacturing and injection molding have been combined before; more frequently, additive manufacturing is being used to manufacture the molds for injection molding. The advantages are many: it is cheaper, faster, and allows for easy production of molds for single or limited use. This paper shows another way that 3D printing can be used to enhance injection molding processes, offering a look at how manufacturing technologies are often better together than by themselves.
Authors of the paper include Yang Zhang, David Bue Pedersen, Michael Mischkot, Matteo Calaon, Federico Baruffi, and Guido Tosello.
Stay up-to-date on all the latest news from the 3D printing industry and receive information and offers from third party vendors.
“This process chain is suitable for products in intermediate scale (from 1000 – 10,000 cycles by injection molding or similar) production, but high variation in design,” the researchers state. “Moreover, for 3D printed inserts, no special mold plates are required. Standard commercial injection molding plates were purchased and machined to fit the inserts.”
© 2001-2024 Plasteurope.com | Imprint | Privacy | Cookie settings Plasteurope.com is a business information platform for the European plastics industry. It is part of KI Kunststoff Information and PIE Plastics Information Europe, one of the leading content providers for the European plastics industry. We offer daily updated business news and reports, in-depth market analysis, polymer prices and other services for the international plastics industry, including a suppliers guide, career opportunities, a trade name directory and videos. News | Polymer Prices | Material Databases | Plastics Exchange | Suppliers Guide | Jobs | Register | Advertising PIE – Plastics Information Europe | KI – Kunststoff Information | KunststoffWeb | Plastics Material Exchange | Polyglobe | K-Profi
The inserts were 3D printed and installed on an injection molding machine. With the inserts installed, the researchers then injection molded parts from PE material.
(a) Inserts produced by additive manufacturing process form the mold cavity; one polyethylene (PE) replica produced by injection molding is displayed. Markings on the reference ruler are millimeters; numbers mark centimeters. (b) Scanning electron microscope (SEM) image shows the surface of the insert; (c) SEM image shows the surface of the PE parts made by injection molding.
Register to view and download proprietary industry data from AM Research and 3DPrint.com Questions? Contact info@3dprint.com
There’s lots to choose from in this week’s 3D Printing Webinar and Event Roundup! Stratasys continues its North American tour, as well as its in-person training classes, and HP will...
Stay up-to-date on all the latest news from the 3D printing industry and receive information and offers from third party vendors.
In a major leadership shift, VulcanForms has appointed Kevin Kassekert as its new CEO and Jay Martin as President. This change comes at a crucial time as the company moves...
The surface quality of the injection molded parts produced with the 3D printed plates was limited, the researchers conclude, but post-processing methods such as chemical etching could be used to improve the surface quality. The precision of the surface features was also limited, they add; however, they did find additive manufacturing to be a time- and cost-effective way of producing injection molding inserts for parts with complex surfaces and micro features.
Amidst the backdrop of last week’s FAA/EASA workshop in Wichita, Bill Bihlman, Consultant and Volunteer to SAE, analyzes the state of AM aerospace standards. Commercial aviation is notoriously risk averse....
GETTING A QUOTE WITH LK-MOULD IS FREE AND SIMPLE.
FIND MORE OF OUR SERVICES:
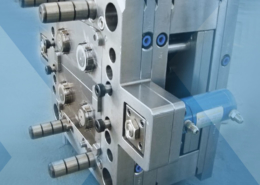
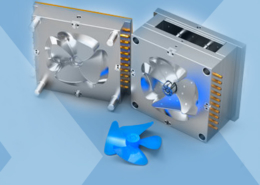
Plastic Molding

Rapid Prototyping
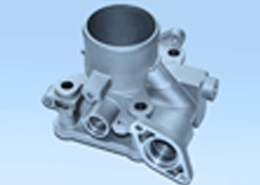
Pressure Die Casting
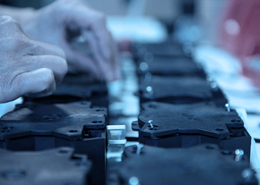
Parts Assembly
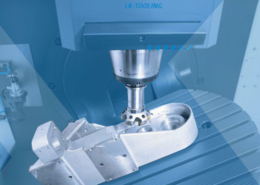