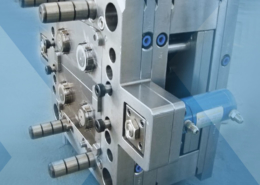
Polyurethane-based engine covers protects pedestrians - polyurethane plastic mol
Author:gly Date: 2024-09-30
Milacron has aggressively expanded its rebuild and remanufacture capabilities for LPIM machines for customers. There are a large number of old LPIM machines in the field that were purchased in the late 1980s and 1990s that need rebuilds and upgrades to control systems and new motor and drive selections, moving away from DC to AC drives which provide better energy efficiency. Milacron’s full remanufacturing consists of fully rebuilding the machine to current model specifications, including full teardown and inspection, platen refurbishment, full re-painting of the machine, new controls, electrical system, and hydraulics. The major tonnage and injection cylinders and hydraulic accumulators are sent out for refurbishment and resealing. New screws, barrels, and injection melt accumulators are also included as part of this program.
“Especially when you are entering new subject areas, competent, reliable and cooperative companions are worth their weight in gold. You also need a good dose of pragmatism, which is present in all project partners at all times,” continued Hennrich. The SKZ supported the component design with rheological simulations of the filling behaviour and degree of cross-linking. Growth rates in the silicone market have been in the double-digit range for several years despite the weakening economic situation. The impending PFAS ban will certainly continue to drive LSR sales in the coming months - as the inquiries from the industry already confirm.
Parts molded with LPIM can replace many rotational molded or industrial blow molded parts with better aesthetics and better cycle times.
In total, Milacron is currently rebuilding eight LPIM machines as well as four HPIM machines. “Milacron’s commitment to the LPIM side of the industry, their quality, performance, and service is second to none and is the reason that we made this decision to have them rebuild and upgrade this equipment,” said Ron Ernsberger, President, 20/20 Custom Molded Plastics.
Machines delivered in the 1980s and 1990s are being upgraded to outperform their original specifications, while new machine deals also are accelerating.
“Only through close cooperation like this is it possible to expand the company's own portfolio and build up the necessary network alongside day-to-day business. The SKZ provides us with a wide range of opportunities to exchange ideas with other industry representatives,” added Markus Scheuerlein, project manager Mold Making at toolcraft AG.
Eric Hallstrom, Business Manager, Milacron LPIM added, “Milacron has been promoting our proprietary Structural Web technology that allows for multi-point gas assist molding that can be added to as an option to our standard LPIM machine. The process allows for a cosmetic part appearance for large projected area parts and can reduce part weights by up to 20%. The gas assist process also creates an inherently strong and durable part, molded with low internal stresses and a dual wall thickness which can replace many rotational molded or industrial blow molded parts with better aesthetics and better cycle times for higher volume parts.”
The jointly developed tool will be available to the SKZ for research and education in the future. The SKZ would like to thank all partners involved and those who have worked in the background. Interested parties are cordially invited to experience the tool live in action at the SKZ Network and Technology Day on June 26 and 27 in Würzburg in the model factory at the SKZ.
The markets driving the increased level of activity are material handling (pallets and boxes), underground enclosures for telecommunications and utilities, drainage and irrigation products, all-terrain vehicle (ATV) components, commercial/institutional, and industrial and safety products. Milacron is also seeing other new products being developed that are conversions from concrete, metal, and wood in the building and infrastructure market as well.
Bestenlehrer GmbH, a tool and mould making company, is a recognized expert in the field of polishing complex cavities. The second-generation family business specialises in the distortion-free and contour-accurate polishing of injection moulding, die casting and forming tools. “Long-standing and highly qualified specialists as well as modern workplaces must be our claim when it comes to the individual requirements of our customers,” explains Marcel Bestenlehrer, managing director of Bestenlehrer GmbH.
“It quickly became clear to us that this project was a unique and good opportunity to test our cold runner system in practice,” said Torsten Schnell, head of Research and Development at GÜNTHER Heisskanaltechnik GmbH. “The electric linear actuators allow precise and infinitely variable adjustment of the needles for optimum filling of different component sizes in one mould,” added Jörg Essinger, head of Application Technology.
Machine builder Milacron Holdings Corp. has seen demand increase for its Low Pressure Injection Molding (LPIM) Structural Foam machines following a successful NPE 2018 in Orlando, FL, including machine rebuilds. Milacron had a dedicated space in the NPE booth focusing on LPIM technologies and large part molding. An eye-catching display showed a replica platen of the massive Cincinnati 6,750 ton machine sold to 20/20 Custom Molded Plastics of Holiday City, OH.
Five partners from the world of plastics have embarked on an ambitious project: two moulded parts made of liquid silicone (LSR), which could not have been more different in terms of their application and geometric dimensions, were to be produced in a single mould. On the one hand, a coffee lid with a shot weight of 28 g, a diameter of 100 mm and a maximum wall thickness of 7 mm was to be produced. On the other hand, a magnifying glass with a shot weight of only 6 g and a diameter of 35 mm with a lens with 6x magnification was on the agenda.
Milacron CEO Tom Goeke stated, “Stories like 20/20’s machine retrofits reinforce the fact that Milacron has an unrivaled aftermarket offering. Our aftermarket offerings aren’t only spare parts, we can literally take an older machine and transform it to like new condition. Milacron has set the standards, driven innovation and led the industry in Multi-Nozzle Low-Pressure Injection Molding Technologies for more than four decades. These machines can be used for Structural Foam, Structural Web, Gas Assist, Solid Molding, or combinations of these technologies depending on the application.” Goeke added, “The LPIM market is strong for our customers that require either new or rebuilt machines in both North America and Europe, and we have a number of solid inquiries both domestically and internationally including many from Latin America and India.”
