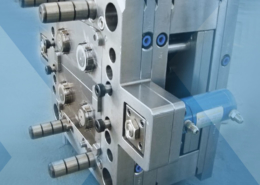
Q&A: a global medical injection moulding insight from Sumitomo (SHI) Demag - pla
Author:gly Date: 2024-09-30
BRUDER Spielwaren was founded in 1926 by Paul Bruder, who began by producing brass tongues for toy manufacturers. Today, the company employs 490 people at its headquarters in Fürth, Germany, plus another 120 at its facility in Plzeň, Czech Republic, which was built in 2015.
Projecting a double-digit increase in sales, Plastic Molding Technology has invested close to $1 million in new injection molding and auxiliary equipment this year.
BRUDER uses a great variety of different technologies to make its plastic toys, such as the internal gas pressure process, which offers the advantages of reducing weight and saving material input. BRUDER also makes use of multi-component technology right up to five-component injection moulding. This enables the production of parts consisting of several different materials and/or in several colours by a single injection moulding process.
Production Manager at BRUDER Sönke Haverich added: “Our experience with the machines delivered so far has been all positive. The machines take up little space and meet all our demands in terms of precision and speed.”
Bernd Klemm, Department Manager of Injection Molding, said: “Energy efficiency is gaining increasingly in significance; space is another important resource. This is why the machine’s footprint is also such an important buying argument for us.”
Its first plastic parts were produced in 1958. Today, BRUDER delivers its high-quality toys to more than 60 countries. Around a quarter of its sales are made in the GAS region, with other major markets in France, Italy, the Netherlands, Eastern Europe, Japan and Korea. In the US, the company operates its own sales subsidiary.
BRUDER’s most important criteria for injection moulding machines are high precision, reliability, stability, energy efficiency and a small footprint.
“Several of our customers are experiencing record growth within their respective industries to support infrastructure in the USA,” said PMT CEO and owner Charles A. Sholtis in a prepared statement. For its part, PMT is projecting a double-digit increase in sales this year. It’s putting that extra money to good use by investing in new injection molding machines and auxiliary equipment that will, in turn, support booming customer demand.
Toy models made by BRUDER are designed to help children understand the functions of real-life objects. Special attention is paid to a well-balanced combination of easy-to-handle playing functions with simultaneous model consistency and the greatest possible stability. With its high-quality products, BRUDER ranks among the leading manufacturers of toy vehicles for children in Europe. BRUDER toys stand out by their quality and accuracy. For example, real appliances and vehicles of world-famous brands are reproduced as toy models on a scale of 1:16.
Compact and user-friendly, the machines of the SmartPower series stand out by their intelligent and economical use of energy – mainly due to the combination of a fast-response, speed-controlled, air-cooled servo motor with a sturdy constant displacement pump known as the ‘drive-on-demand’ system. In this system, the drive unit is only active as long as required for movements and pressure generation. During cooling times and cycle breaks for parts handling, the servo drive remains switched off and consumes no energy.
The products are mostly assembled without auxiliaries such as screws or adhesives. Only the wheels are pressed onto the vehicle axes by metal rods. Otherwise, only plug-in connections are used. The sturdy wheels of the vehicles are produced partly from TPE by way of 2K injection moulding, which makes it possible to achieve the desired similarity to the original. At the same time, this enhances the play value, since the wheels make considerably less noise when played with than hard plastic tires.
The positive experience of BRUDER Spielwaren with Wittmann in robotics and handling systems, in which the two companies have been co-operating for more than 20 years, prompted BRUDER to install a first injection moulding machine from Wittmann’s servo-hydraulic SmartPower series in 2020. Five more have been added this year. Of the six machines, with clamping forces ranging from 600 to 1,600 kN, two are equipped with a WS80 servo picker from Wittmann, and a SmartPower 60 was delivered as an Insider cell with a Wittmann Primus 14 robot. In addition to the robot, a conveyor belt and the protective housing are also integrated in the cell, which makes the entire system extremely compact. Moreover, one of the machines is fitted with a hot embossing system.
PMT has taken delivery of 10 new Maruka USA Toyo injection molding machines so far this year, including three 55-ton, four 110-ton, and two 200-ton presses. PMT also invested in its first injection molding machine under 40 tons, with a new Toyo 20-ton horizontal machine. The new investments will support key customers in the telecommunications, medical device, and electrical industries.
That proverbial rising tide that lifts all boats? Contract manufacturer Plastic Molding Technology (PMT) is riding that wave. The company announced today that it has invested close to $1 million in new equipment this year to support new contract awards that will require additional capacity.
PMT also procured auxiliary equipment for the new presses, including several HY Robotics 3-axis robots and sprue pickers, Novatec dryers with central conveying systems, and conveyors with part separation. Two new Gorbel overhead crane systems will provide safe mold transport and set-up in the company’s white room space and on the plant floor.
PMT now has a total of 72 injection molding machines in its 60,000-square-foot manufacturing facility, and operates 24/7 in its strategic border location in El Paso, TX.
Apart from innovative strength and plastics technology expertise, BRUDER places great emphasis on resources management in the interest of a sustainable economy. An internal recycling circuit and energy-efficient production processes, combined with a range of about 800 spare part sets for repairs to BRUDER toys, are testament to the company’s ecological responsibility. In addition to in-house recycling of sprue and rejects using two granulators operating in the company’s basement, a continuous search for further opportunities to save energy remains ongoing. Another contribution to sustainable management practices is the company’s preference given to co-operation with local partners.
GETTING A QUOTE WITH LK-MOULD IS FREE AND SIMPLE.
FIND MORE OF OUR SERVICES:
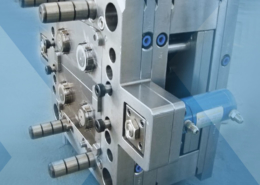
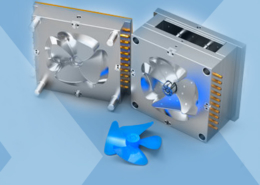
Plastic Molding

Rapid Prototyping
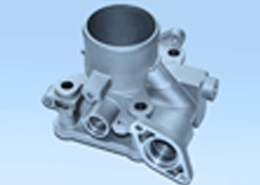
Pressure Die Casting
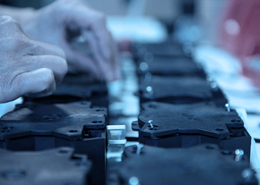
Parts Assembly
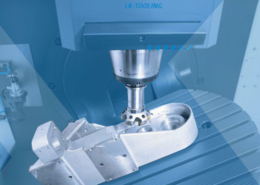