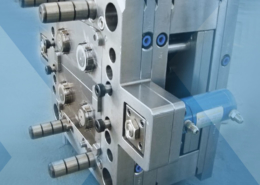
Protolabs CEO Discusses the Digital Age of Manufacturing - short run injection m
Author:gly Date: 2024-09-30
In addition to providing extensive industry news coverage, Metal AM magazine is known for exclusive, in-depth articles and technical reports.
When producing the tooling for a medical diagnostic housing, Mantle’s technology allowed Westec to cut the tooling cost in half by reducing the number of active operation hours on the inserts from 40 hours to 10. The tools were used to mould TPE.
“Many of these hires are younger people for whom this is their first real job. We give them mostly unskilled and semi-skilled jobs as a packer/inspector, material handler or automation operator. But we also get some skilled workers—welders, heavy equipment mechanics, licensed forklift operators. We even had a teacher and an architect.”
In this collection of content, we provide expert advice on welding from some of the leading authorities in the field, with tips on such matters as controls, as well as insights on how to solve common problems in welding.
O’Leary has encouraged other manufacturers to follow his example, with some (limited) success. “I always preach and promote this program. I’ve seen how it changes lives.”
Don't miss any new issue of Metal AM magazine, and get the latest industry news. Sign up to our twice weekly newsletter.
Nicolet Plastics has adopted Mantle’s metal Additive Manufacturing to produce steel production tooling in prototyping time and deliver moulded parts to customers more quickly. The company recently used an AM machine from Mantle to produce production tooling for customer Gamber-Johnson. By additively manufacturing three inserts, Nicolet reduced toolmaker time from 180 hours to 12.5 hours and reduced the time to produce the first moulded parts samples from six to two weeks. Mantle produced inserts that were 95% complete and required only minor finishing before moulding began.
While the major correction in PP prices was finally underway, generally stable pricing was anticipated for the other four commodity resins.
This family-run firm fills a specialized niche with a culture of innovation and environmental stewardship that realizes the dreams of its founders, its employees and its customers.
“Tooling is the base of our company,” stated Tammy Barras, president of Westec Plastics. “Without quality tooling, we can’t produce quality parts, but it’s getting harder and harder to find quality tool makers. Using Mantle’s technology, we can complete up to 70% of the job, and have our toolmakers handle the specialised steps that only a human can do. We need to take advantage of this new technology. With Mantle, we can provide our customers a service they can’t get anywhere else.”
Discover suppliers of these and more in our comprehensive advertisers’ index and buyer’s guide, available in the back of Metal AM magazine.
Exhibitors and presenters at the plastics show emphasized 3D printing as a complement and aid to more traditional production processes.
Mold maintenance is critical, and with this collection of content we’ve bundled some of the very best advice we’ve published on repairing, maintaining, evaluating and even hanging molds on injection molding machines.
Successfully starting or restarting an injection molding machine is less about ticking boxes on a rote checklist and more about individually assessing each processing scenario and its unique variables.
Introduced by Zeiger and Spark Industries at the PTXPO, the nozzle is designed for maximum heat transfer and uniformity with a continuous taper for self cleaning.
John Sewell, CEO of CKS Packaging (center), with brothers Scott, co-COO in charge of operations (left), and Drew, co-COO for sales. Their Second Chance program for low-level offenders and recovered drug addicts has produced long-term employees even at the managerial level. (Photo: CKS Packaging)
Mantle, San Francisco, California, USA, has highlighted two recent injection moulding customers which have successfully adopted its technology to automate their toolmaking processes. Nicolet Plastics and Westec Plastics both serve the medical device market and will implement Mantle’s technology to reduce the time and labour required to make precise injection mould tooling components.
The Plastics Industry Association (PLASTICS) has released final figures for NPE2024: The Plastics Show (May 6-10; Orlando) that officially make it the largest ever NPE in several key metrics.
Across all process types, sustainability was a big theme at NPE2024. But there was plenty to see in automation and artificial intelligence as well.
The aim of this presentation is to guide you through the factors and the numbers that will help you determine if a robot is a smart investment for your application. Agenda: Why are you considering automation? What problems are you trying to solve? How and why automation can help Crunch the numbers and determine the ROI
Ultradent's entry of its Umbrella cheek retractor took home the awards for Technical Sophistication and Achievement in Economics and Efficiency at PTXPO.
