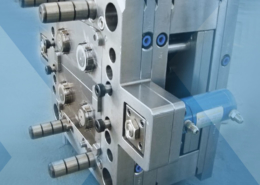
Protolabs introduces colour matching system - plastic injection moulding service
Author:gly Date: 2024-09-30
We will only use your email address to send you the newsletters you have requested. We will never give your details to anyone else without your consent. You can unsubscribe at any time by clicking on the unsubscribe link at the bottom of every email, or by emailing us at [email protected].
News from Dezeen Events Guide, a listings guide covering the leading design-related events taking place around the world. Plus occasional updates and invitations to Dezeen events.
Our most popular newsletter, formerly known as Dezeen Weekly, is sent every Tuesday and features a selection of the best reader comments and most talked-about stories. Plus occasional updates on Dezeen’s services and breaking news.
Their injection moulding machines can manufacture personal protective equipment (PPE) 75 times faster than a 3D printer explained Dickens, who co-founded UK nonprofit Recycle Rebuild.
"The workspaces follow strict guidelines on how to maintain a clean working environment suitable for making the masks and storing them to avoid contamination," he added.
Freeform Injection Molding technology from Nexa3D compresses design, iteration, and validation cycle times into a matter of hours rather than weeks.
Founded in 2014 by Dave Jakkens, Precious Plastic shares designs for its machines as open source, so anyone can design and build a recycling system.
SPT Vilecon said it has begun expanding the range of injection mold prototyping with silicone, metal, and ceramic materials to provide medical device manufacturers with an even wider selection of product development and verification services.
Certified to ISO 13485, Denmark-based SPT Vilecon describes itself as a fully integrated provider of development and manufacturing services to the medical device industry. It offers in-house tool making and injection molding along with other manufacturing services to companies in northern Europe.
Sent every Thursday and containing a selection of the most important news highlights. Plus occasional updates on Dezeen’s services and invitations to Dezeen events.
News from Dezeen Events Guide, a listings guide covering the leading design-related events taking place around the world. Plus occasional updates and invitations to Dezeen events.
Recycling initiative Precious Plastic's open-source machines are being used to recycle plastic and turn it into face shields, respirator masks and hands-free door handles to fight coronavirus.
Based on input collected from the first two iterations, the design of the silicone part was approved and manufacturing of a metal tool was initiated with full confidence of part moldability and performance. The in-house tool shop built the final metal tooling in four weeks without iterations.
Medical device manufacturers are tasked with developing elaborate test protocols to ensure that the product in development is safe and meets essential requirements. If these tests are conducted late in the development process, the more onerous and risky they become. SPT Vilecon often works with silicone, a material that is extensively used in medical applications because of its chemical resistance, mechanical performance, and biocompatibility. However, silicone parts are notoriously difficult to prototype and test, since most grades need to be injection molded to achieve their full performance potential, said the company. FIM enabled SPT Vilecon to offer an alternative to a customer developing an intravenous (IV) silicone product — the use of 3D-printed tooling to perform early design and material verification at a fraction of the cost of conventional methods.
Hospitals treating coronavirus patients need this emergency PPE to keep their staff safe, as medical workers are particularly vulnerable to being seriously infected.
We will only use your email address to send you the newsletters you have requested. We will never give your details to anyone else without your consent. You can unsubscribe at any time by clicking on the unsubscribe link at the bottom of every email, or by emailing us at [email protected].
Other design teams responding to the PPE shortage include MIT in the US, where researchers have invented a flat-pack face shield that can be assembled from a single piece of plastic.
In Germany, the Kunststoffschmiede plastic recycling workshop is using its machines to make 20,000 visors for the Dresden area. Plasticpreneur in Austria, which makes machines for the project, has also gone into mass production.
Our most popular newsletter, formerly known as Dezeen Weekly, is sent every Tuesday and features a selection of the best reader comments and most talked-about stories. Plus occasional updates on Dezeen’s services and breaking news.
Injection-molded silicone parts were produced within two days, allowing early verification of key design and performance aspects.
The 3D-printed molds for the first and second iterations cost less than €2,000 combined. And the technology enabled a two-day design cycle, which is more than 90% faster than conventional metal tooling.
Greek company Alumoulds, which make moulds for Precious Plastic machines, is working with Precious Plastic Leman in Switzerland to make hands-free door handles.
In China, 3D printer company Creality 3D has designed and donated thousands of buckles that hold a face mask in place without hurting the wearer's ears.
Editor in chief of PlasticsToday since 2015, Norbert Sparrow has more than 30 years of editorial experience in business-to-business media. He studied journalism at the Centre Universitaire d'Etudes du Journalisme in Strasbourg, France, where he earned a master's degree.
