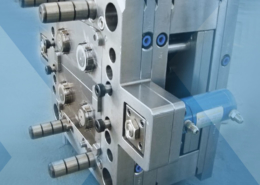
Exploring Molded Plastic Products: A Comprehensive Overview
Author:gly Date: 2024-06-08
Introduction
Molded plastic products have become ubiquitous in our modern world, seamlessly integrated into various aspects of our daily lives. From the keyboards we type on to the chairs we sit on, molded plastic products offer versatility, durability, and affordability. This article aims to delve into the realm of molded plastic products, exploring their significance, applications, manufacturing processes, environmental impact, and future prospects.
Significance of Molded Plastic Products
Functional Diversity
Molded plastic products encompass a vast array of items, ranging from consumer goods to industrial components. Their versatility allows for the creation of intricate designs and shapes, catering to diverse functional needs.
Molded plastic products also play a crucial role in sectors such as automotive, electronics, healthcare, and packaging. In the automotive industry, plastic components contribute to weight reduction and fuel efficiency. In healthcare, they enable the production of sterile and disposable medical devices.
Economic Implications
The mass production capabilities of molded plastic products have significantly impacted global economies. Their cost-effectiveness makes them an attractive option for manufacturers seeking efficient production methods. Moreover, the lightweight nature of plastic reduces transportation costs and energy consumption.
Furthermore, molded plastic products facilitate innovation and product differentiation, driving competitiveness in various industries. They enable companies to bring new designs to market rapidly, meeting evolving consumer demands.
Environmental Considerations
Despite their numerous benefits, molded plastic products raise concerns regarding environmental sustainability. The proliferation of single-use plastics has led to pollution and ecological damage, prompting calls for greater recycling efforts and alternative materials.
However, advancements in biodegradable and recyclable plastics offer hope for mitigating environmental impact. Innovations in manufacturing processes, such as injection molding using recycled materials, demonstrate a commitment to sustainability within the plastics industry.
Manufacturing Processes
Injection Molding
Injection molding is the most common method used to produce molded plastic products. It involves injecting molten plastic material into a mold cavity, where it cools and solidifies to form the desired shape. This process enables high-volume production of complex parts with consistent quality.
Blow Molding
Blow molding is ideal for creating hollow plastic products, such as bottles and containers. It utilizes compressed air to inflate a heated plastic parison within a mold cavity, resulting in the desired shape. This process offers cost-effective production of lightweight and durable containers.
Rotational Molding
Rotational molding, also known as rotomolding, involves rotating a mold filled with plastic resin in multiple axes. The heat from the mold gradually melts the resin, coating the interior surface evenly to form the desired shape. This method is well-suited for large, hollow products and offers design flexibility and durability.
Applications Across Industries
Automotive
In the automotive industry, molded plastic products are integral to interior and exterior components, including dashboards, bumpers, and trim panels. Their lightweight properties contribute to fuel efficiency and vehicle performance, while their durability ensures long-term reliability.
Electronics
Molded plastic products play a crucial role in the electronics sector, where they are used in casings, connectors, and housings for electronic devices. Their electrical insulation properties, combined with design flexibility, make them indispensable for modern electronics manufacturing.
Medical
In healthcare, molded plastic products are essential for medical device manufacturing, including syringes, catheters, and implantable devices. Their biocompatibility, sterilizability, and precision molding capabilities ensure safety and efficacy in clinical settings.
Future Prospects and Challenges
The future of molded plastic products lies in innovation and sustainability. Continued research into biodegradable materials, advanced recycling technologies, and eco-friendly manufacturing processes will be crucial for reducing environmental impact.
Furthermore, emerging technologies such as 3D printing hold promise for revolutionizing the production of molded plastic products. Additive manufacturing techniques offer greater design freedom and customization, opening new possibilities for product development.
However, challenges remain, particularly regarding plastic waste management and pollution prevention. Collaborative efforts involving governments, industries, and consumers are essential for developing holistic solutions to these pressing issues.
Conclusion
In conclusion, molded plastic products have revolutionized various industries, offering functional diversity, economic benefits, and technological advancements. While their significance is undeniable, addressing environmental concerns and embracing sustainable practices are imperative for their continued relevance in the 21st century. By prioritizing innovation, collaboration, and responsible consumption, we can ensure a future where molded plastic products contribute positively to society while preserving our planet for future generations.
GETTING A QUOTE WITH LK-MOULD IS FREE AND SIMPLE.
FIND MORE OF OUR SERVICES:
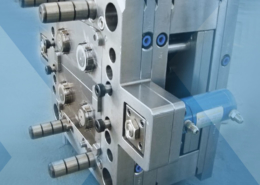
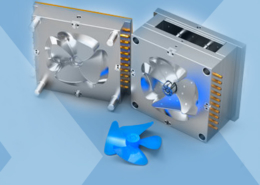
Plastic Molding

Rapid Prototyping
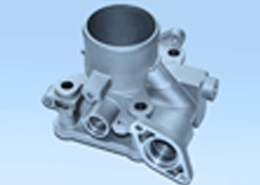
Pressure Die Casting
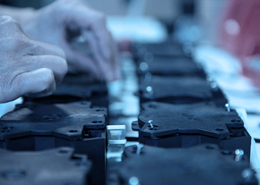
Parts Assembly
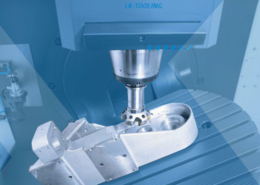