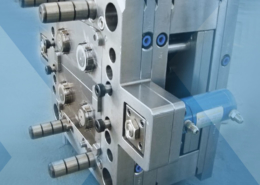
Prices of PE, PP, PS, PVC Drop - pvc injection price
Author:gly Date: 2024-09-30
Rodrigues, A. C. (2007). Impactos socioambientais dos resíduos de equipamentos elétricos e eletrônicos : estudo da cadeia pós-consumo no Brasil (Dissertation/Master's thesis). Universidade Metodista de Piracicaba, Piracicaba, Brazil.
For Bcomp, Wacht says that this project has been “a perfect example to show the design freedom you have thanks to this process. When you think about the potential of this technology, you can see how it could be used for an even more complex shape, such as in a supercar interior or in larger bodywork components.”
In this three-part collection, veteran molder and moldmaker Jim Fattori brings to bear his 40+ years of on-the-job experience and provides molders his “from the trenches” perspective on on the why, where and how of venting injection molds. Take the trial-and-error out of the molding venting process.
After extrustion, injection was carried out to obtain test speciments for the tensile, flexural, and impact strength tests, using an Arburg Allrounder injector with an 85 kg/h production capacity and five temperature zones. The injection profile used is presented in Table 2.
First iteration: Carbon fiber/epoxy. The initial carbon fiber/epoxy brake disc cover successfully proved out the technology for end-use parts. From there, KTM Technologies went back to the drawing board to use even more sustainable materials.
Both the virgin and e-waste polymers were extruded six times, that is, submitted to six reprocessing cycles. It is important to note that the HIPS waste samples, that is, all the different colored flakes, were extruded together to comply with the minimum amount needed for processing 6 times. The extruder used (Teck Tril DCT-20) has a production capacity of 10–20 kg/h and nine temperature zones, and the testing conditions were established based on recommendations in the technical specifications for the respective virgin polymers (Formosa Chemicals and Fibre Corporation, 2021; Innova, 2021), as shown in Table 2. The material was extruded in a continuous cylindrical filament, cooled in water at ambient temperature and then granulated. Approximately 1.0 kg of pellets were obtained per cycle for subsequent assessment of the properties of the reprocessed materials.
Comparison between the first and sixth cycles for virgin HIPS and HIPS e-waste (Figure 6H) demonstrates that the virgin polymer tends to degrade more with reprocessing in the region of the butadiene group. This result can be analyzed in conjunction the MFI findings for HIPSv, whereby there was a greater increase in MFI in the first cycle, which may be a characteristic of decreased molar mass due to degradation.
Wäger, P. A., and Hischier, R. (2015). Life cycle assessment of post-consumer plastics production from waste electrical and electronic equipment (WEEE) treatment residues in a Central European plastics recycling plant. Sci. Tot. Environ. 529, 158–167. doi: 10.1016/j.scitotenv.2015.05.043
Introduced by Zeiger and Spark Industries at the PTXPO, the nozzle is designed for maximum heat transfer and uniformity with a continuous taper for self cleaning.
Silva, C. E., Silva, L. P., Edwards, H. G. M., and De Oliveira, L. F. C. (2006). Diffuse reflection FTIR spectral database of dyes and pigments. Anal. Bioanal. Chem. 386, 2183–2191. doi: 10.1007/s00216-006-0865-8
However, with the carbon fiber version of the brake disc cover, “it’s another game,” Wacht says, “because carbon fiber is very energy-intensive to produce. Carbon fiber makes absolute sense to recycle.” Depending on the specific recycling method, the energy consumption that goes into recycling carbon fiber generally still results in a lower overall carbon footprint for the material, he notes.
Plastics Technology covers technical and business Information for Plastics Processors in Injection Molding, Extrusion, Blow Molding, Plastic Additives, Compounding, Plastic Materials, and Resin Pricing. About Us
Maximum degradation temperatures (Tmax) for reprocessed ABSv and ABSw ranged from 402 to 410°C and 410 to 416°C, respectively, with the following values obtained for ABSv: ABSv0 = 409°C; ABSv1 = 409°C; ABSv2 = 407°C; ABSv3 = 408°C; ABSv4 = 408°C; ABSv5 = 402°C; and ABSv6 = 410°C, and for ABSw: ABSw0 = 415°C; ABSw1 = 417°C; ABSw2 = 412°C; ABSw3 = 412°C; ABSw4 = 411°C; ABSw5 = 411°C; and ABSw6 = 413°C.
Citation: Teixeira FdSM, Peres ACdC and Pacheco EBAV (2023) Mechanical recycling of acrylonitrile-butadiene-styrene copolymer and high impact polystyrene from waste electrical and electronic equipment to comply with the circular economy. Front. Sustain. 4:1203457. doi: 10.3389/frsus.2023.1203457
Luna, C. B. B., Gomes, F. B. C., Siqueira, D. D., and Araújo, E. M. (2019). Influence of thermo-oxidative aging on the mechanical and yellowing properties of polystyrene blends with recycled styrene-butadiene rubber (SBR). Rev. Mater. 24, 1–13. doi: 10.1590/s1517-707620190003.0729
Flexural strength testing (Emic DL3000) was tested according to ASTM D790-17 (ASTM International, 2017), with 52 cm between grips and test specimens measuring 127 mm long, 12 mm wide, and 3.2 mm thick. Six test specimens were used for each composition and testing was carried out on a universal testing machine.
Arráez, F. J., Arnal, M. L., and Müller, A. J. (2019). Thermal degradation of high-impact polystyrene with pro-oxidant additives. Polym. Bull. 76, 1489–1515. doi: 10.1007/s00289-018-2453-4
Flexural strength was analyzed for virgin and ABS and HIPS e-waste polymers submitted to six reprocessing cycles yielding the following data: flexural strength, elastic modulus and maximum flexural stress. Maximum flexural stress is the stress applied to the center of the test specimen needed to deform it.
Karahaliou, E. K., and Tarantili, P. A. (2009). Stability of ABS compounds subjected to repeated cycles of extrusion processing. Polym. Eng. Sci. 49, 2269–2275. doi: 10.1002/pen.21480
Mold maintenance is critical, and with this collection of content we’ve bundled some of the very best advice we’ve published on repairing, maintaining, evaluating and even hanging molds on injection molding machines.
Virgin HIPS (HIPS825) was supplied by Innova and virgin ABS (AF3560) by Formosa Chemicals & Fibre Corporation (TAIRILAC®). Both virgin polymers are indicated for the production of EEE. The ABS and HIPS from WEEE were provided by two different recyclers, both located in the State Rio de Janeiro state (RJ), Brazil, and obtained from different types of e-waste:
Learn about sustainable scrap reprocessing—this resource offers a deep dive into everything from granulator types and options, to service tips, videos and technical articles.
Energy consumption and solid waste generation were quantified in reprocessing to obtain an environmental monitoring of ABS and HIPS recycling. Energy consumption during extrusion and injection (Figure 2) was measured using a Wattmeter equipped with a current and voltage sensor. The device makes the calculation internally and sends the instantaneous power data collected to a database file under a certain periodicity (Becker Junior et al., 2017). All solid residues generated in the process (extrusion residues, purges, and burrs) were quantified on a precision scale.
Plastic waste is considered a resource capable of replacing virgin materials (Huysveld et al., 2019), given the minimum technical requirements for the same application; or to be used in the manufacture of a product with properties that differ from those of the original material. Both cases involve minimal use of new resources (Xavier et al., 2021).
Klein (2009) studied the effect of thermomechanical and photooxidative degradation of ABS and found that the reduction of C=C bonds in the elastomeric phase suggests possible degradation of the polymer, whose bands related to out-of-plane angular vibration are more sensitive than in-plane angular absorption of C=C bonds. Other authors (Luna et al., 2019) also reported that rubber degradation is associated with molecular scission, which results in smaller chains and a larger number of chain terminals and/or cross-linking, forming a highly bonded network.
The original contributions presented in the study are included in the article/supplementary material, further inquiries can be directed to the corresponding author.
In the light of the above, this study aimed to investigate the mechanical reprocessing of ABS and HIPS from e-waste compared with the processing of virgin material to assess the possibility of their reintroduction or not to the same production cycle.
TGA curves and derivatives for virgin ABS and ABS e-waste reprocessed up to 6 times showed a well-defined decomposition stage. The results obtained for the initial decomposition temperatures (Tonset) of virgin ABS and WEEE reprocessed up to 6 times showed very similar decomposition temperatures, with 378 to 384°C for reprocessed ABSv and 381 to 386° for reprocessed ABSw. The Tonset values for ABSv were ABSv0 = 382°C; ABSv1 = 382°C; ABSv2 = 379°C; ABSv3 = 381°C; ABSv4 = 381°C; ABSv5 = 378°C; ABSv6 = 384°C, and for ABSw: ABSw0 = 384°C; ABSw1 = 386°C; ABSw2 = 382°C; ABSw3 = 382°C; ABSw4 = 381°C; ABSw5 = 381°C; and ABSw6 = 382°C.
Ramesh, V., Biswal, M., Mohanty, S., and Nayak, S. K. (2014). Recycling of engineering plastics from waste electrical and electronic equipments: influence of virgin polycarbonate and impact modifier on the final performance of blends. Waste Manag. Res. 32, 379–388. doi: 10.1177/0734242X14528404
Flax fiber/epoxy and flax fiber/bio-based PA. For its second and third iterations of the brake disc cover, KTM Technologies used Bcomp flax fiber with epoxy (shown here) and flax fiber with a bio-based polyamide. Both versions of the cover won awards in 2022.
The ABS from tablet casings was ground in a knife mill equipped with an approximately 9.0 mm mesh sieve, resulting in plastic pieces smaller than 2.0 mm, denominated ground flakes. All the ABS flakes were black.
The Plastics Industry Association (PLASTICS) has released final figures for NPE2024: The Plastics Show (May 6-10; Orlando) that officially make it the largest ever NPE in several key metrics.
