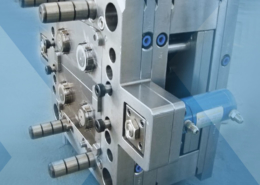
Unlocking Potential: The Art of Molding Polystyrene
Author:gly Date: 2024-06-08
Polystyrene, a versatile thermoplastic polymer, holds a significant place in the realm of manufacturing, offering a multitude of applications ranging from packaging to construction. Central to the utilization of polystyrene is the process of molding, a technique that shapes this material into diverse forms with precision and efficiency. In this article, we embark on a journey to explore the art of molding polystyrene, uncovering its intricacies and delving into its myriad applications.
1. Introduction to Polystyrene Molding
Polystyrene molding is a manufacturing process that involves heating polystyrene resin to its melting point and then injecting or compressing it into a mold cavity, where it cools and solidifies to form the desired shape. This process offers immense versatility, allowing for the production of intricate designs, intricate patterns, and precise dimensions. From disposable utensils to intricate electronic components, polystyrene molding finds its application in various industries, owing to its affordability, lightweight, and ease of processing.
Polystyrene, in its raw form, is a rigid and transparent material. However, through the molding process, it can be transformed into a myriad of forms, including foamed polystyrene for insulation purposes or high-impact polystyrene for durable applications. The versatility of polystyrene molding extends to different techniques such as injection molding, extrusion molding, and foam molding, each offering unique advantages depending on the desired outcome and production requirements.
2. Injection Molding: Precision Engineering
Injection molding stands as one of the most widely used techniques for molding polystyrene due to its precision, efficiency, and scalability. The process involves injecting molten polystyrene resin into a pre-designed mold cavity under high pressure, ensuring uniform filling and solidification. Injection molding enables the production of complex geometries, intricate details, and tight tolerances, making it ideal for mass production of consumer goods, automotive parts, and electronic components.
The success of injection molding lies in the design and fabrication of molds, which require meticulous attention to detail and precision machining. Advanced technologies such as computer-aided design (CAD) and computer-aided manufacturing (CAM) facilitate the creation of intricate mold designs with minimal errors and maximum efficiency. Moreover, the integration of automation and robotics enhances the speed and accuracy of the injection molding process, reducing cycle times and production costs.
3. Environmental Considerations
While polystyrene molding offers unparalleled manufacturing capabilities, it also raises concerns regarding environmental sustainability and waste management. Polystyrene, particularly in its foamed form, is non-biodegradable and can persist in the environment for hundreds of years, posing significant challenges for waste disposal and pollution prevention. Addressing these challenges requires innovative solutions, such as recycling, biodegradable alternatives, and sustainable manufacturing practices.
Recycling plays a crucial role in mitigating the environmental impact of polystyrene waste by diverting used materials from landfills and incineration. Advanced recycling technologies, including mechanical recycling and chemical recycling, enable the conversion of waste polystyrene into raw materials for new products, reducing the reliance on virgin plastic production. Additionally, the development of biodegradable alternatives to conventional polystyrene offers a promising avenue for reducing environmental pollution and promoting sustainability in the manufacturing industry.
4. Future Perspectives and Innovations
Looking ahead, advancements in materials science, recycling technologies, and sustainable practices will continue to shape the landscape of polystyrene molding. Researchers and manufacturers are exploring novel materials with enhanced properties, such as bio-based polystyrene derived from renewable sources or biodegradable polymers with comparable performance characteristics. Furthermore, the adoption of circular economy principles, including closed-loop recycling systems and eco-friendly packaging solutions, holds the key to reducing the environmental footprint of polystyrene manufacturing and consumption.
In conclusion, molding polystyrene represents both an art and a science, offering boundless possibilities for creativity, innovation, and sustainability. By understanding the intricacies of polystyrene molding, embracing sustainable practices, and fostering collaboration across industries, we can unlock the full potential of this versatile material while minimizing its environmental impact. Together, we can pave the way towards a more sustainable and prosperous future for generations to come.
GETTING A QUOTE WITH LK-MOULD IS FREE AND SIMPLE.
FIND MORE OF OUR SERVICES:
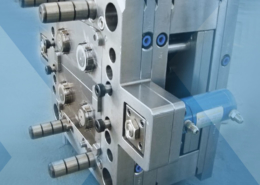
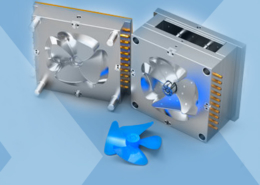
Plastic Molding

Rapid Prototyping
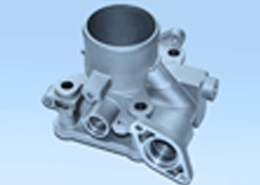
Pressure Die Casting
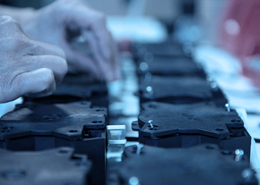
Parts Assembly
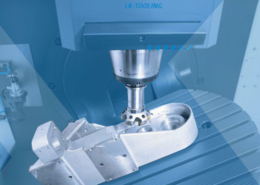