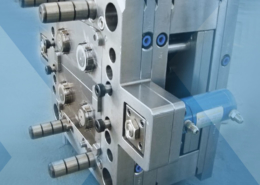
PT Daiho Indonesia Batam Buka 2 Lowongan Kerja, Cek Syaratnya! - Kepri Post - pe
Author:gly Date: 2024-09-30
INDO-MIM is the world’s largest MIM company, with over 3,000 employees producing over 150 million parts annually. Jag Holla, Sr. VP-Marketing at INDO-MIM Ltd, discussed the company’s use of Additive Manufacturing to produce mold inserts.
Covina, March 16, 2023 (GLOBE NEWSWIRE) -- The Plastic Injection Molding for Medical Device Market accounted for US$ 82.7 million in 2020 and is estimated to be US$ 148.88 million by 2030 and is anticipated to register a CAGR of 6.1%. The medical plastic injection molding process is cost-efficient, and ideal for top volume production runs and applications requiring consistency and tight tolerances. This molding process is additionally used for medical device prototype development for the FDA approval process and to be used in laboratory testing. Since inception, the utilization of plastics within modern medicine has steadily increased. Medical devices that are manufactured from injection molded plastic have contributed to a discount in medical costs, communicable disease and pain management. High tech polymers are used within medical device prototype development and are commonly wont to create improved artificial limbs and devices that reduce the danger of infection. Medical plastic injection molding directly results in increased patient safety and therefore the ability to save lots of more lives. Since medical device plastics provide increased versatility and may be combined with metal to make enhanced medical product attributes, medical grade plastics became the well-liked material for varied sorts of electronic medical devices.
Don't miss any new issue of PIM International, and stay up to date with the latest industry news. Sign up to our fortnightly newsletter.
Reach a truly international audience that includes component manufacturers, end-users, industry suppliers, analysts, researchers and more.
Holla talked about how the company began with Laser Beam Powder Bed Fusion (PBF-LB) AM machines but then moved to using Binder Jetting as the preferred production method. This was, in part, due to the speed advantage over PBF-LB, but also enabled the company to use its M2 tool steel powder for the production of mold inserts.
In a recent webinar hosted by Metal AM magazine, Metal Injection Molding company INDO-MIM, Bengaluru, India, discussed in detail the use of its new M2 tool steel for the Additive Manufacturing of mold inserts. The company is now using Binder Jetting (BJT) from HP to produce a wide range of tooling.
Discover suppliers of these and more in our advertisers’ index and buyer’s guide, available in the back of PIM International.
Some key challenges faced by manufacturers of plastic injection molding for medical devices include meeting regulatory requirements, ensuring product consistency and quality, managing costs, and keeping up with advancements in technology and materials.
Analyst View:Increasing technological advancements in plastic injection molding techniques to make sure medical products are free from contamination and safer is additionally expected to drive the expansion of the respective market. Rising healthcare expenditure and spending in both developing and developed economies are among the crucial factors anticipated to bolster the worldwide plastic injection molding for the medical device market. Moreover, the growing global geriatric population, including the prevalence of chronic diseases, is another factor expected to fuel market growth.
Some potential challenges for the plastic injection molding for medical device market in the future include increasing competition, regulatory changes, and the need for more sustainable and eco-friendly materials. Opportunities include advancements in technology and materials science, increased demand for medical devices due to aging populations and the prevalence of chronic diseases, and growing healthcare infrastructure in emerging markets.
There are various applications of plastic injection molding in the medical device industry, such as manufacturing of diagnostic equipment, drug delivery systems, surgical instruments, disposable devices like syringes, IV tubing, and catheters, orthopedic implants, and dental instruments. Plastic injection molding is also used for producing housings, covers, and enclosures for medical devices.
The Global Plastic Injection Molding for Medical Device Market accounted for US$ 82.7 million in 2020 and is estimated to be US$ 148.88 million by 2030 and is anticipated to register a CAGR of 6.1%. The global plastic injection molding for medical device market report segments the market on the basis of type, end-user, and region.
There are several factors that are driving the growth of the plastic injection molding for medical device market, including:
In addition to the design capabilities of AM, such as the inclusion of conformal cooling channels, a key advantage of AM is the speed at which the process can produce the tooling. This can save many weeks, or months, in getting a product to the customer.
Not only is BJT quicker for producing the tooling, it also offers improved properties compared to wrought material. INDO-MIM’s M2 shows superior wear and machineability performance, compared to wrought, explained Holla. This can result in a 30-50% tool life improvement, it was stated.
The free-to-access PIM International magazine archive offers unparalleled insight into the world of MIM, CIM and sinter-based AM from a commercial and technological perspective through:
The market provides detailed information regarding the industrial base, productivity, strengths, manufacturers, and recent trends which will help companies enlarge the businesses and promote financial growth. Furthermore, the report exhibits dynamic factors including segments, sub-segments, regional marketplaces, competition, dominant key players, and market forecasts. In addition, the market includes recent collaborations, mergers, acquisitions, and partnerships along with regulatory frameworks across different regions impacting the market trajectory. Recent technological advances and innovations influencing the global market are included in the report.
Extensive MIM, CIM industry and sinter-based AM industry news, plus the following exclusive deep-dive articles and reports:
About Prophecy Market Insights:Prophecy Market Insights is specialized market research, analytics, marketing/business strategy, and solutions that offers strategic and tactical support to clients for making well-informed business decisions and to identify and achieve high-value opportunities in the target business area. We also help our clients to address business challenges and provide the best possible solutions to overcome them and transform their business.
During the presentation, Harish Irrinki, Sr Applications Engineer and Strategic Account Manager at HP, also provided detailed information on HP’s Metal Jet S100 Binder Jetting solution. The Metal Jet S100 has an effective build volume of 430 x 309 x 140 mm and meets MPIF standards for stainless steel with HP Metal Jet SS 316L and HP Metal Jet SS 17-4PH materials. The HP Metal Jet workflow includes a powder management station, the Metal Jet S100 AM machine, a curing station and a powder removal station. Sintering equipment is provided by a third party, giving users the choice of either investing in a furnace or using a toll service for this stage of the process.
GETTING A QUOTE WITH LK-MOULD IS FREE AND SIMPLE.
FIND MORE OF OUR SERVICES:
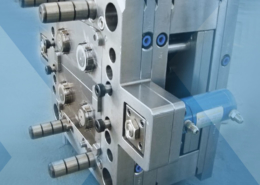
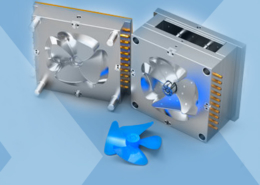
Plastic Molding

Rapid Prototyping
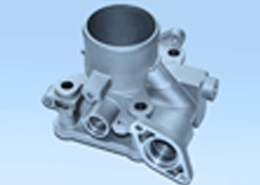
Pressure Die Casting
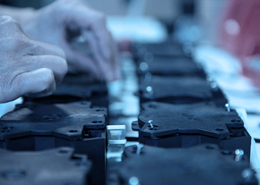
Parts Assembly
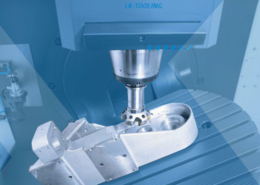