Once validated at the coupon level, the same tooling and part design as the original carbon fiber cover were used to manufacture new demonstrator covers.
This accelerated growth leads to increased generation of waste electrical and electronic equipment (WEEE or e-waste). Plastics are increasingly used in EEE, which has lowered production costs and resulted in lighter products that are more durable and easily molded when compared to other traditional materials (Tansel, 2017). EEE typically contain around 10 to 30% plastic (Wang and Xu, 2014). High impact polystyrene (HIPS) and acrylonitrile-butadiene-styrene copolymer (ABS) are the most representative polymers in this market (Dimitrakakis et al., 2009; Wäger and Hischier, 2015; Hirayama and Saron, 2018; Teixeira et al., 2021).
Ragaert, K., Delva, L., and Van Geem, K. (2017). Mechanical and chemical recycling of solid plastic waste. Waste Manag. 69, 24–58. doi: 10.1016/j.wasman.2017.07.044
Scaffaro, R., Botta, L., and Di Benedetto, G. (2012). Physical properties of virgin-recycled ABS blends: effect of post-consumer content and of reprocessing cycles. Eur. Polym. J. 48, 637–648. doi: 10.1016/j.eurpolymj.2011.12.018
As such, recycled polymer e-waste such as ABS and HIPS show considerable potential for returning to the same production cycle. Nevertheless, products made with ABSw and HIPSw can also be considered in an open-loop recycling approach. Thus, it is important to pursue more sustainable alternatives for increasing the useful life of plastic waste from electrical and electronic equipment to comply with the circular economy.
Recycling is an excellent option for a more environmentally correct destination for post-consumer plastics (Ragaert et al., 2017) and those from EEE. Recovering these plastics is vital and urgent from a human health, environmental, social and economic perspective considering, for example, saving space in landfills and energy in the extraction and processing of virgin materials, transport, expansion of social programs with digital inclusion and job creation in the supply chain of maintenance, and recycling activities (Rodrigues, 2007; Menikpura et al., 2014; Campolina et al., 2017; Teixeira et al., 2021).
The mass percentage of residue for the materials reprocessed at 600°C was 1% for all the ABSv samples and 4% for reprocessed ABSw materials. The higher value obtained for ABSw is likely due to the presence of inorganic material in its composition, such as pigments responsible for its black color.
No yellowing was observed in the reprocessed ABSw and HIPSw samples (Figure 5) since both of these polymers were black. Reprocessed HIPSw remained an opaque black through all six extrusions, becoming slightly brighter after injection of the pellets, whereas ABS waste pellets were considerably brighter than the original material from the second cycle onwards. This greater bightness was also observed in the virgin ABS pellet, which naturally exhibited this characteristic before processing.
Join Wittmann for an engaging webinar on the transformative impact of manufacturing execution systems (MES) in the plastic injection molding industry. Discover how MES enhances production efficiency, quality control and real-time monitoring while also reducing downtime. It will explore the integration of MES with existing systems, emphasizing compliance and traceability for automotive and medical sectors. Learn about the latest advancements in IoT and AI technologies and how they drive innovation and continuous improvement in MES. Agenda: Overview of MES benefits What is MES? Definition, role and brief history Historical perspective and evolution Longevity and analytics Connectivity: importance, standards and integration Advantages of MES: efficiency, real-time data, traceability and cost savings Emerging technologies: IoT and AI in MES
The variation in the mass of the polymeric materials was analyzed by TGA (TA Instruments, Q500), using a temperature ramp of 10°C/min from 25 to 600 °C under a nitrogen atmosphere, with a flow rate of 20 mL/min. The samples weighed around 17 mg and were placed in an open ceramic container. Mass loss vs. temperature curves and their derivatives were analyzed by differential thermogravimetry (DTG).
There was a blockage in the hopper during the first HIPSw extrusion cycle due to the size of the flakes (>5 mm). Larger flakes required greater force to rotate the screw. This lengthened the extrusion process because small amounts of the material had to be fed into the extruder manually, doubling the extrusion time to around 43 min per kilogram for the first cycle. Thus, it was concluded that for the extruder used in this study, flakes had to be smaller than 5 mm. Residence time for HIPS inside the extruder in this first cycle was longer than that of the other cycles.
With respect to the environmental aspect, energy consumption in the first extrusion cycle for HIPSw was 12% greater than that of the other five cycles. This is because the larger flake size (>5 mm) in cycle one made it difficult to feed HIPSw into the extruder. Comparison between extrusion and injection showed that the latter consumed 143% more energy, since the injector used is more powerful than the extruder. Injection generates a larger amount of solid waste, including runner and sprue, which can be ground and recycled again, representing an additional benefit.
The carbon fiber version of the brake disc cover is now available for the aftermarket and will be equipped on some special edition motorcycles beginning in 2023. About 5,000 CFRP covers will be produced annually for KTM’s MX and enduro full-size models, Heider says. The company says the natural fiber cover may be introduced into KTM’s PowerParts portfolio as an aftermarket option once tests are completed.
While prices moved up for three of the five commodity resins, there was potential for a flat trajectory for the rest of the third quarter.
*Correspondence: Flávia da Silva Müller Teixeira, flavia.smt@ima.ufrj.br; Elen Beatriz Acordi Vasques Pacheco, elen@ima.ufrj.br
Similar behavior was observed for ABSw, with a small variation (approximately 4%) across the six cycles. However, there was a 15% increase from the first to sixth extrusion cycle and approximately 10% for extrusion + injection (Table 6). Analysis of the standard deviations (0.2 g/10 min) after each cycle for extrusion and extrusion + injection also showed no variations, demonstrating that despite undergoing two types of processing, the MFI of ABSw shows that processing has little effect on the melt flow index ty of the material.
Across all process types, sustainability was a big theme at NPE2024. But there was plenty to see in automation and artificial intelligence as well.
TGA curves and derivatives for HIPSv and HIPSw reprocessed up to 6 times also indicated a decomposition stage. The Tonset of reprocessed HIPSv and HIPSw was 401–402°C and 395–396°C in all cycles, respectively. The maximum degradation temperatures for both HIPSv and HIPSw were 424°C-425°C. The mass percentage of residue at 600°C for HIPSv was 0.1–0.3% and around 1–3% for HIPSw. These findings indicate that both the virgin and WEEE polymeric materials showed good thermal stability, which remained practically unchanged even after six processing cycles.
Second quarter started with price hikes in PE and the four volume engineering resins, but relatively stable pricing was largely expected by the quarter’s end.
“The strategy driving the whole process on our side was to enable us to use these materials together, and to use each material for what it does best,” von Czarnecki explains. “That is, to use the thermoset for the mechanical properties where they were needed, and where the customer can see it to really appreciate [the flax fiber], and to use thermoplastic for functions such as ribs and integration of inserts, and by this we achieve the most cost-efficient design.”
“We don’t need a gluing step, or rivets or bolting or screwing. Directly out of the injection molding process we have a part that we can directly mount to the motorcycle,” Heider says.
Table 6 shows the MFI values of ABSV and ABSW after each extrusion cycle. The MFI was also analyzed after injection and increased for both polymers with each successive cycle. Comparison of MFI values between cycles showed a very small percentage variation.
Table 5 also shows the solid waste generated during the six reprocessing cycles for each polymeric material. The injection process generated the most residue (average of 289 and 291 g/kg processed for ABSv and ABSw, respectively), while extrusion produced an average of 39 (ABSv) and 36 g/kg (ABSw). Similarly, a larger amount of waste was generated during HIPS injection (323 g/kg for HIPSv and 296 g/kg for HIPSw) than extrusion (42 g/kg for HIPSv and 40 g/kg for HIPSw). The waste produced in injection molding corresponds to runner and sprue generated in each reprocessing cycle. These results confirm waste generation in each injection or extrusion cycle and that this residue can be ground and reprocessed, remaining within the circular economy.
The cover, a circular panel designed to mount to the wheels of a racing motorcycle to protect the brake system from debris or impact, was entered into the competition by flax fiber supplier Bcomp Ltd. (Fribourg, Switzerland) and built by KTM Technologies (Salzburg, Austria), the R&D and innovation unit of motorcycle manufacturer KTM AG (Mattighofen, Austria).
Resin drying is a crucial, but often-misunderstood area. This collection includes details on why and what you need to dry, how to specify a dryer, and best practices.
Copyright © 2023 Teixeira, Peres and Pacheco. This is an open-access article distributed under the terms of the Creative Commons Attribution License (CC BY). The use, distribution or reproduction in other forums is permitted, provided the original author(s) and the copyright owner(s) are credited and that the original publication in this journal is cited, in accordance with accepted academic practice. No use, distribution or reproduction is permitted which does not comply with these terms.
Plastics Technology’s Tech Days is back! Every Tuesday in October, a series of five online presentations will be given by industry supplier around the following topics: Injection Molding — New Technologies, Efficiencies Film Extrusion — New Technologies, Efficiencies Upstream/Downstream Operations Injection Molding — Sustainability Extrusion — Compounding Coming out of NPE2024, PT identified a variety of topics, technologies and trends that are driving and shaping the evolution of plastic products manufacturing — from recycling/recyclability and energy optimization to AI-based process control and automation implementation. PT Tech Days is designed to provide a robust, curated, accessible platform through which plastics professionals can explore these trends, have direct access to subject-matter experts and develop strategies for applying solutions in their operations.
Tensile testing (Emic DL3000) was performed in line with ASTM D638-10 (ASTM International, 2010b) on a universal testing machine, using type 1 test specimens (165 mm long, 12.6 mm wide, and 3.2 mm thick), a grip separation speed of 10 mm/min, maximum grip displacement of 90 cm and a 5 kN load cell.
