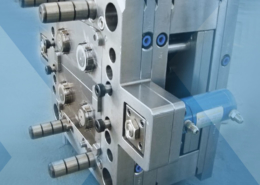
Polyamide makes its mark in high-pressure hydrogen tank for Toyota fue - pa6 inj
Author:gly Date: 2024-09-30
Lisa Eitel has worked in the automation industry since 2001. Her areas of focus include motors, drives, motion control, power transmission, linear motion, and sensing and feedback technologies. She has a B.S. in Mechanical Engineering and is an inductee of Tau Beta Pi engineering honor society; a member of the Society of Women Engineers; and a judge for the FIRST Robotics Buckeye Regionals. Besides her motioncontroltips.com contributions, she also leads the production of the quarterly motion issues of Design World.
The mold, produced by Austria’s z-moulds, is as small and light as a 96-cavity mold and fits into the injection molding machine with a smaller column distance. Cycle time is reduced by the smaller design, which also requires moving less mass. Alltrista has cut the weight of its enclosures by 25%; with 3.1 billion closures produced annually, that means more than 2 million pounds less resin used – about the weight of 160 African Bush elephants, the company said.
“We’re offering both the expertise and machinery we have onsite to support the injection molding needs of inventors, plastic parts suppliers, and manufacturers — whether someone needs high volume parts or a small quantity of intricate pieces.”
Added Christopher Navratil, CTO of Alltrista's parent company: "We were determined to be the first manufacturer to run a system with 128 cavities in under two seconds. In Netstal, z-moulds, and Intravis, we have found the best system partners for this project. Each company is a leader in its field, and the combination is unbeatable. With our 128-cavity systems, we produce more efficiently than ever before, can deliver at any time, and inspire our customers. This has given us an enormous competitive advantage."
Netstal’s CAP-Line 4500 is identical to two production systems being used by Alltrista, a contract manufacturer based in Greer, SC. The line features an all-electric clamping unit with 4,500 kN of force and a dry cycle time of 1.4 seconds. An optimized barrier screw allows for a smaller injection unit with higher plasticizing performance and better homogenization, Netstal expained.
A 128-cavity mold will produce 26-mm water closures in a cycle time of 1.9 seconds in a live experience at Netstal’s booth at NPE 2024.
Copyright © 2024 WTWH Media LLC. All Rights Reserved. The material on this site may not be reproduced, distributed, transmitted, cached or otherwise used, except with the prior written permission of WTWH Media Privacy Policy | Advertising | About Us
For more details on working with Hy-Lite Injection Molding Services, contact Steve Beck at 888-256-2599 or visit www.hy-lite.com.
"With the new CAP-Line concept, we are aligning our portfolio even more closely with our customers' applications,” he noted. “Closure manufacturers benefit from a customized system, while pre-configuration can speed up the consultation and quotation process so that delivery times for the machine are as short as possible."
Overall, Netstal’s CAP-Line also fits in a smaller overall space — 538 square feet — and uses about 12% less electricity than competing machines running 96-cavity molds, Kogler said.
“From downstream assembly to packaging and shipping, we make this process turnkey for the customers. We’re a Made in America company that wants to support the plastics needs of America during this difficult time.”
Beck points out that, while Hy-Lite can’t manufacture safety masks or blow-molded items (such as hand sanitizer bottles), the company has many other options for supporting PPE needs.
In the NPE demonstration, finished caps will travel through an Intravis vision-inspection system. The system executes 360-degree inspection of the closures to an accuracy of hundredths of a millimeter using nine high-resolution cameras.
"Alltrista is the first in the world to produce with 128 cavities and a cycle time of 1.9 seconds,” said Horst Kogler, head of Netstsal’s caps and closures business unit. “They produce more than 3.1 billion closures with two lines [annually]. More output per square meter of production area is currently not possible."
Top global problem solving EE forum covering Microcontrollers, DSP, Networking, Analog and Digital Design, RF, Power Electronics, PCB Routing and much more
To help with the heightened demand for injection-molded products during the COVID-19 outbreak, Hy-Lite is making their Contract Injection Molding Services available to companies nationwide. Located in Pensacola, Fla., the Hy-Lite facility houses seven injection molding machines capable of small, specialty and slow run projects.
“Our team can take on injection molding projects for manufacturers running at capacity, whether it’s supplementing high-demand product production or taking over less-critical secondary lines that have had to be placed on the backburner,” says Beck. “We have three 300-ton, one 390-ton, and three 500-ton machines available at the place for 24/7 operation. This means we can tackle the small quantity runs and slow running parts because the machinery is always ready for projects.”
Browse the most current issue of Design World and back issues in an easy to use high quality format. Clip, share and download with the leading design engineering magazine today.
Hy-Lite services are available on a contracted basis with speedy turnaround. Beck, who has been with Hy-Lite for more than two decades directing the company’s injection molding and manufacturing operations, explains that Hy-Lite can supply products made with most thermoplastics.
Geoff Giordano is a tech journalist with more than 30 years’ experience in all facets of publishing. He has reported extensively on the gamut of plastics manufacturing technologies and issues, including 3D printing materials and methods; injection, blow, micro and rotomolding; additives, colorants and nanomodifiers; blown and cast films; packaging; thermoforming; tooling; ancillary equipment; and the circular economy. Contact him at [email protected].
“We understand manufacturers of personal protection equipment and other supplies are running at maximum capacity and are challenged to keep up with demand,” says Steve Beck, plant/technical manager for Hy-Lite, a U.S. Block Windows Company. “If we can be a small part of the solution in a national emergency, then we want to help.
GETTING A QUOTE WITH LK-MOULD IS FREE AND SIMPLE.
FIND MORE OF OUR SERVICES:
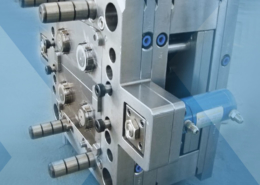
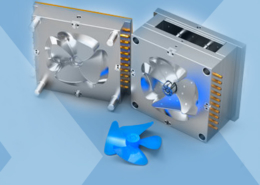
Plastic Molding

Rapid Prototyping
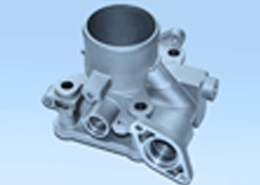
Pressure Die Casting
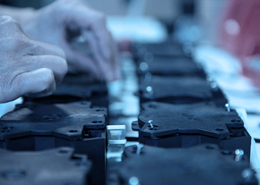
Parts Assembly
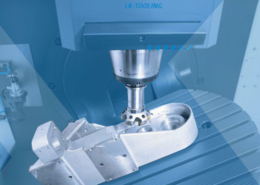