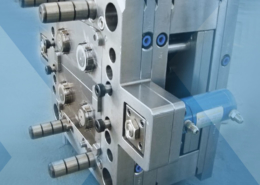
Quadrant CMS brings plastics processing expertise to succesful development
Author:gly Date: 2024-09-30
All Lego bricks are made from the same ABS plastic. It comes to Lego from suppliers and is held in giant silos. Generally it is clear or red, and the color for specific bricks is added at the molding machine. This is a bin full of ABS plastic, with some additional colors mixed in.
"The injection moulding sector offers enormous potential and is one of our strategic growth drivers. The competitive market environment requires maximum cost effectiveness and flexibility. As its own injection moulding division, ALPLAinject will continue to ensure our competitiveness in the future," said ALPLA CEO Philipp Lehner with conviction. The new division reports directly to the CEO.
Shrink-wrapped and ready to go, these cases of Star Wars Lego sets will be shipped to the Czech Republic, where they will be handled by a giant distribution center there operated by DHL for Lego. Please visit the Road Trip 2011 page for all the coverage from CNET reporter Daniel Terdiman's travels through Europe.
Currently, there are about 7,000 active molds being used at Lego. All told, it keeps about 9,000 around, with many stored on shelves like this one. The average mold is worth $72,000, with the most valuable coming in around $360,000.
Standardised processes, centralised product and technology development; and shorter distances will ensure greater flexibility and efficiency in the future. "With ALPLAinject, we are focusing on the specific requirements of the dynamic injection moulding market. We combine technological expertise and regional market knowledge, promote the global roll-out of innovative processes and enable our customers to bring new products to market faster," emphasised the new ALPLAinject managing director Michael Feltes, who had already been business development director in the injection moulding section of the Group since October 2022. The global headquarters of ALPLAinject are located at the ALPLA headquarters in Hard. There are also global teams in all nine regions of the ALPLA Group.
This is one of 12 molding 'modules' located in Billund. Each module, or room, has as many as 64 working molding machines, divided into two aisles of 32 machines each.
Part of Lego's system is to be as efficient as possible. That means making bricks and other elements that can be used in different ways. These blue pieces can either be used as heads for mini-figures, or as decorations for other pieces.
This machine presses down into each Star Wars set that passes through to make sure that the packs of Lego bricks inside isn't too high up. If it is too high, the box may not be able to be closed correctly.
Now in the packaging department, most of the bricks are in packs that are dropped into a package automatically. But some of the packs are too big to fit in when dropped that way and must be shaken and flattened manually in order to fit properly.
These tubes carry ABS plastic into the molding rooms. The sound coming from the pipes is very much like what millions of grains of rice would sound like going through pipes.
Almost none of the plastic used in the Lego factory goes to waste, but a very small amount does get spilled. This giant bin is full of spaghetti-like plastic that has hardened and has no use.
Here we see two ellipsoid pieces that have just been pressed, still sitting in the mold. In a second, they will drop off and onto a belt below.
ALPLAinject stands for high-quality injection-moulded parts such as closures, caps, jars and multi-part packaging components such as pumps or deodorant sticks. With this new division, the international ALPLA Group is setting the course for further growth. The ALPLAinject brand brings together all human and technical resources in this area in one central organisational structure. It comprises a total of three core technologies – injection blow moulding and compression moulding in addition to injection moulding – as well as global toolmaking, development and sales.
This is a cross-section of a Lego brick mold. First, very hot plastic is injected into the mold on the right side. It then spreads through little channels and is then pushed into the press area of the mold through very small slits. When cold water is then flushed through the mold, it cools down the plastic, and the mold opens, allowing the bricks to snap off and drop down onto a belt below.
A mold is used for about four weeks before it is pulled from the production line and completely cleaned out. Here, we see a Lego worker doing a meticulous cleaning of a mold.
If you're a Lego fan like me, visiting this little town in western Denmark is a little like making a religious pilgrimage. That's obviously an overstatement, but this is the home of Lego, maybe the world's most famous toy. I got a chance not only to visit the company's headquarters but also to see the production, processing, and packaging of the famous bricks. The whole process is actually quite simple. Making the bricks involves injecting very hot plastic into a mold and pressing it. Cool it a bit, open the mold, and out drops Lego bricks. This is from the second part of the process, when bricks and other elements--such as these soon-to-be mini-figures--are finished by adding any additional parts, like legs, arms, and heads, and having anything they need printed on, like a suit and tie.
This display shows the weight of a small bag of Lego bricks known as a pre-pack. The weight must be between 94.9 grams and 95.7 grams. Coming in at 94.94 grams, this back passes muster. However, as the display shows, five bags came in too light, and one was too heavy. But 5,354 were in the target range.
Here we see a robot arm inside the molding machine grabbing the waste from the injection and molding process. This plastic will be put into a grinder, and reused almost immediately.
The global ALPLA Group is setting the course for further growth in injection moulding by establishing the ALPLAinject division. By strategically concentrating all injection moulding expertise and capacity under this brand, the plastic packaging specialist is increasing efficiency, speeding up the market launch of new products and unlocking new market segments.
Now in the processing part of the production system, this machine is dropping torsos for mini-figures onto a belt where they will have additional elements like arms and legs and heads added to them.
This is the reception at Lego's world headquarters. Note the way the ceiling and the chairs make up what appears to be two interlocking Lego bricks.
ALPLAinject manufactures roughly 60 billion injection-moulded parts per year at 43 plants around the world. The division has more than 600 high-performance machines and systems. As a specialist in packaging solutions and recycling, ALPLA also relies on technological innovation. ALPLAinject scores highly with its decades of experience in lightweighting, alternative and recyclable materials; and energy-saving production facilities.
GETTING A QUOTE WITH LK-MOULD IS FREE AND SIMPLE.
FIND MORE OF OUR SERVICES:
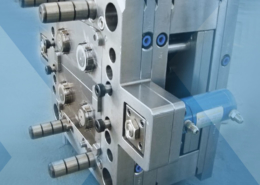
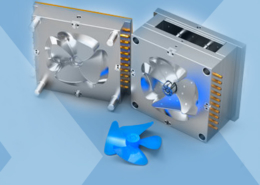
Plastic Molding

Rapid Prototyping
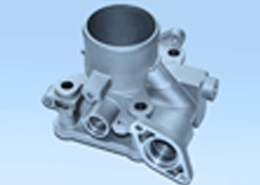
Pressure Die Casting
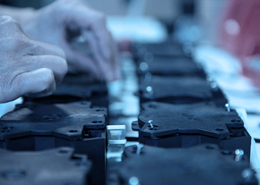
Parts Assembly
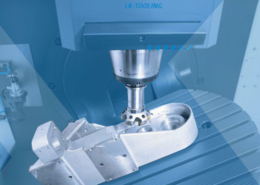