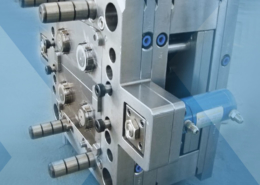
Repairing A Home Injection Molding Machine - pla molding
Author:gly Date: 2024-09-30
Generally the process starts with the part designer and from there, in succession, goes to the tool designer, the tool builder, the molder, and finally the parts get to the OEM, Carobus explained. “When the part is delivered and is failing in the field someone wants a simulation analysis. We don’t want to get involved at that point. We want to work with the part designer or the tool designer at the front end of the project because as you move up the ladder, the mold gets more expensive to fix. But, we seem to get involved at the back end about equally with the front end involvement.” OEMs requiring process flow in initial bidThat said, Carobus acknowledges that business has picked up considerably as some markets, such as the automotive industry, require process flow analysis and design validation prior to the mold build. “More advanced industries like the automotive will automatically include mold and material flow analysis in their design,” he noted. “Big companies tend to have this capability in-house, but some will depend on the mold maker to perform an analysis on the part design prior to cutting steel.”Often material suppliers will run a quick analysis to support the use of their material. “Does it really help the OEM or solve any problems?,” asked Carobus. “They might miss things. It’s not just running an analysis but knowing what you’re looking for—looking for real molding conditions and doing it right is what counts. Many companies own the software but don’t optimize the part design or tool design. They spend money then complain they didn’t get the information they needed. But are they using the tool correctly? Even with the stuff that’s easy to use can give you bad results.” Some OEMs depend upon the tool builder to run the analysis. Industrial Molds Group purchased the MoldEx 3D software from ESP Flotek several years ago, however due to a change in personnel, they lost some of the talent that knew how to use it. A few months ago, they re-evaluated the software and decided that it was a good tool, and that they weren’t using it the way it was meant to be used to provide benefits to both their customers and the company. They called in EPS Flotek and had the latest versions of MoldEx 3D installed and provided training to the engineering department. “Now we use MoldEx 3D to check the mold fill on every job before we cut steel,” said Kerry Smith, Industrial Molds’ Engineering Manager. “Filling the mold properly is the first consideration in the mold design and causes the most angst for our customers or their molders. The simulation allows us to look at the gate, the hot runner system and the venting. We look at hot spots and determine how to implement better cooling. It also has the ability to do warp analysis.”“The analysis tool should be used interactively – not behind the scenes in the closet,” commented Carobus. “The part designer, the tool designer, the moldbuilder, the molder and the customer should all work collaboratively. We want to build a tool as efficiently as possible, so we can tell you what happens if you reduce your cycle time by 2 seconds. The customer wants a tool that produces the best quality part, and it helps the moldmaker get them just that.” Old habits die hardOften it’s the life-long moldmaker who resists this type of software because they’ve been building molds for 40 years and think the software doesn’t know more than they do. “It’s not about the software knowing more but that the plastic process has so many variables that one little change in a rib, a gate location, a material can make a huge difference in the part quality, the cycle time savings and in profitability for their customer,” Carobus commented.Smith pointed out that some of the reluctance of smaller shops is the cost involved in purchasing a seat of mold-filling simulation software, which he acknowledges is not cheap. “They say ‘I can’t buy it because the customer won’t pay for it,’” he said. “But what does that mean? What is the cost of not running a mold-filling analysis? The customer will pay for it. He’ll pay for it with a bad tool that runs slower cycles or bad parts. The tool shop will pay for it by reworking a tool—often on their own dime—that doesn’t run right.”For smaller mold manufacturers that don’t have the resources for in-house simulation software or an analyst on staff, there are companies such as EPS Flotek that can perform a full range of engineering services for them using MoldEx 3D simulation software. EPS Flotek offers that service for them on a per-project basis for about $2500 to $3500.Moldex3D can predict the condition of the plastic parts during the molding process to help moldmakers understand how best to design the mold for optimum processability. The advantage to the mold designer and the moldbuilder is that simulation is a value added service. “The moldmaker can tell his customer, ‘We’re making sure you get the best tool and best part up front. We’ll fix anything that’s wrong after the mold is built but we don’t want to have to do that.’”Industrial Molds has realized the mutual benefits gained by both parties, noted Smith. “Performing the mold-fill simulation analysis saves us from doing an extra round of venting or reworking vents and runners,” he said. “On the customer side, they can see proof positive why their original idea for the design of the part, and the type of mold they thought they wanted, might not be the most optimum production mold for the part. Performing the mold fill analysis with the tool maker is the best path.”