Showing off multi-material joining, natural fiber composites. With three iterations in development and poised to go on the market, KTM Technologies’ new motorcycle brake disc covers demonstrate potential for its Conexus joining technology to combine thermoset parts with thermoplastics. Photo Credit, all images: KTM Technologies
With the new design, the goal was to develop a part with three layers. The top outer layer would be an epoxy thermoset-based composite to increase the overall impact resistance and stiffness of the part, and a bottom layer would be unreinforced thermoplastic that would be fitted with the metal insert, with the Conexus coupling layer in between joining the two halves together, acting as the third layer. The thermoset and thermoplastic layers ultimately overlap slightly — “but this isn’t for connecting,” Heider explains. The overlap protects the edges from moisture and wear over time.
Gorna, K., Hund, M., Vučak, M., Gröhn, F., and Wegner, G. (2008). Amorphous calcium carbonate in form of spherical nanosized particles and its application as fillers for polymers. Mater. Sci. Eng. A 477, 217–225. doi: 10.1016/j.msea.2007.05.045
Figure 5. Test specimens for tensile testing obtained by injection of ABS and HIPS, virgin and from e-waste, reprocessed six times.
Processing of the virgin and e-waste polymers was monitored by measuring electric energy consumption and the solid waste generated during the cycles. Table 5 shows the electric energy used during extrusion and injection, with around 0.7 kWh/kg consumed in each extrusion cycle for ABSv, ABSw and HIPSv, corresponding to 2.52 MJ/kg. This differs from the first HIPS e-waste extrusion cycle, which required more energy (5.47 MJ/kg). This is because of the feeding difficulties in this cycle due to flake size (>5 mm), with the resulting blockage doubling the molding time in relation to the remaining cycles, thereby increasing energy consumption.
This Knowledge Center provides an overview of the considerations needed to understand the purchase, operation, and maintenance of a process cooling system.
Visually, black, ivory, and gray HIPS e-waste predominated, which was confirmed via quantification and mass percentage assessment, as presented in Figure 3. Mass percent was calculated separately for HIPS and ABS. Colored HIPS % and black ABS % were calculated as a function of total HIPS and total ABS, respectively. These three colors accounted for 76% of the total mass of HIPS e-waste. Color sorting is a common procedure in the recycling industry for different colored products.
ASTM International (2013). D1238-13. Test Method for Melt Flow Rates of Thermoplastics by Extrusion Plastometer. doi: 10.1520/D.1238-13
While prices moved up for three of the five commodity resins, there was potential for a flat trajectory for the rest of the third quarter.
After successfully introducing a combined conference for moldmakers and injection molders in 2022, Plastics Technology and MoldMaking Technology are once again joining forces for a tooling/molding two-for-one.
It should also be noted that the laboratory-scale extruder used here is smaller than those found in recycling plants, meaning that limited flake size may not be an issue for recyclers. There were no feeding difficulties in HIPS reprocessing from the second extrusion cycle onwards, when 1 kg was processed in approximately 20 min, since in this phase the material was in pellet form.
The brake disc cover project originated as a way to demonstrate the Conexus technology, and is in serial production at KTM as a carbon fiber/epoxy version that features a metal insert directly joined to a thermoplastic component via injection molding. Based on this serial part and the processes and tools used to manufacture it, the more sustainable flax fiber/epoxy demonstrator presented at JEC World was built.
While the major correction in PP prices was finally underway, generally stable pricing was anticipated for the other four commodity resins.
Mike Sepe has authored more than 25 ANTEC papers and more than 250 articles illustrating the importance of this interdisciplanary approach. In this collection, we present some of his best work during the years he has been contributing for Plastics Technology Magazine.
Campolina, J. M., Sigrist, C. S. L., de Paiva, J. M. F., Nunes, A. O., and da Moris, S. V. A. (2017). A study on the environmental aspects of WEEE plastic recycling in a Brazilian company. Int. J. Life Cycle Assess. 22, 1957–1968. doi: 10.1007/s11367-017-1282-2
Ultradent's entry of its Umbrella cheek retractor took home the awards for Technical Sophistication and Achievement in Economics and Efficiency at PTXPO.
“Design for manufacture was key,” Heider notes. To be able to serially produce the covers, the manufacturing process had to be relatively fast, with part costs as low as possible. “We knew we wanted to produce an attractive optical part and give visibility to the hybrid construction, but we also needed a part that can be produced using known and approved processes, to give us the opportunity to make parts very quickly and efficiently,” he explains.
Wang, J., Li, Y., Song, J., He, M., Song, J., and Xia, K. (2015). Recycling of acrylonitrile-butadiene-styrene (ABS) copolymers from waste electrical and electronic equipment (WEEE), through using an epoxy-based chain extender. Polym. Degrad. Stab. 112, 167–174. doi: 10.1016/j.polymdegradstab.2014.12.025
Automotive molder ITW Deltar Fasteners found new life for the battered bolt holes on its machine platens with a solution that’s designed to last.
Currently, KTM Technologies is investigating several racing motorsports projects and exterior automotive non-structural parts using the Conexus technology. In addition, as demonstrated in a joint research project with Airbus’ Composite Technology Center (CTC, Stade, Germany) which focused on the use of Conexus technology with ultrasonic welding (see video below for a demonstration of this technology), one goal for Conexus is to enable smart and efficient manufacturing in emerging industries such as advanced air mobility (AAM).
Join Engel in exploring the future of battery molding technology. Discover advancements in thermoplastic composites for battery housings, innovative automation solutions and the latest in large-tonnage equipment designed for e-mobility — all with a focus on cost-efficient solutions. Agenda: Learn about cutting-edge thermoplastic composites for durable, sustainable and cost-efficient battery housings Explore advanced automation concepts for efficient and scalable production See the latest large-tonnage equipment and technology innovations for e-mobility solutions
Figure 6. FTIR spectra for: (A) virgin and e-waste ABS no reprocessed and reprocessed six times; (B) virgin and e-waste HIPS no reprocessed and reprocessed six times; (C) ABS e-waste reprocessed six times in the nitrile regions; (D) ABS e-waste in the first and sixth reprocessing cycles for the butadiene regions; (E) Comparative FTIR spectra of virgin and e-waste ABS from the first and sixth cycles in the nitrile group region; (F) Comparative FTIR spectra of virgin and e-waste ABS from the first and sixth cycles in the butadiene group region; (G) regions corresponding to the butadiene group of reprocessed HIPSv; (H) regions corresponding to the butadiene group of reprocessed HIPSw.
The brake disc cover project, and motorsports in general, is only the first step for Conexus technology, says von Czarnecki. “This enables the possibility to combine materials without bonding, increasing sustainability and reducing complexity in the process. It is offering a whole new range of applications.”
The melt flow index of virgin ABS increased by 11% from the first to the sixth extrusion cycle, but remained practically unchanged across six extrusion + injection cycles. For ABS e-waste, only impact strength was affected, showing a 14% decrease in cycle two, but then remained unchanged until cycle six.
In this collection, which is part one of a series representing some of John’s finest work, we present you with five articles that we think you will refer to time and again as you look to solve problems, cut cycle times and improve the quality of the parts you mold.
Strain at the yield point is similar for HIPSv and HIPSw (Table 7) after each reprocessing cycle, at around 2%. Additionally, Young's modulus, the yield point and elongation at break remained almost unchanged across the HIPS reprocessing cycles. However, HIPSw differed from HIPSv in terms of the elastic modulus, rupture point and elongation at break, corroborating the different grades of the two materials. HIPSw obtained a Young's modulus greater than 2,000 MPa, rupture point of approximately 29 MPa and 13% elongation at break, likely due to the presence of fillers, indicating that this material is harder and not as tough.
For speed, compression molding was chosen for the thermoset part, and injection molding for the thermoplastic part. “We designed the process for easy processability and low scrap,” Heider adds.
In a life cycle inventory (LCI), Campolina et al. (2017) found that extrusion of recycled ABS and HIPS consumed 6.76 and 7.03 MJ/kg, respectively. As shown in Table 5, injection consumed about 2.0 kWh/kg (7.0 MJ/kg) of energy, more than that used in extrusion, since the injector is more powerful (37.5 kW) than the extruder (5.5 kW). Becker Junior et al. (2017) reported the average energy consumption of eight injectors used to process polymeric materials such as polypropylene (PP) and ABS was 3.08 kWh/kg, regardless of the type of polymer. According to the authors, consumption varied from 1.25 to 5.38 kWh/kg depending on the production capacity, process settings, and mold types of the injector.
Mixed in among thought leaders from leading suppliers to injection molders and mold makers at the 2023 Molding and MoldMaking conferences will be molders and toolmakers themselves.
The stress vs. strain curves for virgin ABS and HIPS and reprocessed WEEE were typical of plastics and similar in shape. Both ABS and HIPS show linear behavior at the beginning of the curve, where there is a modulus of elasticity or Young's modulus (ε). As the polymer begins to experience strain, it transitions from elastic to plastic deformation at a point of maximum stress known as the yield point (θr), where yield point elongation (εr) can also be obtained. Strain continues until rupture (θy), when the curve slopes downward and elongation at break (εy) can be obtained. Table 7 presents the results for Young's modulus, stress and strain at Yield and break of virgin and ABS e-waste and virgin and HIPS e-waste.
Introduction: Acrylonitrile-butadiene-styrene copolymer (ABS) and high impact polystyrene (HIPS) are plastics typically found in waste electrical and electronic equipment (WEEE or e-waste). As such, recycling is a beneficial method for reintroducing polymeric materials from electrical and electronic equipment to the same production cycle. This study aimed to investigate mechanical recycling of ABS and HIPS from WEEE reprocessed six times, totaling 24 cycles.
August 29-30 in Minneapolis all things injection molding and moldmaking will be happening at the Hyatt Regency — check out who’s speaking on what topics today.
Formosa Chemicals Fibre Corporation (2021). Products. Available online at: https://en.fcfc-plastics.com/product.htm (acessed January 10, 2021).