SPT implemented Nexa3D’s Freeform Injection Molding (FIM) technology to help customers shorten time-to-market on complex medical devices in demanding medical-grade materials and to expand on the range of materials that can be quickly and reliably used in prototyping and early device test manufacturing.
"The injected items also benefit from not being porous like 3D printed counterparts, ensuring bacteria and viruses can't hide inside the plastic."
These face shields protect the wearer from infectious droplets spattering on them and help keep their face masks dry. Medical-grade N95 or FFP2 masks must be replaced if they get wet, but are in short supply all over the world.
"A Precious Plastic workspace in Gran Canaria was requested to provide over 3,000 face visors for the government, hospitals and private sector," said Precious Plastics member Rory Dickens.
The coronavirus can live on surfaces for days, and people can catch it by touching a door handle and then touching their mouth or eyes. Opening doors without hands helps prevent the spread of infection.
The patented FIM process uses high-speed Nexa3D printers and xMOLD resin to print injection molding tools that are compatible with thousands of off-the-shelf injection molding materials, including reinforced high-performance feedstocks. The process reduces design, iteration, and validation cycles using end-product materials to a matter of hours rather than weeks.
Designers and makers that use the Precious Plastic machines are repurposing them to make items needed by local health care workers.
"However, as long as the items can be disinfected, I see no reason why they would need to be incinerated, and instead could be cleaned, shredded and recycled into one of Precious Plastics other opensource products."
Design input collected from the first tests was integrated in a second iteration that took only a couple of hours to complete. By contrast, conventional metal tooling would have taken more than six weeks to design and procure, and the adjustments needed for the second iteration would have taken an in-house tool-shop a week to complete.
A supplier of development and manufacturing services to medical device OEMs used Freeform Injection Molding from Nexa3D to accelerate time-to-market and slash prototyping costs for a complex silicone-based IV device. SPT Vilecon explained the process in a recent press release.
Infection control guidelines mean PPE must be disposed of after use, Dickens said Precious Plastic could offer a way to recycle any discarded plastic.
"No official body has approved our designs for medical use at this time, however, several hospitals around the world – including those in Spain – are currently using them," said Dickens.
"To make the items the plastic is heated to over 200 degrees Celsius which sterilises the plastic and it has previously been cleaned," he explained.
Shredder machines take sorted plastic waste and turn it back into useable flakes of plastic. Separate machines, including an injection moulder, an extruder or a rotation moulder, turn the flakes back into useful objects.
Robust and valid prototyping and verification are key to minimizing cost, time, and risk factors in developing medical devices, said SPI Vilecon. FIM is a new toolbox for medical device companies seeking to accelerate their innovation and obtain early verification of part performance and moldability, added the company.
A quarterly newsletter rounding up a selection of recently launched products by designers and studios, published on Dezeen Showroom.
Groups in Germany, Spain, Greece, Austria and Switzerland are using the open-source machines, which shred and remould old plastic, to make face shields, masks for ventilators and handles that allow the user to open a door without touching it.
Precious Plastic La Safor and Precious Plastic Gran Canaria have been making and sharing designs for visors that sit on the forehead and hold plastic shields over the wearer's face.
A quarterly newsletter rounding up a selection of recently launched products by designers and studios, published on Dezeen Showroom.
Sent every Thursday and containing a selection of the most important news highlights. Plus occasional updates on Dezeen’s services and invitations to Dezeen events.
GETTING A QUOTE WITH LK-MOULD IS FREE AND SIMPLE.
FIND MORE OF OUR SERVICES:
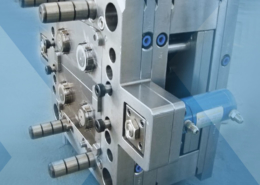
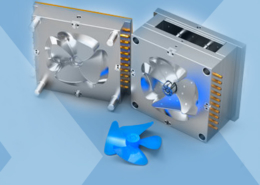
Plastic Molding

Rapid Prototyping
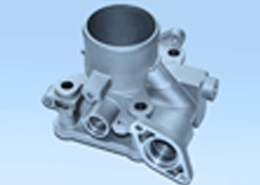
Pressure Die Casting
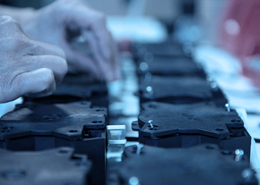
Parts Assembly
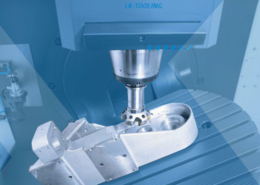