Metal AM magazine, published quarterly in digital and print formats, is read by a rapidly expanding international audience.
“Do well by doing good” is advice often attributed to Benjamin Franklin — a directive characteristically both moral and practical. The briefest internet search will reveal that this principle is integral to today’s concepts of sustainable management, yielding references to McKinsey, Harvard Business Review, Penn Wharton, Forbes, and so on. By chance, I recently happened upon two plastics blow molders who have taken it to heart, with good results for their communities and their companies.
Westec Plastics Corporation is a full-service plastic injection moulder which has adopted Mantle’s Additive Manufacturing technology to increase its tooling capacity without hiring on toolmakers. Mantle’s technology enables the company to produce H13 tool steel inserts anywhere from 75-95% complete with minimal time from Westec’s toolmakers.
“We let them know we have a vacancy, and they’ll look for three candidates that we can interview. They’ve known us for 20 years, so they know who would be a good fit with us. The beauty part is that they offer us pre-qualified candidates.”
Meredith-Springfield thrives on technically difficult blow molding jobs that others avoid. Its latest pioneering effort is pushing the limits in the new field of EPET.
In this three-part collection, veteran molder and moldmaker Jim Fattori brings to bear his 40+ years of on-the-job experience and provides molders his “from the trenches” perspective on on the why, where and how of venting injection molds. Take the trial-and-error out of the molding venting process.
Gifted with extraordinary technical know how and an authoritative yet plain English writing style, in this collection of articles Fattori offers his insights on a variety of molding-related topics that are bound to make your days on the production floor go a little bit better.
“I sincerely appreciate this honor,” O’Leary said at the ceremony, but what’s more important to me is the impact this program has on so many lives. It doesn’t just benefit ex-offenders, but also their families and communities. People make mistakes, and giving them a chance to turn their lives around is very important to me. We’re proud to have helped hundreds of formerly incarcerated people in the last 20 years to transition back into the community with gainful employment.”
In a subsequent phone conversation, I asked O’Leary how the process works. He credited Hampden County in Western Massachusetts as having “the most innovative and progressive program — and one of the lowest recidivism rates — in the country.” He explained, “It starts with their first day in jai. They can’t just sit in their cell. They must engage in education, vocational training, or some constructive activity for at least 40 hours a week.”
Additive technology creates air pockets in film during orientation, cutting down on the amount of resin needed while boosting opacity, mechanical properties and recyclability.
Say “manufacturing automation” and thoughts immediately go to the shop floor and specialized production equipment, robotics and material handling systems. But there is another realm of possible automation — the front office.
Sustainability continues to dominate new additives technology, but upping performance is also evident. Most of the new additives have been targeted to commodity resins and particularly polyolefins.
Thousands of people visit our Supplier Guide every day to source equipment and materials. Get in front of them with a free company profile.
While prices moved up for three of the five commodity resins, there was potential for a flat trajectory for the rest of the third quarter.
Plastics Technology’s Tech Days is back! Every Tuesday in October, a series of five online presentations will be given by industry supplier around the following topics: Injection Molding — New Technologies, Efficiencies Film Extrusion — New Technologies, Efficiencies Upstream/Downstream Operations Injection Molding — Sustainability Extrusion — Compounding Coming out of NPE2024, PT identified a variety of topics, technologies and trends that are driving and shaping the evolution of plastic products manufacturing — from recycling/recyclability and energy optimization to AI-based process control and automation implementation. PT Tech Days is designed to provide a robust, curated, accessible platform through which plastics professionals can explore these trends, have direct access to subject-matter experts and develop strategies for applying solutions in their operations.
I first encountered the phrase “second chance” about a year ago in talking with John and Drew Sewell, two of three brothers in the second generation running family-owned CKS Packaging. Based in Atlanta, the firm has two dozen locations nationwide with over 400 blow molding machines and employing around 3000 people.
In this collection of articles, two of the industry’s foremost authorities on screw design — Jim Frankand and Mark Spalding — offer their sage advice on screw design...what works, what doesn’t, and what to look for when things start going wrong.