“In one instance, the customer wanted to use a three-plate mold. The part was captured by slides on all four sides so the runner system was very large. Early on in the design stage we did a quick runner system design to run a mold analysis. The analysis showed us there would be a tremendous amount of scrap, and the cycle time would be extended because of the distances the runners had to flow. We changed the basic mold configuration based on that problem, showed the customer why we needed to change the design, and got approval to change the mold design.”“We got the answer just a few days into the mold design rather than after we’d cut steel,” said Smith. “It was so meaningful for the customer to actually see the problems that would result from the three-plate mold design. It’s one thing to say to a customer ‘I think this is going to be a problem,’ but when you can show them the actual simulation that reveals the problem, that’s the real evidence—not speculation. And we did that in just a few days’ time rather than well into the design cycle.”“By not using mold analysis software, companies are losing out on unrealized profit and unrealized cost savings in design a mold that doesn’t perform optimally. Address the issues up front and everything becomes more efficient,” said Carobus. “It’s like an insurance policy. You don’t notice just how much you’ve saved until something goes wrong.”
One answer to plastics in packaging is biodegradable materials, which have been on the market for many years and have seen their market share continue to grow. But there are severe restrictions preventing their wider application in food packaging, as these materials do not provide a sufficient barrier against water vapour, oxygen or flavours. The EU-funded HyperBioCoat project addressed this challenge by developing and testing new biodegradable hybrid organic-inorganic coatings for use in food, cosmetics and medical device packaging. “We developed a coating material based on biopolymers extracted from lignocellulosic biomass by combining them with the material class of bioORMOCER®s,” says project coordinator Stefan Hanstein from Fraunhofer IWKS. The bioORMOCER® coatings are bio-based, biodegradable coatings developed by the Fraunhofer Institute for Silicate Research.
Consortium members investigated biodegradable barrier coatings for plastic packaging materials in which the biopolymers are derived from fibrous fruit residues (lignocellulose). According to Hanstein: “One of the project’s greatest challenges involved finding the correct fruit residue for the extraction of lignocellulose and the modification of the hemicellulose to create the desired properties.” Depectinised apple pomace (the main solid waste generated in factories producing cider and apple juice) performed well as a raw material. “The process developed is a combination of extraction and partial hydrolysis (intensified extraction). It provides 1 kg of carbohydrate polymer from 25 kg of dry pomace, with the potential for doubling the yield,” Hanstein explains. Researchers also investigated possible industrial applications for other types of fruit residues, like berry pomace and cocoa shells for novel food production systems and the biotech industry. They demonstrated a route for the chemical modification of carbohydrate polymers that achieves the required compatibility with the lacquer. “This showed how the new bio-based and biodegradable polymer coating can be easily applied and at industrial scale, paves the way for further application in the industry,” comments Hanstein. The next step was to adapt the barrier coating to the different carrier materials, which involves flexible and rigid biopolymer substrates and testing for the packaging applications. According to Hanstein: “This approach improves the properties of packaging materials and of bio-based recyclable materials by using a biodegradable barrier coating.”
Permalink: https://cordis.europa.eu/article/id/413459-polymers-from-fruit-waste-provide-biodegradable-packaging-materials
Today, fresh as well as convenience food is sold in packages, and the hygienic conditions, long shelf life and easy availability of these packaged products are part of our modern lifestyle. However, the result is significant environmental impacts and pollution due to the plastic materials associated with the packaging.