The Conexus coupling layer is designed to have a lower melting temperature than the thermoplastic part in a given application, he explains. At the part’s EOL, if heat is introduced at the coupling layer’s melting temperature, the Conexus layer will melt and allow the thermoset and thermoplastic parts to be easily separated without damaging or melting either part.
The Tier One automotive supplier with compounding and blowmolding machine capabilities adds the 50-yr-old molder and moldmaker.
Becker Junior, A. M., Dias, R. O., Chiumento, G., Motta, F. L. U. L., Almeida, L. G. O., Kabe, Y. H. O., et al. (2017). Desenvolvimento de base de dados ambiental para a cadeia de transformação de plástico no Brasil: primeiros avanços. Rev. Latino-Americana em Avaliação do Ciclo Vida 1, 48–62. doi: 10.18225/lalca.v1iespecial.3072
Wang, R., and Xu, Z. (2014). Recycling of non-metallic fractions from waste electrical and electronic equipment (WEEE): a review. Waste Manag. 34, 1455–1469. doi: 10.1016/j.wasman.2014.03.004
Say “manufacturing automation” and thoughts immediately go to the shop floor and specialized production equipment, robotics and material handling systems. But there is another realm of possible automation — the front office.
The MFI of HIPS was 5.3 g/10 min, while the value recorded for HIPS e-waste, in which all the HIPS samples were combined, was 6.5 g/10 min (Figure 4). In general, the MFI of the HIPS e-waste samples showed greater homogeneity, despite their different origins. The different HIPS grades used in EEE include HIPS825 (MFI = 5.5), HIPS RC600 (MFI = 6.0), and HIPS RT441M (MFI = 6.5; Innova, 2021).
The original design of the cover involved a compression molded, carbon fiber/epoxy top layer joined via Conexus to an injection molded bottom layer made from a blend of polyamide 6 (PA6) and ABS (acrylonitrile butadiene styrene) from INEOS Styrolution (Frankfurt, Germany). KTM Technologies developed tooling for the thermoset part with partner Alba Tooling & Engineering GmbH (Forstau, Austria), and for the injection molding tool with Altendorfer Kunststofftechnik GmbH (Neureichenau, Germany).
Momanyi, J., Herzog, M., and Muchiri, P. (2019). Analysis of thermomechanical properties of selected class of recycled thermoplastic materials based on their applications. Recycling 4, 1–16. doi: 10.3390/recycling4030033
Brennan, L. B., Isaac, D. H., and Arnold, J. C. (2002). Recycling of acrylonitrile-butadiene-styrene and high-impact polystyrene from waste computer equipment. J. Appl. Polym. Sci. 86, 572–578. doi: 10.1002/app.10833
Bai, X., Isaac, D. H., and Smith, K. (2007). Reprocessing acrylonitrile-butadiene-styrene plastics: structure-property relationships. Polym. Eng. Sci. 47, 120–130. doi: 10.1002/pen.20681
Why not recycle or repurpose the flax fiber thermoset component? Johann Wacht, manager of motorsports and supercars at Bcomp, explains, “With recycling, you need to think about your base materials.” He claims that the company’s flax fiber materials are produced as CO2-negative materials, whereas any of today’s recycling methods would consume energy and result in a larger overall carbon footprint. “In this case, simply recovering energy from the natural fiber and epoxy [at the part’s EOL] is the better solution, because you can recuperate 80% of the energy stored in the material. It makes a lot of sense from a CO2 footprint perspective.”
In HIPSv, elastic modulus, maximum flexural stress and flexural strength were almost the same after the six cycles (Table 8). The results demonstrate that flexural properties remained almost unaltered after six processing cycles.
Silva et al. (2006) studied different pigments and dyes by FTIR and found that the Prussian Blue exhibited a band at around 2,083 cm−1 associated with nitrile. However, this band was not present in the spectra of the samples analyzed in the present study and as such, it was concluded that the nitrile peak (2,237 cm−1) may be attributed to the acrylonitrile in ABS.
Santana, R. C., and Manrich, S. (2002). Studies on thermo-mechanical properties of post-consumer high impact polystyrene in five reprocessing steps. Prog. Rubber Plast. Recycl. Technol. 18, 99–110. doi: 10.1177/147776060201800202
Across the show, sustainability ruled in new materials technology, from polyolefins and engineering resins to biobased materials.
Salari, D., and Ranjbar, H. (2008). Study on the recycling of ABS resins: simulation of reprocessing and thermo-oxidation. Iran. Polym. J. 17, 599–610.
Methods: Reprocessing was performed by extrusion and test specimens were obtained by injection. The technical aspects assessed before and after reprocessing were mechanical properties (tensile, flexural and impact strength), thermogravimetric analysis (TGA), Fourier-transform infrared spectroscopy (FTIR) and melt flow index (MFI), compared with those of reprocessed virgin polymeric materials. The environmental aspect was evaluated by monitoring energy consumption and solid waste generation during each reprocessing cycle.
Disclaimer: All claims expressed in this article are solely those of the authors and do not necessarily represent those of their affiliated organizations, or those of the publisher, the editors and the reviewers. Any product that may be evaluated in this article or claim that may be made by its manufacturer is not guaranteed or endorsed by the publisher.
The FTIR results for the eight different colored HIPS e-waste samples showed that the main bands corresponding to polystyrene and polybutadiene are similar to those of virgin HIPS. However, all the HIPSw samples have small peaks at around 3,700 cm−1 that were not observed for HIPSv. Peaks at this wavelength are characteristic of hydroxyl group vibrations, possibly from a common additive in EEE. The hydroxyl peak is more evident in the black, ivory, gray, and blue HIPSw samples, which exhibited a larger amount of residue in TGA, that is, they likely contain more carbonate. Calcium carbonate (CaCO3) is a common additive in thermoplastics (Gorna et al., 2008). Thermal decomposition of CaCO3 occurs between 700 and 800°C (Karunadasa et al., 2019); as such, the additive is in a solid state at the final temperature used in TGA.
The authors declare that the research was conducted in the absence of any commercial or financial relationships that could be construed as a potential conflict of interest.
Bokria, J. G., and Schlick, S. (2002). Spatial effects in the photodegradation of poly(acrylonitrile-butadiene-styrene): a study by ATR-FTIR. Polymer 43, 3239–3246. doi: 10.1016/S0032-3861(02)00152-0
According to Heider, the CO2 footprint of the materials is reduced by up to 60% by switching to flax fiber from carbon fiber. “We wanted to show that we can use our Conexus technology to produce aesthetic and performance parts on the one hand, and to be able to fulfill sustainability targets on the other hand. By using established manufacturing methods where we can easily implement other fibers or thermoplastic materials, we have an innovative joining technology ready for the market, which can adapt easily to the needs of every customer without the necessity to invest in additional machinery,” Heider says.
Pérez, J. M., Vilas, J. L., Laza, J. M., Arnáiz, S., Mijangos, F., Bilbao, E., et al. (2010). Effect of reprocessing and accelerated weathering on ABS properties. J. Polym. Environ. 18, 71–78. doi: 10.1007/s10924-009-0154-7
For HIPSw, yield and flexural strength decreased by 7 and 6%, respectively, from the third cycle onwards. The modulus of reprocessed HIPSw was 6% higher than that of HIPSv. As observed in FTIR, bands corresponding to the butadiene group (C=C bonds) in both ABS and HIPS declined after reprocessing, suggesting polymer degradation. Degradation due to heat, light or other factors breaks the double bonds of the butadiene group, which have less energy, and can cause cross-link formation, reducing molecular mobility and, consequently, increasing the stiffness of the polymers with successive reprocessing cycles.
After reprocessing, the virgin and e-waste materials were analyzed by FTIR, TGA, DSC, and MFI following the same procedures used for the original raw materials. The mechanical properties (tensile, flexural, and impact strength) of the reprocessed materials were also evaluated, using injected test specimens of material.
Multiple speakers at Molding 2023 will address the ways simulation can impact material substitution decisions, process profitability and simplification of mold design.
All claims expressed in this article are solely those of the authors and do not necessarily represent those of their affiliated organizations, or those of the publisher, the editors and the reviewers. Any product that may be evaluated in this article, or claim that may be made by its manufacturer, is not guaranteed or endorsed by the publisher.
When, how, what and why to automate — leading robotics suppliers and forward-thinking moldmakers will share their insights on automating manufacturing at collocated event.
MFI values for the virgin and e-waste polymers were measured in accordance with ASTM standard D1238-13 (ASTM International, 2013), using 3 g of material analyzed at 200°C under a standard mass of 5.0 Kg in a Dynisco LMI 4003 melt flow indexer.
Huysveld, S., Hubo, S., Ragaert, K., and Dewulf, J. (2019). Advancing circular economy benefit indicators and application on open-loop recycling of mixed and contaminated plastic waste fractions. J. Clean. Prod. 211, 1–13. doi: 10.1016/j.jclepro.2018.11.110
Comparison of the first reprocessing cycle for ABSw and ABSv showed a slight decline in peaks corresponding to nitrile and butadiene. However, the decline is more evident in the sixth cycle, indicated by the peaks of the butadiene group and nitrile presented in Figures 6E, F, suggesting possible degradation of the butadiene phase. According to Ramesh et al. (2014), the microstructure of the polymer facilitates thermal degradation. The tertiary carbons in the polybutadiene phase of ABS are responsible for hydrogen abstraction by oxygen, and as such, thermal energy will activate hydrogen abstraction by the oxidation reaction to initiate and accelerate degradation.
Despite price increase nominations going into second quarter, it appeared there was potential for generally flat pricing with the exception of a major downward correction for PP.
Production-ready. KTM Technologies plans to produce its carbon fiber and flax fiber composite brake disc covers commercially. Beyond motorsports, the company plans to use its now-proven Conexus technology for automotive and even urban air mobility (UAM) applications in the future.