Multiple speakers at Molding 2023 will address the ways simulation can impact material substitution decisions, process profitability and simplification of mold design.
While prices moved up for three of the five commodity resins, there was potential for a flat trajectory for the rest of the third quarter.
When, how, what and why to automate — leading robotics suppliers and forward-thinking moldmakers will share their insights on automating manufacturing at collocated event.
After successfully introducing a combined conference for moldmakers and injection molders in 2022, Plastics Technology and MoldMaking Technology are once again joining forces for a tooling/molding two-for-one.
Formnext Chicago is an industrial additive manufacturing expo taking place April 8-10, 2025 at McCormick Place in Chicago, Illinois. Formnext Chicago is the second in a series of Formnext events in the U.S. being produced by Mesago Messe Frankfurt, AMT – The Association For Manufacturing Technology, and Gardner Business Media (our publisher).
technotrans says climate protection, energy efficiency and customization will be key discussion topics at PTXPO as it displays its protemp flow 6 ultrasonic eco and the teco cs 90t 9.1 TCUs.
“We also get some post-release offenders on probation with an ankle bracelet. Either way, Corrections provides regular monitoring and supervision for the first six months to see that everything is working out.
Last month, Mel O’Leary, president and CEO of Meredith-Springfield Associates, Inc. (MSA) in Ludlow, Mass., was honored by the Hampden County Sheriff’s Office’s All-Inclusive Support Services (AISS) for his two decades as a “second-chance” employer in collaboration with AISS. O’Leary, 69, co-founded MSA, which will celebrate its 40th anniversary this year. I interviewed him for a feature profile of his company, which specializes in bottles and technical articles made by extrusion blow and injection-blow molding, in our March 2019 issue. The firm operates 14 blow molders and employs around 100 people.
Processors with sustainability goals or mandates have a number of ways to reach their goals. Biopolymers are among them.
“As an injection moulder, Mantle allows us to bring additional tool production in-house and increase the complexity of the tools and inserts we manufacture. We will significantly reduce the time it takes to produce production-quality tools and be able to start production in weeks versus months,” stated Tony Cavalco, CEO, Nicolet Plastics CEO.
In this collection, which is part one of a series representing some of John’s finest work, we present you with five articles that we think you will refer to time and again as you look to solve problems, cut cycle times and improve the quality of the parts you mold.
August 29-30 in Minneapolis all things injection molding and moldmaking will be happening at the Hyatt Regency — check out who’s speaking on what topics today.
Resin drying is a crucial, but often-misunderstood area. This collection includes details on why and what you need to dry, how to specify a dryer, and best practices.
Join Wittmann for an engaging webinar on the transformative impact of manufacturing execution systems (MES) in the plastic injection molding industry. Discover how MES enhances production efficiency, quality control and real-time monitoring while also reducing downtime. It will explore the integration of MES with existing systems, emphasizing compliance and traceability for automotive and medical sectors. Learn about the latest advancements in IoT and AI technologies and how they drive innovation and continuous improvement in MES. Agenda: Overview of MES benefits What is MES? Definition, role and brief history Historical perspective and evolution Longevity and analytics Connectivity: importance, standards and integration Advantages of MES: efficiency, real-time data, traceability and cost savings Emerging technologies: IoT and AI in MES
Join Engel in exploring the future of battery molding technology. Discover advancements in thermoplastic composites for battery housings, innovative automation solutions and the latest in large-tonnage equipment designed for e-mobility — all with a focus on cost-efficient solutions. Agenda: Learn about cutting-edge thermoplastic composites for durable, sustainable and cost-efficient battery housings Explore advanced automation concepts for efficient and scalable production See the latest large-tonnage equipment and technology innovations for e-mobility solutions
Join this webinar to explore the transformative benefits of retrofitting your existing injection molding machines (IMMs). Engel will guide you through upgrading your equipment to enhance monitoring, control and adaptability — all while integrating digital technologies. You'll learn about the latest trends in IMM retrofitting (including Euromap interfaces and plasticizing retrofits) and discover how to future-proof your machines for a competitive edge. With insights from industry experts, it'll walk you through the decision-making process, ensuring you make informed choices that drive your business forward. Agenda: Maximize the value of your current IMMs through strategic retrofitting Learn how to integrate digital technologies to enhance monitoring and control Explore the benefits of Euromap interfaces and plasticizing retrofits Understand how retrofitting can help meet new product demands and improve adaptability Discover how Engel can support your retrofitting needs, from free consultations to execution
Mel O’Leary, president and CEO of blow molder Meredith-Springfield Associates, was recently honored for hiring hundreds of people in two decades of collaborating with Massachusetts’ Hampden County Sheriff’s Department’s second-chance employment program for low-level offenders. (Photo: Matthew Naitove)
MSA usually hires pre-release offenders with three to six months left on their jail sentence. The Corrections Dept. provides a bus for transportation to and from our plant (only three miles from the county jail) at the beginning and end of shift.