This is a machine translation provided by the European Commission’s eTranslation service to help you understand this page. Please read the conditions of use.
Until she retired in September 2021, Clare Goldsberry reported on the plastics industry for more than 30 years. In addition to the 10,000+ articles she has written, by her own estimation, she is the author of several books, including The Business of Injection Molding: How to succeed as a custom molder and Purchasing Injection Molds: A buyers guide. Goldsberry is a member of the Plastics Pioneers Association. She reflected on her long career in "Time to Say Good-Bye."
Most mold manufacturers do not use material flow analysis software as a part of the mold design process as a general rule. Yet, because the mold is such a critical part of the success or failure of the entire molding process, all available tools should be used. That’s the opinion of Rick Carobus, president of EPS Flotek, a mold and material flow simulation service company and reseller of MoldEx 3D analysis software.“This has always been seen as a luxury item by many moldmakers,” Carobus told PlasticsToday at NPE2012. “While they understand that it will save money in the long run, they know it’s not necessary to build or run a mold. Some OEMs will spend money to do an engineering change on the back end, however they won’t spend money to make it right on the front end.”
Logging out of EU Login will log you out of any other services that use your EU Login account. Use the CORDIS log out button to remain logged in on other services.
Most mold manufacturers do not use material flow analysis software as a part of the mold design process as a general rule. Yet, because the mold is such a critical part of the success or failure of the entire molding process, all available tools should be used. That’s the opinion of Rick Carobus, president of EPS Flotek, a mold and material flow simulation service company and reseller of MoldEx 3D analysis software.
Cosmetic-bottles production based on fibre-enforced wax was taken to the industrial level by making the material compatible with injection moulding. Hanstein notes: “Project partner Stefanski Design has begun using a slush casting, hand-crafted manufacturing approach producing prototypes for a leading luxury bio resort in Spain. Within the HYPERBIOCOAT project, the basic material has been further developed and is now compatible with large scale injection moulding production.” Project partners also demonstrated a new lean biomass extraction facility which can be installed in small agrobiorefineries. The facility covers a range of applications from providing tailored feedstock for fermentation processes (for example, biogas) and for novel food production systems, like insect culture, to delivering herbal extracts with bioactive compounds such as natural antimicrobials. HYPERBIOCOAT benefits the environment due to its lower CO2 footprint and conservation of natural resources: The supply chain does not require additional plant cultivation areas or additional supplies of water, fertiliser and pesticides. Furthermore, the food processing industry will benefit from a new value chain for their fibrous resources. “The advantage of these residues is that they are not competing with animal feed or food production, and provide an abundant feedstock for compostable as well as recyclable plastic packaging materials,” notes Hanstein. The HYPERBIOCOAT project received funding from the Bio-based Industries Joint Undertaking, a public-private partnership between the EU and industry.
GETTING A QUOTE WITH LK-MOULD IS FREE AND SIMPLE.
FIND MORE OF OUR SERVICES:
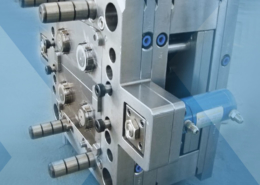
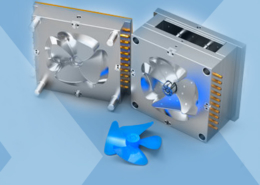
Plastic Molding

Rapid Prototyping
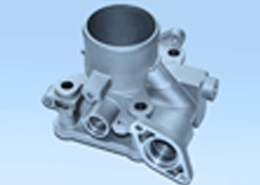
Pressure Die Casting
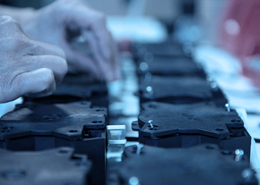
Parts Assembly
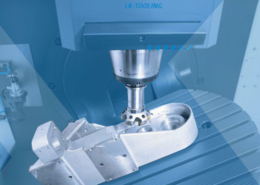