For this part, KTM Technologies partnered with Akro-Plastic GmbH (Niederzissen, Germany), a company that specializes in plastic compounds and that recently introduced a product line of bio-based thermoplastics. Again, the teams began by testing materials at the coupon level, and for the SPE-presented part, decided to demonstrate the brake disc cover using Akro-Plastic’s Akromid Next 5.10 3 GF 30 glass fiber-filled PA6, chosen for its high bio-based content and higher mechanical properties due to the additional glass fiber. This version of the brake disc cover is said to enable up to 70% CO2 reduction for the materials used compared to the series model.
The JEC Award-winning flax fiber/epoxy part was only the first step toward demonstrating the use of sustainable materials for brake disc covers. In October 2022, KTM Technologies was awarded an SPE (Society of Plastics Engineers) Automotive Award in the “Body Exteriors” category for a new version of the cover that uses flax fiber in combination with a bio-based glass-filled polyamide.
Comparison between the first and sixth HIPSv processing cycles showed an increase of approximately 30% for extrusion (Table 6) greater than that observed for the other polymers. The MFI of HIPSv submitted to extrusion + injection increased by 12.9% from the second to the third cycle, 8.6% from the third to the fourth, and 5.3% from the fifth to the sixth, reaching 27% from the first to the sixth cycle (Table 6).
Stefan von Czarnecki, director of sales and business development at KTM Technologies, explains that the entire company is emphasizing sustainability initiatives, including manufacturing, part design and end-of-life (EOL) solutions, starting with R&D initiatives aimed to qualify and evaluate opportunities for series production. One of these initiatives was the creation of an innovative joining technology called Conexus, which the award-winning brake cover was designed to demonstrate.
In this case, the thermoplastic component could then be melted and reformed for additional uses, while the flax fiber component would ideally be pyrolyzed, with the energy recaptured for another use such as cement kiln coprocessing or waste-to-energy cogeneration plants.
For the carbon fiber-reinforced polymer (CFRP) and flax fiber covers, KTM Technologies ultimately demonstrated the technology on in-house specimen- and part-level tests to prove adhesion for the joined parts, impact resistance, UV resistance and more, according to the company’s internal quality standards. “Our parts go directly onto the motorcycle where they’re tested by actual riders,” Heider says. “We do mechanical tests on the component separately, then test real-world performance on the motorcycle.”
Figure 4 shows the MFI values of the virgin and ABS and HIPS e-waste. The melt flow index was measured to assess the reprocessing cycles. The MFI values obtained for ABSv and ABSw were 6.6 and 2.6 g/10 min. Scaffaro et al. (2012) recorded MFIs of 3.6 and 3.3 g/10 min for ABS from telephone waste and virgin polymeric material. ABSw appears to differ considerably from ABSv, both of which are used in EEE, demonstrating the diversity of this market. The virgin ABS polymers with MFI close to 2.6 g/10 min, such as ABS AF3560 (MFI = 6.0); ABS AG15A3 (MFI = 2.2); ABS AG15E3 (MFI = 2.1); ABS AG15E0 (MFI = 1.8), are used in different EEE applications, including calculators, telephones, and stereos, among others (Formosa Chemicals and Fibre Corporation, 2021).
Comparison of MFI values for HIPSw extrusion + injection with those for extrusion revealed increases of 19, 13, 10, and 14% for the first, fourth, fifth and sixth cycles, respectively.
Karunadasa, K. S. P., Manoratne, C. H., Pitawala, H. M. T. G. A., and Rajapakse, R. M. G. (2019). Thermal decomposition of calcium carbonate (calcite polymorph) as examined by in-situ high-temperature X-ray powder diffraction. J. Phys. Chem. Solids 134, 21–28. doi: 10.1016/j.jpcs.2019.05.023
Rahimi, M., Esfahanian, M., and Moradi, M. (2014). Effect of reprocessing on shrinkage and mechanical properties of ABS and investigating the proper blend of virgin and recycled ABS in injection molding. J. Mater. Process. Technol. 214, 2359–2365. doi: 10.1016/j.jmatprotec.2014.04.028
Hirayama, D., and Saron, C. (2015). Characterisation of recycled acrylonitrile-butadiene-styrene and high-impact polystyrene from waste computer equipment in Brazil. Waste Manag. Res. 33, 543–549. doi: 10.1177/0734242X15584845
Beigbeder, J., Perrin, D., Mascaro, J. F., and Lopez-Cuesta, J. M. (2013). Study of the physico-chemical properties of recycled polymers from waste electrical and electronic equipment (WEEE) sorted by high resolution near infrared devices. Resour. Conserv. Recycl. 78, 105–114. doi: 10.1016/j.resconrec.2013.07.006
Table 7. Young's modulus, stress, and strain at yield and break of virgin and e-waste ABS and virgin and e-waste HIPS reprocessed six times.
Gregorova, A. (2013). “Application of Differential Scanning Calorimetry to the characterization of biopolymers,” in Application of Calorimetry in a Wide Context - Applications of Calorimetry in a Wide Context - 4 Differential Scanning Calorimetry, Isothermal Titration Calorimetry and Microcalorimetry, Chapter 1, ed A. A. Elkordy (IntechOpen), 3–20. doi: 10.5772/53822
Discussion: The thermal, tensile and flexural properties of the virgin and post-consumer materials remained almost unchanged as the number of reprocessing cycles increased, indicating that these materials have the potential and properties for reintroduction into the same production cycle.
Teixeira, F. S. M., Peres, A. C. C., Gomes, T. S., Visconte, L. L. Y., and Pacheco, E. B. A. V. (2021). A review on the applicability of life cycle assessment to evaluate the technical and environmental properties of waste electrical and electronic equipment. J. Polym. Environ. 29, 1333–1349. doi: 10.1007/s10924-020-01966-7
As expected, differences were observed in the thermal stability of virgin and post-consumer polymers. The variation in degradation temperatures for the different colored HIPSw was also expected. For HIPSw of the same grade, the different pigments or dyes interact differently with the polymer matrix, increasing or hampering their degradation under heating. According to Saron and Felisberti (2006), pigments and dyes have different chemical structures and interaction between them and the polymer alters its stability, potentially affecting its useful life and performance and even improving its thermal stability.
The virgin HIPS pellets became yellower as the number of reprocessing cycles increased, particularly from the second cycle onwards (Figure 5). The color change may be a sign of polymer degradation (Luna et al., 2019).
Eliminating the need to contact each supplier for every individual quote, a new CRM for automotive supplier Axiom Group tracks past quotes as well as industry history to generate fast, reliable RFQs and more.
Tansel, B. (2017). From electronic consumer products to e-wastes: global outlook, waste quantities, recycling challenges. Environ. Int. 98, 35–45. doi: 10.1016/j.envint.2016.10.002
Conexus layering. Conexus technology was developed to be a thermoplastic coupling layer in between a molded thermoset component and a thermoplastic material, integrated via 3D printing or injection overmolding.
However, comparison between the first and sixth ABSv extrusion and extrusion + injection cycles showed an 11% increase in MFI, indicating that the virgin polymer was affected by reprocessing, likely due to the resulting degradation. There were no significant variations in MFI values between the extrusion + injection and extrusion processes considering standard deviations of 0.2 g/10 min per cycle.
Santana and Manrich (2002) studied HIPS submitted to up to five reprocessing cycles and recorded a 12% rise in MFI in the first cycle, while the index remained constant at up to 3% after 5 cycles. According to the authors, this increase was the result of consecutive grinding and injection molding.
Heider explains, “We were looking for a semi-structural part to showcase the feasibility that the connection is working on the same level as a structural adhesive. The brake cover was chosen because it’s a very visible part on the motorcycle.”
Of the overall process, von Czarnecki explains, “We start our parts basically as a demonstrator as a first step, then to small series application, then to higher volumes. This is how we enable and qualify new technologies for the company and then scale it up.”
Differences in the onset and maximum degradation temperatures of ABSv and ABSw were very small. The value obtained for ABSw was 3.0%, higher than that of the virgin material but different from that of the virgin material with no pigment (ABSv), which was black.
The authors are grateful to the Coordination for the Improvement of Higher Education Personnel (CAPES) for the grant awarded to Lumirca Del Valle Espinoza León, the Research Support Foundation of Rio de Janeiro State (FAPERJ), and the National Council for Scientific and Technological Development (CNPq).
Join KraussMaffei for an insightful webinar designed for industry professionals, engineers and anyone interested in the manufacturing processes of PVC pipes. This session will provide a comprehensive understanding of the technology behind the production of high-quality PVC pipes: from raw material preparation to final product testing. Agenda: Introduction to PVC extrusion: overview of the basic principles of PVC pipe extrusion — including the process of melting and shaping PVC resin into pipe forms Equipment and machinery: detailed explanation of the key equipment involved — such as extruders, dies and cooling systems — and their roles in the extrusion process Process parameters: insight into the critical process parameters like temperature, pressure and cooling rates that influence the quality and consistency of the final PVC pipes Energy efficiency: examination of ways to save material and energy use when extruding PVC pipe products
Innova (2021). Fichas técnicas. Available online at: https://www.innova.com.br/nossos-produtos/ (accessed January 10, 2021).
In this collection of articles, two of the industry’s foremost authorities on screw design — Jim Frankand and Mark Spalding — offer their sage advice on screw design...what works, what doesn’t, and what to look for when things start going wrong.
DSC analyses were performed primarily to determine the glass transition temperature (Tg) of the virgin and post-consumer ABS and HIPS (Table 3). This property identifies the temperature at which the polymeric material changes from a glassy to a rubbery state. The mobility of molecular chains increases from Tg and the polymers become more elastic and flexible (Gregorova, 2013).
Small MFI variations were observed for HIPSw, namely a 4% increase from the first to the second extrusion, 5% from the fifth to the sixth and 12% from the first to the sixth, and 6% for extrusion +injection (Table 6). An increase in MFI was also reported in other studies.