John Sewell, CEO, cites the company’s policy of “celebrating the dignity of every human life. We treat our employees with dignity and respect. In return, they would walk through a wall for us. Some employees have been with the company for 30, 40 and even 50 years. “We have fourth-generation employees in the same family working here.” This extraordinary loyalty has helped the company deal with labor shortages, especially during the recent pandemic. “We’re like everyone else in needing more workers. But when we’re down a few people due to sickness or otherwise, everyone chips in to make up for it.”
“We printed up the inserts and did a little bit of final fitting here and there, and we were able to get it in the press and start moulding parts relatively quickly,” stated Eric Derner, Nicolet Plastics’ Applications Engineer. “We only had about 10 hours worth of secondary operations and final fitting we had to do. Our tool maker was a little bit pessimistic at first, but when I came in that Friday to ask how everything went, he was almost jumping up and down for joy.”
Mike Sepe has authored more than 25 ANTEC papers and more than 250 articles illustrating the importance of this interdisciplanary approach. In this collection, we present some of his best work during the years he has been contributing for Plastics Technology Magazine.
Average tenure of these second-chance hires is about six months—but that’s the same as, or better than, other entry-level unskilled workers, O’Leary says. “We have zero turnover at the technician level and above—but below that level, it’s a revolving door. We have 50% annual turnover no matter what we pay or what we do. Availability of some labor through Corrections provides us relief from these hiring difficulties.”
Take a deep dive into all of the various aspects of part quoting to ensure you’ve got all the bases—as in costs—covered before preparing your customer’s quote for services.
Across the show, sustainability ruled in new materials technology, from polyolefins and engineering resins to biobased materials.
Some second-chance hires have stayed with MSA for up to 15 years. “One even left and came back,” O’Leary recalls. These longer-term successes include one woman supervisor, two warehouse forklift operators, as well as machine mechanics and automation operators.
In a time where sustainability is no longer just a buzzword, the food and beverage packaging industry is required to be at the forefront of this innovation. By adopting circular packaging processes and solutions, producers can meet regulatory requirements while also satisfying consumer demand and enhancing brand reputation. Join Husky to learn more about the broader implications of the circular economy — as well as how leading brands are leveraging this opportunity to reduce costs, increase design flexibility and boost product differentiation. Agenda: The cost and operational benefits of embracing circularity Key materials in circular packaging — including rPET and emerging bioplastics How to design a circular food and beverage package Strategies for selecting sustainable closures to future-proof packaging solutions Optimization and streamlining of production processes for enhanced efficiency How Husky Technologies can enable your sustainable success
Two blow molders with long-standing programs of hiring formerly incarcerated low-level offenders have helped these individuals re-enter their communities and have benefited from an additional resource during chronic labor shortages.
Plastics Technology covers technical and business Information for Plastics Processors in Injection Molding, Extrusion, Blow Molding, Plastic Additives, Compounding, Plastic Materials, and Resin Pricing. About Us
“We’re in regular communication with the Sheriff’s Office. They have a whole staff at the Corrections Dept. just to find employment for pre-release and post-release offenders. This is for low-level offenders who have shown good behavior.
Despite price increase nominations going into second quarter, it appeared there was potential for generally flat pricing with the exception of a major downward correction for PP.
Core Technology Molding turned to Mold-Masters E-Multi auxiliary injection unit to help it win a job and dramatically change its process.
Reach a truly international audience that includes component manufacturers, end-users, industry suppliers, analysts, researchers and more.
Making something out of (almost) nothing is an ‘eye opener’ for youngsters in their first exposure to plastics processing.
