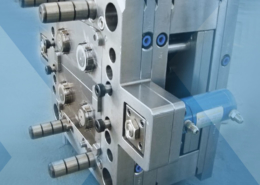
Razer Reveals Viper Mini Signature Edition Gaming Mouse - mini injection molding
Author:gly Date: 2024-09-30
Four decades and three buildings later, Matrix has evolved from strictly a mold design and fabrication shop into a premier plastics manufacturing facility that incorporates moldmaking with injection molding and other value-added services to produce critical components and sub-assemblies for the medical device industry.
The company’s roots are in moldmaking. Today, it incorporates precision moldmaking with injection molding and other value-added services to produce critical components and sub-assemblies for customers in medical manufacturing and other sectors.
Get weekly and/or daily updates delivered to your inbox. You can unsubscribe at any time and we'll never share your details to third parties.
Matrix Plastic Products molds critical components and builds the ultra-precise molds required to produce components for the medical device industry.
Use this form if you have come across a typo, inaccuracy or would like to send an edit request for the content on this page. For general inquiries, please use our contact form. For general feedback, use the public comments section below (please adhere to guidelines).
Researchers at the Fraunhofer Institute for Laser Technology ILT in Aachen have developed a way of automating the polishing work: “We do not polish the surface by hand with grinding and polishing media. Instead we use a laser,” explains Dr.-Ing. Edgar Willenborg, group leader at the ILT. “The laser beam melts the surface to a depth of about 50 to 100 micrometers. Surface tension ensures that the liquid metal flows evenly and solidifies smoothly.” Like in conventional grinding and polishing, the process is repeated with increasing degrees of fineness. In the first stage the researchers melt the surface to a depth of about 100 micrometers, in further steps they gradually reduce the depth.
Founded in 1978 by brothers Paul and James Ziegenhorn and their father, William, Matrix Tooling Inc. began with seven employees, “a rich family tradition of moldmaking craftsmanship, and an unwavering focus on customer service,” said Matrix’s news release. In 2000, Matrix secured the trade name Matrix Plastic Products and built a 10,000-square-foot addition dedicated to molding production. An ISO Class 8 cleanroom was installed in 2006 to accommodate the company’s growing emphasis on medical business. ISO 13485 certification followed in 2010.
Matrix Plastic Products Inc. (formerly known as Matrix Tooling Inc. & Matrix Plastic Products), is celebrating “40 successful years in business” with a new corporate name and website. Matrix Plastic Products (Wood Dale, IL) is a plastic injection molder of critical components that also designs and builds the ultra-precise molds required to produce components for the medical device industry and other high-performance applications.
(PhysOrg.com) -- Polishing metal surfaces is a demanding but monotonous task, and it is difficult to find qualified young specialists. Polishing machines do not represent an adequate alternative because they cannot get to difficult parts of the surface. A new solution is provided by laser polishers.
Today, Matrix Plastic Products operates 15 presses ranging from 5 to 300 tons, and has added assembly and 3D prototyping to further extend its full-service menu. The QA lab has also grown and features four OGP multi-sensor metrology systems to support myriad advanced inspection protocols. A CT scanner is on the soon-to-come list.
Jobs are in short supply, and yet some sectors have difficulty in finding suitable trainees for specialist tasks, such as polishing injection molds. The work is time-consuming and monotonous but requires highest levels of concentration, because any blemish in the mold can render it useless. A skilled worker may often need a whole week to polish a single metal mold. Up to now it has not been possible to use machines for this dreary work because they cannot get into the curved shapes.
“Over the years, as our customers’ demands grew, we responded by broadening our value-added service offerings,” said Paul Ziegenhorn, President. “In 1995, we put our first molding press on the floor so we could perform our own mold samplings and run small volumes for our customers. We also expanded our inspection capabilities by adding a quality assurance lab and certified our quality systems to ISO 9001 by 1999, one of the first mold shops to do so. At that time, molding production made up a very small portion of our sales, but the momentum had already begun.”
“This company has never shied away from technology,” said Gary Johansson, VP of Quality/Regulatory. “We understand that we need to have better equipment than the competition to keep the high-level work coming here.”
Until she retired in September 2021, Clare Goldsberry reported on the plastics industry for more than 30 years. In addition to the 10,000+ articles she has written, by her own estimation, she is the author of several books, including The Business of Injection Molding: How to succeed as a custom molder and Purchasing Injection Molds: A buyers guide. Goldsberry is a member of the Plastics Pioneers Association. She reflected on her long career in "Time to Say Good-Bye."
Your email address is used only to let the recipient know who sent the email. Neither your address nor the recipient's address will be used for any other purpose. The information you enter will appear in your e-mail message and is not retained by Phys.org in any form.
We keep our content available to everyone. Consider supporting Science X's mission by getting a premium account.
Given the evolution of the company, the decision to move forward with the single corporate identity Matrix Plastic Products is both practical and tactical. “It is the more inclusive name and better represents our broader mix of services today,” said Andy Ziegenhorn, COO. “But we are still moldmakers by trade, so ensuring the integrity of the tools we run in production will always be hard-wired into the way we operate here.”
“We can set the melting depth by means of various parameters: the laser output, the speed at which the laser beam travels along the surface and the length of the laser pulses,” states Willenborg. Laser polishing does not achieve the same surface smoothness as perfect hand polishing - hand polishers can achieve a roughness Ra of 5 nanometers, the laser at present can only manage 50 nanometers - but Willenborg still sees considerable market potential for the system. “We will concentrate on automating the medium grades: a roughness of 50 nanometers is adequate for many applications, including the molds used for making standard plastic parts.” The high-end levels of smoothness will therefore remain the domain of skilled hand polishers.
The time gained by laser polishing and the cost saving achieved are enormous. Whereas a skilled polisher needs about 10 to 30 minutes for each square centimeter, the laser polishes the same area in about a minute. A prototype of the laser polishing machine developed by the scientists in cooperation with mechanical engineering firm Maschinenfabrik Arnold has already been built. Willenborg estimates that the system will be ready for industrial use in one to two years’ time. At the Euromold trade show, to be held from December 2 to 5 in Frankfurt, the researchers will be presenting examples of three-dimensional surfaces polished by laser.
GETTING A QUOTE WITH LK-MOULD IS FREE AND SIMPLE.
FIND MORE OF OUR SERVICES:
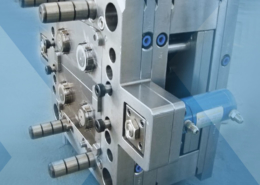
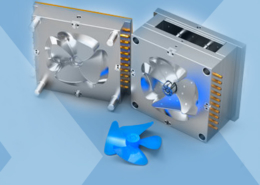
Plastic Molding

Rapid Prototyping
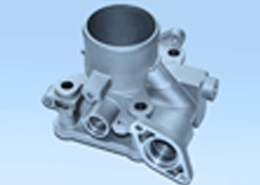
Pressure Die Casting
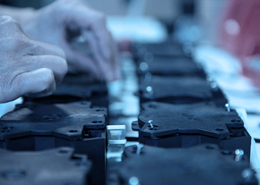
Parts Assembly
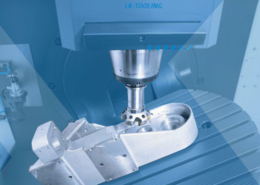