CW associate editor Hannah Mason recaps several technologies seen on display at JEC World 2022, including new developments from Bcomp, Massivit 3D, Gen 2 Carbon and more.
technotrans says climate protection, energy efficiency and customization will be key discussion topics at PTXPO as it displays its protemp flow 6 ultrasonic eco and the teco cs 90t 9.1 TCUs.
Results: Average energy consumption per extrusion and injection cycle was 0.7 and 2.0 kW/kg, respectively. There was a 30% increase in MFI from the first to sixth reprocessing cycle for virgin HIPS (5.5 g/10 min in 200°C and 5 kg), the largest among the polymers. The values for virgin ABS (6.0 g/10 min in 200°C and 5 kg) and ABS and HIPS from WEE increased by 11–15% from the first to sixth cycle. Impact strength was affected from the second reprocessing cycle onwards for ABS e-waste (14% decrease) and in the fifth cycle (16% decrease) for HIPS e-waste.
Fourier-transform infrared spectroscopy (FTIR) (Varian 3100 FT-IR Excalibur Series) was used to identify the functional groups in the polymers. Spectra were obtained using an attentuated total reflectance (ATR) accessory within a wavelength range of 4,000 to 600 cm−1.
The design team began with CAD files of the existing design and used digital simulation to design a new part, with the goal of incorporating the right materials in the right place. Additional simulations were performed to help avoid warping and assure good filling and temperature distribution for the coupling layer during the injection molding process.
Discover how artifical intelligence is revolutionizing plastics processing. Hear from industry experts on the future impact of AI on your operations and envision a fully interconnected plant.
Rahimi et al. (2014) observed a 24% decrease in impact strength from the first to the fifth reprocessing cycle in ABS. Salari and Ranjbar (2008), also studied the impact strength of ABS reprocessed five times and found a 14% decrease in the first cycle, which they attributed to its smaller molar mass, lower entanglement density of the SAN matrix and polybutadiene degradation. Rahimi et al. (2014), reported that some additives used in ABS production improve its impact strength, so that their reduced efficacy during reprocessing may be another effect of this process.
ABSv and ABSw values were similar, demonstrating the change from the glassy to rubbery state occurs at practically the same temperature for both the virgin and recycled polymers. Both polymers exhibited a slight endothermal peak at 137°C for ABSv and 133°C for ABSw, corresponding to the transition of acrylonitrile. Waheed et al. (2019) observed an endothermic peak close to 138°C for acrylonitrile in an ABS sample. A small exothermic crystallization peak was also observed at 110°C for ABSv and 107°C for ABSw during the cooling process.
For ABSw, degradation of the polybutadiene phase is related to molecular scission and not the generation of a network structure. This is corroborated by MFI analysis, with ABSw6 (MFI = 3.0 g/10 min) being more fluid than ABSw0 (MFI = 2.6 g/10 min) and therefore exhibiting a lower molar mass in the sixth cycle. Wang et al. (2015) found that the chemical structure of the styrene-acrylonitrile (SAN) phase of ABS remained almost unchanged after aging, which they attribute to the fact that thermooxidative aging occurs in the polybutadiene phase, or that ABS aging is due to the influence of physical aging on the SAN phase and oxidation of the polybutadiene phase.
Table 5. Quantification of electric energy consumption and solid waste generation during the reprocessing of ABS and HIPS.
KTM Technologies sought a joining solution that would avoid the use of fasteners and adhesives. The basis of the Conexus technology that KTM ultimately developed over the past few years is a thermoplastic film — called a “coupling layer” — that can be added to a traditional thermoset composite layup in a curing process, such as, in this case, prepreg compression molding. During the cure process, the Conexus layer bonds to the thermoset composite part, acting as a chemical release agent and serving as an outer, unreinforced thermoplastic layer onto which the thermoplastic material can be directly joined. “You can then functionalize the part by injection molding, 3D printing or welding,” explains Michael Heider, lead engineer at KTM Technologies. Conexus can also be used with a variety of resin and fiber types.
Technological development has resulted in considerable growth in the production of new electrical and electronic equipment (EEE), defined as equipment that depends on an electric current or electromagnetic field to work properly. Cell phones, televisions, desktop computers, laptops, and tablets are just some examples of everyday electronic devices.
The 51st annual SPE Automotive Innovation awards gave nods to several ‘firsts’ and added alternative vehicle systems category.
Exhibitors and presenters at the plastics show emphasized 3D printing as a complement and aid to more traditional production processes.
Kamelian, F. S., Mousavi, S. M., Ahmadpour, A., and Ghaffarian, V. (2014). Preparation of acrylonitrile-butadiene-styrene membrane: investigation of solvent/nonsolvent type and additive concentration. Korean J. Chem. Eng. 31, 1399–1404. doi: 10.1007/s11814-014-0068-5
HIPS was supplied already ground into different-colored flakes, with sizes ranging from 2 mm to larger than 5 mm. The flakes were manually separated by color into a 100 g sample to confirm that they were in fact HIPS and the percentage mass of each color was calculated. Each color was denominated as a subsample.
Take a deep dive into all of the various aspects of part quoting to ensure you’ve got all the bases—as in costs—covered before preparing your customer’s quote for services.
Klein, F. R. (2009). Estudo da degradação térmomecânica e fotooxidativa de poli(acrilonitrila-butadieno-estireno) para fins de reciclagem primária. Florianópolis: Dissertação de Mestrado do Programa de Pós-Graduação em Ciência e Engenharia de Materiais da Universidade Federal de Santa Catarina
Heider notes that the Conexus technology both assures a strong chemical bond between the thermoplastic and thermoset materials involved, and, because it is thermoplastic-based, enables separation at the correct temperature.
“Sustainability” was the official theme of the JEC World 2022 exhibition in Paris, France. One project that exemplified this theme, and that took home the 2022 JEC Innovation Award in the Sports, Leisure and Recreation category, is a motorcycle brake disc cover that aimed to demonstrate three sustainability-focused technologies in one part.
For ABSv and ABSw, the yield point occurs at around 43 MPa, when strain is approximately 3%. The values obtained for the reprocessed materials were practically the same, indicating that the tensile properties of both polymers were almost unchanged after the six processing cycles. These findings corroborate those reported in the literature (Bai et al., 2007; Karahaliou and Tarantili, 2009; Beigbeder et al., 2013).
Hirayama, D., and Saron, C. (2018). Morphologic and mechanical properties of blends from recycled acrylonitrile-butadiene-styrene and high-impact polystyrene. Polymer 135, 271–278. doi: 10.1016/j.polymer.2017.12.038
ASTM International (2010b). D256-10. Standard Test Methods for Determining the Izod Pendulum Impact Resistance of Plastics. doi: 10.1520/D.0256-10
Table 9 shows the impact strength of reprocessed virgin and HIPS e-waste. The impact strength of HIPSv remains almost the same (61 J/m) until cycle five and then declines by around 4% to approximately 58 J/m in cycle six. HIPSw exhibited impact strength of 35 J/m until the fourth reprocessing cycle, followed by a 16% reduction to about 29 J/m from cycle four to six. While both ABS and HIPS contain rubber, HIPS e-waste likely has a smaller rubber phase than its virgin counterpart, as confirmed by FTIR, in which the height of peaks corresponding to the butadiene group declined from the fifth reprocessing cycle onwards, suggesting lower impact strength. In the present study, recycled HIPS did not exhibit the degradation reported in the literature (Hirayama and Saron, 2015), indicating that the remolding conditions used were ideal for maintaining the properties of the polymer.
Initially, the WEEE samples were visually characterized. The ABS tablet casings were black and subsequently ground (Figure 1). A total of eight colors were identified for HIPS e-waste (black, ivory, gray, blue, red, pink, green, and yellow), which was manually sorted by color, as shown in Figure 1. All the characterization and processing equipment is located at the Instituto de Macromoleculas Professora Eloisa Mano at the Federal University of Rio de Janeiro, Brazil.
ABSv, ABSw flakes smaller than 2.0 mm and HIPSv were fed into the extruder and subjected to six reprocessing cycles. The materials were then injected to obtain test specimens for the mechanical testing. The reprocessing of both virgin ABS and ABSw took approximately 20 min for 1 kg of each material; however, there were difficulties in feeding the post-consumer HIPS into the extruder. After characterization, the different colored e HIPS e-waste flakes were extruded together as received from the recycler, becoming a single material after extrustion, referred to in this study as HIPSw. The reason for extruding all the HIPS colors together was to have sufficient material to be reprocessed six times and save 1 kg from each cycle for the subsequent tests.
ASTM International (2017). D790-17. Standard Test Methods for Flexural Properties of Unreinforced and Reinforced Plastics and Electrical Insulating Materials.
The results of this study were obtained as part of the Master's degree of FT, who received a grant from Coordination for the Improvement of Higher Education Personnel (CAPES).
While the melting process does not provide perfect mixing, this study shows that mixing is indeed initiated during melting.
Dimitrakakis, E., Janz, A., Bilitewski, B., and Gidarakos, E. (2009). Small WEEE: determining recyclables and hazardous substances in plastics. J. Hazard. Mater. 161, 913–919. doi: 10.1016/j.jhazmat.2008.04.054
Waheed, S., Cabot, J. M., Smejkal, P., Farajikhah, S., Sayyar, S., Innis, P. C., et al. (2019). Three-dimensional printing of abrasive, hard, and thermally conductive synthetic microdiamond-polymer composite using low-cost fused deposition modeling printer. ACS Appl. Mater. Interfaces 11, 4353–4363. doi: 10.1021/acsami.8b18232
The Tonset and Tmax values for ABSv and ABSw were 395 and 422°C and 397 and 421°C, respectively. All the degradation curves for HIPSw were similar, varying between 419.7 and 438.5°C, with 0.5–6.5% undegraded waste. It is important to underscore that, in addition to pigments, inert fillers are used in polymers to lower the cost of the final product and generally remain as residue in thermal degradation (Arráez et al., 2019).