At NPE, 20/20 entered into an agreement with Milacron to refurbish and upgrade two of their existing 400-ton LPIM machines to 500-ton LPIM machines, and one of their 500-ton LPIM machines to 750-ton LPIM machines. 20/20 is also having Milacron rebuild and upgrade five of their 750-ton LPIM machines. The machines will undergo a complete remanufacture and rebuild process at Milacron’s Batavia, OH manufacturing plant and be returned like new machines.
The project consortium in front of the LSR injection moulding machine from KraussMaffei with the dosing system from NEXUS in the SKZ model factory. (From left) Jürgen Ritter (Weschu), Sebastian König (Meusburger Georg GmbH & Co KG), Marcel Bestenlehrer (Bestenlehrer GmbH), Jörg Essinger & Torsten Schnell (GÜNTHER Heisskanaltechnik GmbH), Thomas Lender & Markus Scheuerlein (toolcraft AG) and Bernhard Hennrich (SKZ).
Ernsberger added, “Milacron worked closely with our entire team at 20/20 to identify the upgrades to the existing machines to be rebuilt that will put these machines above today’s current machine specifications and give us the widest capabilities for these size machines in the industry.” Ernsberger continued, “We also had Milacron integrate some proprietary technologies into their machines that allow us to have the most versatile LPIM Structural Foam machine fleet in the custom molding market. It’s a great partnership between the companies, as all equipment at 20/20 CMP is 100% Milacron.”
Stephen has been with PlasticsToday and its preceding publications Modern Plastics and Injection Molding since 1992, throughout this time based in the Asia Pacific region, including stints in Japan, Australia, and his current location Singapore. His current beat focuses on automotive. Stephen is an avid folding bicycle rider, often taking his bike on overseas business trips, and is a proud dachshund owner.
“The nice thing about the plastics industry and my job is that after 16 years of professional experience, you can still get to know new materials or classes of materials that are fascinating,” explained Bernhard Hennrich, group manager Injection Molding Research at SKZ.
Ideal for injection molding large, lightweight, durable structural plastic parts, the Milacron LPIM Structural Foam Technology creates a cellular foamed core surrounded by integral skins, forming a total integral and rigid structure. In this process, a foaming agent (nitrogen) is mixed with the polymer melt and short-shot through a modular multiple nozzle system into a mold (or multiple molds) in a volume less than is required to fill a solid part. The injection pressure and expanding gas/polymer cellular mixture act to fill the mold. The mold cavity pressures are 10–20 times lower than conventional injection molding which permits the use of lower cost aluminum molds with no additional hot runner system since the hot runner manifold and nozzle system is integral to the machine. Many molds and large parts of different sizes can be molded at the same time. The multi-nozzle machine design allows for multiple molds to be run simultaneously allowing for higher productivity.
Supported by the expert advice of Dr. Ralf-Urs Giesen and his colleagues from the University of Kassel and thanks to the provision of system technology by KraussMaffei and NEXUS, SKZ and toolcraft AG have been able to press ahead with their developments over the past three years in the production cells set up on site. The significant differences in the shot weight of the two articles quickly led to a solution approach with a cold runner mould with valve gate.
Meusburger Georg GmbH & Co KG contributed to the consortium with its expertise in selecting the right material for the tool steels used. “The silicone market is a stable and growing market. For us at Meusburger it was important to expand our expertise here even more in order to be able to advise customers in the best possible way,” emphasised Sebastian König, regional sales manager at Meusburger. For the planned injection mould, corrosion-resistant steels were proposed and ultimately used for the basic structure and the mould inserts.
Innovation partner GÜNTHER Heisskanaltechnik GmbH provided its valve gate nozzle with electric linear actuator for this purpose and, due to the space available on the machine's clamping unit, supplemented it with drives offset by 90 degrees.
Hallstrom added, “Essentially we are updating machines that have been in production for over 30 years and bringing them up to the same specifications as our new machines. This has been especially popular since we started to promote this capability to our customers, as they see a significant enough savings since we are re-using the most expensive parts of these large machines, being the bases, platens, and cylinders. The customer gets back a machine that outperforms the machine’s original specifications and is as reliable as a new machine with the same warranty.”
“The contacts we make at the specialist conferences allow us to identify trends at an early stage and drive innovation forward,” he continued. The expertise built up over decades in the field of mould making for highly demanding precision small parts is the solid starting point for toolcraft to manufacture the silicone mould within the project. In addition to the ongoing “SiliTemp” research project with the SKZ, toolcraft is now also developing and building the first silicone tools for industry.
GETTING A QUOTE WITH LK-MOULD IS FREE AND SIMPLE.
FIND MORE OF OUR SERVICES:
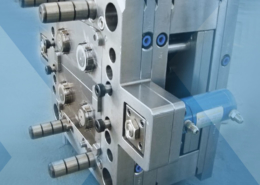
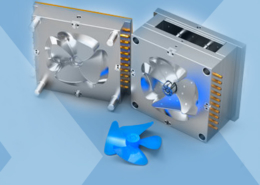
Plastic Molding

Rapid Prototyping
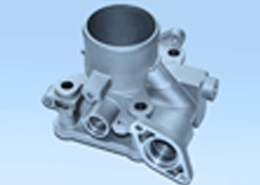
Pressure Die Casting
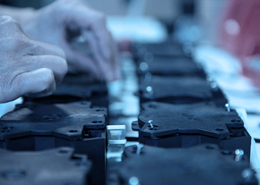
Parts Assembly
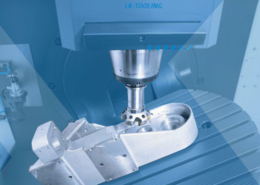