Second quarter started with price hikes in PE and the four volume engineering resins, but relatively stable pricing was largely expected by the quarter’s end.
Learn about sustainable scrap reprocessing—this resource offers a deep dive into everything from granulator types and options, to service tips, videos and technical articles.
This month’s resin pricing report includes PT’s quarterly check-in on select engineering resins, including nylon 6 and 66.
The free to access Metal Additive Manufacturing magazine archive offers unparalleled insight into the world of metal Additive Manufacturing from a commercial and technological perspective through:
Join KraussMaffei for an insightful webinar designed for industry professionals, engineers and anyone interested in the manufacturing processes of PVC pipes. This session will provide a comprehensive understanding of the technology behind the production of high-quality PVC pipes: from raw material preparation to final product testing. Agenda: Introduction to PVC extrusion: overview of the basic principles of PVC pipe extrusion — including the process of melting and shaping PVC resin into pipe forms Equipment and machinery: detailed explanation of the key equipment involved — such as extruders, dies and cooling systems — and their roles in the extrusion process Process parameters: insight into the critical process parameters like temperature, pressure and cooling rates that influence the quality and consistency of the final PVC pipes Energy efficiency: examination of ways to save material and energy use when extruding PVC pipe products
“These hires are not treated any differently from regular employees,” O’Leary says. “They get the same pay, raises and reviews. We deposit their paychecks at the jail, which deducts for room and board and gives a weekly cash allowance of $25 to the workers. The rest is placed in a bank deposit for the workers until they are released.
Mantle uses its proprietary TrueShape technology – a hybrid material extrusion (MEX), CNC and sinter-based process. The system includes its P-200 Additive Manufacturing machine, built on a CNC platform, that integrates building and machining to produce parts with the accuracy and surface finish required for tooling. The P-200 machine has a build volume of 200 mm x 200 mm x 150 mm.
Mixed in among thought leaders from leading suppliers to injection molders and mold makers at the 2023 Molding and MoldMaking conferences will be molders and toolmakers themselves.
The company’s Second Chance hires include shift supervisors, technicians and even a plant manager. “We’re starting a veterans outreach program now,” Drew adds.
Close to 300 of those employees came to CKS through the company’s Second Chance program started by v.p. of manufacturing Lloyd Martin. Says Drew Sewell, COO for sales, “We hire out of prison when nobody else will — nonviolent, non-sex offenders. We don’t judge.” In addition, the company offers a rehab program for people who want to kick alcohol or drug addiction. “After a year in the program we will hire them,” Drew says.
“Information automation” is one of the keys to running a successful custom blow molding business for Meredith-Springfield Associates.
While the melting process does not provide perfect mixing, this study shows that mixing is indeed initiated during melting.
Our audience includes component manufacturers, end-users, materials and equipment suppliers, analysts, researchers and more.
Discover how artifical intelligence is revolutionizing plastics processing. Hear from industry experts on the future impact of AI on your operations and envision a fully interconnected plant.
This Knowledge Center provides an overview of the considerations needed to understand the purchase, operation, and maintenance of a process cooling system.
GETTING A QUOTE WITH LK-MOULD IS FREE AND SIMPLE.
FIND MORE OF OUR SERVICES:
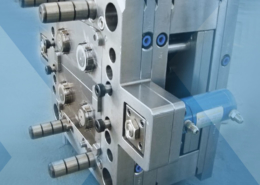
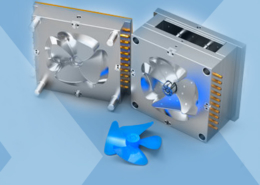
Plastic Molding

Rapid Prototyping
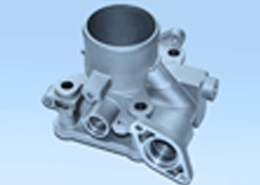
Pressure Die Casting
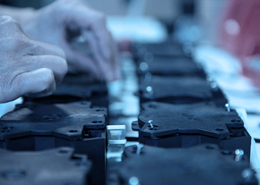
Parts Assembly
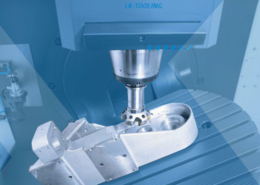