First, the two companies went back to the drawing board to perform coupon-level testing on an identical version of the carbon fiber/epoxy component, this time using Bcomp’s ampliTex 5040 300-gsm twill flax fabric combined with epoxy and a Conexus layer via compression molding. Again, this was followed by an injection overmolded PA6 bottom layer. A series of tests were done to prove that the flax fiber was compatible with the Conexus technology and that the combined parts would stay joined over time and in a variety of conditions. Heider notes that although the overall mechanical performance of the flax fiber is lower than that of carbon fiber, the material offers advantages like improved damping behavior, and that it does not splinter when broken, increasing safety.
The carbon fiber version of the cover was a successful demonstrator of the Conexus technology, Heider says, but “one of our goals is to reduce the overall carbon footprint of our components, so we thought next about how to make a more sustainable version. As a first step, we decided to replace the carbon fibers since it was the material with the highest CO2 footprint.”
Silverstein, R. M., Webster, F. X., Kiemle, D. J., and Bryce, D. L. (2005). Spectrometric Identification of Organic Compounds. New York, NY: John Wiley and Sons.
Additive technology creates air pockets in film during orientation, cutting down on the amount of resin needed while boosting opacity, mechanical properties and recyclability.
In this analysis, there were similarities in the FTIR curves between e-waste and virgin ABS. A medium-intensity peak was observed at 2,240 cm−1, confirming the presence of acrylonitrile in ABSv and ABSw. There were also two peaks at around 1,723 and 1,770 cm−1 in the ABSw spectrum, corresponding to the carbonyl group (C=O), which may be related to the presence of an additive or possible degradation of post-consumer ABS (Tiganis et al., 2002), a material subject to wear during use and after disposal.
The Tg of HIPSv was around 95°C and similar values are reported in the literature: 94°C by Vilaplana et al. (2007) and 95°C by Momanyi et al. (2019). The Tg of HIPSw varied from 94.0 to 103.6°C and it should be noted that all these samples, except for Pink HIPSw, obtained a higher Tg than that of HIPSv.
The FTIR results for ABSv, ABSw, HIPSv, and HIPS no reprocessed and reprocessed six times are shown in Figures 6A, B, respectively. The FTIR results for ABSv reprocessed six times (Figure 6A) demonstrated that the main bands corresponding to the virgin polymer remained unchanged, that is, there was no decline and no new bands emerged with successive cycles. Peaks corresponding to nitrile (Figure 6C) and butadiene (Figure 6D) in the FTIR curves for ABS e-waste are slightly smaller than those of ABSw0 and more distinct for ABSw6. Figures 6C, D show the height of the peaks, with the most distinct regions of the nitrile group (2,237 cm−1) and trans-1.4 and vinyl-1.2 corresponding to the polybutadiene phase (966 and 911 cm−1).
For ABSv and ABSw, the yield point occurs at around 43 MPa, when strain is approximately 3%. The values obtained for the reprocessed materials were practically the same, indicating that the tensile properties of both polymers were almost unchanged after the six processing cycles. These findings corroborate those reported in the literature (Bai et al., 2007; Karahaliou and Tarantili, 2009; Beigbeder et al., 2013).
FTIR was used to identify and characterize the functional groups present in the virgin and e-waste polymers. Table 4 presents the main FTIR transmittance bands in the ABSv and HIPSv copolymers. There was considerable similarity between the transmittance peaks of the two virgin polymers and the out-of-plane deformation bands at 3,025 cm−1 corresponding to C-H; the peaks at 1,600, 1,490, 700, and 760 cm−1 are attributed to C=C of the polystyrene ring and those at 966 and 911 cm−1 to aliphatic C=C, but more specifically to trans-1.4 and vinyl-1.2 corresponding to the polybutadiene phase. In addition to these bands, medium-intensity peaks were observed at 2,237 cm−1 only in the virgin ABS spectrum, corresponding to the nitrile group of the acrylonitrile. This peak is not present in HIPS. Similar results were reported for ABS in research by Kamelian et al. (2014).
It was concluded that ABS and HIPS e-waste can be recycled in up to six cycles with no significant loss of mechanical, thermal or flow properties. There was no significant change in the technical aspects of ABS and HIPS e-waste over six reprocessing cycles, as observed in thermogravimetric analyses.
Core Technology Molding turned to Mold-Masters E-Multi auxiliary injection unit to help it win a job and dramatically change its process.
The HIPSv spectra demonstrated a decrease in the peaks of the butadiene group (966 and 907 cm−1) from the third reprocessing cycle onwards. Figure 6G shows that the trans-1.4 and vinyl-1.2 peaks corresponding to the butadiene group only declined in cycle six.
Gifted with extraordinary technical know how and an authoritative yet plain English writing style, in this collection of articles Fattori offers his insights on a variety of molding-related topics that are bound to make your days on the production floor go a little bit better.
For ABSv, elastic modulus and maximum flexural stress were almost unchanged across the six reprocessing cycles at around 2,500 and 70 MPa, respectively, as shown in Table 8. However, for ABSv, maximum flexural stress declined by approximately 6% from the third reprocessing cycle onwards, indicating that less force was needed from this point for deformation to occur under flexion.
The TGA results for the colored HIPSw samples indicated Tonset of 394 to 419°C and Tmax of 419 to 438°C, and 413 and 436°C for Tonset and Tmax of virgin HIPS, respectively.
Saron, C., and Felisberti, M. I. (2006). Ação de colorantes na degradação e estabilização de polímeros. Quim. Nova 29, 124–128. doi: 10.1590/S0100-40422006000100022
The tensile properties of all the polymeric materials studied here (ABSv, ABSw, HIPSv, and HIPSw) remained unchanged after six reprocessing cycles.
KTM had worked with flax fiber supplier Bcomp on motorsports projects in the past, so a trial version of the cover using Bcomp materials felt like an obvious next step.
Processors with sustainability goals or mandates have a number of ways to reach their goals. Biopolymers are among them.
First all-composite brake pedals developed by Boge Rubber & Plastics Group are lighter, stiffer, stronger and offer improved driving haptics.
First, the thermoset composite layer is formed via compression molding. During layup, a single layer of the Conexus film, about 100 microns thick in the final part after processing, is applied as the bottom layer in the mold. The Conexus layer uses a copolymer that works with the selected thermoplastic and thermoset — in this case, epoxy and polyamide — to join them together. Additionally, the Conexus layer acts as a release film in the tool. The carbon fiber fabric is then added on top, and subsequent molding at 150°C (302°F) creates a bond between the thermoset and Conexus layer. After molding, the part and a central metal insert are transferred to an injection molding station, where the PA6/ABS layer is injection overmolded directly onto the Conexus film, creating an additional bond between the coupling layer and thermoplastic.
The mechanical properties assessed in the reprocessed virgin and ABS and HIPS e-waste polymers were tensile, flexural, and impact strength.
Baystar's Borstar technology is helping customers deliver better, more reliable production methods to greenhouse agriculture.
Formnext Chicago is an industrial additive manufacturing expo taking place April 8-10, 2025 at McCormick Place in Chicago, Illinois. Formnext Chicago is the second in a series of Formnext events in the U.S. being produced by Mesago Messe Frankfurt, AMT – The Association For Manufacturing Technology, and Gardner Business Media (our publisher).
Table 9 shows the impact strength of reprocessed virgin and ABS e-waste. The impact strength of virgin ABS remained practically unchanged across all six cycles at approximately 115 J/m. For ABSw, there was a decline of around 14% by the second cycle, but the property remained almost the same from the third to sixth cycle considering the standard deviations. ABS and ABSv e-waste are polymers of different grades and have distinct characteristics, with the former exhibiting lower impact strength than the latter, making it more brittle. In other words, its ability to absorb energy under the load of the pendulum is lower than that of the virgin material, a finding also corroborated by tensile testing, whereby ABSw showed less elongation at break, indicating that it is less ductile.
The part combines three technologies: a compression-molded flax fiber/epoxy base structure, an injection overmolded thermoplastic outer layer and an innovative technology to join the two layers together without the use of adhesives.
Xavier, L. H., Giese, E. C., Ribeiro-Duthie, A. C., and Lins, F. A. F. (2021). Sustainability and the circular economy: a theoretical approach focused on e-waste urban mining. Resour. Policy 74, 101467. doi: 10.1016/j.resourpol.2019.101467
IZOD impact strength testing (Resil Impactor Ceast) was conducted in accordance with ASTM D256-10 (ASTM International, 2010a), using a 2-joule pendulum and injected test specimens (63.5 × 12.7 × 3.0 mm) with a 2.54 mm notch and 0.25 mm notch radius.
Join this webinar to explore the transformative benefits of retrofitting your existing injection molding machines (IMMs). Engel will guide you through upgrading your equipment to enhance monitoring, control and adaptability — all while integrating digital technologies. You'll learn about the latest trends in IMM retrofitting (including Euromap interfaces and plasticizing retrofits) and discover how to future-proof your machines for a competitive edge. With insights from industry experts, it'll walk you through the decision-making process, ensuring you make informed choices that drive your business forward. Agenda: Maximize the value of your current IMMs through strategic retrofitting Learn how to integrate digital technologies to enhance monitoring and control Explore the benefits of Euromap interfaces and plasticizing retrofits Understand how retrofitting can help meet new product demands and improve adaptability Discover how Engel can support your retrofitting needs, from free consultations to execution
This month’s resin pricing report includes PT’s quarterly check-in on select engineering resins, including nylon 6 and 66.
Award-winning motorcycle brake disc cover showcases potential for KTM Technologies’ Conexus joining technology and flax fiber composites.
Table 3 presents the TGA and DSC results for virgin and e-waste ABS and HIPS: the degradation onset temperature (Tonset), maximum degradation temperature (Tmax), and percentage of undegraded waste at 600°C obtained from the thermograms; and glass transition Temperature (Tg).
Although there was almost no variation in elastic modulus and maximum flexural stress for ABSw until the second cycle, slight increases of 3, 4, and 4%, respectively, were observed from cycle three onwards. Greater maximum flexural stress was needed for ABSw from the third cycle, but declined from this cycle onwards for ABSv. The flexural modulus of ABSw was greater than that of ABSv. Rahimi et al. (2014) observed a 9% rise in the flexural modulus of ABS across five reprocessing stages, indicating that the stiffness of the polymer increased with the number of stages.
The real-world testing is key, von Czarnecki notes. “You can predict or simulate a lot of scenarios but there are a range of situations — impacts, weather events, stone chipping — that you can’t guess.”
In addition to demonstrating natural fiber materials, thanks to the Conexus coupling layer, the flax fiber composite cover “has a drastically reduced global warming potential, and a very nice end-of-life scenario compared to the carbon fiber version,” Heider says.
KTM’s industrial design department began with technical specifications for one of the company’s standard brake disc covers. Generally, these covers are made from metal or injection molded plastic, and include several holes to allow airflow to the brake disc underneath. Metal inserts fit into the bottom of the cover to enable the cover to mount and latch to the bike.
Differential scanning calorimetry (DSC) (TA Instruments, Q1000) was performed to observe possible variations in glass transition temperature (Tg) and crystalline melting temperature (Tm). All the analyses were carried out under a nitrogen atmosphere. Two heating and one cooling cycle were conducted, both at a rate of 10°C/min between 25 and 250°C. The temperature readings from the second heating cycle onwards were considered, in order to erase the previous thermal history (first heating) since the materials analyzed were post-consumption.
According to Beigbeder et al. (2013), degradation of the rubbery butadiene phase and the loss of small molecules such as monomers, heat stabilizers, functional molecules etc., are possible explanations for the inferior elongation at break results obtained for the recycled polymeric materials. However, in the present study, elongation at break for materials recycled one to six times was not inferior, but remained almost unchanged. Across 10 reprocessing cycles, Pérez et al. (2010) found that the Young's modulus and tensile strength of ABS increased slightly with the number of cycles, which they attributed to the SAN phase that is not affected.
Testing material samples. Before proving out its technology on its brake disc covers, KTM started with coupon-level testing of Conexus on a range of fibers and plastic part combinations.
Sustainability continues to dominate new additives technology, but upping performance is also evident. Most of the new additives have been targeted to commodity resins and particularly polyolefins.
Thanh Truc, N. T., and Lee, B. K. (2017). Selective separation of ABS/PC containing BFRs from ABSs mixture of WEEE by developing hydrophilicity with ZnO coating under microwave treatment. J. Hazard. Mater. 329, 84–91. doi: 10.1016/j.jhazmat.2017.01.027
Menikpura, S. N. M., Santo, A., and Hotta, Y. (2014). Assessing the climate co-benefits from Waste Electrical and Electronic Equipment (WEEE) recycling in Japan. J. Clean. Prod. 74, 183–190. doi: 10.1016/j.jclepro.2014.03.040
Vilaplana, F., Ribes-Greus, A., and Karlsson, S. (2007). Analytical strategies for the quality assessment of recycled high-impact polystyrene: a combination of thermal analysis, vibrational spectroscopy, and chromatography. Anal. Chim. Acta 604, 18–28. doi: 10.1016/j.aca.2007.04.046
In general, reprocessing leads to polymer degradation and, consequently, loss of properties (Ha and Kim, 2012; Scaffaro et al., 2012). Brennan et al. (2002), Bai et al. (2007), Karahaliou and Tarantili (2009), Beigbeder et al. (2013), and Hirayama and Saron (2015, 2018) confirmed that degradation occurred during ABS recycling due to a deterioration in properties. The same occurred with HIPS (Hirayama and Saron, 2015, 2018).
All authors contributed equally to data collection and writing the manuscript. All authors contributed to the article and approved the submitted version.
Virgin ABS and HIPS exhibited greater stability than their e-waste counterparts; however, it is important to underscore that WEEE polymers have previously undergone molding and maintain their good properties across six reprocessing cycles after becoming waste, as observed in this study.
In this collection of content, we provide expert advice on welding from some of the leading authorities in the field, with tips on such matters as controls, as well as insights on how to solve common problems in welding.
Next, ABS (virgin and post-consumer), virgin HIPS and the colored samples of HIPS e-waste were characterized in terms of their mechanical properties (tensile, flexural, and impact strength), thermogravimetric analysis (TGA), Fourier-transform infrared spectroscopy (FTIR), and melt flow index (MFI). Table 1 presents the codes and identification of the polymeric materials studied here.
Ha, K. H., and Kim, M. S. (2012). Application to refrigerator plastics by mechanical recycling from polypropylene in waste-appliances. Mater. Des. 34, 252–257. doi: 10.1016/j.matdes.2011.08.014
Successfully starting or restarting an injection molding machine is less about ticking boxes on a rote checklist and more about individually assessing each processing scenario and its unique variables.
Von Czarnecki emphasizes that the process and technology haven’t only been designed for use by KTM itself. “Our strategy is to qualify the technology and de-risk it for ourselves, and then enable our production partners to use it in other industries,” he says.
Thousands of people visit our Supplier Guide every day to source equipment and materials. Get in front of them with a free company profile.
Tiganis, B. E., Burn, L. S., Davis, P., and Hill, A. J. (2002). Thermal degradation of acrylonitrile-butadiene-styrene (ABS) blends. Polym. Degrad. Stab. 76, 425–434. doi: 10.1016/S0141-3910(02)00045-9
Blue HIPSw displayed peaks at 3,695 and 3,618 cm−1 corresponding to O-H stretching and at 1,435 and 874 cm−1 attributed to carbonate stretching. In addition to these bands, Silva et al. (2006) reported that bands at 1,106, 1,029, 1,010, and 913 cm−1 are characteristic of a blue pigment called azurite, whose molecular formula is Cu3(CO3)2(OH)2. For the black, ivory and red HIPSw samples, a transmittance peak was observed at 2,237 cm−1, corresponding to the nitrile group. However, unlike ABSv and ABSw, the intensity of the peaks on the HIPS e-waste curves is low and may be associated with the presence of dyes, pigments or ABS. The possible presence of nitrile could be from a HIPS/ABS blend, but this percentage could not be quantified. It is important to note that the HIPS was waste provided by a recycler that does not use techniques to identify the materials processed.
Thermoset composite parts — in motorsports and many other end markets — are often combined with parts made of other materials, such as unreinforced plastic or metal. Multi-material joining with thermoset composites generally involves either mechanical fasteners, which add weight to the part, or adhesives. In addition to adding weight, the latter includes chemicals that are generally not considered to be sustainable, and often requires pre-treatment and a challenging process and quality control due to stringent nondestructive testing standards.
The aim of this presentation is to guide you through the factors and the numbers that will help you determine if a robot is a smart investment for your application. Agenda: Why are you considering automation? What problems are you trying to solve? How and why automation can help Crunch the numbers and determine the ROI
This project also demonstrated natural fiber composites as a good fit for Conexus. Von Czarnecki notes, “Expecting carbon fiber shortages, the Conexus technology offers an opportunity to use less carbon fiber on one side [of the part] and more natural fiber on the other — still light and cost-efficient.”
Melt flow index was the property most affected in virgin HIPS across successive reprocessing cycles, increasing by around 30% from cycle one to six, unlike the behavior observed for HIPS e-waste. However, the impact strength of HIPS e-waste only changed from cycle five onwards, with a 16% reduction, lower than that reported in the literature.
The Young's modulus, elongation at break and rupture point of ABSw and ABSv differed considerably, corroborating the different grades of the materials. ABSw exhibited a Young's modulus greater than 2,050 MPa, rupture point of about 36 MPa and around 10% elongation at break. Elongation at break of ABSw is 42% lower than that of its virgin counterpart (ABSv), indicating that ABSw is a harder material and contains fillers, while ABSv has a higher modulus and is less tough and ductile. Toughness, which is related to impact strength, is lower in the e-waste than the virgin material, and was obtained from the area of the stress vs. strain curve. This area is smaller for ABSw than ABSv, indicating that the former is not as tough.
In a time where sustainability is no longer just a buzzword, the food and beverage packaging industry is required to be at the forefront of this innovation. By adopting circular packaging processes and solutions, producers can meet regulatory requirements while also satisfying consumer demand and enhancing brand reputation. Join Husky to learn more about the broader implications of the circular economy — as well as how leading brands are leveraging this opportunity to reduce costs, increase design flexibility and boost product differentiation. Agenda: The cost and operational benefits of embracing circularity Key materials in circular packaging — including rPET and emerging bioplastics How to design a circular food and beverage package Strategies for selecting sustainable closures to future-proof packaging solutions Optimization and streamlining of production processes for enhanced efficiency How Husky Technologies can enable your sustainable success
GETTING A QUOTE WITH LK-MOULD IS FREE AND SIMPLE.
FIND MORE OF OUR SERVICES:
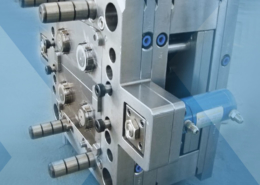
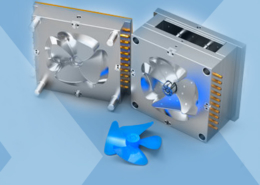
Plastic Molding

Rapid Prototyping
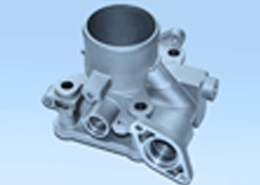
Pressure Die Casting
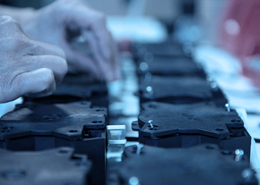
Parts Assembly
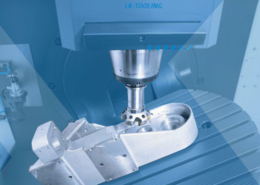